Contributing editor
- FMA
- The Fabricator
- FABTECH
- Canadian Metalworking
Categories
- Additive Manufacturing
- Aluminum Welding
- Arc Welding
- Assembly and Joining
- Automation and Robotics
- Bending and Forming
- Consumables
- Cutting and Weld Prep
- Electric Vehicles
- En Español
- Finishing
- Hydroforming
- Laser Cutting
- Laser Welding
- Machining
- Manufacturing Software
- Materials Handling
- Metals/Materials
- Oxyfuel Cutting
- Plasma Cutting
- Power Tools
- Punching and Other Holemaking
- Roll Forming
- Safety
- Sawing
- Shearing
- Shop Management
- Testing and Measuring
- Tube and Pipe Fabrication
- Tube and Pipe Production
- Waterjet Cutting
Industry Directory
Webcasts
Podcasts
FAB 40
Advertise
Subscribe
Account Login
Search
Press tech showstoppers at FABTECH
What’s new, what’s cool, what’s pressing
- By Kate Bachman
- October 6, 2017
- Article
- Bending and Forming
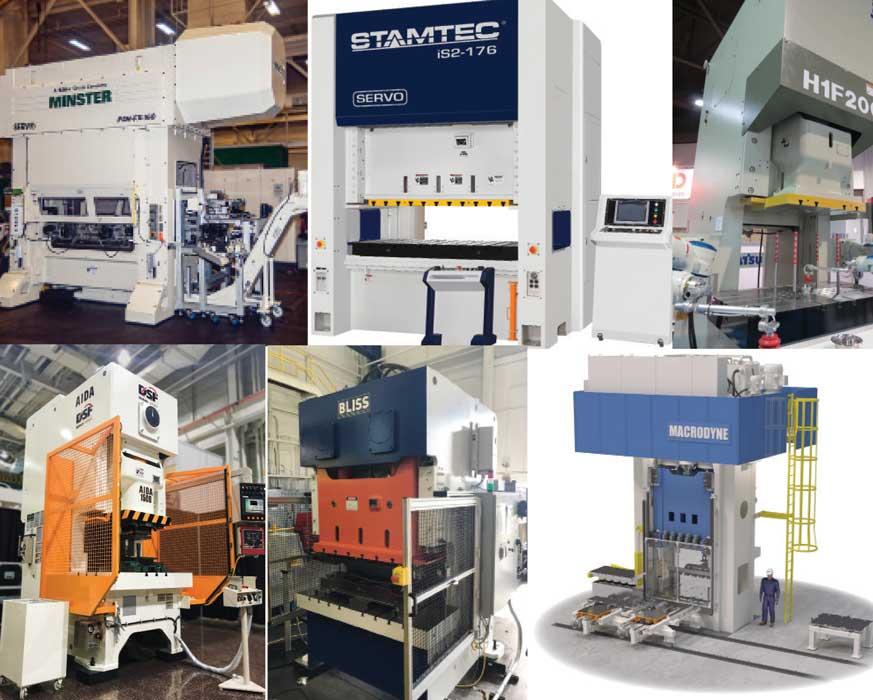
Presses—at the center of all stamping technology—will be alive and kicking at FABTECH® 2017 in transportation mecca Chicago. Exhibitors include Nidec Minster, Stamtec, Komatsu, AIDA, Bliss (Schuler), and Macrodyne.
Chicago has long been known as a transportation hub. Being located at the intersection of east-west routes and north-south corridors and at the southwestern most end of the interconnected Great Lakes, it has become the crossroads of industry and commerce as well. Its first-class intermodal system comprising freight rail, commuter train, elevated “L” passenger rail system, buses of all sorts, vehicular highways, airports, bicycle networks, walkways, pedways, and shipping and ferry waterways makes it one of the best—and busiest—mass and individual transportation systems.
