Contributing Writer
- FMA
- The Fabricator
- FABTECH
- Canadian Metalworking
Categories
- Additive Manufacturing
- Aluminum Welding
- Arc Welding
- Assembly and Joining
- Automation and Robotics
- Bending and Forming
- Consumables
- Cutting and Weld Prep
- Electric Vehicles
- En Español
- Finishing
- Hydroforming
- Laser Cutting
- Laser Welding
- Machining
- Manufacturing Software
- Materials Handling
- Metals/Materials
- Oxyfuel Cutting
- Plasma Cutting
- Power Tools
- Punching and Other Holemaking
- Roll Forming
- Safety
- Sawing
- Shearing
- Shop Management
- Testing and Measuring
- Tube and Pipe Fabrication
- Tube and Pipe Production
- Waterjet Cutting
Industry Directory
Webcasts
Podcasts
FAB 40
Advertise
Subscribe
Account Login
Search
Die Science: Tool steel made simple
How to pick the right tool steel for your stamping application
- By Art Hedrick
- December 18, 2019
- Article
- Bending and Forming
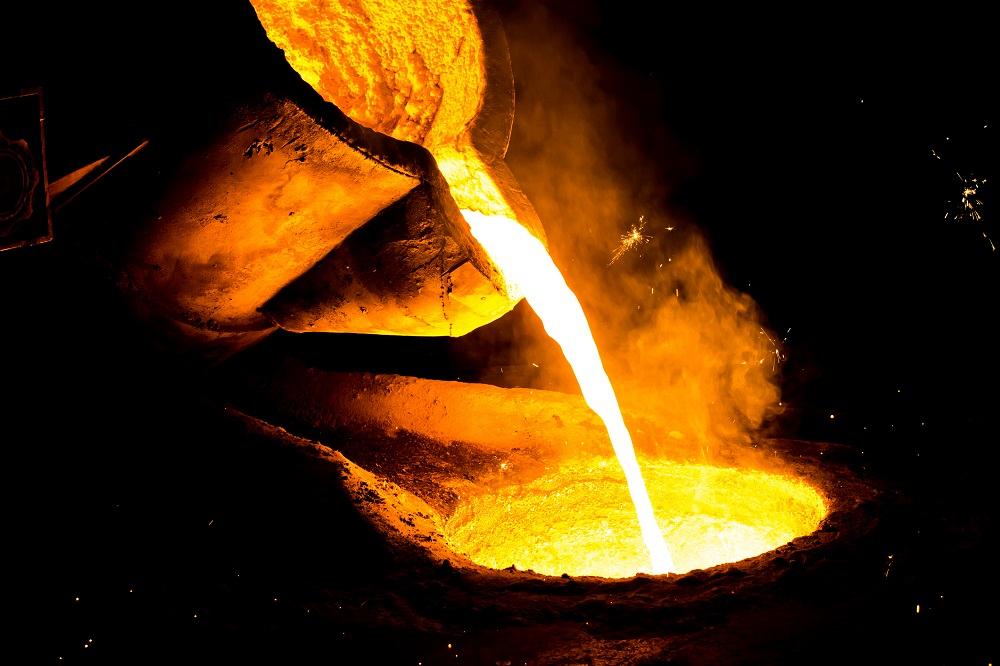
To choose the right tool steel, you need to determine what you expect from its performance, as defined by its mechanical properties and resistance to typical tool steel failures. Getty Images
I remember, as a young tool and die apprentice, sitting in my heat-treat and metallurgy class and listening to the instructor talk about iron carbon diagrams and pearlite diffusion transformation versus the martensite shear process. I spent some time using mini marshmallows and toothpicks to make a molecular structure that could be the cover image of a science magazine.
I must have looked like a deer in the headlights.
I was, to say the least, totally confused. I somehow managed to pass the class—not sure whether I should credit that to sympathy from my instructor or the exam answers I may or may not have written on my arm.
Although I did learn a little about metallurgy, we never discussed tool steel types or how to select the best tool steel for a given application. I guess we were too busy playing with our marshmallow molecules. I think the course would have been more helpful if my career was in steelmaking rather than steel end use.
In any case, as I gained more experience and understanding in the trade, I vowed never to try to explain metallurgy in a complex way. I was determined to make it simple, even though it’s really not—I still don’t understand it all. However, selecting the best tool steel for your application doesn’t have to be complicated.
What Is Tool Steel?
Tool steel is a ferrous metal—which means it contains iron—that has enough carbon in it to be heated to a certain temperature and cooled at a certain rate to increase its hardness. Although this is oversimplified, think of carbon as a chunk of coal. What happens to a chunk of coal when you expose it to intense heat and pressure for a million years? It becomes a diamond. Diamonds are the hardest known material. So the more carbon there is in the metal, the harder it will get when subjected to heating and cooling.
