Contributing editor
- FMA
- The Fabricator
- FABTECH
- Canadian Metalworking
Categories
- Additive Manufacturing
- Aluminum Welding
- Arc Welding
- Assembly and Joining
- Automation and Robotics
- Bending and Forming
- Consumables
- Cutting and Weld Prep
- Electric Vehicles
- En Español
- Finishing
- Hydroforming
- Laser Cutting
- Laser Welding
- Machining
- Manufacturing Software
- Materials Handling
- Metals/Materials
- Oxyfuel Cutting
- Plasma Cutting
- Power Tools
- Punching and Other Holemaking
- Roll Forming
- Safety
- Sawing
- Shearing
- Shop Management
- Testing and Measuring
- Tube and Pipe Fabrication
- Tube and Pipe Production
- Waterjet Cutting
Industry Directory
Webcasts
Podcasts
FAB 40
Advertise
Subscribe
Account Login
Search
Automated heavy plate machinery boosts pace, accuracy for steel fabricator
Minneapolis metal fabricator builds confidence to take on stadiums, auditoriums, bridges
- By Kate Bachman
- March 9, 2020
- Article
- Cutting and Weld Prep
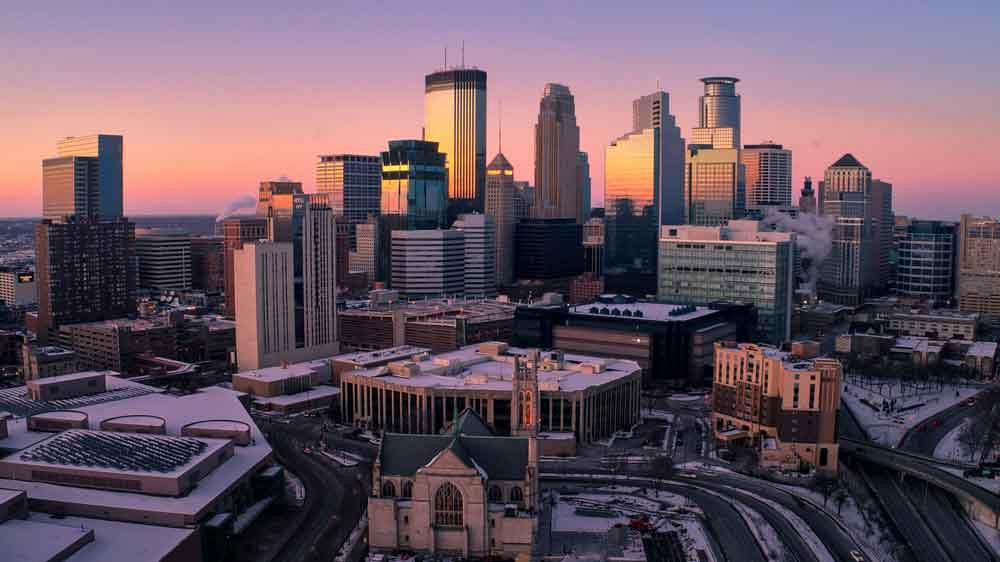
LeJeune Steel Co. has fabricated so many structural steel assemblies in Minneapolis, you could almost say the company built the Minneapolis skyline. Getty Images.
If you want to build royal fabrications for towering stadiums, deep underground caverns of epic proportions, and bridges across the widest river in the world, you had better be well-equipped.
Structural steel fabricator LeJeune Steel Co. vies for—and frequently wins—bids for the largest and most complex structural jobs around the country. “We like to specialize in large and complicated projects,” said Vice President of Operations Josh Barten.
The company’s website showcases the sports and entertainment, medical, and university building projects it has fabricated, including the U.S. Bank Stadium, a massive underground auditorium project for a large software company in Wisconsin, the Washington Avenue Bridge across the mighty Mississippi River—and nearly the entire Minneapolis skyline.
Getting those monumental, showcase projects depends upon having the ability to meet speed, accuracy, and repeatability requirements.
