Contributing editor
- FMA
- The Fabricator
- FABTECH
- Canadian Metalworking
Categories
- Additive Manufacturing
- Aluminum Welding
- Arc Welding
- Assembly and Joining
- Automation and Robotics
- Bending and Forming
- Consumables
- Cutting and Weld Prep
- Electric Vehicles
- En Español
- Finishing
- Hydroforming
- Laser Cutting
- Laser Welding
- Machining
- Manufacturing Software
- Materials Handling
- Metals/Materials
- Oxyfuel Cutting
- Plasma Cutting
- Power Tools
- Punching and Other Holemaking
- Roll Forming
- Safety
- Sawing
- Shearing
- Shop Management
- Testing and Measuring
- Tube and Pipe Fabrication
- Tube and Pipe Production
- Waterjet Cutting
Industry Directory
Webcasts
Podcasts
FAB 40
Advertise
Subscribe
Account Login
Search
Medical device manufacturer takes on high-speed stamping, overmolding
Becomes first-time stamper to produce a life-saving device
- By Kate Bachman
- February 10, 2022
- Article
- Bending and Forming
Precision in stamping is always important, but rarely is it a life-and-death scenario. Precision and repeatability are of critical importance to Facet Medical Technologies, a medical device component manufacturer based in Atlanta. The nearly 50-year-old manufacturer serves the global diabetes care, wound care, and drug-delivery marketplaces. It is one of the largest providers of lancets and lancing devices in the world.
In response to a request from a major OEM customer a few years ago, Facet began investigating what it would take to produce stamped and formed needles in-house.
Stamping Life-sustaining Needles
Facet produces needles, or “sharps,” made for various critical applications for in-home drug-delivery systems, such as insulin delivery, and glucose-level detection. These needles must meet stringent medical industry standards.
For a recent project, Facet was tasked with producing a specialized, high-precision stamped needle. This needle is inserted subcutaneously as part of a larger system. Because the system is designed to be used by a person in their own home and not in a medically supervised clinic or hospital, accuracy is of the utmost importance.
The sharps must be stamped from chemically etched stainless steel material, precision-beveled, and overmolded with plastic bodies specifically designed to reduce discomfort and enhance performance.
Bringing Stamping In-house
Although Facet Medical had extensive experience with high-volume automation, vision inspection, and micro-insert molding, the needle project involved stamping, which Facet had never performed before. The project required a complete, automated production line and all related disciplines to stamp and produce the overmolded sharps.
Facet Medical Director of Operations and Engineering Brett Rogers was assigned to investigate potential suppliers for the company’s turnkey project. “Facet is an OEM of various diabetic products, focusing on high-volume micro-overmolding. In fact, the facility in Atlanta has capacity to do more than 2 billion units of overmolded parts. We’re very familiar overmolding, with automation, working with large volumes, and using our OEM expertise to contract manufacture for one of the largest diabetes companies in the world. Through that customer we had the opportunity to overmold a stamped part,” Rogers said.
“But stamping was new to us. So as this project came onboard, I started looking around for a company I could partner with to help on that aspect.”
Goals for the Stamping Line
Facet’s goals for bringing the stamping process in-house were numerous. Paramount among them was quality control.
“Contract manufacturing is really understanding your customer; what their concerns are and making sure that you’re spec’ing out a system to fulfill those needs,” Rogers said. “What we definitely understood from them was that it is extremely important to have high accuracy and really robust inspection.”
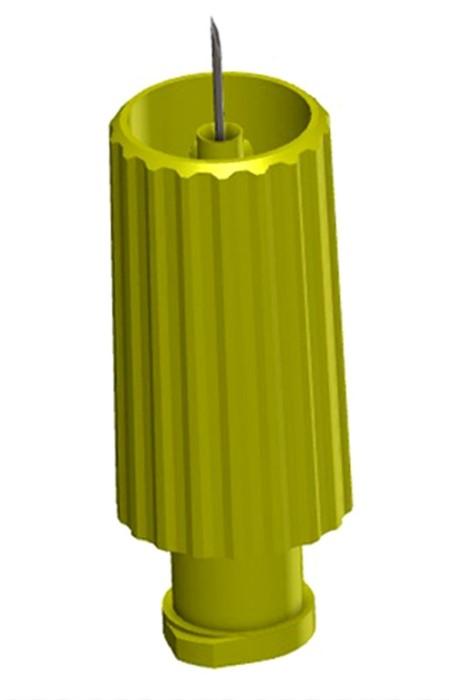
So much depends on a tiny, stamped needle for diabetic care in insulin delivery and glucose-level detection. The stamped, beveled needle itself is shorter than 1-in. It is overmolded for secure handling, to reduce discomfort, and to enhance performance.
