- FMA
- The Fabricator
- FABTECH
- Canadian Metalworking
Categories
- Additive Manufacturing
- Aluminum Welding
- Arc Welding
- Assembly and Joining
- Automation and Robotics
- Bending and Forming
- Consumables
- Cutting and Weld Prep
- Electric Vehicles
- En Español
- Finishing
- Hydroforming
- Laser Cutting
- Laser Welding
- Machining
- Manufacturing Software
- Materials Handling
- Metals/Materials
- Oxyfuel Cutting
- Plasma Cutting
- Power Tools
- Punching and Other Holemaking
- Roll Forming
- Safety
- Sawing
- Shearing
- Shop Management
- Testing and Measuring
- Tube and Pipe Fabrication
- Tube and Pipe Production
- Waterjet Cutting
Industry Directory
Webcasts
Podcasts
FAB 40
Advertise
Subscribe
Account Login
Search
Ask the Stamping Expert: How can we minimize progressive tool development costs?
- By Thomas Vacca
- June 2, 2018
- Article
- Bending and Forming
Q: We build and run our progressive tools in-house for manufacturing a variety of stampings for the electronics and lighting industry. Our average tool cost is $35,000 to $60,000. The problem is that sometimes the development costs approach the tool costs. We spend many hours in re-engineering to get rid of problems. For example, the last tool we fabricated took about 12 weeks to build; then we spent another five weeks developing it and getting it to run at speed. During this time, we had several misfeeds, resulting in component repairs and replacements. So while we had estimated the in-house tool cost to be $38,000, we ended up spending another $23,500 on engineering, supervision, toolmaker, press, and setup costs and about $6,200 in purchases. How can we eliminate these cost overruns?
A: Sounds like you have a problem with your design process. If the design is robust, development time will be minimal. But if you don’t address these issues upfront and, for example, design your tool and safeties to prevent breakage in case of a misfeed, you will continue to spend way too much on die development.
Minimizing development time and costs is a daunting task that needs to be addressed over time; there is no quick fix. Here are seven things to take into consideration as you start to whittle away at development time. They often are overlooked in the tool design phase, and that can increase costs:
- Stock lace-up point. The stock lace-up point should be designed so you can lace up without creating half-slugs that can get stuck in the die and cause breakage.
- Press stroke. Have you minimized it? Running 200 strokes per minute with a 2-inch stroke is essentially the same as running 400 SPM with a 1-in. stroke.
- Slug controls. Be sure to put appropriate slug controls—such as slug notches in the die sections, vacuums, punch rooftops, and slug darts—into the design.
- Die features. Don’t try to skimp on die features, even if they increase cost. Sometimes beefing up the die shoe to prevent flexing, using larger-diameter guide pins, and adding some extra stations in the tool where you see significant risk is a very wise decision. It’s much better than trying to address robustness and adding a restrike station after the tool is built!
- Tool support. Review the press the tool will go into and make sure the press bolster opening will support the tool where work is being done. A tool flex of even a few thousandths of an inch is a common problem that leads to part variation. You might need a custom support plate under your die shoe.
- Sensors and stock support liners. These must be engineered in. Die designers often leave out feed-to-die support liners and buckle sensors and expect the pressroom to put something together. That’s a mistake. At the minimum, include a micron sensor to detect slug pulls, a misfeed sensor for stock feeding issues, a buckle sensor for stock infeed issues, and a loop sensor between the coil stock and press feed. If you can, build in part-out sensors as well.
- Checklist. Probably one of the most important keys to success is a progressive die design checklist. This checklist is a living document that will change with every die build so you can use it to make subsequent die builds more effective. After every build, sit with the team and discuss each problem that was addressed in development. What could you do differently in the design phase to eliminate the problem before it required development time? Here are some examples:
- Verify the flat blank, bend lines, and trim geometry.
- Add undercuts to reduce material bulging at bend lines.
- Define the start strip location to prevent generation of half-slugs on lace-up.
- Add an in-tool camber corrector if you are stamping a reeled strip off the die.
- Using computer-aided design software, complete an interference check on the punch, die, and stripper assemblies.
- Complete the proper calculations for forming and make sure the springs have sufficient pressure with an added safety margin.
- Address slug retention in every trim station.
- Mark plates and components as required with numbers or as front, back, left, and right.
- At a minimum, engineer all service items so they cannot be put in backwards or upside down.
- Make sure all rails, punches, and die sections have sufficient lead-ins.
- Add a form-qualifying station if the bend angle is difficult to achieve in one hit.
Our build checklist has hundreds of “lessons-learned” items accumulated over the years, and we review it before every die build. We just completed build on five new tools from 30 tons to 160 tons; we eliminated debug time on some of the tools and minimized it on others. Are we working really hard? No, not really. Are we working smart? Yes!
About the Author
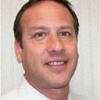
Thomas Vacca
Micro Co.
Has a shop floor stamping or tool and die question stumped you? If so, send your questions to kateb@thefabricator.com to be answered by Thomas Vacca, director of engineering at Micro Co.
subscribe now
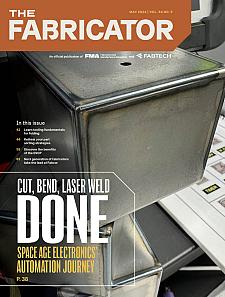
The Fabricator is North America's leading magazine for the metal forming and fabricating industry. The magazine delivers the news, technical articles, and case histories that enable fabricators to do their jobs more efficiently. The Fabricator has served the industry since 1970.
start your free subscription- Stay connected from anywhere
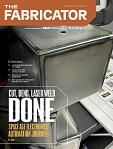
Easily access valuable industry resources now with full access to the digital edition of The Fabricator.
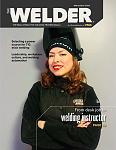
Easily access valuable industry resources now with full access to the digital edition of The Welder.
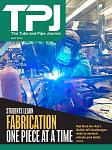
Easily access valuable industry resources now with full access to the digital edition of The Tube and Pipe Journal.
- Podcasting
- Podcast:
- The Fabricator Podcast
- Published:
- 04/16/2024
- Running Time:
- 63:29
In this episode of The Fabricator Podcast, Caleb Chamberlain, co-founder and CEO of OSH Cut, discusses his company’s...
- Trending Articles
Tips for creating sheet metal tubes with perforations
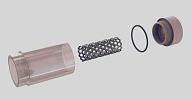
Supporting the metal fabricating industry through FMA
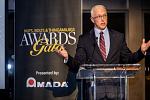
JM Steel triples capacity for solar energy projects at Pennsylvania facility
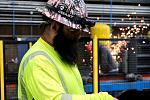
Are two heads better than one in fiber laser cutting?
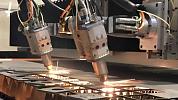
Fabricating favorite childhood memories
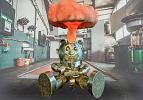
- Industry Events
16th Annual Safety Conference
- April 30 - May 1, 2024
- Elgin,
Pipe and Tube Conference
- May 21 - 22, 2024
- Omaha, NE
World-Class Roll Forming Workshop
- June 5 - 6, 2024
- Louisville, KY
Advanced Laser Application Workshop
- June 25 - 27, 2024
- Novi, MI