- FMA
- The Fabricator
- FABTECH
- Canadian Metalworking
Categories
- Additive Manufacturing
- Aluminum Welding
- Arc Welding
- Assembly and Joining
- Automation and Robotics
- Bending and Forming
- Consumables
- Cutting and Weld Prep
- Electric Vehicles
- En Español
- Finishing
- Hydroforming
- Laser Cutting
- Laser Welding
- Machining
- Manufacturing Software
- Materials Handling
- Metals/Materials
- Oxyfuel Cutting
- Plasma Cutting
- Power Tools
- Punching and Other Holemaking
- Roll Forming
- Safety
- Sawing
- Shearing
- Shop Management
- Testing and Measuring
- Tube and Pipe Fabrication
- Tube and Pipe Production
- Waterjet Cutting
Industry Directory
Webcasts
Podcasts
FAB 40
Advertise
Subscribe
Account Login
Search
Ask the Stamping Expert: What kind of raw material feed is best?
- By Thomas Vacca
- July 27, 2018
- Article
- Bending and Forming
Q: We are setting up a new stamping line and debating which type of raw material feed would be best. Can you give us some guidance?
A: Raw material feeds come in three styles: mechanical, air-driven, and servo-driven. If this is a “one feed needs to fit all” situation, I recommend my personal favorite—a servo feed.
Servo Feeds
While servo feeds can be the more expensive option, depending on the model, they are very versatile, handling a variety of stock thicknesses and widths. Servo feeds also can be programmed for individual jobs, so you don’t need to set up the feed on changeover. Just pull up the program and the pitch (the length of the coil stock fed on every press cycle), and the pilot release is preset. Some models can store up to 200 programs.
Servo feeds also are relatively fast. Of course, speed is a function of the pitch setting: the longer the pitch, the more time you need to feed, which affects the press’s speed. Even so, for speeds up to 600 or even 800 strokes per minute (SPM) on very short pitches, they can do the job very well.
With servo feeds you get a virtually infinitely adjustable feed cycle. So for instance, if you are doing in-die tapping and the strip is free to move only for 90 degrees of the press cycle, you can program this on the servo feed. It will affect the speed somewhat because you have to feed your pitch in a shorter time frame, but by the same token, if you can use 220 degrees of the press cycle, you have a longer time to feed your raw material and can run faster.
Another great feature is the ability to microadjust the pitch while the press is running to fine-tune the progression. And a third great option is the zigzag feeder, which feeds the strip not only left to right but front to back. This feeding action can reduce webbing between parts, saving as much as 13 percent of raw material. Speed increases with both axes moving at the same time, and parts are nested in the die strip, resulting in a shorter pitch.
Finally, one of the biggest benefits of a servo feed is that it senses the force required to feed the material. If your stamping die is running and you pull a slug, or you are in-die tapping and you break a tap, or a punch breaks and gets stuck in the die strip and die section, the die strip probably won’t be able to advance. When the servo feed senses a spike in the force required to feed the die strip, it will stop and pull back to the previous pitch. That way, if the press does not stop before making the next hit, you will not have a misfeed that is off-pitch. This can save many thousands of dollars in broken tooling.
Air Feeds
Air feeds are a reliable, very cost-effective choice. I have run coil stock from 0.005 to 0.060 inch thick and 0.375 to 5.0 in. wide successfully up to 400 SPM, although this isn’t their limitation. They are not as accurate as servo or mechanical feeds, but often the stamping tool pilots are sufficient to make up for slight variations in feed length. This tends to occur when the force to pull the coil stock varies because of changing loop control conditions at the infeed.
The biggest issue I have found with air feeds is timing them. There is an inherent lag because they are air-driven. As you speed up the press, you have to advance the signal to feed. I have run jobs at 400 SPM with the signal to feed set just before bottom dead center of the stroke—and that was when the punches were still in the raw material. With that lag time, feeding actually occurred around 270 degrees on the press cycle. There is an art to timing the feeds perfectly at higher speeds, and it can be challenging to lace up at low speed since the feed is so far ahead that it wants to drive the coil stock while the tool is still closed.
Mechanical Feeds
I have no experience with purchasing a mechanical feed and retrofitting it to a press, because with the top-quality, high-speed presses we run, the builder supplies the mechanical feeds. But in my experience using them, they are by far the fastest and most accurate feeds.
Mechanical feeds can run more than 2,000 SPM given the right conditions. We regularly run 1,200 SPM on light-gauge material at a pitch of 0.590 in. I do not believe servos can compete in this arena!
About the Author
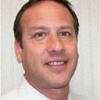
Thomas Vacca
Micro Co.
Has a shop floor stamping or tool and die question stumped you? If so, send your questions to kateb@thefabricator.com to be answered by Thomas Vacca, director of engineering at Micro Co.
subscribe now
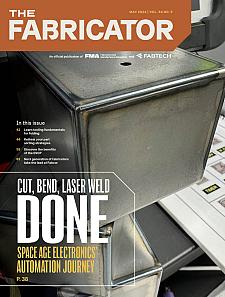
The Fabricator is North America's leading magazine for the metal forming and fabricating industry. The magazine delivers the news, technical articles, and case histories that enable fabricators to do their jobs more efficiently. The Fabricator has served the industry since 1970.
start your free subscription- Stay connected from anywhere
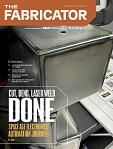
Easily access valuable industry resources now with full access to the digital edition of The Fabricator.
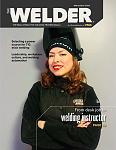
Easily access valuable industry resources now with full access to the digital edition of The Welder.
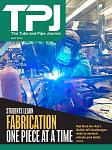
Easily access valuable industry resources now with full access to the digital edition of The Tube and Pipe Journal.
- Podcasting
- Podcast:
- The Fabricator Podcast
- Published:
- 04/16/2024
- Running Time:
- 63:29
In this episode of The Fabricator Podcast, Caleb Chamberlain, co-founder and CEO of OSH Cut, discusses his company’s...
- Trending Articles
Tips for creating sheet metal tubes with perforations
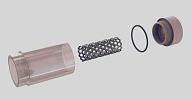
Supporting the metal fabricating industry through FMA
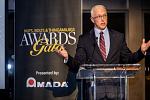
JM Steel triples capacity for solar energy projects at Pennsylvania facility
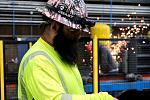
Are two heads better than one in fiber laser cutting?
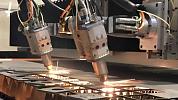
Fabricating favorite childhood memories
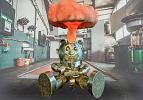
- Industry Events
16th Annual Safety Conference
- April 30 - May 1, 2024
- Elgin,
Pipe and Tube Conference
- May 21 - 22, 2024
- Omaha, NE
World-Class Roll Forming Workshop
- June 5 - 6, 2024
- Louisville, KY
Advanced Laser Application Workshop
- June 25 - 27, 2024
- Novi, MI