- FMA
- The Fabricator
- FABTECH
- Canadian Metalworking
Categories
- Additive Manufacturing
- Aluminum Welding
- Arc Welding
- Assembly and Joining
- Automation and Robotics
- Bending and Forming
- Consumables
- Cutting and Weld Prep
- Electric Vehicles
- En Español
- Finishing
- Hydroforming
- Laser Cutting
- Laser Welding
- Machining
- Manufacturing Software
- Materials Handling
- Metals/Materials
- Oxyfuel Cutting
- Plasma Cutting
- Power Tools
- Punching and Other Holemaking
- Roll Forming
- Safety
- Sawing
- Shearing
- Shop Management
- Testing and Measuring
- Tube and Pipe Fabrication
- Tube and Pipe Production
- Waterjet Cutting
Industry Directory
Webcasts
Podcasts
FAB 40
Advertise
Subscribe
Account Login
Search
Ask the Stamping Expert: Should I use stamping or machining to produce critical components?
- By Thomas Vacca
- October 10, 2018
- Article
- Bending and Forming
Q: What are the basic differences between stamping and machining for manufacturing critical components? What do I need to consider when choosing between the two?
A: Regardless of the final component’s end use—medical, automotive, electronics—there are many things to consider when choosing between stamping and machining.
Volume
The number of parts you are going to make is probably the biggest factor in your decision. While a stamping press can produce several million components a week, you would need 100 vertical mills to machine that many parts. For this kind of volume, your part must be designed for stamping.
You can pursue creative ways to address functional attributes you cannot achieve in one stamping. We once needed a specific cross-sectional strength, so we redesigned the part, built two stamping dies, and then laser welded the two parts together in a secondary operation. Another application required a ¼-inch-deep threaded hole to meet pull-out force requirements. We redesigned the part from thinner stock, stamped it, and welded an off-the-shelf nut in a secondary operation. Both cases eliminated the need for a machined component.
The key is to get design-for-manufacturability input from your stamping supplier as early as possible in the component design process.
On the other hand, if you need tolerances of +/-0.0005 in. and have volumes of three to 5,000 pieces a week, machining is the way to go. You don’t have the high up-front capital requirements of a stamping tool, plus the machining process generally is more versatile and more precise than stamping.
Tolerances
Stamping has come a long way in the past few years in achieving tight tolerances. You can stamp light-gauge parts with very fine features, holding tolerances of +/-0.001 in. In some cases you can stamp very fine-formed components holding tolerances of 0.0008 in.
Generally, the lighter the gauge and the smaller the part, the tighter the tolerances. In material up to 0.06 in. thick and 18 in. long, you can hold tolerances of +/-0.004 in. with stamping. Any larger than this and the ability to stamp the component depends on the part geometry.
Machining is much more forgiving of tight-tolerance parts. For tolerances of +/-0.0005 in., machining is the way to go.
Part Geometry
Part geometry is a make-or-break game changer. Some part shapes just cannot be stamped. For example, a part made of fullhard 304 stainless steel 1/8 in. thick with a hole that is 0.04 in. in diameter cannot be stamped. No punch material can take the load required to pierce that material at that diameter. In contrast, this part would be no problem to produce with machining.
Any part with geometry outside the raw stamping coil stock thickness needs to be formed or extruded, but there are physical limitations to the extent you can work the material to form features such as extrusions and gussets. The design must facilitate moving the base material to produce them. With machining, however, you can start with a larger billet and machine around these features, seemingly “adding” material to create the desired features. The accuracy of machining will surpass stamping and prevent you from having to make sacrifices on the part geometry.
Material Selection
In general you can stamp most red metals, stainless steels, titanium, and cold-rolled steel. However, the heavier the gauge and the higher the hardness, the more difficult it is to stamp them.
The medical components produced at my company are made from 302,304,17-4, and 17-7 stainless steel. We stamp all commercially available tempers, including full hard. In thicknesses up to 0.06 in., machining can work these same materials and tempers. With very thick blanks, machining is far more capable of creating tight-tolerance, complex shapes out of any of the materials that can be stamped.
Secondary Processes
Secondary processes need to be addressed on a case-by-case basis. They are not part of the machining-versus-stamping debate unless they are part of the up-front product design and made necessary by volume requirements.
Sometimes part geometry dictates the secondary process steps. For example, part geometry may allow you to passivate in bulk where required, or it might dictate the parts be racked for passivation. These are two very different cost drivers, regardless if the part is stamped or machined.
Stamping brings real value when you stamp the components, leave them on a carrier, and coil them onto reels. This lets you design automation for cleaning, plating, or performing a secondary operation such as welding on a threaded nut, adding a silver contact, laser marking, or sharpening.
Cost Targets and Up-front Capital Requirements
Cost targets and up-front capital requirements can be very different depending on volume. A high-volume (1 million per week) precision progressive stamping tool has a high initial cost but yields a very low piece-part cost and is the most economical method. A low-volume (1,000 per week) machining fixture has a very low initial cost but yields a higher piece-part cost. At low volumes, a progressive die cannot be justified.
About the Author
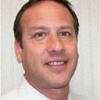
Thomas Vacca
Micro Co.
Has a shop floor stamping or tool and die question stumped you? If so, send your questions to kateb@thefabricator.com to be answered by Thomas Vacca, director of engineering at Micro Co.
subscribe now
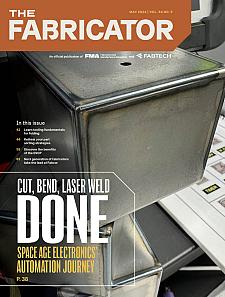
The Fabricator is North America's leading magazine for the metal forming and fabricating industry. The magazine delivers the news, technical articles, and case histories that enable fabricators to do their jobs more efficiently. The Fabricator has served the industry since 1970.
start your free subscription- Stay connected from anywhere
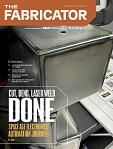
Easily access valuable industry resources now with full access to the digital edition of The Fabricator.
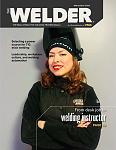
Easily access valuable industry resources now with full access to the digital edition of The Welder.
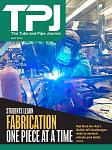
Easily access valuable industry resources now with full access to the digital edition of The Tube and Pipe Journal.
- Podcasting
- Podcast:
- The Fabricator Podcast
- Published:
- 04/16/2024
- Running Time:
- 63:29
In this episode of The Fabricator Podcast, Caleb Chamberlain, co-founder and CEO of OSH Cut, discusses his company’s...
- Trending Articles
Tips for creating sheet metal tubes with perforations
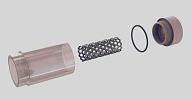
JM Steel triples capacity for solar energy projects at Pennsylvania facility
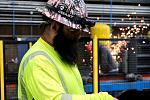
Are two heads better than one in fiber laser cutting?
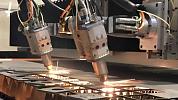
Supporting the metal fabricating industry through FMA
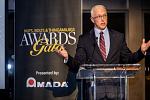
Omco Solar opens second Alabama manufacturing facility
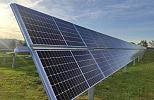
- Industry Events
16th Annual Safety Conference
- April 30 - May 1, 2024
- Elgin,
Pipe and Tube Conference
- May 21 - 22, 2024
- Omaha, NE
World-Class Roll Forming Workshop
- June 5 - 6, 2024
- Louisville, KY
Advanced Laser Application Workshop
- June 25 - 27, 2024
- Novi, MI