- FMA
- The Fabricator
- FABTECH
- Canadian Metalworking
Categories
- Additive Manufacturing
- Aluminum Welding
- Arc Welding
- Assembly and Joining
- Automation and Robotics
- Bending and Forming
- Consumables
- Cutting and Weld Prep
- Electric Vehicles
- En Español
- Finishing
- Hydroforming
- Laser Cutting
- Laser Welding
- Machining
- Manufacturing Software
- Materials Handling
- Metals/Materials
- Oxyfuel Cutting
- Plasma Cutting
- Power Tools
- Punching and Other Holemaking
- Roll Forming
- Safety
- Sawing
- Shearing
- Shop Management
- Testing and Measuring
- Tube and Pipe Fabrication
- Tube and Pipe Production
- Waterjet Cutting
Industry Directory
Webcasts
Podcasts
FAB 40
Advertise
Subscribe
Account Login
Search
Ask the Stamping Expert: How do I calculate shear pressure when figuring stamping die tonnage?
- By Thomas Vacca
- March 9, 2016
- Article
- Bending and Forming
Q: I read the article “How can I reduce snap-through condition effects?” in the September/October 2012 STAMPING Journal®. If I understand the article correctly, you do not want to stagger the punches too much to prevent the stored energy from releasing before the next set of punches hit. If the intent is to reduce the energy release by picking up the shear pressure of the next set of punch impact, then wouldn’t you figure one-third of the material thickness (the point of fracture) minus 0.001 to 0.003 inch instead of full material thickness? Also, the article had a disclaimer that some people do not multiply the .3 factor and use that as a safety factor. One way or the other, it makes a big difference in the tonnage required to run a die. What is the most common or correct way to calculate shear pressure when figuring the tonnage of a stamping die?
A: You can search the Internet and find several ways to calculate shear pressure to determine the tonnage required for a particular stamping die using different compensation factors. Following is one technique for calculating the load for stamping any shape with a flat-faced punch and matching die insert:
P = L x t x S
Where:
P = Punch force in tons
L = Perimeter of stamped shape in inches
t = Material thickness in inches
S = Shear strength of material
I do not use the 0.3 factor. Our experience shows the formula will get you close. Another way to calculate the load when using shear angles on your punches is:
F = (P x T x S x f)
Where:
F = Punch force in tons
P = Perimeter of the stamped shape in inches
t = Thickness in inches
S = Shear strength of material
f = Factor between 0.5 and 0.95 when using punches with shear
Note that punch-to-die clearance, staggered punch lengths, and angular punch faces do not affect the overall total load requirement. They simply affect the distribution of the force required over a varying time period.
As an example, a stamping die may have 10 punches blanking 0.100-in.-thick steel. If all contact the steel at the same time, the press would have to exert 100 tons at a single moment in time to blank through. Assume that during piercing, the pierce slug fractures free from the strip at 50 percent of the material thickness. If you stagger the punches in 0.050-in. increments, each being 0.050 in. shorter than the next, then theoretically only one punch would be cutting at a time. It still takes the same force to blank each hole, and the total force required is additive for all 10 punches. Theoretically, though, the press needs to exert only 10 tons at any single point in time, but for 10 times longer.
The purpose of staggering the punches is to reduce the single impact spike in tonnage required, which in turn reduces the resulting shock wave and stress to the press frame and crank, minimizing flexing of the machine frame. This phenomenon is especially important in a C-frame press. Remember, vibration/lateral movement is the cause for carbide wear. Eliminate this and you will see two to 10 times the hits per service depending on the application. You can achieve similar results using shear angles on punches. Of course, punch penetration considerations and slug holding conditions in your tools will dictate just how far you can go with this.
You are correct when you state “you do not want to stagger the punches too much to prevent the stored energy from releasing before the next set of punches hit.” If you have 30 percent shear, then the punch stagger would be about 24 percent of material thickness. Under the right circumstances, this can have a major effect on the service life of the tooling.
Remember that lubrication, proper tooling materials, minimized vibration, and robust tool guidance are essential for maximizing hits between services.
About the Author
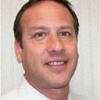
Thomas Vacca
Micro Co.
Has a shop floor stamping or tool and die question stumped you? If so, send your questions to kateb@thefabricator.com to be answered by Thomas Vacca, director of engineering at Micro Co.
Related Companies
subscribe now
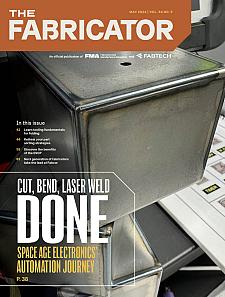
The Fabricator is North America's leading magazine for the metal forming and fabricating industry. The magazine delivers the news, technical articles, and case histories that enable fabricators to do their jobs more efficiently. The Fabricator has served the industry since 1970.
start your free subscription- Stay connected from anywhere
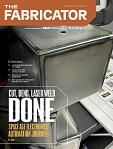
Easily access valuable industry resources now with full access to the digital edition of The Fabricator.
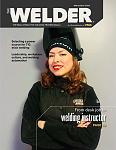
Easily access valuable industry resources now with full access to the digital edition of The Welder.
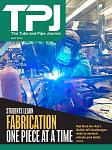
Easily access valuable industry resources now with full access to the digital edition of The Tube and Pipe Journal.
- Podcasting
- Podcast:
- The Fabricator Podcast
- Published:
- 04/16/2024
- Running Time:
- 63:29
In this episode of The Fabricator Podcast, Caleb Chamberlain, co-founder and CEO of OSH Cut, discusses his company’s...
- Trending Articles
Tips for creating sheet metal tubes with perforations
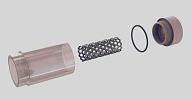
Are two heads better than one in fiber laser cutting?
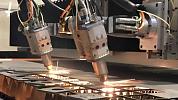
Supporting the metal fabricating industry through FMA
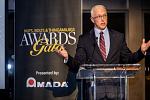
JM Steel triples capacity for solar energy projects at Pennsylvania facility
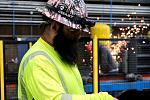
Omco Solar opens second Alabama manufacturing facility
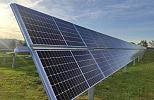
- Industry Events
16th Annual Safety Conference
- April 30 - May 1, 2024
- Elgin,
Pipe and Tube Conference
- May 21 - 22, 2024
- Omaha, NE
World-Class Roll Forming Workshop
- June 5 - 6, 2024
- Louisville, KY
Advanced Laser Application Workshop
- June 25 - 27, 2024
- Novi, MI