Contributing editor
- FMA
- The Fabricator
- FABTECH
- Canadian Metalworking
Categories
- Additive Manufacturing
- Aluminum Welding
- Arc Welding
- Assembly and Joining
- Automation and Robotics
- Bending and Forming
- Consumables
- Cutting and Weld Prep
- Electric Vehicles
- En Español
- Finishing
- Hydroforming
- Laser Cutting
- Laser Welding
- Machining
- Manufacturing Software
- Materials Handling
- Metals/Materials
- Oxyfuel Cutting
- Plasma Cutting
- Power Tools
- Punching and Other Holemaking
- Roll Forming
- Safety
- Sawing
- Shearing
- Shop Management
- Testing and Measuring
- Tube and Pipe Fabrication
- Tube and Pipe Production
- Waterjet Cutting
Industry Directory
Webcasts
Podcasts
FAB 40
Advertise
Subscribe
Account Login
Search
Hot stamping automotive parts in 2019 vehicles
And the die steel, furnace technologies enabling it
- By Kate Bachman
- Updated January 20, 2023
- July 26, 2018
- Article
- Bending and Forming
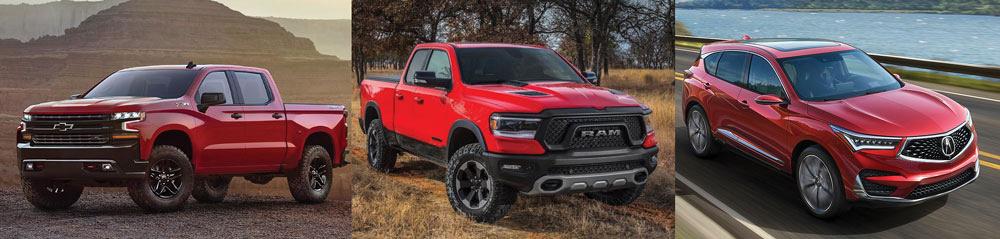
Underneath the red-hot exteriors of the Acura RDX, Ram, Silverado, and other 2019 vehicles are their cool, steely, hot-stamped components.
Hot stamping, also called press hardening, is a process used to form very thin, but also very strong metals into automotive parts to reduce weight while also increasing strength and safety. Metals actually transform from one material chemistry to another during the process, producing steel strengths of up to 2,000 megapascal (MPa). By performing the stamping while the steel is nearly molten, the process eliminates springback and allows for the manufacture of complex geometries.
Hot stamping once was a novice technology, used infrequently on very high-strength steels in specialty applications. If ever there were doubt that the process would increase in use, the 2019 auto industry fleet of vehicles should put those doubts to rest. Hot-stamped, high-strength steel components and assemblies are pervasive in nearly all vehicles.
At this year’s Great Designs in Steel (GDIS) conference in May in Livonia, Mich., several automakers and Tier 1 suppliers revealed where in the 2019 vehicles they used hot-stamped components to achieve lightweighting while also strengthening them.
Although hot stamping has been acknowledged as a resolver of forming problems such as springback, the resulting extremely hard steel component brings with it a new set of challenges related to downstream processes. Steel producers and other OEMs shared recent innovations in steels and in the hot stamping process itself at the conference that temper some of these challenges and facilitate automotive manufacturing improvements.
In the 2019 vehicle fleets, hot-stamped components include door rings, bumpers, roof rails, and chassis in the Honda Acura, GM Silverado, FCA Ram, and other vehicles.
GM Chevy Silverado
The 5.5 percent press-hardened steel in the new Silverado® cab and box contributed to a vehicle level mass reduction of about 450 pounds, even while the automaker built the wheelbase 4 inches longer and the truck 1.5 in. longer overall (see Figure 1), according to General Motors Co.’s Jeff Sulik, engineering group manager, and Joy Geeraerts, senior design release engineer, in their GDIS presentation, “Advanced High-Strength Steel Technologies in the 2019 Chevy Silverado.”
GM achieved the overall vehicle fuel savings with part-specific gauging and material optimization of the cab and frame (see Figure 2), a 7 percent increase in aerodynamic effect, and dynamic fuel management.
The material strategy for the cab with closures and box was to increase the use of UHSS/AHSS/HSLA materials in the cab and higher HSLA grades in the bed and frame for the greatest possible mass reduction. In addition, it uses aluminum closures, disciplined part design, integral front structure, and an aggressive redesign of the upper body structure for mass reduction.
GM engineers used a topological cycle to determine the best load paths and performed shape optimization to establish the most efficient section sizes within the possible design envelopes.
FCA Ram 1500
The 2019 Ram® 1500 has a steel-intensive, lightweight design. Some grade of high-strength steel comprises most of it. The material composition is a strategic mix of hot-stamped, UHSS, DP, and HSLA steels and an aluminum hood and tailgate for a total mass reduction of 225 lbs., according to presenters Dave Reed of FCA US LLC and Paul Belanger, Gestamp, in their presentation, Hot-Stamped Steel One-Piece Door Ring in the All-New 2019 Ram 1500.
