- FMA
- The Fabricator
- FABTECH
- Canadian Metalworking
Categories
- Additive Manufacturing
- Aluminum Welding
- Arc Welding
- Assembly and Joining
- Automation and Robotics
- Bending and Forming
- Consumables
- Cutting and Weld Prep
- Electric Vehicles
- En Español
- Finishing
- Hydroforming
- Laser Cutting
- Laser Welding
- Machining
- Manufacturing Software
- Materials Handling
- Metals/Materials
- Oxyfuel Cutting
- Plasma Cutting
- Power Tools
- Punching and Other Holemaking
- Roll Forming
- Safety
- Sawing
- Shearing
- Shop Management
- Testing and Measuring
- Tube and Pipe Fabrication
- Tube and Pipe Production
- Waterjet Cutting
Industry Directory
Webcasts
Podcasts
FAB 40
Advertise
Subscribe
Account Login
Search
Ask the Stamping Expert: Which method of slug control is best? Part II
- By Thomas Vacca
- March 26, 2019
- Article
- Bending and Forming
In the January/February 2019 issue we discussed the many mechanical ways to control slugs. Now we’ll delve further into the topic, exploring the use of vacuum generators—also known as bazookas—for slug control.
Bazookas come in many sizes. We commonly use one that has a ¾ inch outside diameter (OD) by about 3 in. long, with about a ½-in. inside diameter (ID). We have also used units that are 2.5 in. OD and 6 in. long with a very large ID.
The ID is important, because bazookas are pass-through units. That means the slug you are sucking out of the tool has to pass through the ID with some clearance.
Bazookas require compressed air to create suction, and they are much stronger than building airflow into the progressive tool to create suction.
Whenever you are forced (by design) to have a partial cut slug and cannot contain the slug in the die section, the bazooka is a great solution. You will need to be creative with the installation, though. If you slide a die onto the bed of the press, you will have to crawl under the machine to access the bottom of the die shoe to connect the bazooka. Usually we make a subplate that we set up in the press first, drop in our bazookas from the top, and then slide the die onto the subplate. We use two T-handle dowels that pass through the die shoe into the subplate to guarantee alignment. Also, the dowel locations are offset so you can install only one way.
Tips for Success
Here are two very important points to remember:
1. The exit hose from the bazooka will guide the slug to a receptacle under the press. If the slugs are small and light, you will find them blowing everywhere you don’t want them. You can build a screened basket to capture the slugs and allow plenty of venting for the air to escape to eliminate back pressure.
2. You need an uninterrupted opening in the air path through the entire press cycle. When the tool is at dead bottom, the punch cannot be the exact same geometry as the die (minus some cutting clearance). Grind a slot on the side of the punch where you are not cutting the partial slug to allow significant air to flow at all times. If you do not allow enough airflow, there will be no vacuum as your punch pulls out of the die. You have a split second to get the air flowing again, and this is where you need the vacuum most.
Bazooka Versus In-die Air
You can also design in this type of slug control by drilling holes in the top of the die chase backup plate that break into the slug opening wall very close to the bottom of the opening. Try drilling the holes at a 30-degree angle and channel air feed to these holes. Make sure the air feed path is sealed and perfectly symmetrical to each of the holes. All holes must be symmetrically placed and the same size. Again, you can build a screened basket to capture the slugs, and you need to provide plenty of air venting.
In my experience, I’ve never been able to get as much vacuum with in-die air as with using a bazooka. But the in-die method does have advantages: Machined-in tool vacuums don’t get lost, they are permanently installed, and you can’t put them on backward. With either method, though, if the slugs get packed in the bottom of the tool or if the exit hole for the slugs gets covered or clogged, the air will reverse direction and blow up into the die—and that’s a big problem!
About the Author
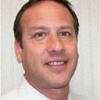
Thomas Vacca
Micro Co.
Has a shop floor stamping or tool and die question stumped you? If so, send your questions to kateb@thefabricator.com to be answered by Thomas Vacca, director of engineering at Micro Co.
subscribe now
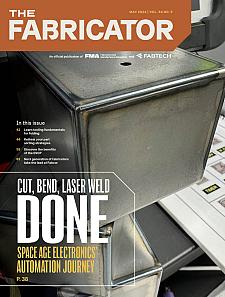
The Fabricator is North America's leading magazine for the metal forming and fabricating industry. The magazine delivers the news, technical articles, and case histories that enable fabricators to do their jobs more efficiently. The Fabricator has served the industry since 1970.
start your free subscription- Stay connected from anywhere
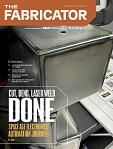
Easily access valuable industry resources now with full access to the digital edition of The Fabricator.
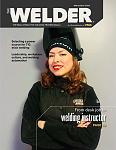
Easily access valuable industry resources now with full access to the digital edition of The Welder.
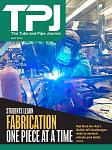
Easily access valuable industry resources now with full access to the digital edition of The Tube and Pipe Journal.
- Podcasting
- Podcast:
- The Fabricator Podcast
- Published:
- 04/16/2024
- Running Time:
- 63:29
In this episode of The Fabricator Podcast, Caleb Chamberlain, co-founder and CEO of OSH Cut, discusses his company’s...
- Trending Articles
Tips for creating sheet metal tubes with perforations
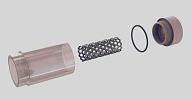
JM Steel triples capacity for solar energy projects at Pennsylvania facility
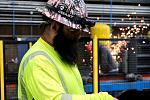
Are two heads better than one in fiber laser cutting?
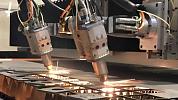
Supporting the metal fabricating industry through FMA
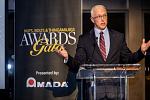
Omco Solar opens second Alabama manufacturing facility
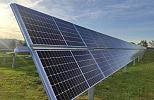
- Industry Events
16th Annual Safety Conference
- April 30 - May 1, 2024
- Elgin,
Pipe and Tube Conference
- May 21 - 22, 2024
- Omaha, NE
World-Class Roll Forming Workshop
- June 5 - 6, 2024
- Louisville, KY
Advanced Laser Application Workshop
- June 25 - 27, 2024
- Novi, MI