- FMA
- The Fabricator
- FABTECH
- Canadian Metalworking
Categories
- Additive Manufacturing
- Aluminum Welding
- Arc Welding
- Assembly and Joining
- Automation and Robotics
- Bending and Forming
- Consumables
- Cutting and Weld Prep
- Electric Vehicles
- En Español
- Finishing
- Hydroforming
- Laser Cutting
- Laser Welding
- Machining
- Manufacturing Software
- Materials Handling
- Metals/Materials
- Oxyfuel Cutting
- Plasma Cutting
- Power Tools
- Punching and Other Holemaking
- Roll Forming
- Safety
- Sawing
- Shearing
- Shop Management
- Testing and Measuring
- Tube and Pipe Fabrication
- Tube and Pipe Production
- Waterjet Cutting
Industry Directory
Webcasts
Podcasts
FAB 40
Advertise
Subscribe
Account Login
Search
The press brake questions keep coming
New versus used press brake equipment, bend function calculations for metal, and more
- By Steve Benson
- February 11, 2020
- Article
- Bending and Forming
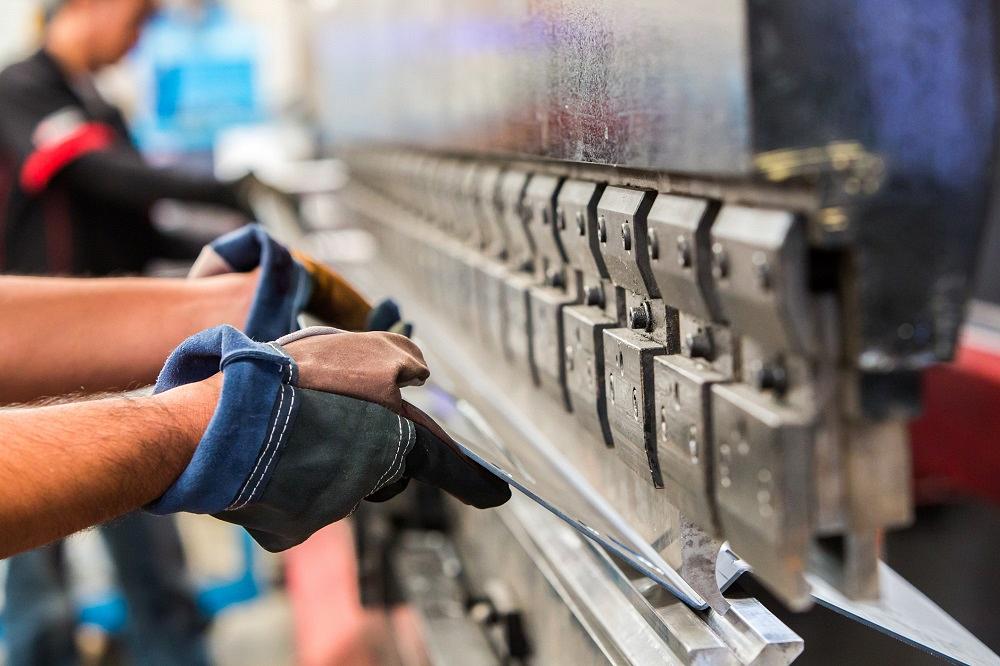
Press brake guru Steve Benson answers a list of reader questions regarding bend functions, equipment, tooling, and calculating the inside bend radius. Getty Images
In any given month, I receive quite a few emails and letters from readers throughout the world. While I respond to some, I receive far too many to respond to all of them promptly. For those who have been waiting, I apologize for the delay, and I hope that my tardy answers are still of some value to your day-to-day operations. On that note, on to the questions!
Should a School Buy New or Used?
Question: I’m a second-year metal fab instructor at a small vocational school. We just received a grant to purchase a new press brake. Currently we have a 135-ton, 10-foot press brake that uses traditional precision-planed tooling. I am looking for help deciding on what type of press brake and tooling to purchase. Should I buy new or used?
Naturally, being a school, we don’t make any specific products, nor are we a production shop. I want to make sure I get something that will benefit my students the most.
Answer: Congratulations on getting a grant to purchase a press brake for your class. If you have been reading my column for any length of time, you’ll already know I do not recommend any specific manufacturer, make, or model. I do this only to remain neutral and avoid promoting one brand over another.
