Contributing editor
- FMA
- The Fabricator
- FABTECH
- Canadian Metalworking
Categories
- Additive Manufacturing
- Aluminum Welding
- Arc Welding
- Assembly and Joining
- Automation and Robotics
- Bending and Forming
- Consumables
- Cutting and Weld Prep
- Electric Vehicles
- En Español
- Finishing
- Hydroforming
- Laser Cutting
- Laser Welding
- Machining
- Manufacturing Software
- Materials Handling
- Metals/Materials
- Oxyfuel Cutting
- Plasma Cutting
- Power Tools
- Punching and Other Holemaking
- Roll Forming
- Safety
- Sawing
- Shearing
- Shop Management
- Testing and Measuring
- Tube and Pipe Fabrication
- Tube and Pipe Production
- Waterjet Cutting
Industry Directory
Webcasts
Podcasts
FAB 40
Advertise
Subscribe
Account Login
Search
How stamping press controls have evolved to keep up with automation
Growing press control technology help stamping manufacturers with staffing shortages
- By Kate Bachman
- July 28, 2022
- Article
- Bending and Forming
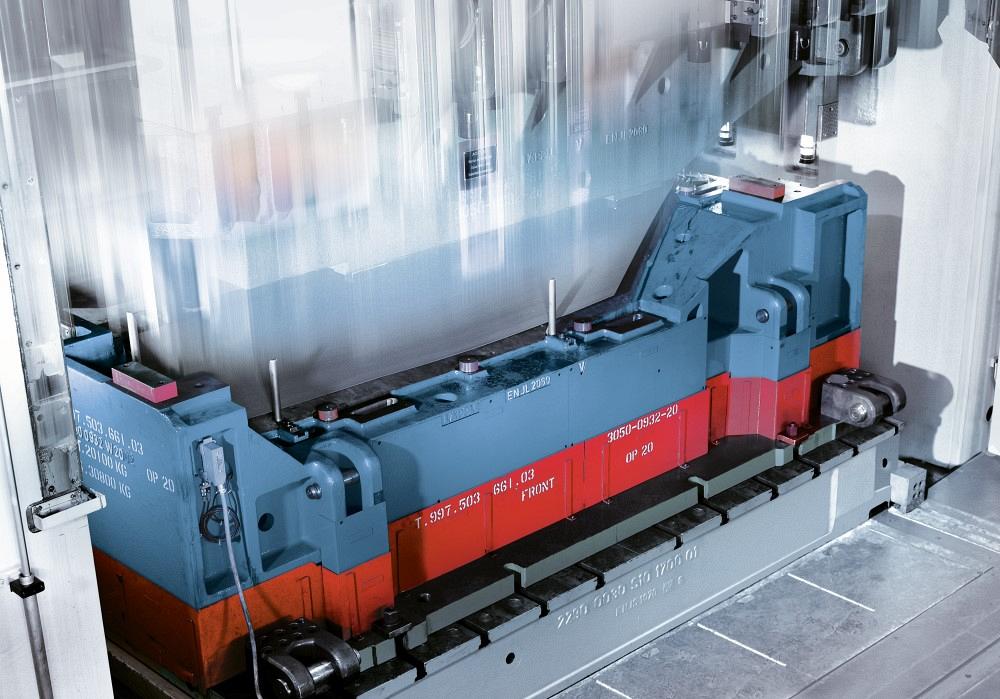
The trend in automobile bodies is towards larger panels with deeper draws. This necessitates the use of more complex presses, including servo-hydraulic cushion systems. Bosch Rexroth
Employee shortages and high turnover have made training important so that new employees—or those filling in for others—can adapt quickly to the challenges at hand … not to mention, the task flexibility required by supply chain disruptions. At the same time, press lines and tooling have become more automated with multiple interfaces that result in more complicated operations.
Press controls have been upgraded frequently to modernize an older press system. Now they have evolved to help stamping manufacturers grapple with today’s personnel and automation challenges.
Wintriss Controls Group Product Manager Jim Finnerty, and Bosch Rexroth Control System Application & Engineering Manager Ken Rayden weigh in on trends in press control technology affecting stamping manufacturing.
Stamping Journal: What challenges are stampers currently faced with related to press controls?
