Contributing editor
- FMA
- The Fabricator
- FABTECH
- Canadian Metalworking
Categories
- Additive Manufacturing
- Aluminum Welding
- Arc Welding
- Assembly and Joining
- Automation and Robotics
- Bending and Forming
- Consumables
- Cutting and Weld Prep
- Electric Vehicles
- En Español
- Finishing
- Hydroforming
- Laser Cutting
- Laser Welding
- Machining
- Manufacturing Software
- Materials Handling
- Metals/Materials
- Oxyfuel Cutting
- Plasma Cutting
- Power Tools
- Punching and Other Holemaking
- Roll Forming
- Safety
- Sawing
- Shearing
- Shop Management
- Testing and Measuring
- Tube and Pipe Fabrication
- Tube and Pipe Production
- Waterjet Cutting
Industry Directory
Webcasts
Podcasts
FAB 40
Advertise
Subscribe
Account Login
Search
Lubricant application system smooths the road for stamper’s ramp-up
Gains efficiencies, cuts lube waste and cost, ensures quality
- By Kate Bachman
- March 23, 2018
- Article
- Bending and Forming
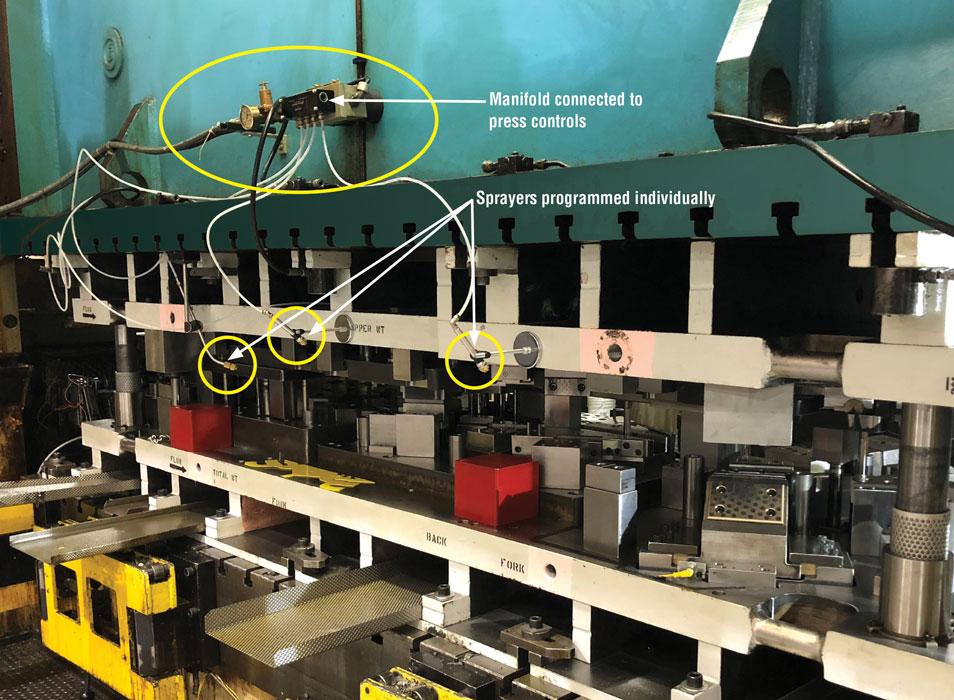
This Industrial Innovations lubrication application system is installed on ODM’s 600-ton Brown Boggs press with a 168-in.-long bed, which is stamping parts that will be assembled into an SUV. The manifold is connected to the press controls. Lubricant sprayers are programmed individually. Photo courtesy of ODM Tool and Mfg. Co. Inc., McCook, Ill.
ODM Tool & Mfg. Co. Inc., McCook, Ill., has blazed its own trail in the automotive segment.
Its heavy-gauge, high-strength steel stamped components and welded assemblies comprise the frames, engine mounts, axles, seating, and inner structures of many of the four-wheel drives and light trucks on the road (and off-road) today, including the Ford F-150®, Toyota Tacoma®, Chevy Silverado®, and Jeep® Grand Cherokee (see Figure 1).
Automakers and their Tier 1 suppliers rely upon the sturdiness and accuracy of the parts ODM manufactures.
Forming that structural steel right depends on having a well-oiled machine, and ODM’s part accuracy depends in no small way on the accuracy of the lubricant blend and its efficient application in the die, especially as material has gotten thicker and higher strength. Lubrication must be mixed accurately and thoroughly, and its application must be precise, controllable, efficient, and cost-effective to meet quality standards and ensure profitability.