Stamping manufacturers and metal fabricators will converge on Chicago at FABTECH® 2017, Nov. 6-9, at McCormick Place. The event will be a microcosm of the city’s transit system, with attendees traversing the exhibit floor, hustling to conference sessions and demonstrations, and observing machines in motion.
If you plan to go, you’ll have a multitude of transportation means to do so. No matter how you get there, get there—and once you are there, veer to the southwest area of the South Hall, where all things stamping will be humming, buzzing, clanking, and whirring.
As you traverse the exhibition floor, you’re likely to find yourself drawn to the pounding rhythms of the presses on display. After all, while all the metal forming equipment exhibits are important, the presses truly are the heartbeat of the show.
This year’s exhibits are dominated by technology that puts you in the driver’s seat: motion control, energy management, and monitoring devices.
1. Martensitic Steel, Formed and Served Cold
SEYI-America. Forming martensitic ultrahigh-strength steel is very challenging (springback, anyone?) and usually done in a hot stamping process. SEYI (Booth A5225) will be cold forming Docol 1,500M (1,500-MPa tensile strength) martensitic steel in a single hit in its SD1-220 servo press, using the specialized motions that only a servo press can offer, the company said (see Figure 1).
“We will be showcasing our direct-drive servo press technology with our second-generation, high-torque, low-RPM servomotors that are designed exclusively for the stamping press market,” said Scott Braito, a director of sales for large press systems. Paired with fast-response controls, the motors allow for unique control of slide speed, position, and direction.
In addition, the company will demonstrate single-station deep-drawing of DC06 draw-quality steel on the servo press. “Using the Vibration motion, we will produce a part with a 50.7 percent draw ratio in a single hit. The process will generate minimal heat, allowing the part to be handled with bare hands as soon as it exits the die,” Braito said.
The system offers energy control, too. Capacitor bank energy storage provides instant, clean power to the press, eliminates surges on incoming supply power, and reduces overall energy usage compared to a conventional press by up to 40 percent, according to Braito.
SEYI’s direct-drive servomechanical presses range from 88 to 1,760 tons.
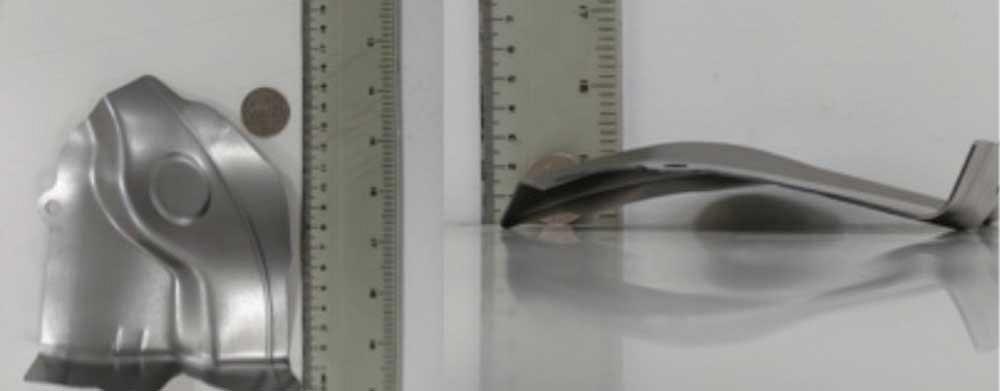
Figure 1
SEYI will demonstrate the cold-forming of martensitic steel, usually done on a hot-forming press.
Of course, several other press manufacturers are serving up servo technology at the show.
2. Low Inertia, High Acceleration and Deceleration
Nidec Minster (Booth A5706) will demonstrate how the industry-unique low-inertia drive of its P2H-FX servo press facilitates higher acceleration and deceleration rates, which contribute to increased productivity, a reduced stopping angle, and higher overall efficiency, according to Jim Schulte, general manager, servo and contract products.