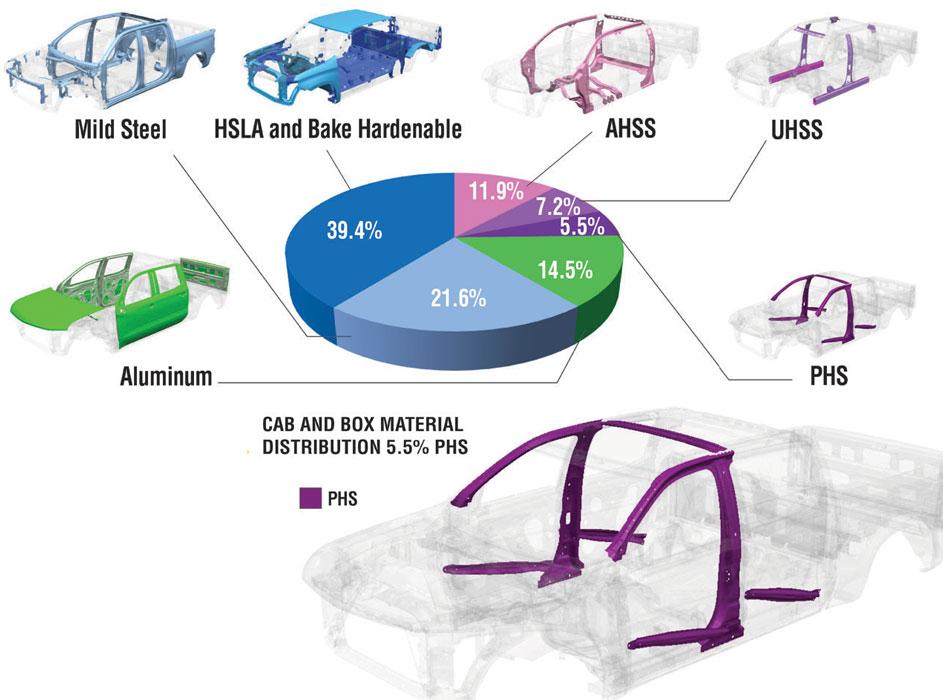
Figure 1
GM’s 2019 Chevrolet Silverado comprises 5.5 percent press-hardened components, in addition to numerous other high-strength steels.
The entire door ring—a six-piece, laser-welded blank composed of four gauges and two material grades—is hot stamped, as is the front header. The press-quenched, lower B-pillar is designed to allow increased elongation and to be optimized for side impact (see Figures 3 and 4). More than one-third of the upper body comprises hot-stamped steel.
The 225-lb. weight reduction was achieved by cuts to both the mass of the frame and the body. The frame is manufactured of 98 percent HSS, saving 125 lbs. over the 2018 model. The increased use of HSS in the body, from 12 to 54 percent, plus a material change from steel to aluminum in the tailgate, reduced body weight by 101 lbs. (see Figure 5).
Honda Acura RDX
Honda increased its use of UHSS by 50 percent in the 2019 Acura® RDX, including 15 percent press-hardened steel, said Joe Riggsby, Honda R&D Americas, Inc., in his presentation, 2019 Acura RDX World’s First Inner & Outer Door Ring System. The result is a 41-lb. (19-kg) weight-down. At least 56 percent of the body components are made of UHSS (PH, AHSS, and HSS) (see Figure 6).
With the new model, Honda introduces what it says is the world’s first inner and outer door ring system (see Figure 7).
“Acura has been advancing hot-stamped door ring technology forward for over a decade, working closely with our partners,” Riggsby said. “The door ring was a natural progression in the application of hot-stamped material on Acura vehicles.”
The inner and outer door ring system takes full advantage of this technology, he continued. The inner ring incorporates the inner side sill, which enables improved connections to both the floor and roof structure. As part of a system, the outer ring has been optimized to balance with the inner ring for additional weight reduction.
The system meets or exceeds safety targets for panoramic roof opening, front crash, side crash, and rollover.
The previous version with a pillar offset form sill structure does not have an efficient load path, Riggsby explained. Smooth joints can facilitate a more efficient design. An integrated door ring system eliminates welded joints, which are the weak points in the system, he said. Additional weight reductions are achieved by deleting overlapping material.
Various Automakers, Gestamp
In his presentation, Press-Hardened and Roll-Formed Lightweight Bumpers in Steels with Enhanced Strength, Johan Nilsson of Tier 1 supplier Gestamp relayed that several automakers have used hot-stamped bumpers to reduce mass.