Ramping Up
Founded in 1946, the third-generation, family-owned company has toughed it out through bad times and good times. Each generation of the family has fortified the company, expanded the facility, added equipment capacity and capabilities, and grown annual sales--and each decade has tested the company’s mettle.
Today ODM’s 104 employees are working two full-time-plus shifts, six days a week, in the 100,000-square-foot plant. The manufacturer has been ramping up at a breakneck growth rate since 2009, when its annual sales were significantly down and its staff of 33 employees were working three days a week.
Having survived that historic national economic downturn, the last thing the company’s management wanted to do was to turn down work because of the challenges inherent in explosive growth. They recognized the need to become even more efficient to handle the increasing work volume without sacrificing quality, safety, or on-time delivery—currently above 99 percent.
Maintaining Quality. ODM’s clients demand zero defects. Everywhere you look in the plant you see evidence of extreme attention to quality: vision systems, coordinate measuring machines (CMMs), and manual 100 percent verification checks (see Figure 2). One bad part out the door creates hundreds of hours of rechecks.
With 17 presses—ranging from a 1,500-ton with a 20-foot bed to a 110-ton—running up to 150 hours a week, the company’s operations go through a whole lotta lube.
A sizable aspect of managing its business growth involved ODM’s switching up its lubricant application methods to achieve efficiencies. The manufacturer needed airtight control on its lubrication application in terms of amount, location, timing, duration, and force, as well as accurate formulations to meet quality expectations. It needed to attain optimal labor usage and maximize cost-effectiveness.
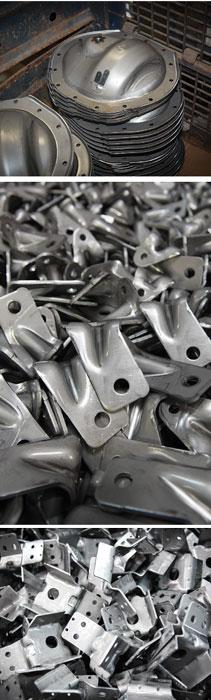
Figure 1
ODM’s heavy-gauge, high-strength steel components comprise the frames, engine mounts, axles, seating, and inner structures of many of the toughest drives on the road (and off-road) today.
Problems
The main problems with ODM’s small, stand-alone lubricant sprayer application process were inconsistency and waste as a result of hand-mixing the lubricants. Also, the lubrication system caused substantial downtime because the small, stand-alone sprayers had to be refilled frequently and by hand.
In addition, the stamper’s larger presses sometimes needed more than one stand-alone lubricant sprayer (see Figure 3).
Downtime. “We had three or four stand-alone spray systems on it. They have little reservoirs with a 2-gallon capacity. We would get the lubricant concentrate and we would have to mix it with water in a 5-gallon bucket, and then dump it into the sprayer reservoir,” said Vice President Jay Michaelsen. Not exactly a good use of labor time and talent—or machine utilization.
The stand-alone sprayers were a maintenance nuisance as well. “Not that they were bad sprayers, but the spray units were not always reliable and frequently had to be taken down for maintenance,” Michaelsen said. “If one sprayer went down, you had to stop the press, take it offline, bring another one over, redo the mix and everything …”
Inconsistency. To some degree, the formula blend was mixed at the discretion of the operator performing the blend, but part quality, tool life, and profitability depended on using the correct formula.
“We might quote a job to run at 10-to-1 [mixture concentration/ratio of water to lubricant], but we might actually be running at a different ratio. It was dependent on the operator to mix it accurately, but we did not have a precise way of measuring the concentration,” he said. “Certain jobs require a higher concentration of lubricant than others—and the quality of the stamping depends on the accuracy of that blend.”
Too much lubricant or not enough lubricant, or the right amount of lubricant applied incorrectly, could mean the difference between good parts and bad parts. In today’s automotive manufacturing environment, even one bad part can mean hundreds of hours of rechecks.
“And that’s what got us going on exploring other options. All of those problems made it very evident that we needed a better way to apply lubrication into our stamping tools, especially because we were getting very busy. We needed to become more efficient,” Michaelsen added.
Evaluation
ODM toured a stamping facility in Michigan that had an Industrial Innovations PRO-MIX™ proportional lubricant mixing and application system installed, and considered that it might resolve the company’s problems. Around that same time, the stamper had an opportunity to learn more about the system from Industrial Innovations President Troy Turnbull at a Precision Metalforming Association (PMA) meeting. After the ODM team conferred, it decided to try the system on a small, pilot scale (see Figure 4).
