Graduate Research Associate
- FMA
- The Fabricator
- FABTECH
- Canadian Metalworking
Categories
- Additive Manufacturing
- Aluminum Welding
- Arc Welding
- Assembly and Joining
- Automation and Robotics
- Bending and Forming
- Consumables
- Cutting and Weld Prep
- Electric Vehicles
- En Español
- Finishing
- Hydroforming
- Laser Cutting
- Laser Welding
- Machining
- Manufacturing Software
- Materials Handling
- Metals/Materials
- Oxyfuel Cutting
- Plasma Cutting
- Power Tools
- Punching and Other Holemaking
- Roll Forming
- Safety
- Sawing
- Shearing
- Shop Management
- Testing and Measuring
- Tube and Pipe Fabrication
- Tube and Pipe Production
- Waterjet Cutting
Industry Directory
Webcasts
Podcasts
FAB 40
Advertise
Subscribe
Account Login
Search
R&D Update: Fundamentals and applications of deep drawing, Part I
- By Advaith Narayanan, David Diaz-Infante, Dr., and Taylan Altan, Ph.D.
- June 13, 2019
- Article
- Bending and Forming
In deep drawing, a flat blank is constrained by a blank holder, while the central portion of the sheet is pushed into a die opening with a punch to draw the metal into the desired shape without causing wrinkles or splits in the drawn part. Large parts, such as automotive doors and hoods, are drawn using draw beads and spacers (or standoffs) to control metal flow into the die cavity (see Figure 1).
The Use of Spacers and Draw Beads
Spacers, which are usually 10 or 15 percent thicker than the blank, are used to ensure that the die halves close in a parallel fashion, which then compensates for elastic deformations that may occur in the dies and press bed. Shims increase or decrease the height of the spacers during die tryout and in production to ensure appropriate metal flow and to eliminate wrinkles at desired locations in the die.
By restraining the metal flow, draw beads reduce the required amount of blank holder force (BHF) that usually is exerted by an air cushion, nitrogen cylinders, or a hydraulic cushion (see Figure 2). Several types of draw beads are commonly used (see Figure 3), and their dimensions depend on the sheet material strength and thickness and the press capacity. When draw beads are in use, the BHF must remain sufficient to keep the die and spacers in contact throughout the forming operation.
When spacers are used, the die and blank holder are pressed against the spacers. At the start of the stroke, the blank is free to flow into the die cavity with the relative movement of the punch against the die. As deformation and punch stroke proceed, the edges of the blank become thicker at the corners of the part, and some minor wrinkling may occur in the flange region. The blank thickness and wrinkle height increase but cannot exceed the clearance between the die and blank holder, provided by the spacers, if the BHF is sufficiently large. At this stage in drawing, the blank holder controls the material flow. The force exerted by the deforming blank upon the die and blank holder increases, while the contact among the die, blank holder, and spacers is maintained.
The heights and locations of the spacers usually are determined during tryout through several trial-and-error stampings. Recently Audi developed a laser sensor that measures the flange draw-in (see Figure 4). A control algorithm and a small servomotor activate an adjustable spacer to the optimal value. Called the Intelligent Tool, the laser sensor now is used in production at Audi.
Drawing Without Draw Beads
Deep drawing of small to medium-size parts in transfer and progressive dies is accomplished without draw beads and spacers. Progressive dies perform a series of operations at several stations during each press stroke, shaping the workpiece as the strip moves through the die, with the partially formed parts transported by the strip. Metal flow from the flange into the die cavity is controlled by the pressure applied on the flange of the die, usually with mechanical or elastomer springs or nitrogen cylinders.
Whether or not draw beads are used in stamping, blank shape optimization is important (see Figure 5). The optimum blank shape can be determined with process simulation, using conventional codes such as PAM-STAMP.
About the Authors
Advaith Narayanan
Center for Precision Forming
The Ohio State University 1971 Neil Ave., Room 339 Baker Systems Engineering Building
Columbus, OH 43210
(614) 292-5063
David Diaz-Infante, Dr.
Servo Press Scientist
250 W 5th St.
Minster, OH 45865
o 419 628 2331, d 419 501 1890, m 419 733 7971
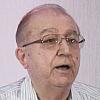
Taylan Altan, Ph.D.
Professor Emeritus and Director - Center for Precision Forming
Related Companies
subscribe now
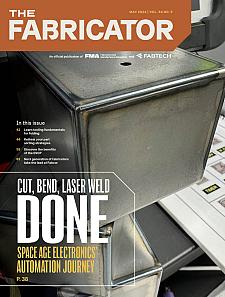
The Fabricator is North America's leading magazine for the metal forming and fabricating industry. The magazine delivers the news, technical articles, and case histories that enable fabricators to do their jobs more efficiently. The Fabricator has served the industry since 1970.
start your free subscription- Stay connected from anywhere
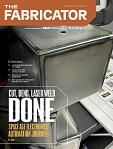
Easily access valuable industry resources now with full access to the digital edition of The Fabricator.
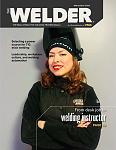
Easily access valuable industry resources now with full access to the digital edition of The Welder.
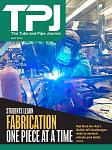
Easily access valuable industry resources now with full access to the digital edition of The Tube and Pipe Journal.
- Podcasting
- Podcast:
- The Fabricator Podcast
- Published:
- 04/16/2024
- Running Time:
- 63:29
In this episode of The Fabricator Podcast, Caleb Chamberlain, co-founder and CEO of OSH Cut, discusses his company’s...
- Trending Articles
Tips for creating sheet metal tubes with perforations
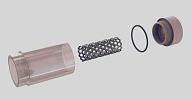
JM Steel triples capacity for solar energy projects at Pennsylvania facility
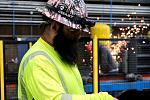
Are two heads better than one in fiber laser cutting?
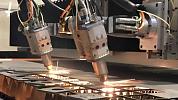
Supporting the metal fabricating industry through FMA
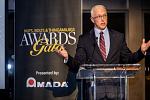
Omco Solar opens second Alabama manufacturing facility
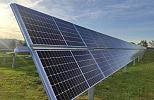
- Industry Events
16th Annual Safety Conference
- April 30 - May 1, 2024
- Elgin,
Pipe and Tube Conference
- May 21 - 22, 2024
- Omaha, NE
World-Class Roll Forming Workshop
- June 5 - 6, 2024
- Louisville, KY
Advanced Laser Application Workshop
- June 25 - 27, 2024
- Novi, MI