I can still answer your question, though. First, I would not get rid of the press brake that you have and replace it with a state-of-the-art press brake with modern precision-ground tooling. While it would be wonderful if everyone were working with up-to-date press brakes and tooling, that’s not the reality of the shop environment. Many shops still use older press brakes, and some are hopelessly outdated and are museum pieces at best. Nonetheless, they’re out there and in use, and a well-trained operator needs to understand how these machines function, how to set them up, and how to operate them safely and efficiently.
At the same time, a solid working knowledge of the state-of-the-art is also necessary. If it were my choice, I would look for a 4- to 6-ft. machine with all the bells and whistles that I could get for the money.
However, I would stay away from any used equipment as you have no idea what the machine has been through. It has been my experience that most shops will keep the current press brake while adding a new machine, increasing the production capacity of the shop unless the press brake has an issue—in which case, they trade it in for the latest equipment. Of course, there are good used press brakes out there that become second-hand for other reasons: shop bankruptcy, for example. But again, which one is the good one?
The same goes for press brake tooling. Your students need to learn the differences between planer tooling and precision-ground tooling, how they are set up and used, and what the limitations are. For example, planer tooling is not well-suited for staging, or stage bending. At the same time, older precision-ground tools can throw shrapnel if overloaded with tonnage.
When it comes to press brake tooling, I have only three words of advice: Don’t buy used! There might be a tool or two that will be in good shape, but by the time you get to the bottom of the pile, you’ll find junk tooling.
By the way, I have a textbook that you might want to consider using for teaching your class. It’s titled Bending Basics and is available through the Fabricators & Manufacturers Association.
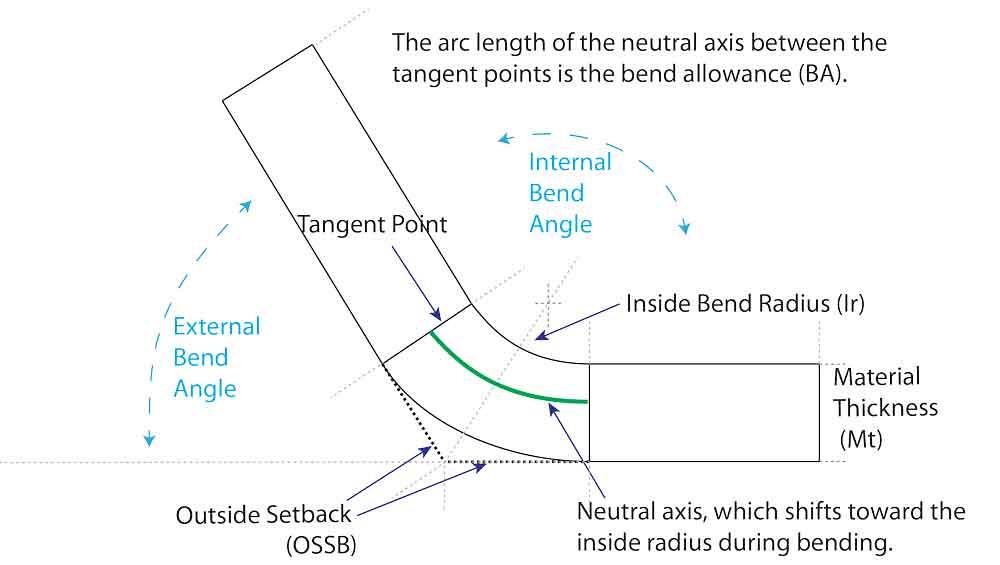
Figure 1
To perform basic bend calculations, we use the bend angle (A), inside bend radius (Ir), and outside setback (OSSB).
Insights on Bend Functions
Question: I’m an instructor at a sheet metal training facility and need to clear up 90-degree bend calculations for bottoming. We have been teaching two methods, and I would like to know which is correct. We use mild steel in both situations.
Under one method, bend allowances are determined by adding 20% of the material thickness per half-bend for the ID or subtracting 80% per half-bend for the OD.
The other method is based on material thicknesses. For an ID bend allowance, add half a material thickness for an OD calculation and subtract half a material thickness from the ID legs. (Editor’s note: In this instance, ID and OD stand for inside and outside dimensions of the finished part.)
