Contributing editor
- FMA
- The Fabricator
- FABTECH
- Canadian Metalworking
Categories
- Additive Manufacturing
- Aluminum Welding
- Arc Welding
- Assembly and Joining
- Automation and Robotics
- Bending and Forming
- Consumables
- Cutting and Weld Prep
- Electric Vehicles
- En Español
- Finishing
- Hydroforming
- Laser Cutting
- Laser Welding
- Machining
- Manufacturing Software
- Materials Handling
- Metals/Materials
- Oxyfuel Cutting
- Plasma Cutting
- Power Tools
- Punching and Other Holemaking
- Roll Forming
- Safety
- Sawing
- Shearing
- Shop Management
- Testing and Measuring
- Tube and Pipe Fabrication
- Tube and Pipe Production
- Waterjet Cutting
Industry Directory
Webcasts
Podcasts
FAB 40
Advertise
Subscribe
Account Login
Search
Facade-maker doubles output using folding technology
Folded metal parts finish right in the shop and fit right in the field
- By Kate Bachman
- November 9, 2021
- Article
- Bending and Forming
This 47,180-sq.-ft. facility in Hopkinton, Mass., functions as the new home of the Massachusetts Department of Transportation’s Central Research and Materials Testing Laboratory, replacing the original laboratory in South Boston. Sunrise’s scope included work on the facade, panel install, and storefront.
Sunrise Erectors Inc., Canton, Mass., began 25 years ago as an erector and transitioned into a full building contractor that manufactures and installs high-performance, custom-engineered facade systems. “We're in the architectural facade business,” said Vice President/Partner John Erickson. The facade is the face of a building, whether it be glass, metal, phenolic panels, terra cotta, or cementitious panels, he explained.
Sunrise Erectors is a family business, and it's very employee-oriented, Erickson said. The three partners—John Erickson, his brother Jeff Erickson, and Jeff’s son Andy—believe in treating their employees very well—and that’s no false front. Recently the company set up a certified day care center on the premises, free to office employees. “So, the folks who work on-site in the Canton office have their kids right downstairs,” Erickson said.
All of the company’s shop and field employees are paid good union wages. The staff encompasses six unions—fabricators, sheet metal workers, ironworkers, glaziers, carpenters, and laborers.
The highly skilled and experienced union staff has no doubt contributed to the company’s enormous growth and success. It has an impressive client list and portfolio of distinguished projects. It is one of the largest of its kind in New England, with 275 employees, two shops, and two plants.
Push for Productivity
Being highly productive is of extreme importance to the company, Erickson said, to meet the high-volume and timeliness demands of the many projects. In addition, the company wants to make the best use of its highly skilled, not-inexpensive workforce.
“The problem with the conventional press brakes was their inefficiency in terms of die changes,” Erickson said. "We have a high mix of components—different shapes from day to day. There's a lot of handling when you have to keep switching dies. We might have to put in a hemming die, custom die, or a flattening die, for example.
“We also had a lot more errors when we were doing it the old-school way.”
Erickson continued, “We were having some issues with backgauges on the press brakes, which usually have another company’s backgauge on them. The operators were constantly having problems with the computer boards. And that can drive you nuts, you know, chasing down the different backgauge-makers. We had a backgauge from Europe go bad and that press brake was down for 90 days because they sent the wrong replacement part twice.
