- FMA
- The Fabricator
- FABTECH
- Canadian Metalworking
Categories
- Additive Manufacturing
- Aluminum Welding
- Arc Welding
- Assembly and Joining
- Automation and Robotics
- Bending and Forming
- Consumables
- Cutting and Weld Prep
- Electric Vehicles
- En Español
- Finishing
- Hydroforming
- Laser Cutting
- Laser Welding
- Machining
- Manufacturing Software
- Materials Handling
- Metals/Materials
- Oxyfuel Cutting
- Plasma Cutting
- Power Tools
- Punching and Other Holemaking
- Roll Forming
- Safety
- Sawing
- Shearing
- Shop Management
- Testing and Measuring
- Tube and Pipe Fabrication
- Tube and Pipe Production
- Waterjet Cutting
Industry Directory
Webcasts
Podcasts
FAB 40
Advertise
Subscribe
Account Login
Search
Ask the Stamping Expert: How do manufacturers choose a prototype house?
In-house capabilities and consideration of product efficiency key to manufacturing process
- By Thomas Vacca
- December 12, 2019
- Article
- Bending and Forming
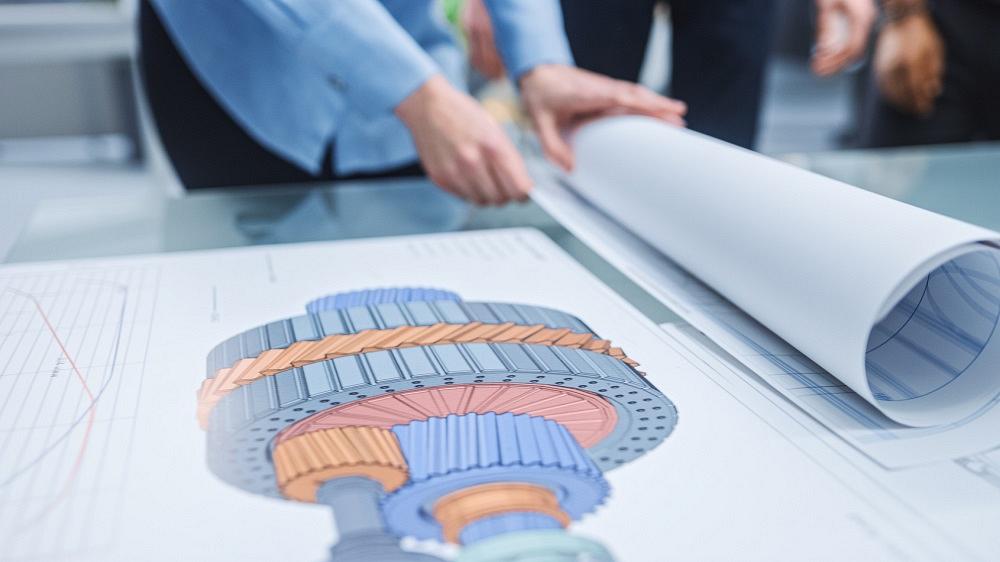
When picking a prototype shop, its capabilities to produce the whole part in-house are important to final part quality for manufacturers. But the shop also needs to be able to design a part that can be made quickly and cost-effectively on the production line. Getty Images
Q: We manufacture cardiovascular diagnostic equipment. Often we need prototypes—mostly small metal components and simple assemblies. What should I look for in a prototype manufacturer?
A: When sourcing a prototyping house, look first at its capabilities as they relate to the services you require. If you need a simple, straightforward part, then you might be concerned with only one or two competencies.
For example, let’s say you need a stainless steel disk, 1 inch in diameter and 0.050 in. thick. You might not care how it’s made or how you’ll use the component in your testing lab. But given that you work in the medical arena, even with this simple example, you might find burrs that are not acceptable. So machining the prototype might not be acceptable unless the prototyping shop also has deburring capabilities, since machining almost always produces a burr.
Then you might need parts serialized. Does the shop have laser marking capabilities? Let’s say you have a tube that needs laser-cut features. Laser cutting brings up the need for pickling to remove slag, inherent in the laser cutting process. And do you need passivation to prevent oxidation over time?