The nonproprietary Siemens servo-motors that drive the press are equipped with a liquid cooling technology that helps maintain thermal stability and cooler operating temperatures. These characteristics contribute to a more energy-efficient operation, longer component life, and a cleaner operating environment, the company says.
Engineered from Minster’s legacy Piece-Maker design, the P2H-FX is precision-built from a cast-iron frame and an eccentric shaft forged from high-strength alloy steel for a 50 percent reverse load rating and a full press tonnage rating.
The press will be demonstrating its other high-performance characteristics, slide motions, and production capabilities, the company said.
3. Stroke Profiles to Stampings
Stamtec (Booth A5431) will stamp parts in a servo press and feed line, demonstrating various operating modes and stroke profiles that showcase the advantages and versatility of servo technology (see Figure 2). The company’s compact servo feeder/straightener/uncoiler production line is integrated and synchronized with its model iS2-176 two-point, 176-ton straight-side servo press.
The servo presses are powered by all-Siemens servo systems, including motors, drives, motion controllers, press controls, Simo-Press software, and HMI, said Lee Ellard, national sales manager.
4. Onboard Speed Override
Komatsu. At Komatsu’s servo press (Booth A5231), visitors can see how an operator can set all slide motion parameters, including a speed override provision that slows the press speed during production. This allows him or her to view in-die processes such as cam timing and pilots release while the press is still producing parts. A servo drive maintains full energy regardless of speed.
“The built-in, onboard monitor displays slide motion parameters like velocity, dwell, and material touch points,” said Jim Landowski, vice president. A load monitor shows how much energy is being consumed or saved.
The press features automatic settings by part number for control of slide position, speed, cam settings, and load monitor limits, he added.
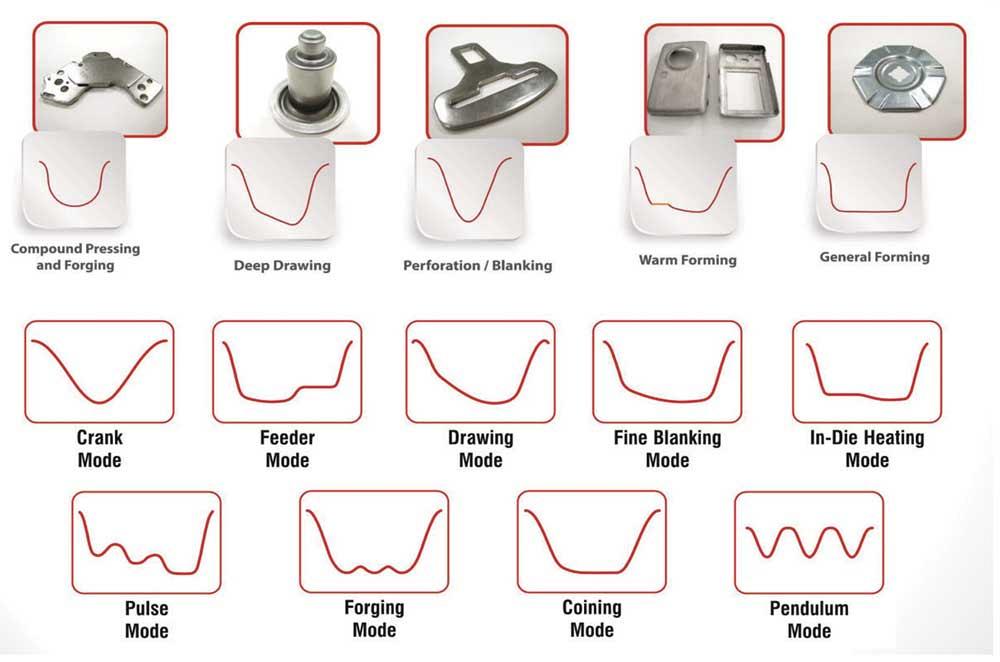
Figure 2
Stamtec will demonstrate how various operating modes and stroke profiles relate to the types of operations that can be done on its servo press.
