- FMA
- The Fabricator
- FABTECH
- Canadian Metalworking
Categories
- Additive Manufacturing
- Aluminum Welding
- Arc Welding
- Assembly and Joining
- Automation and Robotics
- Bending and Forming
- Consumables
- Cutting and Weld Prep
- Electric Vehicles
- En Español
- Finishing
- Hydroforming
- Laser Cutting
- Laser Welding
- Machining
- Manufacturing Software
- Materials Handling
- Metals/Materials
- Oxyfuel Cutting
- Plasma Cutting
- Power Tools
- Punching and Other Holemaking
- Roll Forming
- Safety
- Sawing
- Shearing
- Shop Management
- Testing and Measuring
- Tube and Pipe Fabrication
- Tube and Pipe Production
- Waterjet Cutting
Industry Directory
Webcasts
Podcasts
FAB 40
Advertise
Subscribe
Account Login
Search
Press brake strategies for T6 aluminum; sharp bending insights
- By Steve Benson
- September 14, 2021
- Article
- Bending and Forming
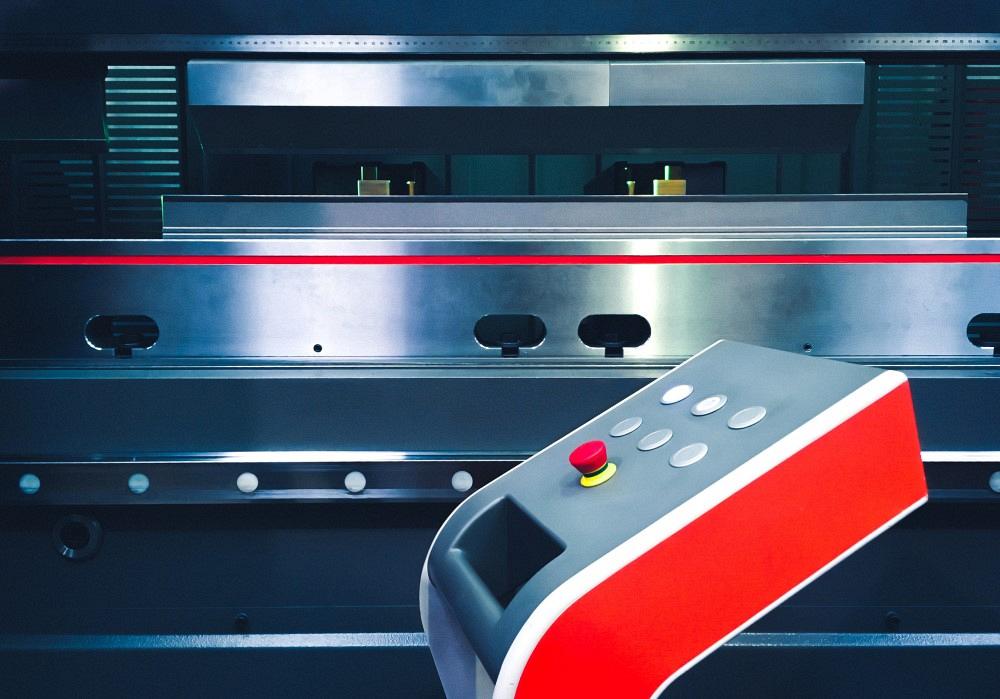
Press brake guru Steve Benson covers the sharp bend’s parabola as well as strategies for bending high-temper aluminum. Getty Images
This month I continue to work through a backlog of emailed questions. They involve one question about bending sharp and two more about the bending of T6 aluminum. The first covers a sheet metal application, and the second is a question on bump-bending thick 6061-T6 plate.
If you haven’t received an answer yet, know that one will be coming. Thanks to you all for your questions and your patience. Although I might be slow to respond, please don’t hesitate to drop me a line.
The Parabola When Bending Sharp
Q: I am researching air bending on the press brake, and I have a question about predicting the inside bend radius. You’ve described how a parabola forms during bending. Why does this happen, exactly, and how does this affect process repeatability?
A: Predicting the inside bend radius should be a relatively simple task. However, it is not. The repeatability of the press brake’s stroke at a few microns is phenomenal, as is the precision of modern tooling, with tolerances often as close as 0.0008 in. However, precision air bending still must deal with variabilities in the material.
Sheet metal tolerances vary greatly from piece to piece, sheet to sheet, and supplier to supplier. No two pieces of the same material type are the same over a wide range of material properties. Your part tolerances always should be generous enough to allow you to create functional parts, considering all of the possible variables within the material.
For instance, the thickness tolerance for 16-ga. sheets ranges from 0.053 to 0.067 in. The tensile strength ranges from 58 to 80 KSI. They also have a tolerance in yield strength. Any measurable aspect of the material will have a tolerance zone applied to it. Then there’s the material’s crystal and grain size and whether you are bending across or with the grain. All of this affects the final inside bend radius.
