Contributing editor
- FMA
- The Fabricator
- FABTECH
- Canadian Metalworking
Categories
- Additive Manufacturing
- Aluminum Welding
- Arc Welding
- Assembly and Joining
- Automation and Robotics
- Bending and Forming
- Consumables
- Cutting and Weld Prep
- Electric Vehicles
- En Español
- Finishing
- Hydroforming
- Laser Cutting
- Laser Welding
- Machining
- Manufacturing Software
- Materials Handling
- Metals/Materials
- Oxyfuel Cutting
- Plasma Cutting
- Power Tools
- Punching and Other Holemaking
- Roll Forming
- Safety
- Sawing
- Shearing
- Shop Management
- Testing and Measuring
- Tube and Pipe Fabrication
- Tube and Pipe Production
- Waterjet Cutting
Industry Directory
Webcasts
Podcasts
FAB 40
Advertise
Subscribe
Account Login
Search
3 angles on press brake training: Part III
Taught by the OEM
- By Kate Bachman
- August 3, 2018
- Article
- Bending and Forming
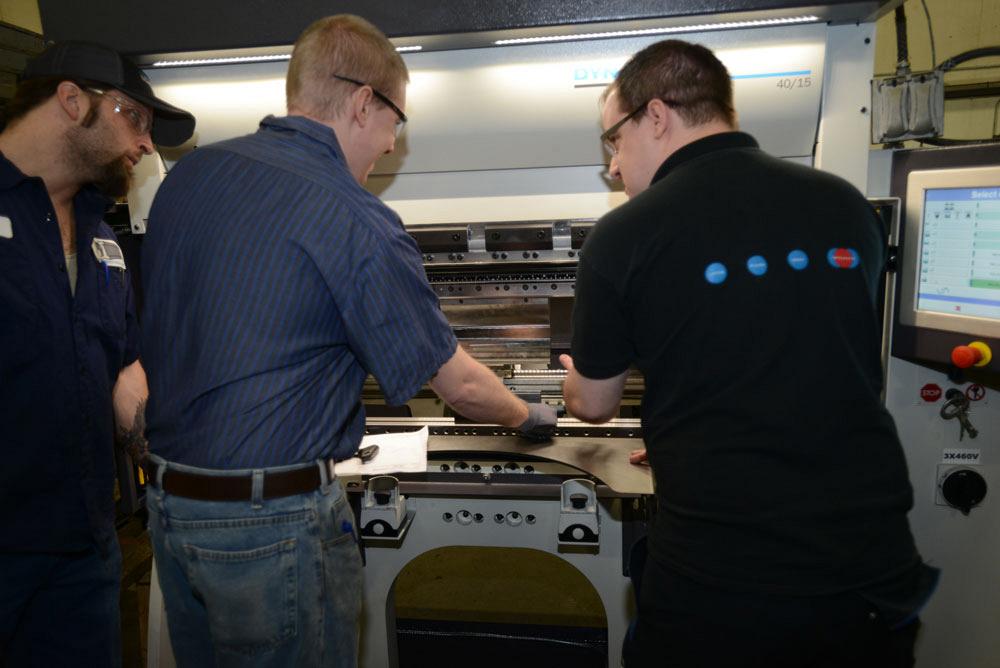
Louis Industries press brake operators received training on the equipment they use from the OEM’s expert trainer.
Editor’s Note: This article is the final installment in a three-part series about different approaches to press brake training. Part I, which was published in April, highlights training in a classroom environment. Part II, which appeared in May, explored on-site training. Part III explores OEM training.
Louis Industries, Paynesville, Minn., has reached for the stars with its feet planted firmly in the Minnesota farmland that surrounds it.
The manufacturer is equipped with a fleet of new high-tech, modern machinery, but its workforce’s expertise and experience are uneven. Some press brake operators are highly trained and knowledgeable, while others are rough-cut and untrained, with little or no fabrication background at all.
