Contributing editor
- FMA
- The Fabricator
- FABTECH
- Canadian Metalworking
Categories
- Additive Manufacturing
- Aluminum Welding
- Arc Welding
- Assembly and Joining
- Automation and Robotics
- Bending and Forming
- Consumables
- Cutting and Weld Prep
- Electric Vehicles
- En Español
- Finishing
- Hydroforming
- Laser Cutting
- Laser Welding
- Machining
- Manufacturing Software
- Materials Handling
- Metals/Materials
- Oxyfuel Cutting
- Plasma Cutting
- Power Tools
- Punching and Other Holemaking
- Roll Forming
- Safety
- Sawing
- Shearing
- Shop Management
- Testing and Measuring
- Tube and Pipe Fabrication
- Tube and Pipe Production
- Waterjet Cutting
Industry Directory
Webcasts
Podcasts
FAB 40
Advertise
Subscribe
Account Login
Search
Compound tools stamp precise, thin materials in a complex world
Stamping flat, round parts compounded by volume, simplified by tool design
- By Kate Bachman
- January 24, 2018
- Article
- Bending and Forming
Washers, shims, seals, gaskets, and spacers. Round, flat parts, 6 inches in diameter and smaller. Nothing could be simpler to stamp, right?
But what if 75 percent of your clients are in the aerospace, medical, and industrial segments and have extremely precise requirements for dimensions, concentricity, and flatness to meet stringent industry certifications?
And what if they only need short-run quantities, so your changeovers cannot last longer than 45 minutes and your trial times must be nonexistent?
To complicate matters further, what if you service 25 new clients every month and build 10 new tools and have 50 tool setups and job completions every day?
Factor in the problems that are innate with stamping thin-gauge materials—sometimes as thin as foil—and that simple math just got algebraic.
That is the dizzying pace and those are some of the short-run challenges that Phoenix Specialty Mfg. Co., Bamberg, S.C., encounters every day. The company, founded in 1907, has had time to figure it out. It is 111 years old this year.
Short-run, First-run Success
Phoenix Specialty specializes in short- to medium-run production. “We define our niche as from one piece to about 250,000 pieces per year,” said President Pat Moloney.
Aerospace is the largest customer base segment, comprising about 50 percent of the business. General industry, which includes pumps, electric motors, pneumatic cylinders, flowmetering devices, and valves is the next largest customer segment; medical is the third, Moloney added.
“Our customers in those segments typically have low annual volumes,” said Vice President of Sales and Marketing Russell Hurst, who is a fourth-generation member of the family-owned company. “The average work order in our shop is right at about 10,000 pieces. So in our short-run world, first-run success is what it’s all about.”
Operations Manager Steve Cornforth explained. “If you’re doing million-piece runs, you can have longer setups, but our internal target is for our changeovers to be under 45 minutes, from last good piece to first good piece. We don’t have a trial time. We’re doing an average of 48 to 51 setups and job completions per day. That puts us right at about 500,000 pieces a day and about 150 new parts a month. So we’re basically in the setup business.”
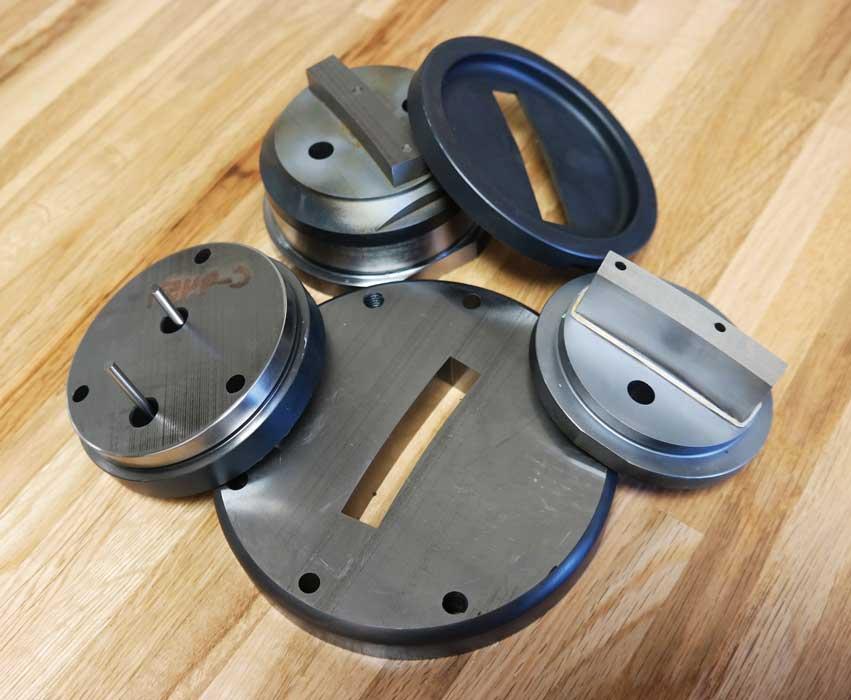
One way that stamping manufacturer Phoenix Specialty Mfg. Co. meets the demand for multiple short-run jobs per day making very precise flat and circular parts is by using compound die sets with interchangeable tooling. The company re-engineered its master die set, which it calls next-generation tooling, to substantially simplify changeover.