The company will demonstrate its own press diagnostic and PM system, which not only monitors press conditions and sends notifications through the internet to smartphones and other devices, but also monitors other press system components, such as the coil line, lasers, welders, and robotics.
5. Silent Blanking; Machined to Stamped Conversion
AIDA-America (Booths A5425 and A5624) will demonstrate servo press technology versatility on two presses.
In a countermove to the typical loud pounding, clanging, and whirring of mechanical and hydraulic presses, an AIDA DSF-C1-1500, a 150-ton, gap-frame servo press, will be blanking HSLA material in silent blanking mode, which can only be achieved using a servo press, according to Shrinivas Patil, product manager.
In addition, a DSF-N2-3000, 300-ton, two-point, unitized frame servo press will be part of a full production line producing near-net-shape fine-blanked parts that have been redesigned as stampings, originally manufactured by machining. The demonstration is intended to show how the servo press technology’s accuracy and programmability facilitate the transition of a machined part to a more efficient and economical stamped part.
The presses are part of the OEM’s fleet of servo and mechanical stamping presses ranging in capacity from 30 to 4,000 tons, from 1 to 1,500 SPM, from gap-frame to straight-side, high-speed to cold forging, transfer and progressive die.
6. Virtual Press Design,
Real Time
Beckwood Press Co. (Booth A5448) will introduce LaunchTM, a virtual press design platform that uses real-time data to generate concept drawings on-site (see Figure 3). Visitors can work with company personnel at the simulator to input their own variables and parameters to flesh out their press concepts—right on the show floor.
Visitors will be able to discuss their applications with staff to determine which press options and features would be most beneficial for their operations. Once the general specs have been determined, visitors can “launch” their designs by choosing a frame style (two-post, four-post, gib, or C-frame). Next, they can add general specifications such as bed size, tonnage, speed, stroke, and heat parameters. Then they can finish by adding desired production system options, such as quick die change, shuttles, light curtains, reservoir location, and variable-frequency drives.
Once all known parameters have been entered, the software generates a preliminary sketch that can be used as a starting point for further discussions. As the project progresses, the sketch specifications (and subsequent pricing) can be revised to reflect the most recent updates.
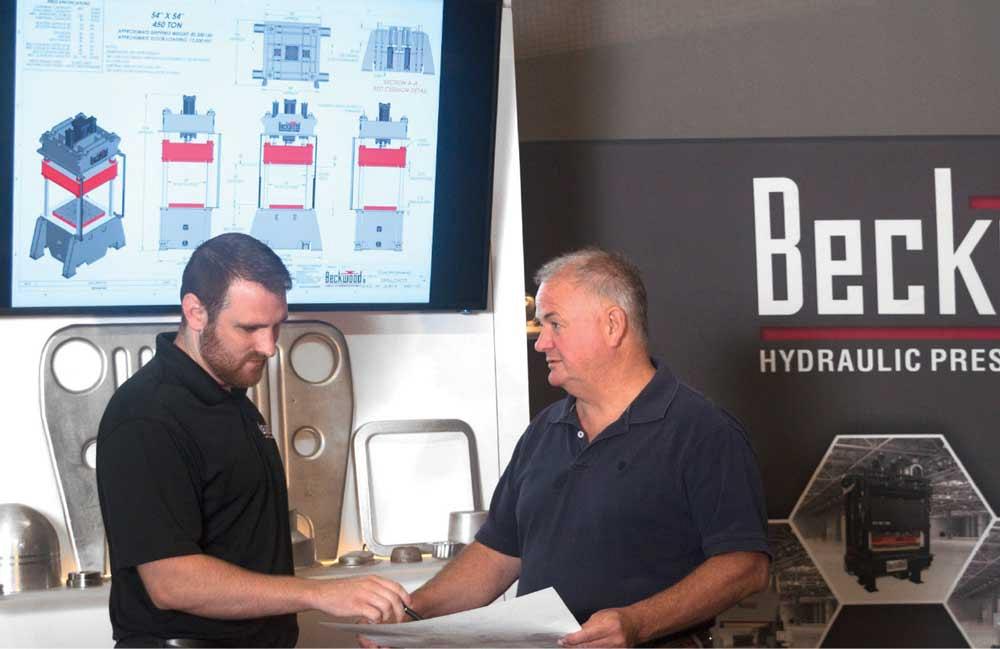
Figure 3
FABTECH attendees will be able to custom-build a press on the exhibit floor, virtually, with Beckwood Press Co.’s LaunchTM.