Accuracy. The needle is less than 1 in. long. It is held in a carrier strip through the production process, similar to how lead frames are held. Even that carrier is only 1-1/4 in. wide. “This is a very, very small part,” Rogers said.
“Because the part is so small and the tolerances are quite tight—some tolerances on the part are in the 10s of microns—we needed a press that would be very accurate and very reliable over time,” Rogers said.
“This particular part goes into a subassembly where there are other surfaces that it’ll interact with. It’s critical that it doesn’t interact to where the frictional forces go up. This device is patient-contacting and patient-administered. It goes into the body and is retracted out, so it’s got to work every time.”
The defect rate had to be zero. “We just cannot produce rejects,” Rogers stated. “So you have to inspect every single part to meet that.”
Speed. The production line had to be able to handle the extremely high part volumes—hundreds of millions of needles.
Tool Life. Another goal was that the press would not hinder tool life. “While shortened tool life is not a risk to the patient, it’s a risk to the program. You want your tools to stay intact, last long, and produce identical parts as long as possible,” Rogers said.
Integrated. Finally, Facet wanted to integrate the stamping, assembly, molding, cleaning, and inspection.
The Search
Rogers said he views his role as an advocate for the customer within his organization. “If I were on the other side, what would I want out of a piece of equipment? The accuracy of the press and the tooling, the automation … it's just really important that you have very high confidence that the whole system is going to be able to achieve that. Plus, our lead time was pretty tight on this project. So you can't afford to pick a piece of equipment and find out it's not quite good enough.”
Rogers vetted several press companies, personally visiting and interviewing them, one of which was Ridgefield, N.J.-based OEM Bruderer Americas.
“Late on a Friday afternoon, I just cold-called them, and talked to AJ [Bruderer Americas President Alois J. Rupp]. We talked for over an hour. Getting up to speed on stamping myself, I asked him a lot of questions, which he quickly and thoroughly answered. He walked me through things that I should think about, such as a die house for developing the die. That was a great jumping-off point for this program,” Rogers said.
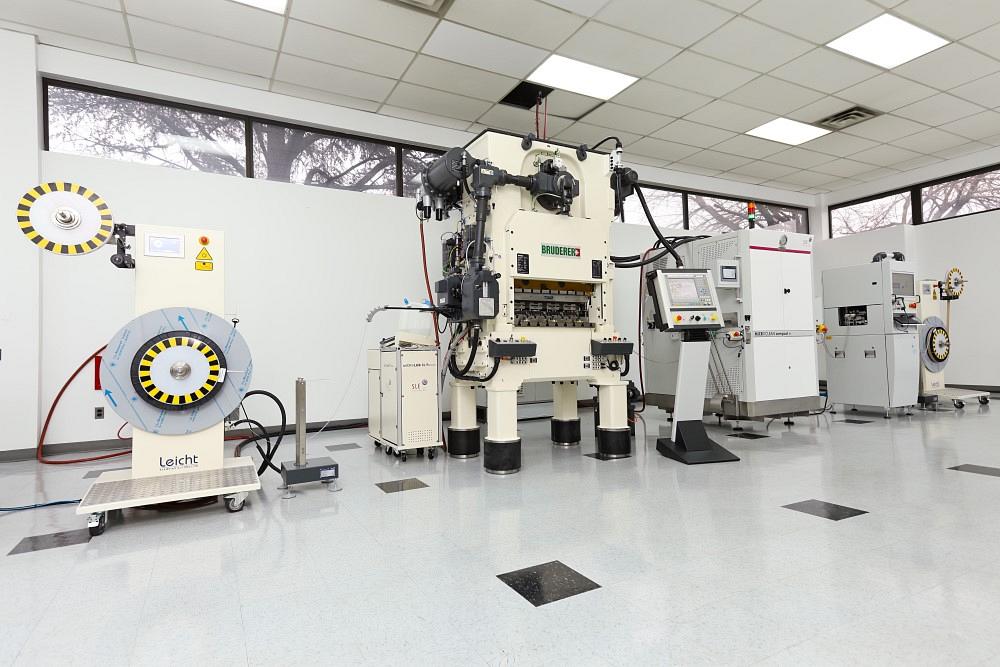
FIGURE 1. Facet Medical Technologies, which had never performed metal stamping before, installed a Bruderer high-performance, high-speed, 30-ton mechanical press line to stamp needles. It comprises a decoiler (left), which unrolls a coil of chemically etched stainless steel, which then enters an inline microlubricant station before entering the high-speed press. The lubricant is washed off in the next station before the stamped needles are inspected before being recoiled, ready for the overmolding line.