Finnerty: A lot of employee turnover has occurred the last few years, and it has been difficult for stampers to fill skilled positions with qualified people, so training has become more important than ever.
In addition, press lines and tooling have become more automated with multiple interfaces, which results in more complicated operations, exacerbating the training issue.
Also, supply chain interruptions have forced manufacturers to become more adaptable. Instead of sticking to a “normal” schedule, shops are scheduling jobs when raw material and parts become available. This results in more frequent tool changes at the presses. Reducing set up time has become a constant challenge.
Rayden: The trend in automobile bodies is towards larger panels with deeper draws. This necessitates the use of more complex presses, including servo-hydraulic cushion systems.
At the same time, stamping manufacturers continue to face the erosion of skilled maintenance technicians and engineers who are capable of providing robust and timely troubleshooting and repair services for this equipment, including hydraulics.
SJ: How are press controls evolving to help meet these challenges?
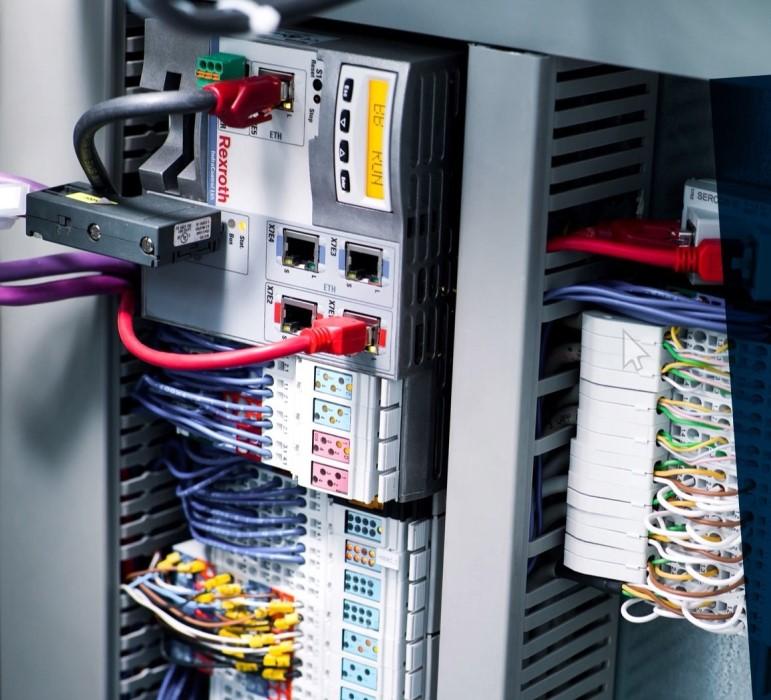
The Bosch Rexroth advanced diagnostics package is a PLC-, HMI-, and sensor-based system to assist stampers with rapid troubleshooting, repair, and part procurement. Built-in tests automatically check the system and pinpoint failed components. Bosch Rexroth
Rayden: In all markets using advanced hydraulic machinery, there is a need to include troubleshooting assistance within the control system to bridge the gap between skilled labor and complex machinery. More and more control systems include some form of graphical representation of the status of the electric, pneumatic, and hydraulic press systems to aid troubleshooting. However, much more can and needs to be done on this front.
Finnerty: Multiple automated systems on the press can result in multiple user interfaces that require programming and adjustment each time a job is changed. The challenge for control manufacturers is to find a way to unify these systems and reduce the number of screens on the machine, while keeping the interface as simple and user-friendly as possible. This is no small task.
SJ: What have you done with press controls to address these challenges?
Finnerty: We have adopted a “one press, one screen” philosophy. We’ve collaborated with suppliers of servo feeds, lube systems, PLCs, and other devices to enable our controls to act as the main user interface for their equipment. Now, when the job changes at the press, operators need to learn how to use only one controller and access only one screen instead of many. This alleviates the training burden and reduces set up time.
As part of our interoperability mandate, we’ve expanded the remote access features of our controllers. Now, subject matter experts can quickly access and program our controllers remotely from a computer or mobile device whenever application problems arise or when programming help is needed.