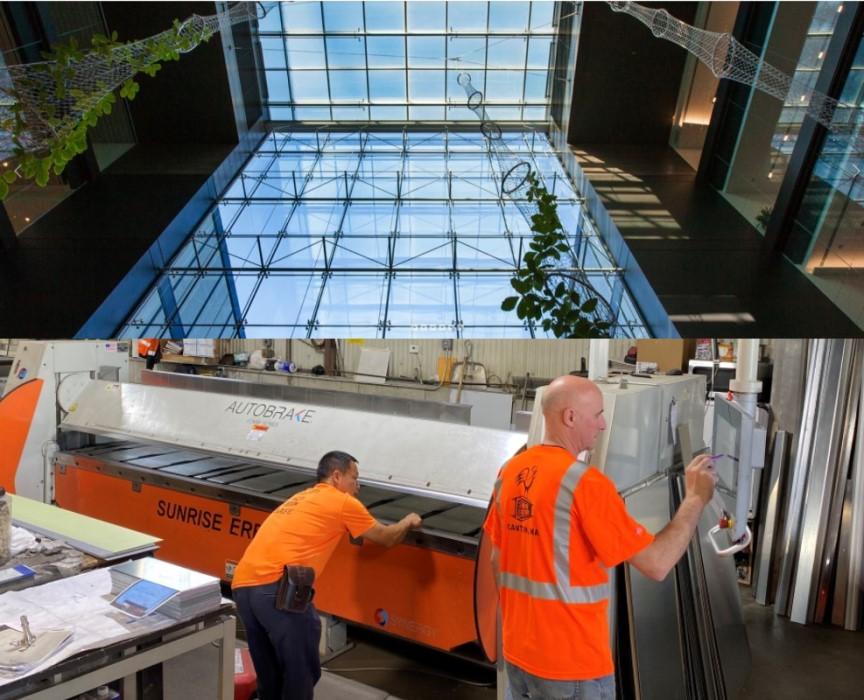
Sunrise Erectors fabricates and installs aluminum curtainwalls, composite aluminum panels, vents, skylights, thermally broken framing, phenolic panels, and other building facades using folding machines to increase productivity and leave the panels unmarred by tooling.
“We wanted to upscale the shop’s productivity. I wanted the shop to make parts faster, more reliably, and cut down on mistakes.”
Needed Accuracy for Fit and Finish
Several of the projects require a lot of intricate bends, especially at building entrances. Part accuracy is critical to a good field fit, Erickson relayed. “Everything has to align—the windows, wall panels, storefront, curtainwall, and sunshades—and everything really needs to line up to fit properly. The tolerances are very, very important,” he said.
Naturally, because facades are the outermost part of buildings, a large percentage of the company’s parts are very visible. That means TLC is needed in the shop during fabrication, especially on the appearance pieces. They must be unmarked by tooling during fabrication.
“We bend a lot of finish material—painted aluminum, painted steel, stainless steel, zinc, copper, brass, and a few other alloys. Much of it is masked, but it's not all masked,” he said. “We do a lot of European facade systems, panel systems. And some of them use exotic metals such as titanium.
“A lot of what we fabricate are appearance pieces just because they’re architectural and for a facade. So it's critical that all these parts are accurate and undamaged—not only the trim, but the backup systems behind the facade.”
The materials for “backup” structural members typically are formed of galvanized steel or mill-finished stainless steel. All of those systems require metal fabricated parts, pieces, and flashings. Although the structural parts aren't visible, even those tolerances are very important too, Erickson explained. “Everything has to line up, either vertically, horizontally, or offset—whatever the design is.”
Folding Machines to the Fore
Sunrise Erectors had two new Roper Whitney folding machines built: a 10-ft.-long Autobrake and a 12-ft.-long 1214K Autobrake.
The company has realized greater efficiencies and accuracy using the folders, Erickson relayed. “There is a big improvement.” The folding machines have accelerated Sunrise’s productivity both in the shop and in the field.