Rupp explained, “Facet needed both speed and precision. It needed the precision to ensure that they could make the same needle part every time, and it needed speed to be able to keep up with the volumes. Our high-speed presses are the fastest machines that are available and the most precise.
“One of the critical elements that makes the press so accurate is that we build a ram control system into our machine. We measure every stroke and we measure the most important features in the die. If there's any deviation, we can automatically correct that and move the ram a little further down or up to ensure that every single part is being made precisely the same.”
After conducting due diligence, Rogers hired Bruderer to install a high-speed stamping line and to integrate the stamping, molding, cleaning, inspecting, and material handling processes.
“The Bruderer press is a fantastic piece of equipment and best for our application for the accuracy that you get. And that precision also maximizes tool life. Plus, they build fully integrated systems, so I narrowed the selection down to them,” Rogers said.
An Integrated Ecosystem
Working with Facet, Rupp and his team developed a three-line solution comprising an automated precision stamping line, reel-to-reel overmolding line, and an aqueous cleaning line.
Bruderer engineered the system to intake the chemically etched stainless steel, precision-stamp the stainless steel into sharps, wash the lubricant off, then feed them through overmolding, run them through an aqueous cleaning stage, and inspect them again before packaging them.
“Step one was the stamping process (see Figure 1). Step two was the molding process (see Figure 2). And then, obviously, because the parts are going to be inserted into a human body, they needed to be cleaned. So the third line is just a dedicated aqueous cleaning line where the needles are cleaned,” Rupp said (see Figure 3).
After the sharps are stamped, they are processed in one of four injection molding lines. Facet sourced the molding machine and auxiliary equipment, which was integrated into the Bruderers America-designed overmolding strip handling operation. Completing the production system, the parts go through a final cleaning and inspection line.
Facet purchased the molding machines and Bruderer built the process, Rupp explained. “So we provided the decoiler, feeding system, and recoiler for the molding machines,” Rupp said. Bruderer provided and oversaw the installation of the controls, interlocks, power distribution, and all additional aspects required as well.
Etching, Positioning, Vision Inspection Are Mission-Critical
A unique aspect of the project was the extreme degree of accuracy required for a medical part that is intended to be inserted into a human being. That brought an additional wave of critical complexity for the material and process.
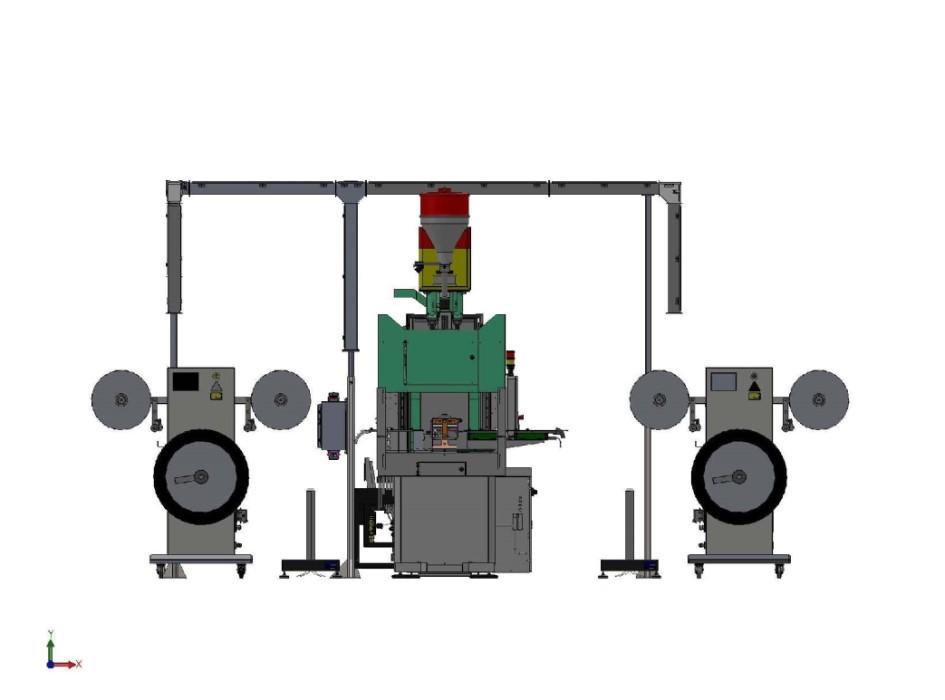
FIGURE 2. In the second line, the stamped needles, or sharps, are decoiled, overmolded, and recoiled.
