- FMA
- The Fabricator
- FABTECH
- Canadian Metalworking
Categories
- Additive Manufacturing
- Aluminum Welding
- Arc Welding
- Assembly and Joining
- Automation and Robotics
- Bending and Forming
- Consumables
- Cutting and Weld Prep
- Electric Vehicles
- En Español
- Finishing
- Hydroforming
- Laser Cutting
- Laser Welding
- Machining
- Manufacturing Software
- Materials Handling
- Metals/Materials
- Oxyfuel Cutting
- Plasma Cutting
- Power Tools
- Punching and Other Holemaking
- Roll Forming
- Safety
- Sawing
- Shearing
- Shop Management
- Testing and Measuring
- Tube and Pipe Fabrication
- Tube and Pipe Production
- Waterjet Cutting
Industry Directory
Webcasts
Podcasts
FAB 40
Advertise
Subscribe
Account Login
Search
Ask the Stamping Expert: What designs are available for in-die forming?
- By Thomas Vacca
- April 22, 2021
- Article
- Bending and Forming
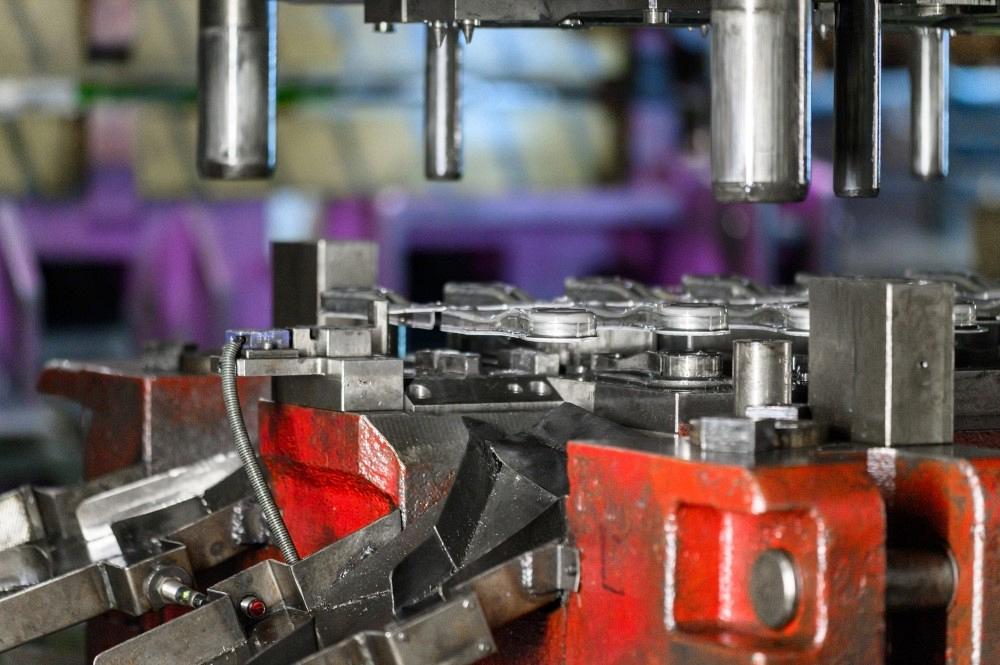
Ask the Stamping Expert columnist Tom Vacca presents four in-die forming designs for tweaking bends while the tool is in the press.
Q: I’m looking for an adjustable bend design to incorporate into a progressive stamping die. I want to be able to tweak the bends while the tool is in the press. Do you have any suggestions or reference material for assembly and design?
A: There are four commonly used in-die forming designs, each with its own advantages.
Pivot Die Cam Adjuster
In this fairly simple and inexpensive design, a forming punch that’s designed to pivot is mounted in the punch holder. A spring block is mounted next to the punch and maintains the punch in the open position when the die is open. For this you can use a Vlier pin or any homemade spring pusher. It only needs to be strong enough to hold the punch open. As the tool closes, the punch contacts the adjustable cam support on the die chase.
Although not shown in the figure, the top of the forming punch has a radius to allow it to pivot, but the adjustment cam can be mounted on a slide or designed so it can be removed in the press and shimmed. As the cam is adjusted vertically, it will force the bending punch to bend your part. Ideally, you want the angles on the punch and forming insert to be the same and the cam adjusted to hit home. As you back off the cam, you essentially will be air bending. It works fine for minor adjustments, but the variation will increase if you back it off more than a degree or two.
