Contributing Writer
- FMA
- The Fabricator
- FABTECH
- Canadian Metalworking
Categories
- Additive Manufacturing
- Aluminum Welding
- Arc Welding
- Assembly and Joining
- Automation and Robotics
- Bending and Forming
- Consumables
- Cutting and Weld Prep
- Electric Vehicles
- En Español
- Finishing
- Hydroforming
- Laser Cutting
- Laser Welding
- Machining
- Manufacturing Software
- Materials Handling
- Metals/Materials
- Oxyfuel Cutting
- Plasma Cutting
- Power Tools
- Punching and Other Holemaking
- Roll Forming
- Safety
- Sawing
- Shearing
- Shop Management
- Testing and Measuring
- Tube and Pipe Fabrication
- Tube and Pipe Production
- Waterjet Cutting
Industry Directory
Webcasts
Podcasts
FAB 40
Advertise
Subscribe
Account Login
Search
Die Science: Die maintenance felonies and misdemeanors
- By Art Hedrick
- October 13, 2017
- Article
- Bending and Forming
In my 36-year career in the tool and die industry, I have seen amazing metal forming and cutting techniques. I’ve also seen shops that make me wonder how in the world they ever even make a part. What a contrast! I have been in stamping shops so clean that you could almost eat off the floor, and I have been in stamping shops where I suspect the rats outnumber the employees.
Many of these companies had well-defined, precise, and efficient die maintenance programs to prevent mishaps in their presses. Others had die maintenance programs that were sufficient but not totally effective, and some shops had very little or no maintenance whatsoever. Even though many of these shops had a lot of people working in the toolroom, they were too busy performing die repair to focus on maintenance.
Unfortunately, some serious die maintenance violations are fairly common across the board. Some of these practices can end up causing catastrophic tooling damage and downtime. I will call these methods “felonies.” Other methods that are not quite as serious but still can result in tooling damage and downtime, I will call “misdemeanors.”
Top Four High Court Die Felonies
What are the most serious violations?
- Allowing Shims to Encroach into Slug-drop Areas. Shims should be designed to support the die section as completely as possible without encroaching into slug-drop or scrap-falling areas. If not, slugs can be trapped in the die and build up in the tool, eventually causing cutting and trimming sections to explode. More often than not, the broken sections get carried through the remainder of the tool, damaging the entire tool. I have seen entire progressive dies costing far more than $100,000 be completely destroyed because of a shim encroachment problem that could have been prevented with just an extra minute or two for daily inspection. Clearance holes for the screws and dowels should be large enough so that assembly is easy but not so large that they allow the shim to move outside of the cutting edge.
- Shimming a Ball Lock Punch Inside the Retainer. Ball lock retainers are designed so that the spring-loaded ball bearing fits precisely into a teardrop-shaped groove machined into the punch. The distance between the bottom of the punch and this groove is critical. If a shim is placed directly underneath the punch, it will not seat properly in the retainer, so the punch could fall out during a production run. If the punch falls out, it will likely be carried through the tool, causing further damage. Instead, the entire ball lock retainer assembly should be shimmed, with adequate clearance underneath the stripper or pressure pad for the additional retainer height (see Figure 1).
- Welding Air-hardened Tooling Sections Without Preheating Them. Although the results of this may not be immediate, welding on a section of air-hardened tool steel eventually will result in the tool steel section cracking or breaking. Welding on a cold piece of tool steel causes localized thermal expansion, most likely resulting in hydrogen embrittlement. The most common violation is welding on D-2, a common air-hardened tool steel.
- Allowing Cutting Punches to Pump up and Down Within the Retainer or Die. A piston-style movement of cutting punches within the retainer can result in catastrophic die damage. Although the pressure is on the bottom of the punch when it hits the material, once it breaks through, the forces exerted on the punch will reverse, which is called snap-through or reverse tonnage. The reverse tonnage often is very close to the same tonnage needed to perform the cutting, and it can literally rip the cutting punch out of the holder or retainer. It's not always the force that causes the failure, but the shock that the retainer must absorb during the transition from positive to negative tonnage. A cutting punch should fit precisely into a holder or retainer, and the bottom of the punch should be perfectly flush with the bottom of the retainer. Vertical cutting punch movement should be curtailed as much as possible.