“We have to punch it once, do it right, and move on to the next job,” Hurst added. “That’s the only way this company succeeds. On short-run jobs, you have to keep moving forward. It’s like running on a treadmill.”
At industry networking events, the managers hear other stamping manufacturers tell tooling stories that are quite different from theirs. “People in other companies will say, ‘We ran off 10 new tools last year,’” Moloney said. “That’s such a different business model. In our world, we’re doing almost 10 new tools every day. Phoenix has over 20,000 different dies in inventory—all built to meet a specific customer’s requirements.
That’s the short-run world. These parts come in, they’ve got a finite life to them, and then they’re gone.”
Meeting Demands With Compound Tooling …
One way that the stamping manufacturer meets the demand for multiple short-run jobs a day making very precise flat and circular parts is by using compound die sets with interchangeable tooling.
“Phoenix uses compound tooling almost exclusively,” said Hurst. Compound tooling consists of a stand-alone die set that is set up in a stamping press, he explained. Compound tooling is different than progressive tooling because in compound tooling, all piercing, shearing, and forming are completed in a single hit of the tool. With progressive tooling, the strip of material may be punched multiple times as it progresses through the die to form the completed part (see Figure 1).
Stamping a part’s ID and OD simultaneously eliminates distortion. It also enhances concentricity, which is critical for most of the washers and shims that the company manufactures for its customers in the aerospace, medical, and energy segments. “We find that on a number of our customers’ prints, they’ll spec a maximum for concentricity,” Hurst said. “Some of our customers produce components for lithium-ion batteries, and it seems that concentricity is extremely critical for their applications, as well as the flatness.”
Phoenix Specialty had been using a master die set concept for its compound tooling developed in the early ’80s, but it had shortcomings. The original master die set’s components had to be manually aligned during assembly. While the original dies served the company well for many years, the company wanted a more precise die set that was easier to assemble, and would give them a competitive advantage with very thin materials. “The company brought in a team of consultants to help develop and design a more modern master die set,” Moloney said.
… and Next-generation Master Die Sets
The outside consultants and in-house engineering and production groups worked for months designing the current master die sets, which Phoenix calls next-generation tooling (NGT). “The reason we can build so many new tools so quickly is that we have designed proprietary master die sets with interchangeable components. We wanted the die set to be easier for our people to assemble and manufacture because we’re making those five components every day,” Moloney said.
“The way the tooling works is that by changing out five components, we can completely change which parts that die is running,” Cornforth said. The five tool components are (see lead image)
- Punch
- Knockout
- Bushing (also called button by some)
- Stripper insert
- Die plate
NGT Result: Reliability
The redesign not only completely changed the way the stamper manufactures its tooling components, it completely changed the reliability of the dies.
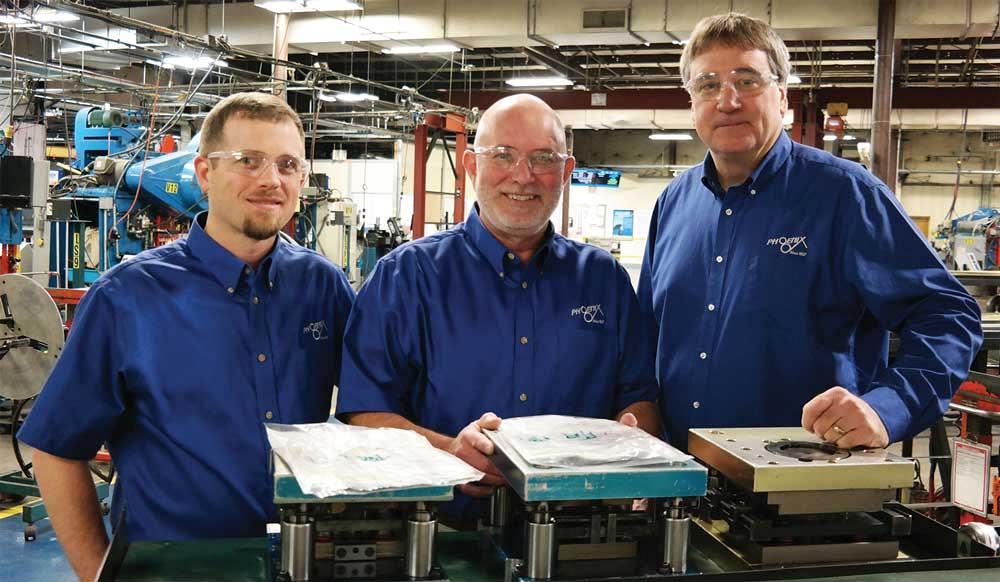
Phoenix Specialty Mfg. Co. Vice President of Sales Russell Hurst, Operations Manager Steve Cornforth, and President Pat Moloney (left to right) manage the 111-year-old, 100-employee, $20 million annual sales stamping manufacturing company which services 25 new clients every month, builds 10 new tools every day, and has 50 tool setups and job completions daily.