Answer: Both are correct to a point; however, there are other ways. It all depends on the accuracy your parts require.
If your parts are always made from the same type and thickness of sheet or plate material and using the same punch and die set, you could bend a piece and measure the change and run with that number. And you could use either of the two formulas that you suggested if you have a significant enough tolerance, something like a tolerance of 0.032 in., for example.
You could also use one of many other formulas that are very accurate. I use them to calculate the outside setback (OSSB), bend allowance (BA), and bend deduction (BD). Without a long-winded explanation, they are:
Ir = Inside radius
(equals punch radius when bottoming and coining,
or a percentage of the die width when air bending)
Mt = Material thickness
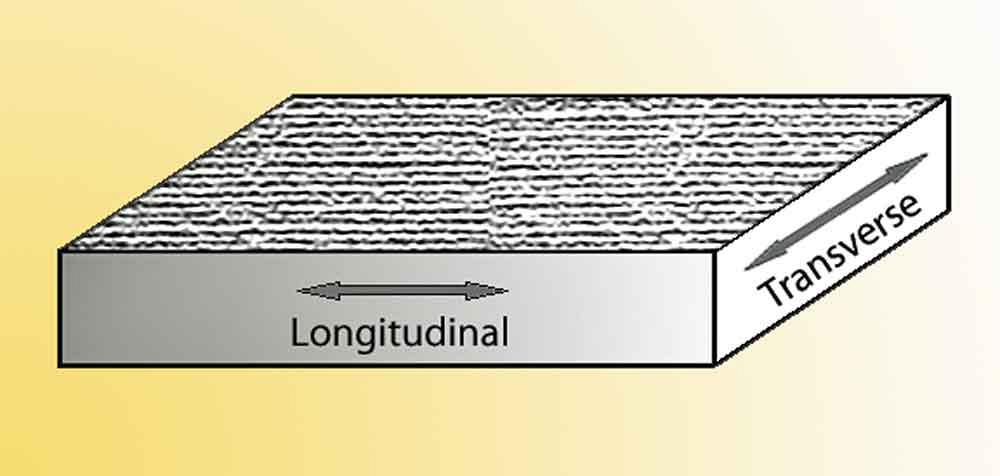
Figure 2
When you bend with, or longitudinal to, the grain, the bend line runs parallel with the grain direction. When you bend against, or transverse to, the grain direction, the bend line is perpendicular to the material grain direction.
A = Bend angle (BA requires external angle;
OSSB can use internal or external angle, depending
on how you calculate your flat blank)
BA = [(0.017453 × Ir) + (0.0078 × Mt)] × A
OSSB = tan (A/2) × (Ir + Mt)
BD = (OSSB × 2) – BA
Figure 1 shows you where these measurements appear on a bend. You can find many more details about the bend functions in the Bending Basics archive here. For more details on these bend functions, you can refer to the Grand unified theory of bending that ran from September through December 2015. You can also check out The basics of applying bend functions, which walks you through the basics of flat-blank calculations using these formulas.
Also, if you’re curious, the BA formula I use does incorporate a k-factor, it’s just hidden. The “0.0078” figure in the formula is pi divided by 180 multiplied by 0.446, an average k-factor that works for many applications. The k-factor is a ratio that describes the neutral axis’s shift during bending. For more on this, check out K-factors, Y-factors, and press brake bending precision.
Precision or Planer?
Question: I’m looking for press brake tooling to replace some worn-out tools, and I wonder if you could give your input regarding the advantages of precision tooling versus standard tooling. We air-bend stainless steel 304, 16 and 18 gauge, most of the time, and we perform U-shape forming. We produce about 2,000 parts a day and our tolerances are to within 0.032 in.
Answer: Quite often choosing tooling is more about what your product line consists of, or at least where you are planning to go with your company.
If you are consistently running the same parts with the same gauges and types of material, and if your parts are not too intricate, either precision-ground or planer tools will work fine. I would most likely go with the standard planer-style punch and dies, just because they’re less expensive.
Know that if you’re currently using planer tools and you wish to switch to precision-ground tools, you’ll need adapters to make the precision-ground tools operational.