Etching. First, chemical etching is used to achieve the blank. Rogers said, “Etching allows us to hit tolerances that you may not necessarily be able to hit by blanking in a stamping operation. Also, it provides an opportunity for unique features that cannot be done with the current technology around stamping. So, in this part, we're using the etching process to hit both—tight tolerances and unique features.
“We're receiving coils of the etched material and then we're feeding that material through the stamping die. But that poses challenges because all of your pilot holes are already made, and the core features of the part are already there. You're not blanking them inside the die. So you do have tolerance stackups that you have to think about, especially between plates. It's pretty tight, but it's not perfect. You have to deal with that as you're feeding it through the die.”
Inspection. Facet is doing 100% inspection of the millions of parts that it’s producing, Rogers said. “It's a big, big deal to inspect every one of those parts coming down the line for various features.”
The press runs at up to 2,000 parts per minute, so robust vision systems are especially critical at those high speeds.
The inspection system is highly specialized, Rupp said. “We installed cameras not only to check the overall geometry of the components, but also to very accurately measure the internal features of the needle. The only way we could do that was with a laser. So we have the two cameras working together with a laser to get the exact measurements needed.” The top-view camera has an optical resolution of 6.5 microns.
“We first check those measurements initially at the stamping stage, because those dimensions are defined as they’re forming the needle in the stamping process. We installed an inspection system there before they go on to the molding stage. Then we also put one last inspection system after the sharps are washed and before they’re packaged,” Rupp added.
The vision systems are equipped with a reject-part removal system. They will reject failed parts and keep track of the number rejected. If they see more than a specified number, they'll stop the process. This reduces scrap and ensures that only good parts are overmolded and shipped.
Overmolding Positioning. With any insert molding application, part placement is key, Rogers said. “If the part is placed correctly into the mold and it indexes correctly into the right location, you know that it's the best place to be; then it's repeatable. We have servo feed and indexers and we worked to make sure that the indexing was going to be really precise consistently,” Rogers said.
Overcoming Newness to Stamping, Etching …
The first challenge in bringing the stamping process in-house was just getting familiar with the technology, Rogers said. “Just understanding the application, how you go about stamping this product is the first thing.” He added, “If you're entering a new space, it's all about reducing risk. I felt like we accomplished that through open communication.”
The etching process was another area of unfamiliarity, he said. “So it was important to just kind of get familiar with that space and pick really good partners, frankly, to reduce risk and maximize the opportunity for success.”
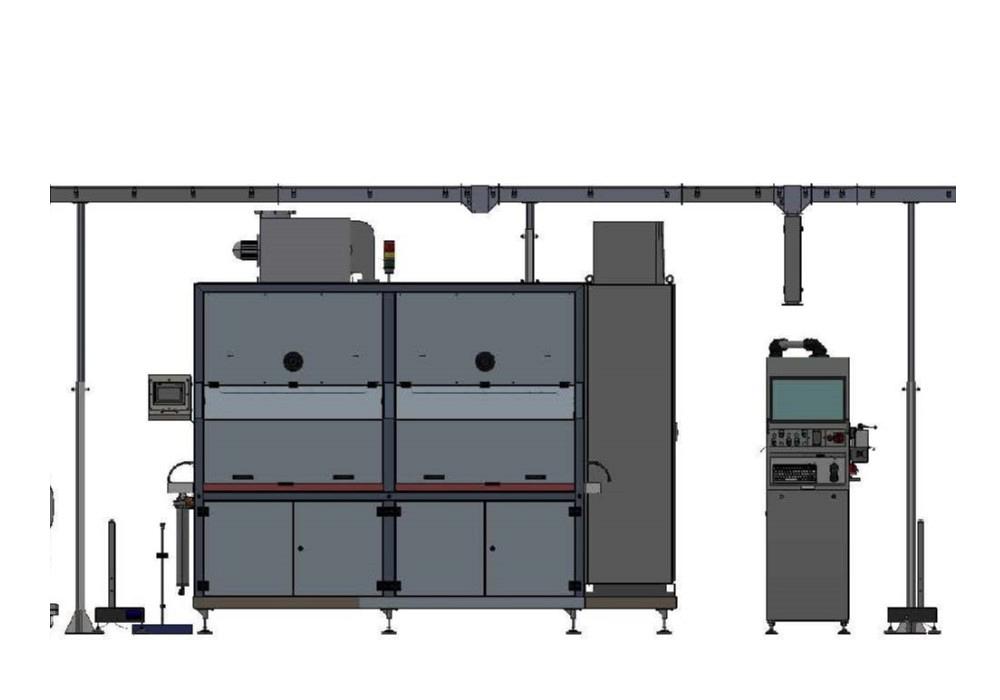
FIGURE 3. In the final line, the sharps are washed to a clean condition and inspected. Then the good parts are recoiled, ready for shipping to the customer.