Bumpers protect the body-in-white (BIW) and external attributes in low-speed collisions and contribute to crash safety in high-speed collisions by transferring loads to the BIW, Nilsson said (see Figure 8). “They are continuously improved through implementation of materials with enhanced strength, new design features, new manufacturing processes, a reduction of number of components, and reduction of package space,” he said.
Gestamp conducted tests comparing bumpers manufactured by press hardening the front bumper cross beam to 2,000 MPa and three-layered, 1,200-MPa material crash boxes; roll forming the front bumper cross beams and press-hardening the crash boxes; and press-hardening a rear bumper beam with 2,000-MPa tensile strength with patch technology (see Figure 9).
The results showed that the 2,000-MPa tensile strength press-hardened beam and crash boxes reduced the bumper weight by 15 percent, compared to a benchmark bumper.
A roll formed beam with M profile in 1,200-MPa material and crash boxes in press-hardened, 1,200-MPa material is 13 percent lighter than the benchmark bumper.
A rear bumper, press-hardened beam with patch with 2,000-MPa tensile strength fulfills global low-speed crash requirements and withstands only minor material failure in high-speed impacts. S
Ebner Industries, www.ebner.cc/en/home
FCA, www.fcagroup.com
Gestamp, www.gestamp.com
Hitachi, www.hitachimetals.com
Honda, www.honda.com
The Great Designs in Steel event is administered by the Steel Market Development Institute, www.autosteel.org/about-autosteel.
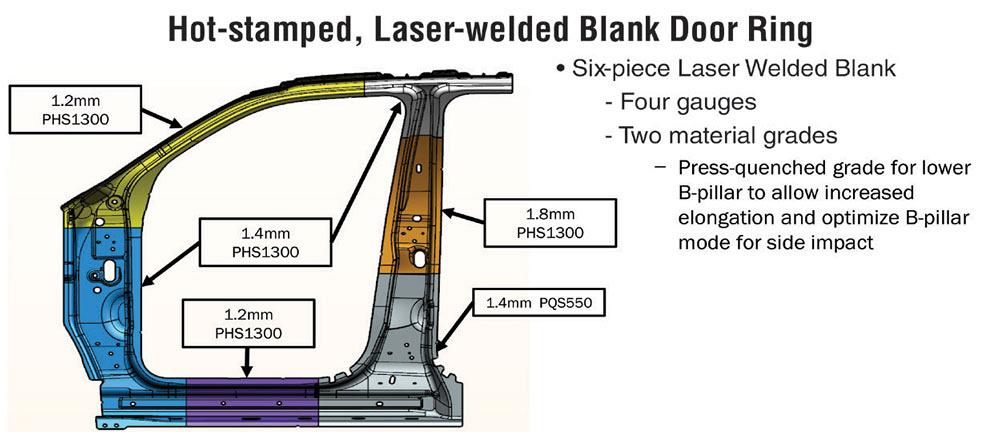
Figure 3
The entire FCA Ram door ring is hot-stamped, albeit composed of different grades and gauges.
Legend
Advanced High-strength Steel (AHSS)
Dual-phased (DP)
High-strength Steel (HSS)
High-strength Low-Alloy (HSLA)
Low-strength Steel (LSS)
Press-hardened Sateel (PHS)
Ultrahigh-strength Steel (UHSS)
Hot Stamping Automotive Parts Process Improvements
Enabling the broadening use of hot stamping in vehicular component manufacturing are improvements in the die steel and the furnaces.
Hot Stamping Die Steels Optimized for the Process. Advanced-grade die materials are needed for forming, trimming, piercing, and punching AHSS. Until now, die standards have not kept up with increased-strength trends. Die failures include chipping, galling, and cracking. New tool steels have been engineered specifically for hot stamping, said Thomas Bell, Hitachi Metals Americas, in his presentation, Die Steel Improvements for AHSS Applications.
During hot stamping, die surfaces can reach 752 degrees F. The extreme temperatures of hot stamping require that die materials be upgraded to a NADCA Class C Hot Work Steel to replace what is commonly used today, AISI H13, he said. Class C steel has higher strength at high temperatures and is better for heat conductivity than H13, a Class B die steel. Class B H13 is 32.6 at 1,112 degrees F, while Class C is 35.8 at 1,112 degrees F. This translates to a better cycle time in the cooling system.
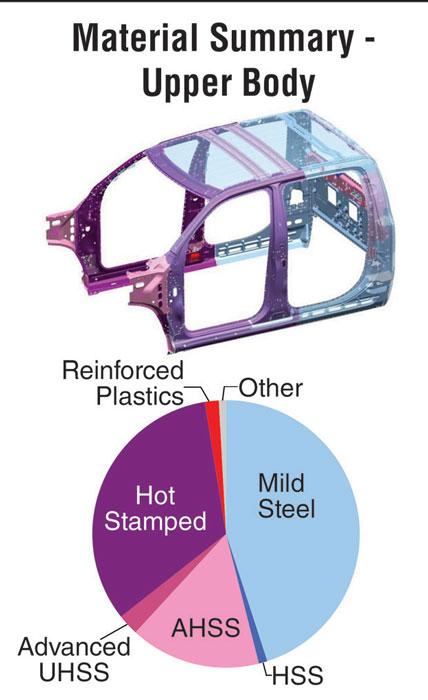
Figure 4
The hot-stamped steel door ring structure and front header, which comprise about a third of the upper body, provide strong, lightweight designs for impact.