ODM purchased an Industrial Innovations PRO-MIX DUAL™ proportional lubricant mixing and SPRA-RITE™ application system for four of its busiest presses and planned to expand the new system to other presses if the results were satisfactory and once the operators became familiar with it (see lead image). This system mixes and delivers one lubricant compound at two different mix ratios.
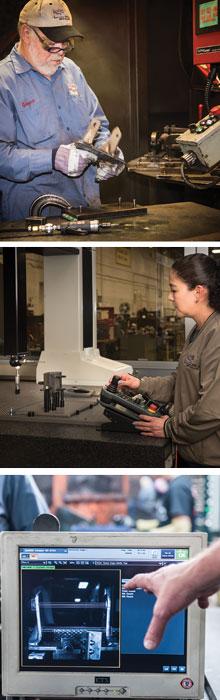
Figure 2
Accuracy is of utmost importance, so ODM uses 100 percent verification, CMM, and vision systems to check the parts.
Upgraded Lubricant Application System
Today the advanced mixing and application systems supply lubricant to 13 of ODM’s 17 presses. Lubricants are distributed continuously via an in-plant pressurized piping network (see Figure 5). The water line goes into the system, where the stamping lubricant and the water combine. “System one is set for 4-to-1, and system two is set for 8-to-1. So one’s thicker, one’s thinner. Then that mixture is pumped to the presses,” Michaelsen said.
The Pro Mix V mixing system is delivered “ready-to-run,” so the installation itself was very quick, although having a plumber install the water piping network took eight weeks, Michaelsen said.
The company’s management has been pleased with the results. The system has reduced downtime, improved the consistency of both the lubricant formula and its application, and cut waste—and therefore consumption—by about 30 percent, they reported.
“Operators no longer need to stop presses to refill the stand-alone lube sprayers,” Michaelsen said. This has reduced downtime, optimized labor use, and increased productivity.
The higher precision of the new application system has made it easier for ODM to achieve its zero-defect requirements because it has eliminated quality and tooling problems caused by excessive or insufficient lubrication application (see Figure 6). “We now have consistent mixes of water to lubricant at either a 4-to-1 or an 8-to-1 ratio [see Figure 7]. We use a richer concentrate for certain jobs and a less rich concentrate for others. Right now we’re running a part that’s 4-to-1 because there is a lot of forming to it and a lot of material. Yesterday we were running a job stamping thin material that requires hardly any lubrication at all,” Michaelsen said.
“There is also consistency in terms of how much lubricant is sprayed, where it is sprayed, and how often it is sprayed,” Michaelsen said (see Figure 8). The system includes a Spra-Rite controller that allows for the individual control of 16 nozzles with just one I/O required at the press control.
The stamping industry requires continuous improvement and waste reduction. The stand-alone spray systems created a lot of waste, he said. Waste on the floor means safety hazards and money out the window. “A lot of waste has been eliminated, resulting in a very quick return on our investment.
“Also, we can put those sprayers in different locations,” he continued. “We have two manifolds on this 1,500-ton press, and the manifolds have eight different lines to them—16 in total. All of them are programmed through the application system and through the channels on our press. You can program it to spray at a certain time. You can spray it once, twice, or three times. It can spray short, quick blasts, or it can spray for a longer duration.
It gives you so many different variables, so many different combinations.”
The lubrication application system itself is located in the back corner of the plant. “It doesn’t matter how far away it is from the press. It’s about 100 feet from one press and about 200 feet from one of the other presses. This is where all the programming is done, and our operators do that. Once it’s programmed, it’s saved by the job number, and it remembers all the settings,” Michaelsen said. The Spra-Rite controller has a 200-part recipe storage capability and is key lock-protected from undesired application setting changes.
The system has had other beneficial impacts as well. It has enhanced safety—very important to the company—because operators are no longer spilling fluid on the floor while transporting it to and from the central mixing station (see Figure 9). Further zeroing out spillage and leaking, the Spra-Rite Z-Drip Nozzles halt almost all dripping with patented technology that eliminates the use of check valves, which tend to leak.