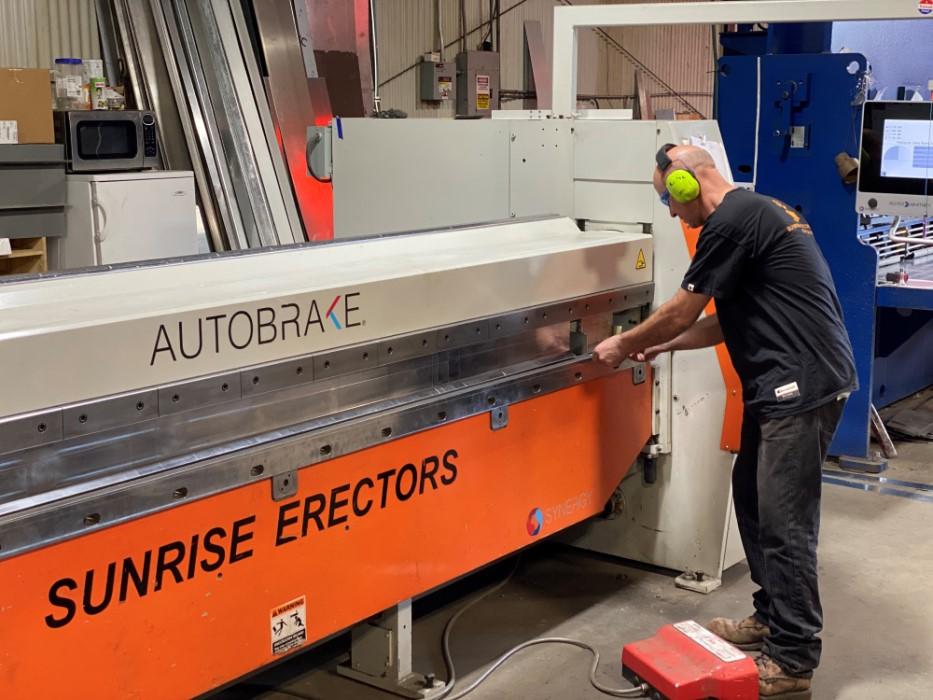
Jorge Lima bends a component for a building facade on a Roper Whitney Autobrake folding machine at Sunrise Erectors. Most of the sheet is supported by the machine and only the portion being bent is outside of the folder.
No Die Changes. Not having to perform die changes escalated shop productivity. “With the folder, you can perform the bends without die changes. And sometimes being able to just switch the bar in the front for different shapes and gauges just saves a tremendous amount of time, labor, and handling,” Erickson said.
Labor Maximizing. One operator can handle that sheet because in a folding machine, the sheet goes completely into—and is supported by—the machine. The sheet remains stationary while the bending tool forms flanges both up and down
To bend large sheets in the press brake, two or more operators were needed to handle it. “A lot of the large building shapes that we are forming lend themselves very well to folding versus bending in conventional press brakes,” Erickson added.
Intuitive Backgauges. Calculating the backgauges on the folding machines is intuitive, Erickson said. “The controller shows the sequence of the bends. That’s one of the reasons there is less margin of error using the folding machines.”
Extra-Long Gains 20%. The extra 2 ft. that the 12-ft.-long folder produces extends productivity, Erickson said. “That helps us tremendously because you're producing 20% more material with every bend. It helps not only in the shop, but also in the field, because when the pieces go out into the field, they have to be staged on aerial lifts. Every time people handle one 12-ft. piece and install it, they're installing 20% more material than the 10-ft. pieces that are bent on the 10-ft. folder.” The 10-ft.-long folder is used for material that is not available in 12-ft. sizes.
“I’m always thinking about how the fabrications will work and fit in the field,” he added.
Nonmarking for Fine Finish
The way folding machines form the bends results in minimal or no marking of the material, a critical feature for the facade manufacturing company.
Folding machines tend not to mark or scratch most materials because the bending process is different, according to Roper Whitney. In a press brake, the material is formed by pushing it into two dies. Because press brakes draw the material over the edges into the V die, the long sliding distance can cause visible scratches on the outside of the sheets.
On a folding machine, the material is formed by the bending beam in the bend process. In this way, a folder minimizes the sliding area of tools on the material surface, which reduces or eliminates scratches.