Automated to Keep Pace With Volume Demands
In 2008 LeJeune Steel management decided that if it were going to keep pace with the volume and throughput demands of the clients it had—and wanted to have in the future—it really needed to automate its fabrication equipment and processes.
“The type of work that we felt like we excelled at, which is the larger, more complex work, became more complicated because of advances on the design side. New 3D design software like Tekla and SDS/2 have given architects and engineers the ability to design more complex buildings with more complex connections. Our ability to fabricate and keep pace with these new designs was really limited when doing it by hand, using manual layout, mag drills, and trying to flame-cut copes and bevels with just a hand torch,” Barten said.
“We recognized that if we wanted to continue to excel with this increasingly complex kind of work, we needed automation and CNC equipment that could take these really detailed 3D files and put them into a program that the machines could run automatically,” Barten said.
The structural steel company purchased several Peddinghaus automated processing machines, including the Advantage-2 drill line, the BDL/B drill line, the DG-1250 band saw, and the PeddiWriter layout marking line. “Generally speaking, the equipment is accurate within 1/32 inch,” Barten said.
“We processed a significant amount of the plate for the Washington Avenue Bridge, for the massive underground auditorium, and for the U.S. Bank Stadium. We also have a Peddinghaus ABCM-1250/3D that we use for making bevel cuts on the ends of beams and for weld prep, cutting copes, and beams for weld penetration.”
Since automating, the manufacturer fabricates more than 30,000 tons of steel a year. Barten said that automation significantly increased the pace at which the company could process steel. In addition, it was able to do so without increasing labor costs. “Even though the buildings that we fabricate have continued to increase in complexity, our annual production volume has also continued to go up without really any appreciable additional labor hours—in fact, that has actually decreased. So, I think that was one key benefit,” Barten said.
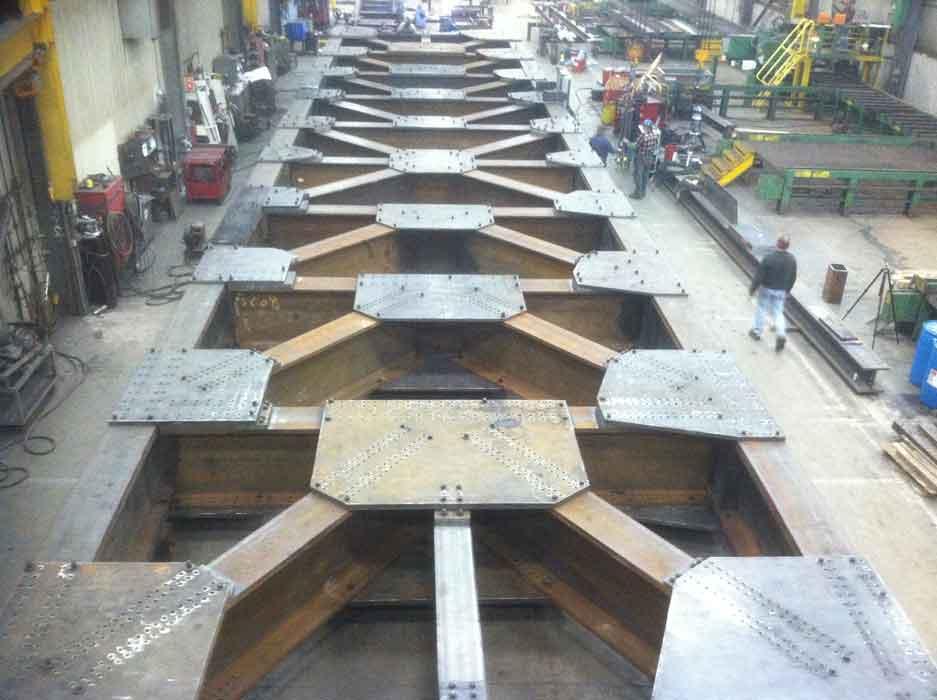
The king truss for a massive auditorium was fabricated and assembled on the floor of LeJeune’s fabrication plant. Photos courtesy of LeJeune Steel Co.