The company is growing and taking on jobs with increasingly more complex parts. It needs a well-trained workforce from a rural area that is losing its population like sand through a sieve, according to a company spokesperson.
How Faster?
Louis Industries COO Lance Louis explained that the family-owned company is firmly committed to the region it grew from organically, but that experienced press brake operators are few and far between there. The shortage creates pressure to shorten the time to educate an employee to be adept at bending parts and to limit the scope of the skill set they need to bend parts perfectly.
“How do we take a person that we can hire who doesn’t have fab experience and train them faster? How do we make them a rock star sooner? How do we make them comfortable in front of that machine and productive, long-term, without wearing their body out? Without having to send them to years of schooling? How do we take those stresses out of learning and knowledge?” Louis queried.
The need to educate press operators intensified when the company upgraded to LVD Strippet’s CADMAN®-B software suite, Louis said. “When we decided to get the software, one of the big things we wanted to do was sit down and retrain our operators—not only our more advanced operators, but our inexperienced ones too. We wanted to find a solution so that we could bring someone in and teach them the simplest and the best way to bend parts with the least amount of instructions—and have it be usable the first time and every time.
“And how do we teach our operators things we don’t know how to explain?”
Louis Industries sought and received a training grant from the state of Minnesota and applied the funding to bring LVD Co.’s press brake expert and manager, Steven Lucas, over from Belgium for a week. “Steven has taken a lifetime to study this. He and our best operators and our newest operators met up in our training room upstairs, and then went out on our plant floor to retrain on the new process,” Louis said.
OEM Training
Louis Industries received training from LVD Strippit when it bought an Easy-Form® press brake from the company. Vice President of Sales and Marketing Elizabeth Victor and Chad Brazelton, product sales manager, press brakes and shears, explained how LVD Strippit conducts its training sessions.
“Press brakes are a complicated product. They seem straightforward, but they’re really not. There’s a lot to understand about press brakes, how they function, and how to perform the bending,” Victor said. “So the initial part of training is on the technical formulas: which materials you’re bending, which angles you’re trying to create, bend allowances, tolerances, springback … All these variables go into training on press brakes and sizing the machine appropriately.”
Brazelton said that the first thing the trainer does is to evaluate the experience and skill level of the operators, their applications, their bending techniques, and how the training can improve their processes. The training that is included with the brake purchase concentrates on the capabilities of that specific machine, the machine software, and touch controls. That training is conducted on-site, Brazelton said.
“You start your evaluation simply by discussing everything with the person you’re doing the training with, whether it be the purchasing agent, an operator, or the operations manager. So you’re going to start the conversation just by asking them about their experience, applications, and how they’re doing the bending.
“We’ll have them load some parts that they typically run, and we’ll run through the process of how to program the parts and make the press brake bend the parts that they want.”
If the fabricator also purchases the machine package with the off-line programming CADMAN-B software, the fabricator gets an additional three days of training, which is usually done at LVD Strippit’s facility in Akron, N.Y.
The CADMAN software suite is a full programming system for the design, production planning, automatic program generation, and management of unfolding, punching, laser cutting, and bending of sheet metal parts.
Louis Industries was not able to send its press brake personnel to Akron, so LVD performed the three-day training on CADMAN-B at Louis’ Paynesville plant. Two operators, the production manager, and one engineer participated in the training.
Brazelton and Lucas walked through the machine operation, including how to use the Easy-Form® Laser adaptive bending system it is equipped with.
“We taught them everything from the basics of bending to calibrating the machine to the training at a high level in the proper use of the Easy-Form,” Brazelton said.
The Easy-Form Laser is an angle measurement system, Victor explained. “So when you bend the part, it measures the angle. It’s designed so that you can get the correct angle from the first bending operation.” Brazelton added, “It’s a real-time measurement system. It feeds the measurements back to the control and makes automatic adjustments during the bend in real time to make sure the first bend is accurate.”
If, after training, operators are still having difficulties, LVD Strippit trainers will come back—either as a courtesy or as a service—and help them figure out where the gaps are, Brazelton said.
