- FMA
- The Fabricator
- FABTECH
- Canadian Metalworking
Categories
- Additive Manufacturing
- Aluminum Welding
- Arc Welding
- Assembly and Joining
- Automation and Robotics
- Bending and Forming
- Consumables
- Cutting and Weld Prep
- Electric Vehicles
- En Español
- Finishing
- Hydroforming
- Laser Cutting
- Laser Welding
- Machining
- Manufacturing Software
- Materials Handling
- Metals/Materials
- Oxyfuel Cutting
- Plasma Cutting
- Power Tools
- Punching and Other Holemaking
- Roll Forming
- Safety
- Sawing
- Shearing
- Shop Management
- Testing and Measuring
- Tube and Pipe Fabrication
- Tube and Pipe Production
- Waterjet Cutting
Industry Directory
Webcasts
Podcasts
FAB 40
Advertise
Subscribe
Account Login
Search
Ask the Stamping Expert: Achieving a consistently formed cup without wrinkling
Blank holding pressure, press condition, and raw material all play a role
- By Thomas Vacca
- September 9, 2021
- Article
- Bending and Forming
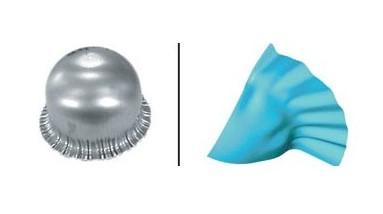
When forming in a progressive die, blank holding pressure, press condition, and raw material all affect the ability to achieve consistent drawing results without wrinkling.
Q: We are drawing a cup from 304 grade stainless steel. In the first station of our progressive die, we draw to around 0.75 in. deep. When I check the flange perimeter of the blank for thickness, there can be a difference of as much as 0.003 in. from one side to the other. It is not the same on every hit and does not come out in the same location. I was told this has something to do with the raw material processing, possibly being the outermost edge of the master coil. How can we achieve a consistently formed cup without wrinkling?
A: I see two concerns raised with your question: First is the variation you are getting in the draw process, and second is the raw material and its specifications.
The first concern speaks to fundamental tooling design flaws, so let’s review the basics. The intermittent wrinkling on the cup flanges and variation in thickness after the draw indicate that the tooling blank holder in the draw station of your progressive die is insufficient. Without seeing your tooling design, I will have to assume your draw punch and die radii and their respective clearances meet all standard design parameters.
In drawing, the blank is held between the draw die and the blank holder while the draw punch draws the material into the draw die, pulling it around the draw radius to form the shell. There is great friction between the die and the blank holder. During this process, the material suffers a lateral compression, which is the reason for wrinkling and radial elongation while the blank holder is resisting the flow of material. If the holding pressure is too high, the material will fracture under the pulling force of the draw punch. If it’s too low, wrinkling will occur.
There is a limit between the shell diameter and the blank diameter that cannot be exceeded for a successful draw operation. This limit varies depending on the elongation percentage of the material. The general rule is 55% to 60% for the first draw, followed by 20% for each draw thereafter. Figure 1 shows the standard formula for calculating the blank holding pressure required in a draw (I always add at least 30% additional force as a safety factor. You can decrease it if needed, but it’s hard to increase it after the design is completed).
Blank holding pressure p is 2.5 N/mm2for steel, 2.0 to 2.4 N/mm2for copper alloy, and 1.2 to 1.5 N/mm2for aluminum alloy.
The variation in the flange thickness also indicates that your tool design is not robust enough. Your die shoe must be thick enough to handle the draw forces without flexing. Your support under the die shoe must be solid steel, and the tooling guide pins must be big enough to prevent any lateral movement of top and bottom tooling during drawing.
Also take a look at your press. If the press guide gibs are worn and sloppy, it won’t matter how robust your tooling is—you won’t be successful. Inspect the press ram and make sure it is true and square for the entire stroke length of the press. Verify that your draw lubricant is filtered and well-maintained, and that the application volume and nozzle positions to the tooling are fixed. Fully inspect all tooling to print to ensure surface finish, coatings, and symmetry are correct. And pay special attention to the draw radii; they must be perfect in geometry and surface finish.
Also, while customers tend to see 304L and standard 304 as interchangeable, 304L is a better choice for drawing. The L stands for low carbon, which gives 304L a 0.2% yield strength of 35 KSI, compared to 304’s 0.2% yield strength of 42 KSI. With this 16% lower yield strength, 304L requires less force to yield during forming and to set a formed shape. It’s just easier to work with.
Last, make sure your raw material specification to your mill spells out “draw quality.”
About the Author
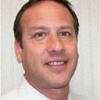
Thomas Vacca
Micro Co.
Has a shop floor stamping or tool and die question stumped you? If so, send your questions to kateb@thefabricator.com to be answered by Thomas Vacca, director of engineering at Micro Co.
subscribe now
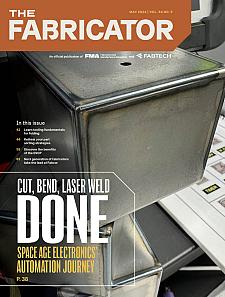
The Fabricator is North America's leading magazine for the metal forming and fabricating industry. The magazine delivers the news, technical articles, and case histories that enable fabricators to do their jobs more efficiently. The Fabricator has served the industry since 1970.
start your free subscription- Stay connected from anywhere
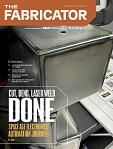
Easily access valuable industry resources now with full access to the digital edition of The Fabricator.
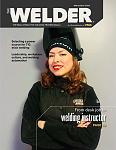
Easily access valuable industry resources now with full access to the digital edition of The Welder.
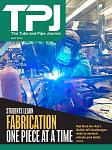
Easily access valuable industry resources now with full access to the digital edition of The Tube and Pipe Journal.
- Podcasting
- Podcast:
- The Fabricator Podcast
- Published:
- 04/16/2024
- Running Time:
- 63:29
In this episode of The Fabricator Podcast, Caleb Chamberlain, co-founder and CEO of OSH Cut, discusses his company’s...
- Trending Articles
Tips for creating sheet metal tubes with perforations
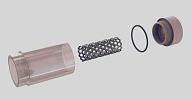
Are two heads better than one in fiber laser cutting?
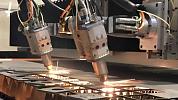
Supporting the metal fabricating industry through FMA
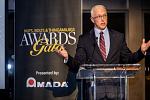
JM Steel triples capacity for solar energy projects at Pennsylvania facility
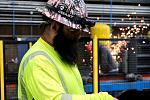
Omco Solar opens second Alabama manufacturing facility
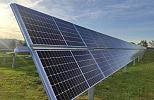
- Industry Events
16th Annual Safety Conference
- April 30 - May 1, 2024
- Elgin,
Pipe and Tube Conference
- May 21 - 22, 2024
- Omaha, NE
World-Class Roll Forming Workshop
- June 5 - 6, 2024
- Louisville, KY
Advanced Laser Application Workshop
- June 25 - 27, 2024
- Novi, MI