Also, Wintriss is including training specialists and user experience experts on our control design teams. This helps to ensure that our systems continue to be intuitive and user friendly. We’ve added features such as unique, context-sensitive help screens written in simplified language for every programming screen on the control. We’ve created the ability for press operators to configure custom dashboards for the controls that put the features they want at their fingertips for quick access.
To meet the challenges raised by advanced tooling and automation, Wintriss has greatly expanded our controllers’ sensor monitoring and programmable limit switch capabilities.
We’ve added dozens of new features to provide next-generation flexibility to our die protection systems. We’ve also included functions to make the system more forgiving and to reduce nuisance stops. Complex automation can require complex timing and control logic. In the past, this was often accomplished by adding a separate PLC to our integrated systems. We have recently reduced the need for these additional controllers by releasing a sweeping upgrade of our programmable limit switch capabilities. Users can now control automated tooling, complex operations, and external ancillary equipment without the need for a custom control.
Rayden: We have developed an advanced diagnostics system to assist stampers with rapid troubleshooting, repair, and part procurement for our hydraulic systems. The Bosch Rexroth advanced diagnostics package is a PLC-, HMI-, and sensor-based system. It brings together a number of features, hosted through the machine HMI. Its sole purpose is to provide real-time, embedded system component testing; system documentation; and system visualization into one central location.
A key feature of the diagnostics is the inclusion of expert hydraulic troubleshooting for each system component. This exists even for those without a direct electrical interface, such as check valves, relief valves, and throttles. Think of it as an “engineer in a box.”
The user simply launches the troubleshooting portion of the package. A series of predetermined tests are executed, systematically testing each component and reporting the findings to users. The report offers either a specific action item or a short list of possible solutions. The operator makes the recommended checks or corrections and then reruns the test to verify that the correction was successful.
About the Author
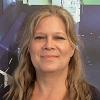
Kate Bachman
815-381-1302
Kate Bachman is a contributing editor for The FABRICATOR editor. Bachman has more than 20 years of experience as a writer and editor in the manufacturing and other industries.
Related Companies
subscribe now
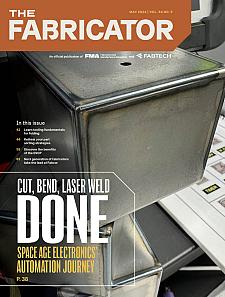
The Fabricator is North America's leading magazine for the metal forming and fabricating industry. The magazine delivers the news, technical articles, and case histories that enable fabricators to do their jobs more efficiently. The Fabricator has served the industry since 1970.
start your free subscription- Stay connected from anywhere
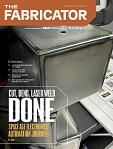
Easily access valuable industry resources now with full access to the digital edition of The Fabricator.
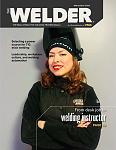
Easily access valuable industry resources now with full access to the digital edition of The Welder.
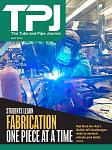
Easily access valuable industry resources now with full access to the digital edition of The Tube and Pipe Journal.
- Podcasting
- Podcast:
- The Fabricator Podcast
- Published:
- 04/16/2024
- Running Time:
- 63:29
In this episode of The Fabricator Podcast, Caleb Chamberlain, co-founder and CEO of OSH Cut, discusses his company’s...
- Trending Articles
Tips for creating sheet metal tubes with perforations
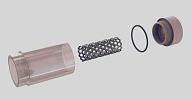
JM Steel triples capacity for solar energy projects at Pennsylvania facility
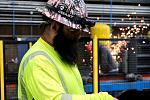
Are two heads better than one in fiber laser cutting?
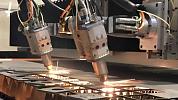
Supporting the metal fabricating industry through FMA
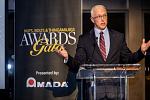
Omco Solar opens second Alabama manufacturing facility
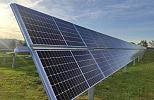
- Industry Events
16th Annual Safety Conference
- April 30 - May 1, 2024
- Elgin,
Pipe and Tube Conference
- May 21 - 22, 2024
- Omaha, NE
World-Class Roll Forming Workshop
- June 5 - 6, 2024
- Louisville, KY
Advanced Laser Application Workshop
- June 25 - 27, 2024
- Novi, MI