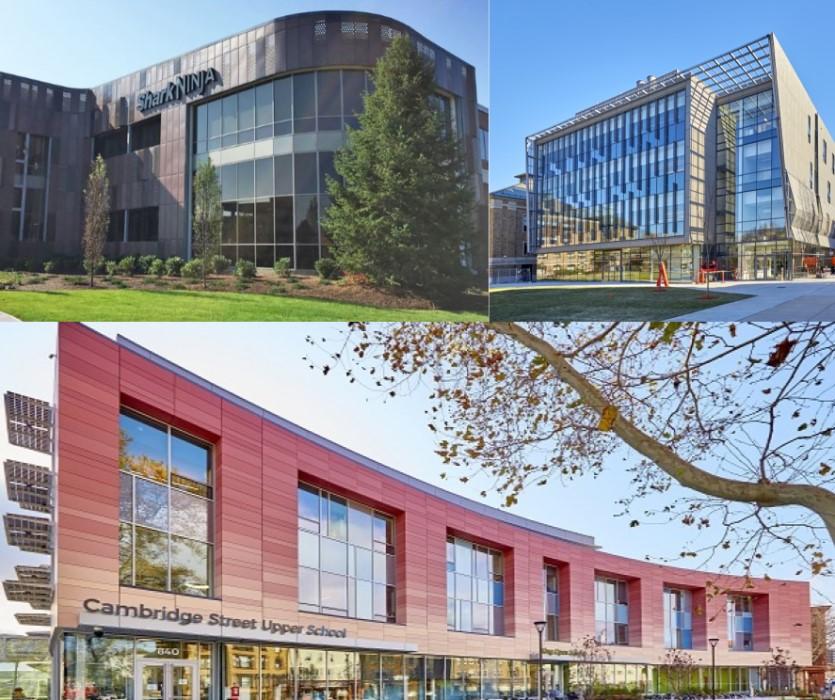
Sunrise fabricated the entire zinc facade ACM soffit, ACM fascia, and corrugated panels for the new international headquarters of SharkNinja, the maker of Shark vacuums and the Ninja line of kitchen appliances. The company also fabricated facades for MIT and the aluminum curtainwall, aluminum vents, aluminum skylight, thermally broken framing, insulation, terra cotta, phenolic panels, and composite aluminum panels for the Cambridge Street Upper School & Community Complex, Cambridge, Mass.
“We really like that the folder doesn’t mark the material,” Erickson said.
Folders Replace Press Brakes
Erickson said that the folding machines are replacing the company’s fleet of press brakes and that the press brakes that remain are relegated to bending heavy-gauge material.
“I had a few press brakes but I'm down to one now because that's all we need.” He continued, “I’m not saying they're dinosaurs because they still have their place. We have a 200-ton press brake we need for bending thicker-gauge materials and certain shapes. You're always going to need a press brake, but these folding machines have replaced most of our press brakes because they fit our architectural needs.”
Pleased With Results
Erickson said that the company is very happy with the outcome. “The results really have been pretty outstanding. We've become more efficient. It's been a win-win situation with these machines.” He said he is thinking about getting a third one, because they're running all the time.
“The productivity on these machines has been double compared to doing it the old-fashioned way on conventional brakes—and that's not exaggerating. On many shapes, it's at least twice as effective. And that makes a lot of difference.”
He added, “Because we’re a union shop, it probably helps us even more than some shops because our rates are high. We're saving that much more money because of the productivity aspect of it.”
Erickson made a point to say how much it meant that the machines were custom-designed and -built domestically in Rockford, Ill.
“I’m as patriotic as the next person, but I also have a lot of foreign specialty machines. In this case, I decided to try to stick with a domestic machine where the parts are much more readily available,” he said.