Also, Class C steel toughness means that it has higher impact values, which prevent surface cracking of hot stamping dies close to the cooling channel.
Pre-hardened Steel. Another die steel advancement is prehardened die steels. (see Figure 10). Tests show that prehardened steels have good machinability even at 60 Rockwell hardness (HRC) because they have fewer primary and secondary carbides.
Hitachi predicts that wear and conductivity demands on die materials will increase. Developments in 3-D printing/additive manufacturing, cooling systems, and the use of higher alloyed die steel may continue to improve die life.
Press Hardening Furnaces with Tailored Tempering
Advancements in press hardening furnaces have enhanced the hot stamping technology as well, particularly in allowing flexible tailored tempering, according to Anton Oppermann of Ebner Industrieofenbau GmbH, in his presentation Press Hardening Furnaces with Integrated Flexible Tailored Tempering. Press hardening furnaces with integrated flexible tailor tempering allow stamping manufacturers using hot stamping to temper, or make more ductile, specific areas of a component.
Tailored tempering technology is a process by which the cooling in the forming and quenching process of the hot stamping operation is controlled through use of thermally stabilized tools. This allows the stamper to target zones to have microstructures of lower strength and greater ductility than the traditional full martensitic microstructure achieved with traditional hot stamping.
By controlling the microstructure in select areas of the part, the stamper can realize targeted deformation zones or zones with greater elongation in specific areas, while the remainder of the part can be at the full ultrahigh strength. As a result, the lower-strength metal can be located for compression in crashes while ultrahigh tensile strength is maintained in the rest of the part.
(For more about tailored tempering, read “How 2016 Car of the Year Honda Civic maneuvered around AHSS obstructions,” published in September/October 2016 issue of STAMPING Journal.)
About the Author
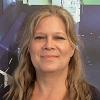
Kate Bachman
815-381-1302
Kate Bachman is a contributing editor for The FABRICATOR editor. Bachman has more than 20 years of experience as a writer and editor in the manufacturing and other industries.
Related Companies
subscribe now
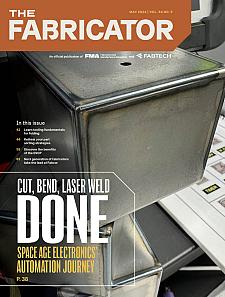
The Fabricator is North America's leading magazine for the metal forming and fabricating industry. The magazine delivers the news, technical articles, and case histories that enable fabricators to do their jobs more efficiently. The Fabricator has served the industry since 1970.
start your free subscription- Stay connected from anywhere
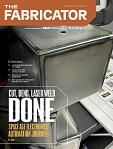
Easily access valuable industry resources now with full access to the digital edition of The Fabricator.
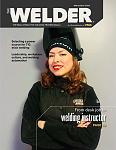
Easily access valuable industry resources now with full access to the digital edition of The Welder.
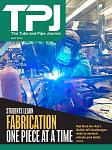
Easily access valuable industry resources now with full access to the digital edition of The Tube and Pipe Journal.
- Podcasting
- Podcast:
- The Fabricator Podcast
- Published:
- 04/16/2024
- Running Time:
- 63:29
In this episode of The Fabricator Podcast, Caleb Chamberlain, co-founder and CEO of OSH Cut, discusses his company’s...
- Trending Articles
Tips for creating sheet metal tubes with perforations
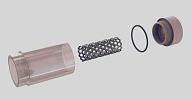
Supporting the metal fabricating industry through FMA
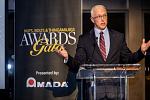
JM Steel triples capacity for solar energy projects at Pennsylvania facility
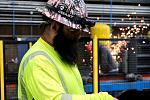
Are two heads better than one in fiber laser cutting?
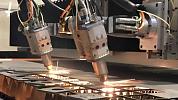
Fabricating favorite childhood memories
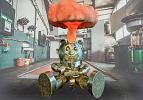
- Industry Events
16th Annual Safety Conference
- April 30 - May 1, 2024
- Elgin,
Pipe and Tube Conference
- May 21 - 22, 2024
- Omaha, NE
World-Class Roll Forming Workshop
- June 5 - 6, 2024
- Louisville, KY
Advanced Laser Application Workshop
- June 25 - 27, 2024
- Novi, MI