Then you need to consider the effects of a sharp bend radius. A sharp bend is defined as the point where the area of contact between the punch nose and the material is so small and the forming pressure is high enough to cause the punch nose to penetrate the material surface. This elongates the bend from an actual radius to more of a parabolic shape, causing the inside bend radius to vary. This in turn affects the bend allowance, outside setback, and bend deduction. (For more on this, you can check out “How to calculate the air-formed radius of different bend angles.”)
If you can avoid bending sharp by, for instance, keeping the ratio of the inside bend radius to material thickness as close as possible to a one-to-one relationship (that is, your inside bend radius equals or is close to your material thickness), your air-bending accuracy and repeatability will improve. But if you can’t avoid bending sharp, your part tolerances should take this variability into account.
Temper, Temper, Temper (of Aluminum)
Q: I need to bend 6082 and 6061 aluminum in the T6 state. What strategies would you suggest? Is using cast material an option?
A: As far as bending a casting goes, that is not going to happen. Cast material does not form. It just breaks! But there are ways to bend sheet aluminum in the T6 state. They’re not easy or consistent, and the reasons why build upon the previous question’s answer.
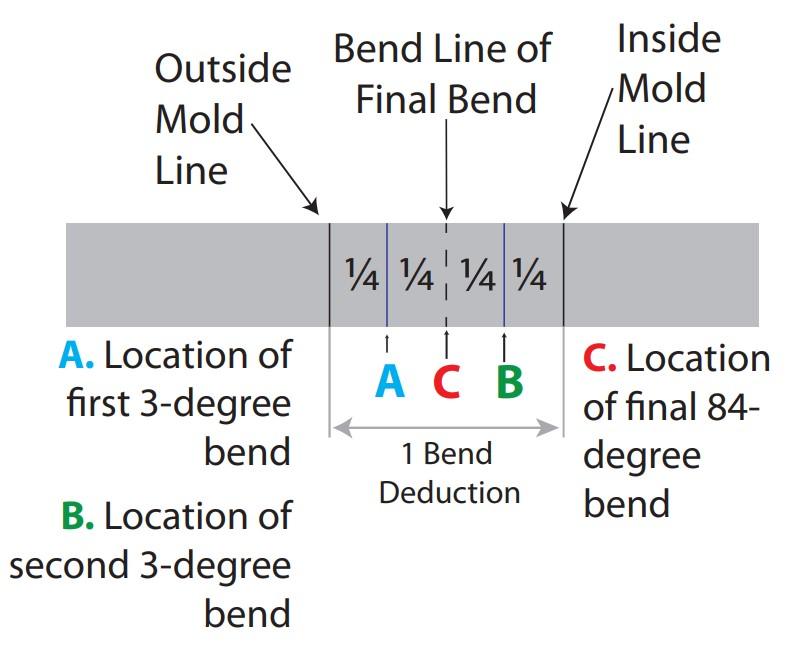
FIGURE 1. Step bending can help you achieve a 90-degree bend in 6061-T6 aluminum without cracking. Note, however, that this increases the bend radius slightly, which changes your bend deduction. To accommodate for this, you might need to change the flat part dimensions.
The first would be to heat the part with an acetylene torch. Using a rosebud tip, gradually heat the bend line back and forth down the entire length of the bend. This process will anneal (soften) the material and allow it to form without cracking or breaking.
This process, though, has three significant problems. First, the heating will most likely change the temper at the bend line, requiring it to be brought back to its original temper.
Another issue has to do with how aluminum behaves when heated. Unlike steel, aluminum does not change color when heated. Consequently, getting badly burned then becomes a real possibility.
When you heat steel and it gets too hot, you will see that it is about to blow through the material, creating a hole. Granted, it does take a practiced eye to see it, but with experience you should see the potential blow-through coming. With aluminum, however, even the most practiced eye cannot see it coming. All of a sudden, excessive heat will just blow through the sheet.
Aluminum melts from the inside out. The melting happens this way because unfinished or untreated aluminum, as a result of its natural reaction with oxygen, forms an aluminum oxide coating on all exposed surfaces. Aluminum itself melts at around 1,200 degrees F, while aluminum oxide melts at about 5,000 degrees F.
The most practical way to form sheet aluminum in the T6 state is to use a three-step bump radius bending strategy. As a rule, 6061-T6 aluminum sheet will only bend to an external angle of 84 degrees before cracking or breaking. This bend angle leaves you with a 6-degree deficit to achieve a 90-degree bend.