Top Four Misdemeanors
- Cock Shimming. Cock shimming, also known as jimmy shimming, is the process of placing shims under one side of a die section, retainer, or component in an effort to relocate it or tighten up the clearance between it and another die section (see Figure 2). This technique often is used to relocate the position of a pierced hole or to tighten the bending clearance between forming sections. When a die section is cock shimmed, it is not fully supported and, therefore, prone to deflection and breakage. In addition, if the section is removed, the shims must be placed in the exact same position for the die section to be in the same, precise location. A much better choice is to take the time to move and realign the die sections correctly.
- Using a Ball Bearing, Ball Peen Hammer, or Prick Punch to Reduce the Size of a Dowel or Button Hole. This could be considered a diemaker’s trick for keeping dowels tight. Although it prevents the dowel from coming out, it also defeats the purpose of the dowel. The dowels in a section are meant to precisely locate the section on the die set or subplate assembly. If they are oversized, then they are not precisely locating the section. Instead, the section should be plugged and doweled again to solve the problem.
- Using an Excessive Number of Shims. A good die maintenance program should have a three-shim-maximum rule. Using an excessive number of thin shims under a die section makes it very spongy and subject to deflection. So instead of using eight 0.010-in. shims, the better choice is to use one each of 0.050-, 0.020-, and 0.010-in. shims.
- Using a Steel Hammer on Tool Steel Sections. Using a hardened steel hammer on a hardened tool steel die section can cause the section to chip, crack, and break. A dead-blow, shot-filled plastic hammer is a better choice, as are lead, soft brass, and aluminum hammers.
Don’t Do Time – Make Time
An ounce of prevention is worth a pound of cure. Saying “I don’t have time for proper die maintenance” is like saying “I don’t have time to change the oil in my car because I'm too busy driving it.” Crime doesn’t pay—not even in a stamping die.
About the Author
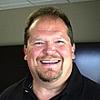
Art Hedrick
10855 Simpson Drive West Private
Greenville, MI 48838
616-894-6855
subscribe now
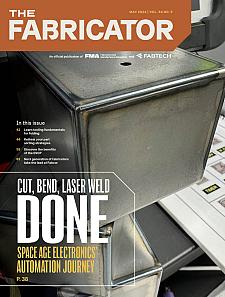
The Fabricator is North America's leading magazine for the metal forming and fabricating industry. The magazine delivers the news, technical articles, and case histories that enable fabricators to do their jobs more efficiently. The Fabricator has served the industry since 1970.
start your free subscription- Stay connected from anywhere
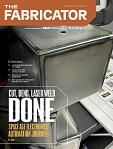
Easily access valuable industry resources now with full access to the digital edition of The Fabricator.
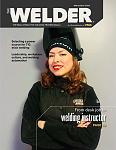
Easily access valuable industry resources now with full access to the digital edition of The Welder.
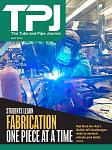
Easily access valuable industry resources now with full access to the digital edition of The Tube and Pipe Journal.
- Podcasting
- Podcast:
- The Fabricator Podcast
- Published:
- 04/16/2024
- Running Time:
- 63:29
In this episode of The Fabricator Podcast, Caleb Chamberlain, co-founder and CEO of OSH Cut, discusses his company’s...
- Trending Articles
Tips for creating sheet metal tubes with perforations
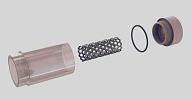
Are two heads better than one in fiber laser cutting?
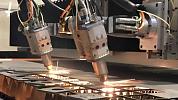
Supporting the metal fabricating industry through FMA
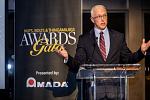
JM Steel triples capacity for solar energy projects at Pennsylvania facility
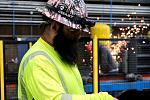
Omco Solar opens second Alabama manufacturing facility
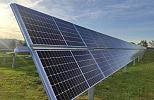
- Industry Events
16th Annual Safety Conference
- April 30 - May 1, 2024
- Elgin,
Pipe and Tube Conference
- May 21 - 22, 2024
- Omaha, NE
World-Class Roll Forming Workshop
- June 5 - 6, 2024
- Louisville, KY
Advanced Laser Application Workshop
- June 25 - 27, 2024
- Novi, MI