Tool steel contains more than carbon. It also contains alloys, which are homogeneous compounds added to tool steel to give it some of the alloy’s properties. Some add toughness, others add hardness, some increase wear resistance. Some alloys combine with others to make different compounds that give the tool steel different performance characteristics. The type and amount of alloys added to the tool steel are commonly referred to as its chemistry.
Tool steel most commonly is available in conventional and powdered metal styles. Both types contain certain amounts of alloys, but the process in which the tool steel is made is significantly different. Although more expensive, powdered metal tool steels typically outperform conventional tool steels.
What Is the Best Tool Steel?
You might as well ask, “What is the best car?” It really depends on what you intend to use the car for. A Ferrari is a great car if you’re trying to go fast on a paved surface, but it won’t do well in mud, whereas a 4WD SUV or truck would be the best choice in mud, but not on a racetrack.
To begin with, the main two properties to consider for tool steel are toughness—the ability to withstand severe impact shock—and wear resistance—the ability to resist abrasive wear. S-7, one of the most common types of tool steel, has very high toughness properties. Tool steels that have both high toughness and wear resistance are best suited for cutting applications that require them to adsorb the shock of cutting punch entry, as well as to withstand the abrasive rubbing that occurs during punch withdrawal.
In addition to considering those two main properties, you also need to determine what you expect from the tool steel’s performance, as defined by its mechanical properties and resistance to typical tool steel failures:
- Abrasive wear - Material being cut or formed sometimes contains elements that can erode the surface of the tool steel. Applications such as deep drawing require a tool steel with high wear resistance.
- Severe impact – Severe impact shock can cause cracking, denting, or deformation. Processes such as coining require a tool steel with high toughness to withstand these impacts.
- Adhesive wear - When the tool steel and the sheet material are not compatible or are metallurgically similar, microwelding or cold welding may be pulled out of the tool surface. Such a loss of material can result in significant wear of the tool surface.
- Cracking - Cracking tends to occur spontaneously and usually means that the die section needs to be repaired or most likely replaced. Cracks often result from improper grinding or machining methods and excessive hardness.
- Chipping - Chipping occurs when cracking is confined to an isolated area. The cracks often cause small fragments of the tool steel to fall off. Point chipping is a common problem with piercing.
- Plastic deformation - When the tool steel’s yield strength is exceeded, plastic deformation occurs. This can be the result of insufficient tool steel hardness or extreme impact force.
About the Author
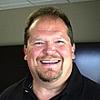
Art Hedrick
10855 Simpson Drive West Private
Greenville, MI 48838
616-894-6855
Related Companies
subscribe now
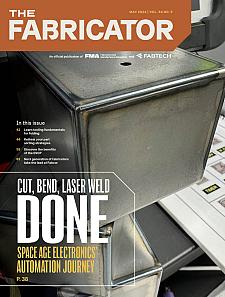
The Fabricator is North America's leading magazine for the metal forming and fabricating industry. The magazine delivers the news, technical articles, and case histories that enable fabricators to do their jobs more efficiently. The Fabricator has served the industry since 1970.
start your free subscription- Stay connected from anywhere
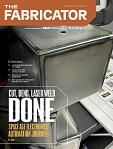
Easily access valuable industry resources now with full access to the digital edition of The Fabricator.
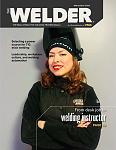
Easily access valuable industry resources now with full access to the digital edition of The Welder.
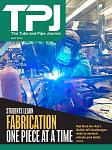
Easily access valuable industry resources now with full access to the digital edition of The Tube and Pipe Journal.
- Podcasting
- Podcast:
- The Fabricator Podcast
- Published:
- 04/16/2024
- Running Time:
- 63:29
In this episode of The Fabricator Podcast, Caleb Chamberlain, co-founder and CEO of OSH Cut, discusses his company’s...
- Trending Articles
Tips for creating sheet metal tubes with perforations
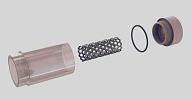
Are two heads better than one in fiber laser cutting?
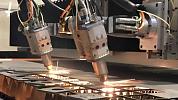
Supporting the metal fabricating industry through FMA
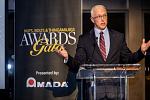
JM Steel triples capacity for solar energy projects at Pennsylvania facility
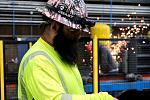
Omco Solar opens second Alabama manufacturing facility
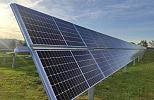
- Industry Events
16th Annual Safety Conference
- April 30 - May 1, 2024
- Elgin,
Pipe and Tube Conference
- May 21 - 22, 2024
- Omaha, NE
World-Class Roll Forming Workshop
- June 5 - 6, 2024
- Louisville, KY
Advanced Laser Application Workshop
- June 25 - 27, 2024
- Novi, MI