On the other hand, if your parts are complicated and require you to stage your tooling, form internal and external flanges, and perhaps reverse the punch direction within a single setup, then precision-ground tooling would be the way to go. Yes, these tools are more expensive than the planer-style tools. Nonetheless, if your product line becomes diverse and complicated, and requires staging, precision-ground tools will pay for themselves in labor savings alone.
Stainless and the Grain
Question: I have 15 years of experience as a press brake operator. Today my boss had me test blanks of heat-treated stainless steel to check for fractures. What followed was a discussion as to which way is forming “against” the grain. I insist that against the grain is when the material grain is perpendicular to the backgauges, but he says that’s forming “with” the grain. We need you, the guru, to settle this once and for all. Which direction does the grain run if you are forming against the grain?
Answer: Forming against the grain means the bend line is perpendicular to the grain direction; it’s also called “transverse to the grain.” When you form “with” the grain, it’s parallel to the grain direction—also called “longitudinal to the grain” (see Figure 2). You can find more on this here.
When you form against the grain, you’re less likely to induce fractures in the part. When forming with the grain, the stresses on the outside of the bend can pull or separate the grains with far less effort. Also, forming an inside bend radius that’s too small will exacerbate the issue.
That said, I seriously doubt that you will see this effect on heat-treated stainless, though it’s possible. However, steel and aluminum will crack with relative ease. As a point of note, any material will bend with less effort when bending with the grain and require more force to bend against the grain. Bending across the grain also will create a stronger bend.
More Questions, More Answers
This is just a taste, and more tastes will be coming soon. All the questions here came from the U.S., but I receive many others from around the world, including Canada, Germany, India, and several countries in Africa. I’ll be addressing these in future months.
Shop environments might differ with the people they employ and the products they produce. But no matter where a skilled operator runs a press brake, the physics behind sheet metal bending is the same. So wherever you live and wherever you work, keep the questions coming!
About the Author
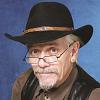
Steve Benson
2952 Doaks Ferry Road N.W.
Salem, OR 97301-4468
503-399-7514
subscribe now
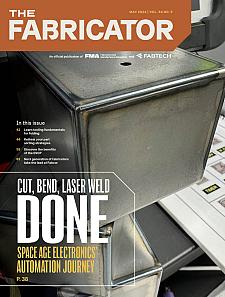
The Fabricator is North America's leading magazine for the metal forming and fabricating industry. The magazine delivers the news, technical articles, and case histories that enable fabricators to do their jobs more efficiently. The Fabricator has served the industry since 1970.
start your free subscription- Stay connected from anywhere
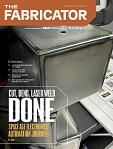
Easily access valuable industry resources now with full access to the digital edition of The Fabricator.
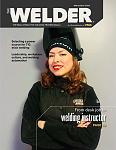
Easily access valuable industry resources now with full access to the digital edition of The Welder.
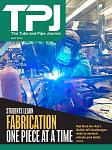
Easily access valuable industry resources now with full access to the digital edition of The Tube and Pipe Journal.
- Podcasting
- Podcast:
- The Fabricator Podcast
- Published:
- 04/16/2024
- Running Time:
- 63:29
In this episode of The Fabricator Podcast, Caleb Chamberlain, co-founder and CEO of OSH Cut, discusses his company’s...
- Trending Articles
Tips for creating sheet metal tubes with perforations
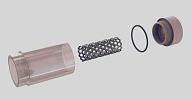
Supporting the metal fabricating industry through FMA
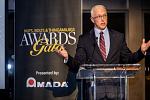
JM Steel triples capacity for solar energy projects at Pennsylvania facility
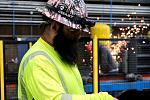
Fabricating favorite childhood memories
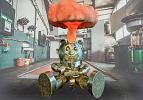
Omco Solar opens second Alabama manufacturing facility
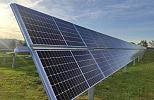
- Industry Events
16th Annual Safety Conference
- April 30 - May 1, 2024
- Elgin,
Pipe and Tube Conference
- May 21 - 22, 2024
- Omaha, NE
World-Class Roll Forming Workshop
- June 5 - 6, 2024
- Louisville, KY
Advanced Laser Application Workshop
- June 25 - 27, 2024
- Novi, MI