As you can see, even a simple part isn’t really simple. A comprehensive prototype house ideally will have all the process capabilities required to supply your component or assembly. Of course, you can get a quality part even if your prototype house doesn’t have all these capabilities, since the shop can outsource those processes. But the risk for quality problems tends to rise proportionally as the number of subcontracted processes increases.
In general, a best-in-class prototyping house will have as many of the following characteristics as possible:
- Complete in-house production capabilities to support 99 percent of your manufacturing process needs. One-stop shopping ensures your supplier has control over all the steps required in the prototyping process (see Figure 1).
- Contract manufacturing capabilities. A prototype house that is also a contract manufacturer will understand that a prototyped part needs to be duplicated cost-effectively in production. I can’t tell you how many times my colleagues in the industry have been “bit in the behind” when they have received prototypes that were produced in a way that wasn’t suitable for mass production or that didn’t meet federal regulation standards. At that point, they go back to square one in the development process.
- Very good documentation practices. A prototype manufacturer must understand the need to use control plans and sufficiently document the precise manufacturing process. Only the shops that produce medical components and assemblies for the medical device industry can really appreciate and guide you through the minutia of the extremely complicated medical regulations that are required for production components. If you don’t care about this and just want to see if something works, then you can make it any way you want. But if you are looking for a prototype that works and plan to scale up manufacturing immediately, then you need to be careful. Find out what the process flow will look like, what the controls are and if they’re robust and repeatable, whether the processes will be statistically capable, and if the part will be cost-effective in high-volume production quantities.
So, when choosing a prototyping shop, consider what you want in the prototype and, just as importantly, think about the next steps. A prototype manufacturer can guide you through the process and deliver a part that exceeds expectations, but make sure it also has developed the most cost-effective and efficient manufacturing processes while designing in the highest quality capabilities.
About the Author
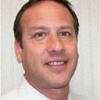
Thomas Vacca
Micro Co.
Has a shop floor stamping or tool and die question stumped you? If so, send your questions to kateb@thefabricator.com to be answered by Thomas Vacca, director of engineering at Micro Co.
subscribe now
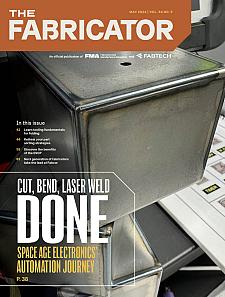
The Fabricator is North America's leading magazine for the metal forming and fabricating industry. The magazine delivers the news, technical articles, and case histories that enable fabricators to do their jobs more efficiently. The Fabricator has served the industry since 1970.
start your free subscription- Stay connected from anywhere
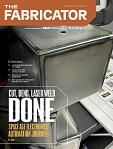
Easily access valuable industry resources now with full access to the digital edition of The Fabricator.
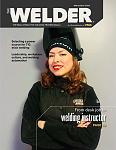
Easily access valuable industry resources now with full access to the digital edition of The Welder.
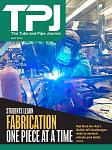
Easily access valuable industry resources now with full access to the digital edition of The Tube and Pipe Journal.
- Podcasting
- Podcast:
- The Fabricator Podcast
- Published:
- 04/16/2024
- Running Time:
- 63:29
In this episode of The Fabricator Podcast, Caleb Chamberlain, co-founder and CEO of OSH Cut, discusses his company’s...
- Trending Articles
Tips for creating sheet metal tubes with perforations
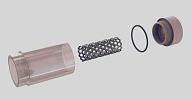
Supporting the metal fabricating industry through FMA
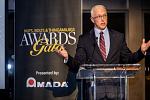
JM Steel triples capacity for solar energy projects at Pennsylvania facility
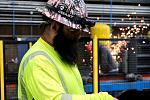
Are two heads better than one in fiber laser cutting?
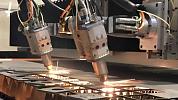
Fabricating favorite childhood memories
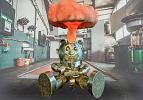
- Industry Events
16th Annual Safety Conference
- April 30 - May 1, 2024
- Elgin,
Pipe and Tube Conference
- May 21 - 22, 2024
- Omaha, NE
World-Class Roll Forming Workshop
- June 5 - 6, 2024
- Louisville, KY
Advanced Laser Application Workshop
- June 25 - 27, 2024
- Novi, MI