Washington Avenue Bridge: Transition Project
The first project LeJeune Steel used the new CNC equipment for was a retrofit of the Washington Avenue Bridge in Minneapolis. The bridge, located on the University of Minnesota’s main campus, connects the east and west banks of the Mississippi River.
The retrofit bridge project needed an estimated 450,000 drilled holes in plate and box girders. The box girders were fabricated in LeJeune’s Minneapolis facility and then trucked to the company’s affiliate fabricator Wisconsin Structural Steel facility to run through the Peddinghaus BDL/B drill line.
“Of the literally hundreds of thousands of holes on that job, fewer than 10 holes had to be reamed to fit up in the field because of the accuracy of the CNC equipment,” Barten said.
“The customer was ecstatic. That project really set the tone for the future pursuit of projects and the confidence level we could have in the automated equipment. It was a milestone for LeJeune,” Barten said.
Underground Arena: Profoundly Accurate
LeJeune Steel/Wisconsin Structural Steel was selected to supply steel roof trusses for a health care software giant’s auditorium. The underground arena is an intriguing building in many ways, and especially challenging in terms of its size and complexity, Barten said.
The five-story, 1.2-million-square-foot auditorium was built in a 74-ft.-deep underground excavation. The 25-ft.-deep, 270-ft.-long span roof trusses that go over the seating area all tie into one large king truss over the stage. The long-span roof was one of the project’s most challenging components.
The entire 4,200-ton roof structure—king truss with all the long-span trusses intact—was assembled on the ground and then strand-jacked into position. Then the columns were positioned underneath the roof and the roof lowered onto them.
“It was a very complex, very fast-track project,” Barten said.
The truss plates were more than 41/2 in. thick. Sometimes the steel was four or five different plies of steel, making it 12 to 14 in. thick.
The project required extreme accuracy for the splice plates and chord splice bolt hole locations. “We had to have the holes line up. We could not afford a missed drill hole.”
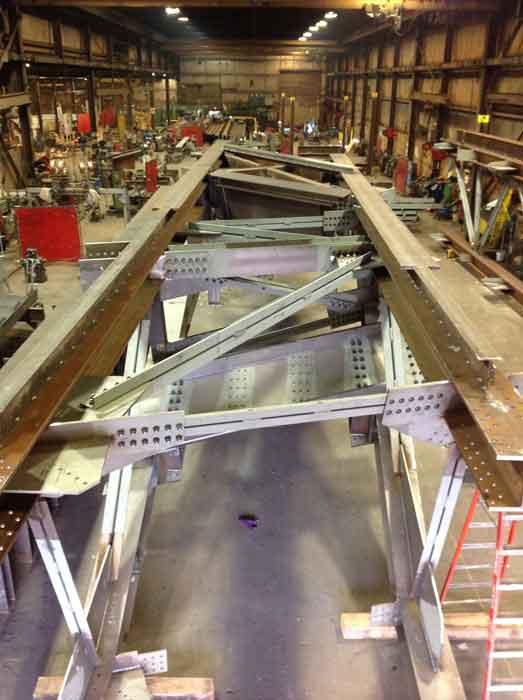
A section of the queen post truss for an underground auditorium of epic proportions was fabricated and built in LeJeune’s plant.
Barten said that the CNC machinery provided the cut and hole accuracy needed for off-the-truck fit-up. “It used to be that we’d have to put a lot of work into making sure that even relatively simple connections would be able to bolt together in the field straight off the truck. The automation has allowed the more complex work to fit up on the first try.
“You just don’t get that kind of accuracy unless you’ve got really good equipment,” Barten said. “We relied heavily on the Peddinghaus CNC automated equipment.”