“In the change from the old style of Phoenix dies to the NGT, our die reliability has gone up by our internal metrics somewhere around 40 percent,” Cornforth said. “The way we calculate reliability is from the moment the tooling leaves the machine shop, the tooling components can be assembled into the master die sets and run the entire production order without ever having to come out of the press. We call that first-run success, and that is significantly higher with the NGT.”
No Charge for Tooling
Phoenix Specialty doesn’t charge for its tooling. “Typically, we don’t add any tooling charges,” Hurst said. “We quote our customers a piece price for a stamped part. The reason is that the consumable tooling for round, flat parts is such a small piece of the total equation. These five components literally fit in the palm of your hand. They probably require less than 5 pounds of tool steel.
“We’re able to be very competitive at the lower-volume parts without a stand-alone tooling charge.”
Make Tooling Without Toolmaker Skill Set
The stamping manufacturer produces, warehouses, and ships the parts it stamps from its Bamberg headquarters.
The facility is located in a rural area where it is hard to find employees who have a wealth of expertise in tooling. However, the company hires talented individuals and trains them for six months to a year to gain the skills and expertise they need to successfully produce and assemble the Phoenix NGT. Phoenix’s in-house toolroom produces the consumable NGT die components, and the components are installed in the master die sets right in the pressroom by a group of die assemblers.
“So, at the die assembly table, our operators are taking these master die sets, removing the old tooling, inserting the new tooling, tightening it down, and putting it in the press,” Moloney said.
“We’re able to run successfully without having many traditional tool and die people in our shop. We’ve been successful with a less demanding skill set because it’s a very standardized component, and a standardized process. That’s critical to our business,” Hurst said.
It requires six months to a year for the assemblers to get quick and accurate at assembling the die set, Cornforth said.
Thin-gauge Material
Hurst said that Phoenix Specialty’s proprietary compound tooling gives the company an edge over its competitors in stamping very thin-gauge metal. “A lot of our competitors struggle to stamp under 0.004-inch-thick material. The thinnest that we currently stamp is a 0.0005-in.-thick beryllium copper sheet. We stamp 0.001-in.-thick material every day [see Figure 2].
“That has to do with the next-gen tooling set that we designed. It is more precise,” Hurst said.
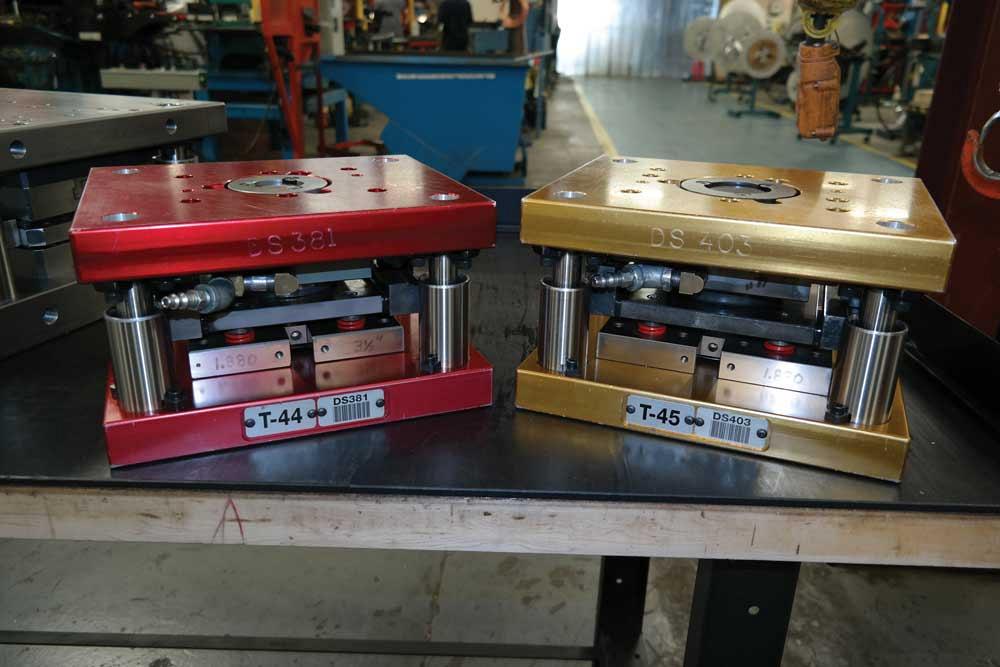
Figure 1
Using compound tooling, all piercing, shearing, and forming is completed in a single hit of the tool. That type of tooling is especially useful for stamping washers, shims, seals, gaskets, and spacers.