Hands-on Training
Louis said that one of the biggest advantages of having the OEM’s trainers do the training on-site is that operators can learn on their own equipment (see Figure 1). “I think anytime you can get the fabricators pushing the buttons, touching and feeling what they’re doing, it’s better. You can only simulate so much.
“A big part of training, of maintenance, of safety, and quality is making sure that this part of the tool, the tang, fits into the machine properly. It’s called ‘seating,’” Louis said.
He added that part of the training that is valuable is learning how to correct mistakes on their own machines.
“They might hit the wrong button. What do you do now? Oh, no big deal. The trainer will show them how to correct it, or will explain why it’s really important to do x, y, and z, or why not to do it this way. Are you checking the ball screws? Are you verifying the grease? Are you seating the tooling?
“When Steven Lucas was here for training, he spent a lot of time talking about things like this and just stressing the importance of taking that little extra time to verify it. And if it isn’t seated right, here’s what happens. Your rails start to warp. Your tool wears unevenly. You can get witness marks in your die.
“Normally it takes two years to be good out there, because you just have to experience it. You gotta make your mistakes. You have to be patient. You have to grin and bear it when you make a mistake. Hopefully, with this training, you limit their mistakes to something very small instead of something large and explosive,” Louis added.
Louis Industries, www.louisind.com
LVD Strippit, www.lvdgroup.com/us
Photography by Mark Peterson.
About the Author
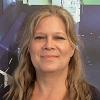
Kate Bachman
815-381-1302
Kate Bachman is a contributing editor for The FABRICATOR editor. Bachman has more than 20 years of experience as a writer and editor in the manufacturing and other industries.
Related Companies
subscribe now
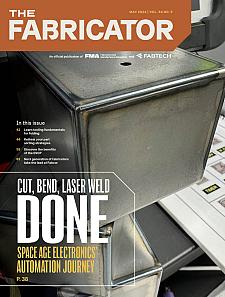
The Fabricator is North America's leading magazine for the metal forming and fabricating industry. The magazine delivers the news, technical articles, and case histories that enable fabricators to do their jobs more efficiently. The Fabricator has served the industry since 1970.
start your free subscription- Stay connected from anywhere
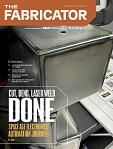
Easily access valuable industry resources now with full access to the digital edition of The Fabricator.
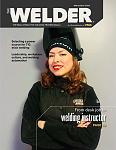
Easily access valuable industry resources now with full access to the digital edition of The Welder.
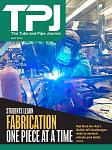
Easily access valuable industry resources now with full access to the digital edition of The Tube and Pipe Journal.
- Podcasting
- Podcast:
- The Fabricator Podcast
- Published:
- 04/16/2024
- Running Time:
- 63:29
In this episode of The Fabricator Podcast, Caleb Chamberlain, co-founder and CEO of OSH Cut, discusses his company’s...
- Trending Articles
Tips for creating sheet metal tubes with perforations
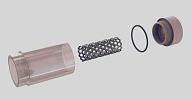
JM Steel triples capacity for solar energy projects at Pennsylvania facility
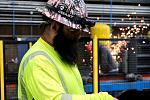
Are two heads better than one in fiber laser cutting?
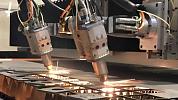
Supporting the metal fabricating industry through FMA
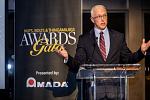
Omco Solar opens second Alabama manufacturing facility
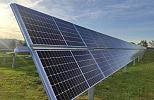
- Industry Events
16th Annual Safety Conference
- April 30 - May 1, 2024
- Elgin,
Pipe and Tube Conference
- May 21 - 22, 2024
- Omaha, NE
World-Class Roll Forming Workshop
- June 5 - 6, 2024
- Louisville, KY
Advanced Laser Application Workshop
- June 25 - 27, 2024
- Novi, MI