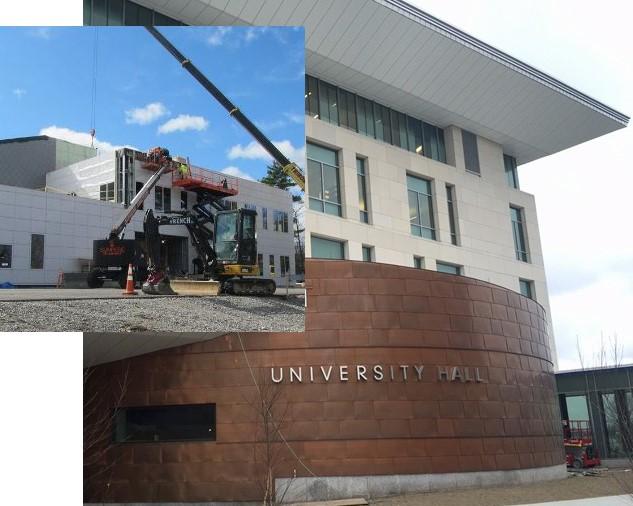
Accuracy in the shop is critical so that fit-up in the field is pitch-perfect. Sunrise fabricated and installed 21,000 sq. ft. of copper panels, 22,000 sq. ft. of its composite metal rainscreen system, and 16,000 sq. ft. of corrugated metal panels on this facade at UMass Boston University Hall, Boston.
“Roper Whitney really tailored them to our needs,” he said. He was able to visit the plant and select the options and features he wanted so that they would be tailored for the type of work Sunrise performs. It was also important to him that the same company that builds the machines builds the backgauges.
“Overall, we've had just great success with the machines and the responsive service.”
Images: Sunrise Erectors Inc., sunriseerectors.com
About the Author
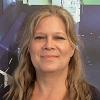
Kate Bachman
815-381-1302
Kate Bachman is a contributing editor for The FABRICATOR editor. Bachman has more than 20 years of experience as a writer and editor in the manufacturing and other industries.
Related Companies
subscribe now
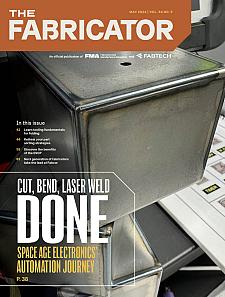
The Fabricator is North America's leading magazine for the metal forming and fabricating industry. The magazine delivers the news, technical articles, and case histories that enable fabricators to do their jobs more efficiently. The Fabricator has served the industry since 1970.
start your free subscription- Stay connected from anywhere
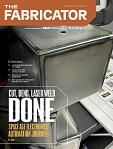
Easily access valuable industry resources now with full access to the digital edition of The Fabricator.
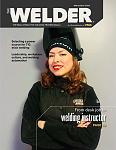
Easily access valuable industry resources now with full access to the digital edition of The Welder.
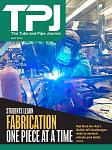
Easily access valuable industry resources now with full access to the digital edition of The Tube and Pipe Journal.
- Podcasting
- Podcast:
- The Fabricator Podcast
- Published:
- 04/16/2024
- Running Time:
- 63:29
In this episode of The Fabricator Podcast, Caleb Chamberlain, co-founder and CEO of OSH Cut, discusses his company’s...
- Trending Articles
Tips for creating sheet metal tubes with perforations
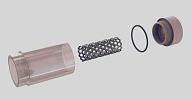
Are two heads better than one in fiber laser cutting?
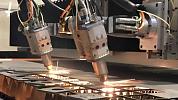
Supporting the metal fabricating industry through FMA
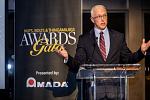
JM Steel triples capacity for solar energy projects at Pennsylvania facility
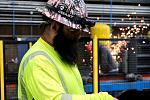
Omco Solar opens second Alabama manufacturing facility
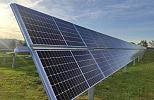
- Industry Events
16th Annual Safety Conference
- April 30 - May 1, 2024
- Elgin,
Pipe and Tube Conference
- May 21 - 22, 2024
- Omaha, NE
World-Class Roll Forming Workshop
- June 5 - 6, 2024
- Louisville, KY
Advanced Laser Application Workshop
- June 25 - 27, 2024
- Novi, MI