- FMA
- The Fabricator
- FABTECH
- Canadian Metalworking
Categories
- Additive Manufacturing
- Aluminum Welding
- Arc Welding
- Assembly and Joining
- Automation and Robotics
- Bending and Forming
- Consumables
- Cutting and Weld Prep
- Electric Vehicles
- En Español
- Finishing
- Hydroforming
- Laser Cutting
- Laser Welding
- Machining
- Manufacturing Software
- Materials Handling
- Metals/Materials
- Oxyfuel Cutting
- Plasma Cutting
- Power Tools
- Punching and Other Holemaking
- Roll Forming
- Safety
- Sawing
- Shearing
- Shop Management
- Testing and Measuring
- Tube and Pipe Fabrication
- Tube and Pipe Production
- Waterjet Cutting
Industry Directory
Webcasts
Podcasts
FAB 40
Advertise
Subscribe
Account Login
Search
Ask the Stamping Expert: Helpful tips for tool and die apprentices
- By Thomas Vacca
- February 13, 2020
- Article
- Bending and Forming
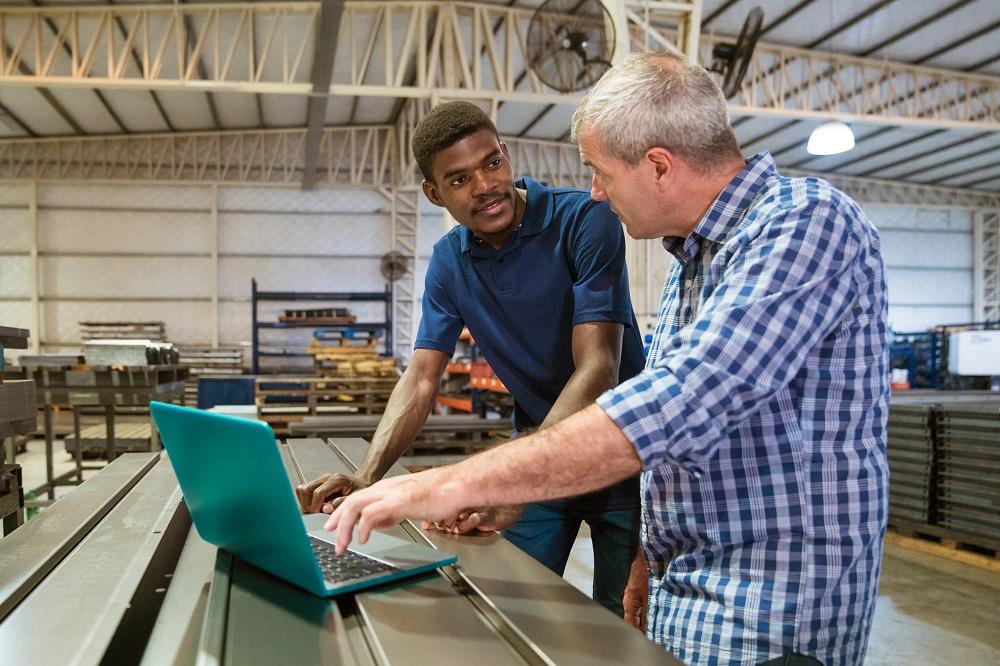
Newcomers and trainees in the tooling industry only know what they know, and that can cause many problems, including wasted time, damaged equipment and workpieces, and even injury to themselves and others. Getty Images
Over the years I have had the opportunity to observe the work of many tool and die apprentices during their training. From those observations, I’ve collected the following bits of advice. Some may seem obvious, but all newcomers and trainees in the tooling industry only know what they know, and that can cause many problems, including wasted time, damaged equipment and workpieces, and even injury to themselves and others.
Learn From Their Mistakes
Maintain Your Computer Skills. Computers are becoming more and more a part of all toolroom equipment. In our toolroom, the lathes, mills, jig grinders, jig borers, and grinders are CNC, and you likely have a similar setup. It only promises to become more technical with time.
Learn to Use Your Indicator. I often see trainees who don’t use an indicator because they don’t know a good way to fixture it to take a measurement. Actually, indicators can be used in an infinite number of ways to measure very accurately. Try to keep the indicator plane in line with the indicator. This will yield the most reliable measurement method. And use a minimal amount of preload on the tip so that you can move on and off the work plane with little risk of shifting the zero setting.
Wear Safety Glasses, Not Gloves. Gloves and loose clothing around machinery are killers! They can easily snag on rotating spindles. New apprentices learn dozens of safety rules, including wearing the proper shoes and pants, tight-sleeved shirts, safety glasses, and no ties. In my opinion, the two most important rules are don’t wear gloves while operating machinery and always wear your glasses (with side shields) in the shop.