“We are all really excited about the Launch simulator. This is the first time that we will be able to showcase our ability to engineer just about anything that can be dreamed up,” said Christie Williams, technical marketing manager. “It is sometimes difficult to illustrate to prospective customers all of the options available for new machinery.
“Too often we have had to rely on showing photos and specs of presses that are ‘similar’ to someone’s application. Now we can create real-time machine models designed specifically for the user’s application and production needs. This is a game-changer.”
7. Energy-conserving, Space-conserving Servo Cushion
FAGOR Arrasate (Booth A5269) will showcase its recently developed cushion concept that improves some aspects of the conventional servo hydraulic cushion (see Figure 4). According to the company, the mechanically driven, servo-controlled new e-cushion offers several advantages over conventional servo hydraulic cushions: 74 percent less energy consumption, reduced pit area occupation, and reduced maintenance.
In addition, the press OEM will highlight its servo mechanical transfer press, said Victor Esteban, business development director, automotive division. “Now hot forming of boron steels can be processed in multistep installations that offer reduced cycle time because they work in continuous mode. Additionally, energy consumption is also reduced because the servo mechanical presses conserve more than 50 percent of energy when compared to equivalent hydraulic presses.”
8. Old Is New and New Is Back
Schuler. Seeing the legacy Bliss brand name on a press on the show floor (Booth A5031) may cause some to blink and do a double-take. First relaunched at last year’s FABTECH, Schuler’s Bliss brand will showcase its newest addition to the Bliss fleet, C1-125 mechanical gap-frame press.
The 125-metric-ton stamping press
produces at 30 to 60 SPM. It is equipped with an Allen-Bradley controls system, a hydraulic overload system, Ross valves, Siemens drive motor, Grayco lubrication, OMPI clutch, and flywheel brake. The bolster size is 47.2 by 28.3 inches.
In addition, Schuler will present its new Pressure Controlled Hardening (PCHflex) technology for improved hot stamping. By controlling pressure during hardening, press force can be distributed evenly over the part. The flexible bed cushion ensures a uniformly high contact pressure, resulting in cooling time that is only half that of conventional methods and an optimized metallurgical transformation process.
9. Mammoth Hydraulic
Macrodyne Technologies Inc. (Booth A5063), manufacturer of heavy-duty hydraulic presses up to 20,000 tons and fully automated press lines and die handling equipment for dies weighing more than 100 tons, will highlight its ability to build presses up to 50 ft. tall.
Its hydraulic presses and press lines power general metal forming applications, hot stamping, deep drawing, forging, extrusion, coining, die spotting, and hydroforming.