To correct for this, start with the bend deduction between the inside and outside mold lines on the part layout. Divide that value by 4. Now, measure this value from the bend centerline toward the mold lines; this is halfway between the bend line and the mold line, where the first hit of 3 degrees is made. Then add one-half of the bend deduction to that first location and bend another 3 degrees there. Finally, gauge the part so that your third hit contacts the center of the bend, where you can put the remaining 84 degrees of bend into the part and make the total bend angle 90 degrees (see Figure 1).
This kind of step bending will increase the inside bend radius slightly. Any increase in the inside bend radius will change the bend deduction and cause the flat blank to change. To accommodate the new inside radius of the flat part, you need to change the bend deduction and maybe change the flat part.
Bumping at the Perfect Pitch
Q: I am bump forming 0.750-in.-thick 6061-T6 aluminum. The bend length is 2 in. I need to achieve an inside radius of 4.50 in. at an open angle of 142 degrees (external angle of 38 degrees). I am using a 0.500-in.-radius punch and a die with a 2-in. V opening. I’m performing 30 bends at about 4 degrees each, with a pitch (space between bumps) of 0.125 in.
I achieved the angle. However, the radius is about 6.50 in. What do I need to change to get the radius tighter? Should I use another die opening, punch tip, or pitch? The part is thick, so penetrating too far is not an option. Decreasing the V opening is problematic because I'm afraid of the excessive tonnage. What do you think?
A: Changing the radius pitch to a smaller value is the answer, and here is why. Because you are bending to an angle of only 4 degrees, the contact area between the punch tip and the material is minimal, not much more than a line. And your punch radius is large enough not to create a sharp-bend situation with the material. (For more on sharp bends, see “What makes an air bend sharp on the press brake.”)
Changing to a narrower die opening will, as you noted, raise the required tonnage, increase your chances of overloading the press brake, and possibly cause a sharp bend even with your 0.500-in. punch nose radius. A smaller die opening will also increase variations in bend angle, none of which will change the bump-formed inside radius.
When setting up a bump-forming operation, you calculate the distance around the inside radius and divide that value by the number of times you want to bump the bend. For more on this, see “Precision sheet metal bending, bump by bump.”)
You mention that your inside bend radius is coming out too large. It might be because of the material’s temper, tensile, yield, or variations in springback. In this case, shortening the distance between each hit will make a smaller inside bend radius. Note that you will most likely need to add a little more angle to each hit to make it work.
About the Author
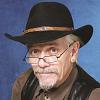
Steve Benson
2952 Doaks Ferry Road N.W.
Salem, OR 97301-4468
503-399-7514
Related Companies
subscribe now
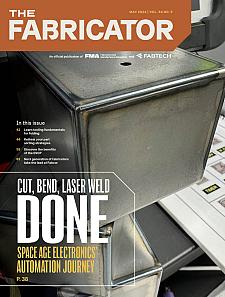
The Fabricator is North America's leading magazine for the metal forming and fabricating industry. The magazine delivers the news, technical articles, and case histories that enable fabricators to do their jobs more efficiently. The Fabricator has served the industry since 1970.
start your free subscription- Stay connected from anywhere
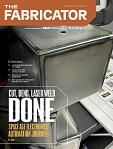
Easily access valuable industry resources now with full access to the digital edition of The Fabricator.
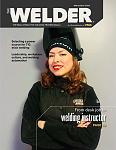
Easily access valuable industry resources now with full access to the digital edition of The Welder.
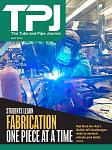
Easily access valuable industry resources now with full access to the digital edition of The Tube and Pipe Journal.
- Podcasting
- Podcast:
- The Fabricator Podcast
- Published:
- 04/16/2024
- Running Time:
- 63:29
In this episode of The Fabricator Podcast, Caleb Chamberlain, co-founder and CEO of OSH Cut, discusses his company’s...
- Trending Articles
Tips for creating sheet metal tubes with perforations
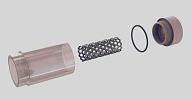
JM Steel triples capacity for solar energy projects at Pennsylvania facility
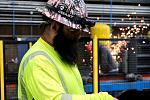
Are two heads better than one in fiber laser cutting?
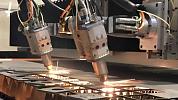
Supporting the metal fabricating industry through FMA
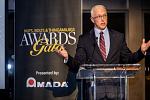
Omco Solar opens second Alabama manufacturing facility
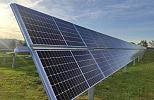
- Industry Events
16th Annual Safety Conference
- April 30 - May 1, 2024
- Elgin,
Pipe and Tube Conference
- May 21 - 22, 2024
- Omaha, NE
World-Class Roll Forming Workshop
- June 5 - 6, 2024
- Louisville, KY
Advanced Laser Application Workshop
- June 25 - 27, 2024
- Novi, MI