Cornforth said that the No. 1 challenge in stamping thin-gauge material is burr. Although parts made of thick-gauge material can be tumbled to remove burr, parts made of thin-gauge cannot. “Our customers expect a burr-free part. If there’s any burr, you can’t remove it. With thin-gauge parts, what you stamp is what’s going in the box.
“To stamp a burr-free part in thin-gauge metal, that’s where the alignment, the concentricity, and die clearance are absolutely critical.”
Better Fit, Better Impression
The die components are designed with a slip fit. “You almost have to push them together, they’re so tight,” Cornforth said. “What’s nice about the Phoenix NGT system is that the die plate has a slip fit to the knockout; the knockout has a slip fit to the punch. So the concentricity at the top is almost perfect because of this slip-fit, self-aligning design.”
“For the concentricity and flatness requirements of our customers, the self-aligning system is unbeatable,” Hurst added.
Cornforth said that aligning the master die sets and the components that go into those die sets—the fits and finishes—has to be exact. “They have to be really tight so you don’t create a burr. So it’s a testament to our master die set design, our machine shop that creates these dies, and the assemblers of those sets that this works. It’s not just one thing. If we’re missing one piece of the puzzle, we cannot make it.
“Again, proper assembly of the master die set, and inserting the die set into the press, all are very critical to stamping that part.”
Maintenance
Cornforth considers the company’s master die set maintenance program to be essential to production success. “Performing maintenance to the pins, the bearings, and the sleeves and ensuring that the die set is aligned are absolutely critical. We check the components on the CMM [coordinate measuring machine] to make sure that they are all lined up with each other,” he said. S
Photos courtesy of Phoenix Specialty Mfg. Co., www.phoenixspecialty.com.
About the Author
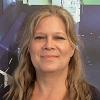
Kate Bachman
815-381-1302
Kate Bachman is a contributing editor for The FABRICATOR editor. Bachman has more than 20 years of experience as a writer and editor in the manufacturing and other industries.
subscribe now
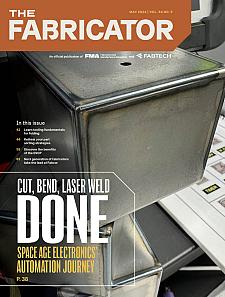
The Fabricator is North America's leading magazine for the metal forming and fabricating industry. The magazine delivers the news, technical articles, and case histories that enable fabricators to do their jobs more efficiently. The Fabricator has served the industry since 1970.
start your free subscription- Stay connected from anywhere
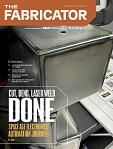
Easily access valuable industry resources now with full access to the digital edition of The Fabricator.
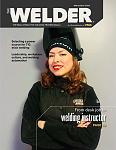
Easily access valuable industry resources now with full access to the digital edition of The Welder.
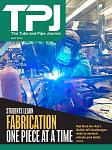
Easily access valuable industry resources now with full access to the digital edition of The Tube and Pipe Journal.
- Podcasting
- Podcast:
- The Fabricator Podcast
- Published:
- 04/16/2024
- Running Time:
- 63:29
In this episode of The Fabricator Podcast, Caleb Chamberlain, co-founder and CEO of OSH Cut, discusses his company’s...
- Trending Articles
Tips for creating sheet metal tubes with perforations
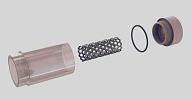
JM Steel triples capacity for solar energy projects at Pennsylvania facility
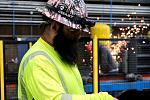
Are two heads better than one in fiber laser cutting?
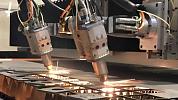
Supporting the metal fabricating industry through FMA
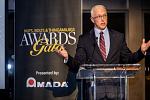
Omco Solar opens second Alabama manufacturing facility
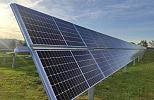
- Industry Events
16th Annual Safety Conference
- April 30 - May 1, 2024
- Elgin,
Pipe and Tube Conference
- May 21 - 22, 2024
- Omaha, NE
World-Class Roll Forming Workshop
- June 5 - 6, 2024
- Louisville, KY
Advanced Laser Application Workshop
- June 25 - 27, 2024
- Novi, MI