The Ready Bender
This is a brand-name, off-the-shelf tool produced by Ready Technology Inc. The design specs are basically done, so you can plug in your information and design it into your tool. The unit transfers the vertical movement of the press into a rotary forming motion, allowing you to overbend so you can compensate for springback. In my experience, in holding +/- 1 degree I’ve been able to maintain a consistent bend. This tool rolls around the bend line during forming, so on very abrasive materials, galling is not much of an issue.
The company says the tool runs at 250 strokes per minute (SPM), but we have run it significantly faster. It can hold a 1/2-degree angle and overbend up to 135 degrees. The tool tolerates minor variations in material thickness and requires less tonnage than other bending designs.
Cam Slide Form Adjustment
We often use this design to qualify or set the final angle required after bending a part at 90 degrees. Because of springback, some final tweaking is necessary, so we mount the cam punch in the punch holder and install a punch wedge behind it. This can be changed out for wear. The adjustment slide sits behind it so it can be moved up or down to adjust the bend. The 0.015-in. shim keeps the punch taut on the wedge to prevent it from flopping up and down with each press stroke. In addition, a keeper prevents the punch from falling out if the shim gives way.
Then we mount the cam slide in the die chase spring-loaded in the open position, allowing the cam punch to drive it in with each press stroke. Since the part is prebent, we limit the travel of the cam slide to about 0.010 in. to run at speeds up to 800 SPM.
This design is a little more complex than the others, but it’s an accurate, consistent way to adjust a 90-degree bend on-the-fly.
Radius for Springback
In some cases, we have a little extra tolerance on the angle, but it cannot be open or over 90 degrees. Adding the radius on the bending die is a great—and very often overlooked—little trick.
This design is cheap, not complex, and can run at speeds up to 1,000 SPM. When the tooling is closed, the wipe by forms the bend at 90 degrees. In the center of the part, we have ground a shallow radius. When the tool opens, the radius relaxes and the 90-degree bends move in, compensating for springback and giving you 90-degree bends in one shot.
Make sure the pressure pad does not hit home and is spring-loaded just enough to bend the part but not set the form. Note that the radius does not show up on the final part.
About the Author
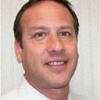
Thomas Vacca
Micro Co.
Has a shop floor stamping or tool and die question stumped you? If so, send your questions to kateb@thefabricator.com to be answered by Thomas Vacca, director of engineering at Micro Co.
subscribe now
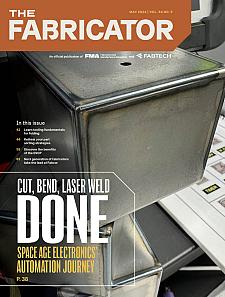
The Fabricator is North America's leading magazine for the metal forming and fabricating industry. The magazine delivers the news, technical articles, and case histories that enable fabricators to do their jobs more efficiently. The Fabricator has served the industry since 1970.
start your free subscription- Stay connected from anywhere
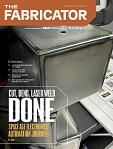
Easily access valuable industry resources now with full access to the digital edition of The Fabricator.
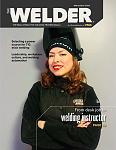
Easily access valuable industry resources now with full access to the digital edition of The Welder.
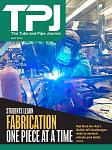
Easily access valuable industry resources now with full access to the digital edition of The Tube and Pipe Journal.
- Podcasting
- Podcast:
- The Fabricator Podcast
- Published:
- 04/16/2024
- Running Time:
- 63:29
In this episode of The Fabricator Podcast, Caleb Chamberlain, co-founder and CEO of OSH Cut, discusses his company’s...
- Trending Articles
Tips for creating sheet metal tubes with perforations
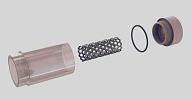
Supporting the metal fabricating industry through FMA
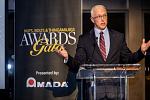
JM Steel triples capacity for solar energy projects at Pennsylvania facility
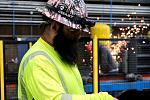
Are two heads better than one in fiber laser cutting?
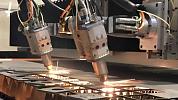
Fabricating favorite childhood memories
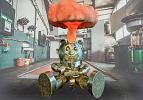
- Industry Events
16th Annual Safety Conference
- April 30 - May 1, 2024
- Elgin,
Pipe and Tube Conference
- May 21 - 22, 2024
- Omaha, NE
World-Class Roll Forming Workshop
- June 5 - 6, 2024
- Louisville, KY
Advanced Laser Application Workshop
- June 25 - 27, 2024
- Novi, MI