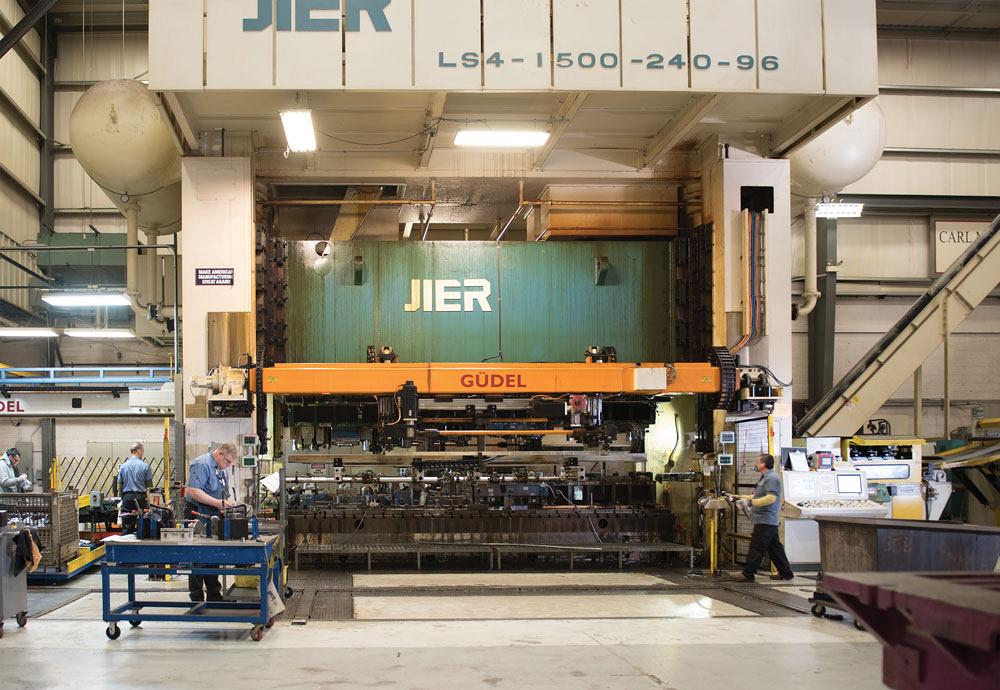
Figure 3
ODM’s 1,500-ton press had multiple stand-alone lubricant sprayers before they were replaced with an Industrial Innovations PRO-MIX™ proportional lubricant mixing and application system.
It has even eliminated the need for parts washing in some instances when the blend is very thin.
ODM now has a reliable, accurate lubrication application system; the company is well-positioned to roll with the changes.
Photography by Michael Candee, FirstLight, except where noted, for STAMPING Journal®.
ODM Tool & Mfg. Co. Inc., www.odmtool.com
Industrial Innovations, www. industrialinnovations.com
About the Author
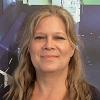
Kate Bachman
815-381-1302
Kate Bachman is a contributing editor for The FABRICATOR editor. Bachman has more than 20 years of experience as a writer and editor in the manufacturing and other industries.
subscribe now
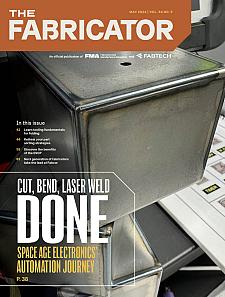
The Fabricator is North America's leading magazine for the metal forming and fabricating industry. The magazine delivers the news, technical articles, and case histories that enable fabricators to do their jobs more efficiently. The Fabricator has served the industry since 1970.
start your free subscription- Stay connected from anywhere
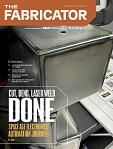
Easily access valuable industry resources now with full access to the digital edition of The Fabricator.
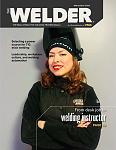
Easily access valuable industry resources now with full access to the digital edition of The Welder.
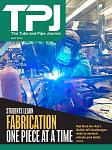
Easily access valuable industry resources now with full access to the digital edition of The Tube and Pipe Journal.
- Podcasting
- Podcast:
- The Fabricator Podcast
- Published:
- 04/16/2024
- Running Time:
- 63:29
In this episode of The Fabricator Podcast, Caleb Chamberlain, co-founder and CEO of OSH Cut, discusses his company’s...
- Trending Articles
Tips for creating sheet metal tubes with perforations
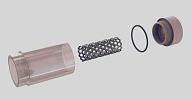
Supporting the metal fabricating industry through FMA
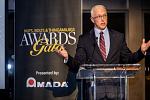
JM Steel triples capacity for solar energy projects at Pennsylvania facility
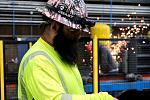
Are two heads better than one in fiber laser cutting?
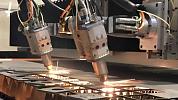
Fabricating favorite childhood memories
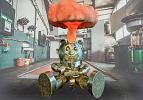
- Industry Events
16th Annual Safety Conference
- April 30 - May 1, 2024
- Elgin,
Pipe and Tube Conference
- May 21 - 22, 2024
- Omaha, NE
World-Class Roll Forming Workshop
- June 5 - 6, 2024
- Louisville, KY
Advanced Laser Application Workshop
- June 25 - 27, 2024
- Novi, MI