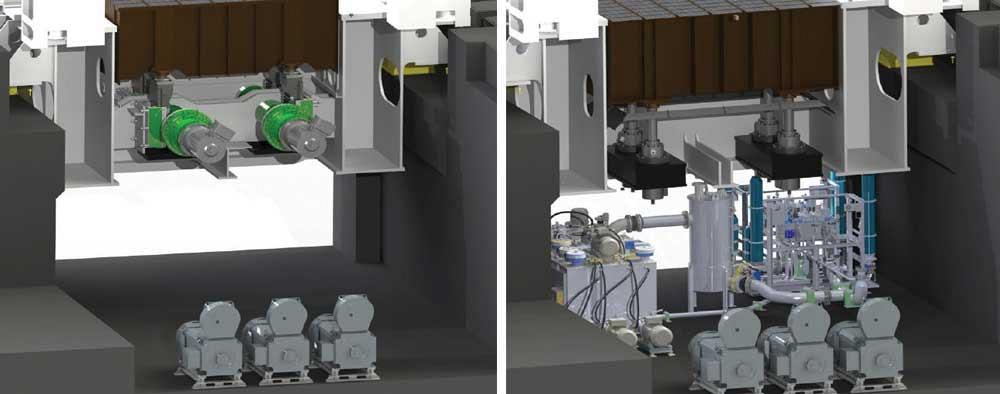
Figure 4
FAGOR Arrasate will showcase its new cushion concept (at left) that uses 74 percent less energy than a conventional servo-hydraulic cushion and reduces the pit space it occupies. Images courtesy of Fagor Arrasate, S.Coop.
AIDA-America Corp., www.aida-america.com
Beckwood Press Co., www.beckwoodpress.com
FAGOR Arrasate, www.fagorarraste.com
Komatsu, www.komatsu.com
Macrodyne, www.macrodynepress.com
Nidec Minster, www.minster.com
Schuler Inc., www.schulergroup.com
SEYI-America Inc.,www.seyi.com
Stamtec, www.stamtec.com
About the Author
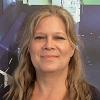
Kate Bachman
815-381-1302
Kate Bachman is a contributing editor for The FABRICATOR editor. Bachman has more than 20 years of experience as a writer and editor in the manufacturing and other industries.
subscribe now
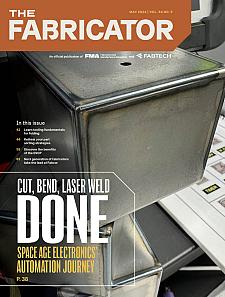
The Fabricator is North America's leading magazine for the metal forming and fabricating industry. The magazine delivers the news, technical articles, and case histories that enable fabricators to do their jobs more efficiently. The Fabricator has served the industry since 1970.
start your free subscription- Stay connected from anywhere
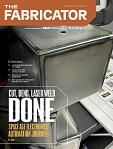
Easily access valuable industry resources now with full access to the digital edition of The Fabricator.
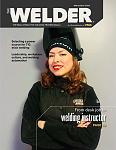
Easily access valuable industry resources now with full access to the digital edition of The Welder.
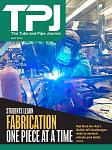
Easily access valuable industry resources now with full access to the digital edition of The Tube and Pipe Journal.
- Podcasting
- Podcast:
- The Fabricator Podcast
- Published:
- 04/16/2024
- Running Time:
- 63:29
In this episode of The Fabricator Podcast, Caleb Chamberlain, co-founder and CEO of OSH Cut, discusses his company’s...
- Trending Articles
Tips for creating sheet metal tubes with perforations
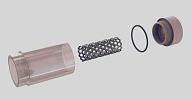
JM Steel triples capacity for solar energy projects at Pennsylvania facility
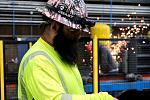
Are two heads better than one in fiber laser cutting?
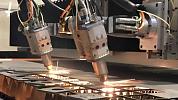
Supporting the metal fabricating industry through FMA
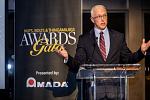
Omco Solar opens second Alabama manufacturing facility
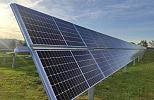
- Industry Events
16th Annual Safety Conference
- April 30 - May 1, 2024
- Elgin,
Pipe and Tube Conference
- May 21 - 22, 2024
- Omaha, NE
World-Class Roll Forming Workshop
- June 5 - 6, 2024
- Louisville, KY
Advanced Laser Application Workshop
- June 25 - 27, 2024
- Novi, MI