- FMA
- The Fabricator
- FABTECH
- Canadian Metalworking
Categories
- Additive Manufacturing
- Aluminum Welding
- Arc Welding
- Assembly and Joining
- Automation and Robotics
- Bending and Forming
- Consumables
- Cutting and Weld Prep
- Electric Vehicles
- En Español
- Finishing
- Hydroforming
- Laser Cutting
- Laser Welding
- Machining
- Manufacturing Software
- Materials Handling
- Metals/Materials
- Oxyfuel Cutting
- Plasma Cutting
- Power Tools
- Punching and Other Holemaking
- Roll Forming
- Safety
- Sawing
- Shearing
- Shop Management
- Testing and Measuring
- Tube and Pipe Fabrication
- Tube and Pipe Production
- Waterjet Cutting
Industry Directory
Webcasts
Podcasts
FAB 40
Advertise
Subscribe
Account Login
Search
Ask the Stamping Expert: Should we choose press speed based on productivity, or maintenance?
- By Thomas Vacca
- October 12, 2017
- Article
- Bending and Forming
Q: I work in a stamping facility in the Midwest. We have 40 high-speed stamping presses from 20 to 80 tons, with maximum speed of 800 strokes per minute (SPM). The actual speed at which the press should run is a constant battle between the toolroom supervisor and the production manager. The toolroom supervisor prefers the presses to run slower, claiming they “run better” at lower speeds. The production manager obviously wants to increase press speed and throughput. Any advice on how to balance speed versus maintenance?
A: I understand exactly the toolroom’s concerns. If a punch breaks while running a die at 200 SPM, it generally does less damage than if the same punch breaks while running at 800 SPM. The safety device that detects the punch break can stop the press more effectively at lower speeds than at higher speeds and prevent the press from making another hit. In fact, because of the inertia of the ram at very high speed, the press could make two more damaging hits even after the stop circuit is activated.
Another problem with running at high speed is that it makes setting the raw material feed more difficult. The feed has to be tweaked slightly as speeds increase because of inertia of the raw stock slipping through the feed rollers. At 800 SPM, raw material is fed more than 13 times per second!
Raw material payoffs, the straightener, and other auxiliary equipment used to support the production line must be set up and operated precisely, and this is simply more difficult at 800 SPM than at 200 SPM.
Another reason the toolroom will tend to run a stamping line more slowly is to compensate for nonrobust tool construction. You can maximize speed and accuracy only when using robust tooling. Design in extra-thick die shoes top and bottom, keeping the top weight to a minimum to minimize inertia when stopping. Install large roller guide pins, thick internal die plates, large surface area down stops, and a thick press bolster, with scrap and openings under the die minimized.
I have seen a 3-foot-long die with 2.0-in.-thick top and bottom die shoes, using four 1-in.-diameter guide pins on each corner, working 2.7-in.-wide by 0.045-in.-thick ½ hard stainless steel with oversized openings in the bolster so the working area of the die is not supported. A tool build and press setup like this cannot support the stamping without the tooling flexing and moving. All of these issues combine to make a recipe for production variation.
Running the press more slowly just makes it a little easier to run nonrobust tooling and presses that may have too much play in the guides and crankshaft.
But let’s assume the equipment is in good shape. When designing a progressive die build, be sure to follow these guidelines:
- Minimize strip lift. If the tool requires lifters, make sure they are as short as possible. This directly affects press stroke.
- Minimize pitch or feed length. The raw material is stationary at press bottom when stamping. As the press opens, the rollers need to begin feeding. The raw material has inertia and resists acceleration. If your feed window is one second, feeding 1 in. of material per second requires feeding at a speed 10 times greater than feeding 1/10 in. per second. The slower the feed (in inches per second), the less possibility of slippage.
- Minimize the press stroke. Press ram speed is not linear. The ram moves fastest at the 9 and 3 o’clock positions and comes to a stop at the 12 and 6 o’clock positions. If you reduce the ram stroke from 1.0 in. to 0.5 in., you can double the press SPM without changing ram speed.
- Make part ejection robust. Get the parts out of the die as soon as possible. For the most robust part ejection, blank the parts through the die. Removing parts on a carrier strip is the second best option. Blowing the parts out of the die is the slowest and least robust method.
When all is said and done, you always want to maximize the speed at which you run your stamping dies. And maximizing speed starts mainly in the design phase.
About the Author
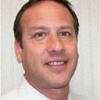
Thomas Vacca
Micro Co.
Has a shop floor stamping or tool and die question stumped you? If so, send your questions to kateb@thefabricator.com to be answered by Thomas Vacca, director of engineering at Micro Co.
Related Companies
subscribe now
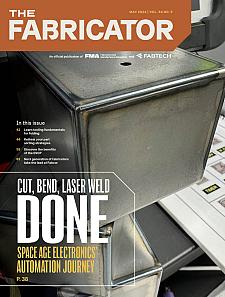
The Fabricator is North America's leading magazine for the metal forming and fabricating industry. The magazine delivers the news, technical articles, and case histories that enable fabricators to do their jobs more efficiently. The Fabricator has served the industry since 1970.
start your free subscription- Stay connected from anywhere
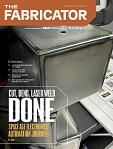
Easily access valuable industry resources now with full access to the digital edition of The Fabricator.
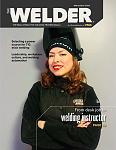
Easily access valuable industry resources now with full access to the digital edition of The Welder.
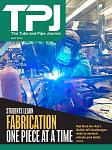
Easily access valuable industry resources now with full access to the digital edition of The Tube and Pipe Journal.
- Podcasting
- Podcast:
- The Fabricator Podcast
- Published:
- 04/16/2024
- Running Time:
- 63:29
In this episode of The Fabricator Podcast, Caleb Chamberlain, co-founder and CEO of OSH Cut, discusses his company’s...
- Trending Articles
Tips for creating sheet metal tubes with perforations
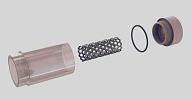
Are two heads better than one in fiber laser cutting?
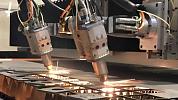
Supporting the metal fabricating industry through FMA
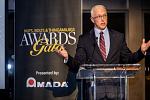
JM Steel triples capacity for solar energy projects at Pennsylvania facility
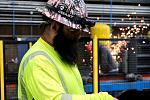
Omco Solar opens second Alabama manufacturing facility
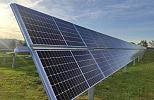
- Industry Events
16th Annual Safety Conference
- April 30 - May 1, 2024
- Elgin,
Pipe and Tube Conference
- May 21 - 22, 2024
- Omaha, NE
World-Class Roll Forming Workshop
- June 5 - 6, 2024
- Louisville, KY
Advanced Laser Application Workshop
- June 25 - 27, 2024
- Novi, MI