U.S. Bank Stadium: Midair Connections
The success of those projects bolstered the company’s confidence to take on another unique, even more massive job. Barten points to the company’s fabrication of the trusses for the U.S. Bank Stadium as an example of the expediency and accuracy it was able to achieve with the automated machinery. The fabrications for the 66,655-seat stadium were challenging and the automation equipment was critical, Barten said.
The expectation for expediency was one major challenge of the stadium build. “They demolished the Metrodome at the end of one football season and they wanted to have it up and running a year and a half later for kickoff on opening day 2016. To be able to fabricate steel at that pace, we had to be fast,” Barten said, adding, “We couldn’t have done it without the automated equipment.”
A second challenge was that the stadium roof design was very complex. Each truss section that went into the main assembly had up to 50 individual section cuts to assist assembly. The stadium roof trusses weigh 6,000 tons.
“The most significant, impressive steel fabricated members on that job were the queen post trusses.” These are the trusses that run from the center ridge truss, which runs the length of the building, down to the perimeter. “Those nine trusses are four chord trusses—-two top and two bottom—and then they’re laced together with infill. In addition, there’s a large tension truss that runs under those queen post trusses.”
The trusses were built in sections in the shop and painted. “Because of their size, we could really assemble only one 40-ft. section in our shop at a time.” Then they were taken to the job site to be assembled on the ground and lifted into position or, in some cases, assembled midair. On-site and in-air assembly meant that hole location and size accuracy was critical.
The bolted connections on the ends of the chords, the splice plates, had to be put together very precisely. The overall geometry of each truss had to be exact so that everything fit together. “We used a Peddinghaus BDL/B drill line and the DG-1270 band saw to process each of the chords. Then we used a couple of different plate processing systems to cut the splice plates and all the infill and connection plates.”
The whole process worked really well, Barten relayed. “They fit up with really no issues at all. The complexity of the geometry of the queen post trusses and all the connections could not have been done without the CNC equipment. I think we would have really struggled to be able to drill all those holes and fabricate them manually and not have setup problems in the field.”
The U.S. Bank Stadium was on full display at the 2018 Super Bowl.
About the Author
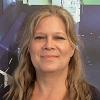
Kate Bachman
815-381-1302
Kate Bachman is a contributing editor for The FABRICATOR editor. Bachman has more than 20 years of experience as a writer and editor in the manufacturing and other industries.
Related Companies
subscribe now
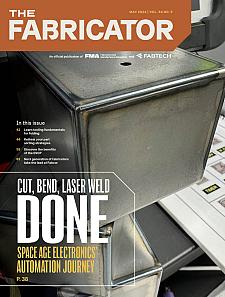
The Fabricator is North America's leading magazine for the metal forming and fabricating industry. The magazine delivers the news, technical articles, and case histories that enable fabricators to do their jobs more efficiently. The Fabricator has served the industry since 1970.
start your free subscription- Stay connected from anywhere
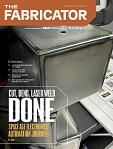
Easily access valuable industry resources now with full access to the digital edition of The Fabricator.
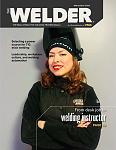
Easily access valuable industry resources now with full access to the digital edition of The Welder.
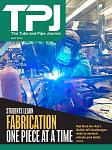
Easily access valuable industry resources now with full access to the digital edition of The Tube and Pipe Journal.
- Podcasting
- Podcast:
- The Fabricator Podcast
- Published:
- 04/16/2024
- Running Time:
- 63:29
In this episode of The Fabricator Podcast, Caleb Chamberlain, co-founder and CEO of OSH Cut, discusses his company’s...
- Industry Events
16th Annual Safety Conference
- April 30 - May 1, 2024
- Elgin,
Pipe and Tube Conference
- May 21 - 22, 2024
- Omaha, NE
World-Class Roll Forming Workshop
- June 5 - 6, 2024
- Louisville, KY
Advanced Laser Application Workshop
- June 25 - 27, 2024
- Novi, MI