Facet also sent pressroom personnel for training at the etching, molding, and press companies’ facilities.
... With Expertise, Project Management
Good project management documentation was required to meet medical industry standards and testing protocols. This included a thorough knowledge of the functional requirement specifications, scope of work, detailed design specifications, factory acceptance tests, testing the programmed system before delivery, and the site acceptance test.
As the system integrator, Bruderer created documentation to support the work required, including equipment drawings such as schematics, enclosures, pipe schedules, I/O lists, HMI screen prints and report formats, and guiding the project and subcontractors toward complete installation. “What we received in addition to the equipment was a valuable network – an entire ecosystem of stamping, strip handling, molding, cleaning, and inspection expertise,” Rogers added.
Up and Running, Growing
Facet Medical currently produces at a rate of more than 100 million sharps annually, Rogers estimated.
Its production line for the large medical OEM customer is growing very quickly. “Production is significantly up quarter over quarter and our customer is very happy with the quality,” Rogers said. “We’re in the midst of moving forward on new commercial opportunities and planning how to expand and grow line capacity.”
Facet has since successfully bid and won an additional large-scale program.
“From the beginning, Facet saw this as an opportunity to push the boundaries of our knowledge base and expand into an adjacent manufacturing technology,” Rogers said. “Finding the right partner and equipment solution was critical to realizing that vision.
“We now have a complete production system to intake raw materials and ship out sharpened, overmolded, cleaned, and inspected needles,” Rogers said.
Rupp added, “Facet Medical is, in my opinion, one of the best examples of a successful complex, turnkey customer.”
About the Author
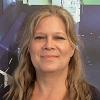
Kate Bachman
815-381-1302
Kate Bachman is a contributing editor for The FABRICATOR editor. Bachman has more than 20 years of experience as a writer and editor in the manufacturing and other industries.
Related Companies
subscribe now
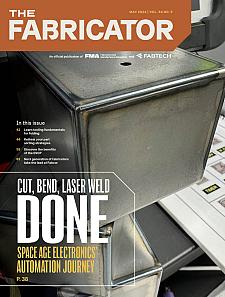
The Fabricator is North America's leading magazine for the metal forming and fabricating industry. The magazine delivers the news, technical articles, and case histories that enable fabricators to do their jobs more efficiently. The Fabricator has served the industry since 1970.
start your free subscription- Stay connected from anywhere
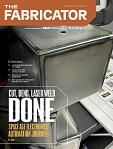
Easily access valuable industry resources now with full access to the digital edition of The Fabricator.
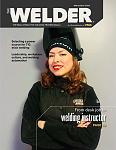
Easily access valuable industry resources now with full access to the digital edition of The Welder.
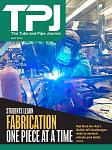
Easily access valuable industry resources now with full access to the digital edition of The Tube and Pipe Journal.
- Podcasting
- Podcast:
- The Fabricator Podcast
- Published:
- 04/16/2024
- Running Time:
- 63:29
In this episode of The Fabricator Podcast, Caleb Chamberlain, co-founder and CEO of OSH Cut, discusses his company’s...
- Trending Articles
Tips for creating sheet metal tubes with perforations
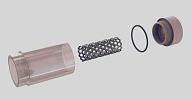
JM Steel triples capacity for solar energy projects at Pennsylvania facility
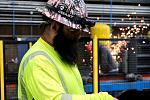
Are two heads better than one in fiber laser cutting?
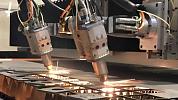
Supporting the metal fabricating industry through FMA
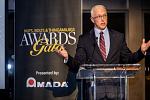
Omco Solar opens second Alabama manufacturing facility
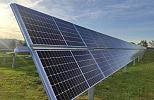
- Industry Events
16th Annual Safety Conference
- April 30 - May 1, 2024
- Elgin,
Pipe and Tube Conference
- May 21 - 22, 2024
- Omaha, NE
World-Class Roll Forming Workshop
- June 5 - 6, 2024
- Louisville, KY
Advanced Laser Application Workshop
- June 25 - 27, 2024
- Novi, MI