Don’t Use the Support Table on Your Disc Sander When Deburring Thin Plates. I have seen the plate get sucked into the small opening between the disc and the support, which pulls the apprentice’s thumbs into the disc. Hold your plate above the support table. Apprentices should practice how they plan to execute an operation on a piece of equipment. Mount the stock in the machine and clamp and support it properly. Especially on lathe work, you may see you will need additional stock supports.
Be Careful With Compressed Air. Be aware of the dangers that compressed air presents to you and those around you. Again, keep your glasses on. Do not use full line pressure to clean off parts you are holding in your hand. Never use air to blow chips off a machine. And be aware of the people working around you—you can easily blow debris across the room.
Quick Tips for the Inexperienced
Following are a few more common mistakes I see. These practices are second nature to an experienced journeyman, but not to an apprentice:
- Never hammer gauge pins.
- Don’t use a diamond wheel to grind steel—it gums up the wheel.
- Don’t use the granite surface as an anvil!
- Never ever use compressed air to blow off a grinder.
- Always pull when using a wrench if possible.
- When using an end mill for heavy roughing cuts, minimize the length of the mill that is exposed outside of the collet for maximum rigidity.
- Use masking tape to help keep a straight line when using letter and number stamps.
- Try using toilet paper to apply Dykem ink.
- Pay attention to safety, and especially watch out for your hands, eyes, and feet.
- Run edge finders at 800 to 1,200 RPM for optimal performance.
- Understand the difference between absolute and incremental measurement. *Use a drill press vise upside-down to hold round stock when using a band saw.
- When machining, aim to miss your dimensional goal to the safe side. You can always take off more material but it’s hard to put it back!
- Use a magnet to see if material is stainless steel.
- Know the countersink angle of your screw and match the tooling. Metric screws use 90 degrees, standard English screws use 82 degrees, and aircraft screws use 100 degrees.
- Know that a micron is a millionth of a meter.
- Stop milling if you are getting a lot of cutting smoke—it’s a sign you’re doing something wrong.
- Don’t stone the chuck on your grinder or any accurate machine surfaces with a brown stone—you can very quickly affect the flatness of very precise surfaces.
- Do ask questions! The more you know why and how things work, the better decisions you can make.
About the Author
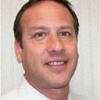
Thomas Vacca
Micro Co.
Has a shop floor stamping or tool and die question stumped you? If so, send your questions to kateb@thefabricator.com to be answered by Thomas Vacca, director of engineering at Micro Co.
subscribe now
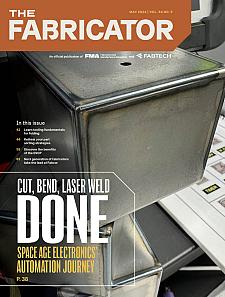
The Fabricator is North America's leading magazine for the metal forming and fabricating industry. The magazine delivers the news, technical articles, and case histories that enable fabricators to do their jobs more efficiently. The Fabricator has served the industry since 1970.
start your free subscription- Stay connected from anywhere
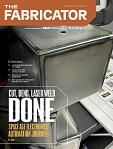
Easily access valuable industry resources now with full access to the digital edition of The Fabricator.
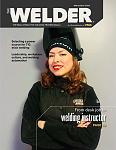
Easily access valuable industry resources now with full access to the digital edition of The Welder.
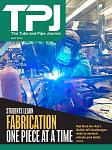
Easily access valuable industry resources now with full access to the digital edition of The Tube and Pipe Journal.
- Podcasting
- Podcast:
- The Fabricator Podcast
- Published:
- 04/16/2024
- Running Time:
- 63:29
In this episode of The Fabricator Podcast, Caleb Chamberlain, co-founder and CEO of OSH Cut, discusses his company’s...
- Trending Articles
Tips for creating sheet metal tubes with perforations
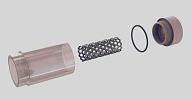
JM Steel triples capacity for solar energy projects at Pennsylvania facility
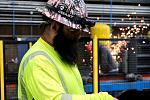
Are two heads better than one in fiber laser cutting?
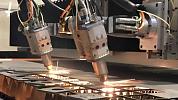
Supporting the metal fabricating industry through FMA
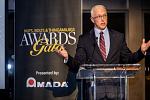
Omco Solar opens second Alabama manufacturing facility
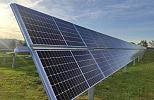
- Industry Events
16th Annual Safety Conference
- April 30 - May 1, 2024
- Elgin,
Pipe and Tube Conference
- May 21 - 22, 2024
- Omaha, NE
World-Class Roll Forming Workshop
- June 5 - 6, 2024
- Louisville, KY
Advanced Laser Application Workshop
- June 25 - 27, 2024
- Novi, MI