Contributing editor
- FMA
- The Fabricator
- FABTECH
- Canadian Metalworking
Categories
- Additive Manufacturing
- Aluminum Welding
- Arc Welding
- Assembly and Joining
- Automation and Robotics
- Bending and Forming
- Consumables
- Cutting and Weld Prep
- Electric Vehicles
- En Español
- Finishing
- Hydroforming
- Laser Cutting
- Laser Welding
- Machining
- Manufacturing Software
- Materials Handling
- Metals/Materials
- Oxyfuel Cutting
- Plasma Cutting
- Power Tools
- Punching and Other Holemaking
- Roll Forming
- Safety
- Sawing
- Shearing
- Shop Management
- Testing and Measuring
- Tube and Pipe Fabrication
- Tube and Pipe Production
- Waterjet Cutting
Industry Directory
Webcasts
Podcasts
FAB 40
Advertise
Subscribe
Account Login
Search
3 angles on press brake training: Part II
Guru comes to you
- By Kate Bachman and Rob Colman
- May 6, 2018
- Article
- Machining
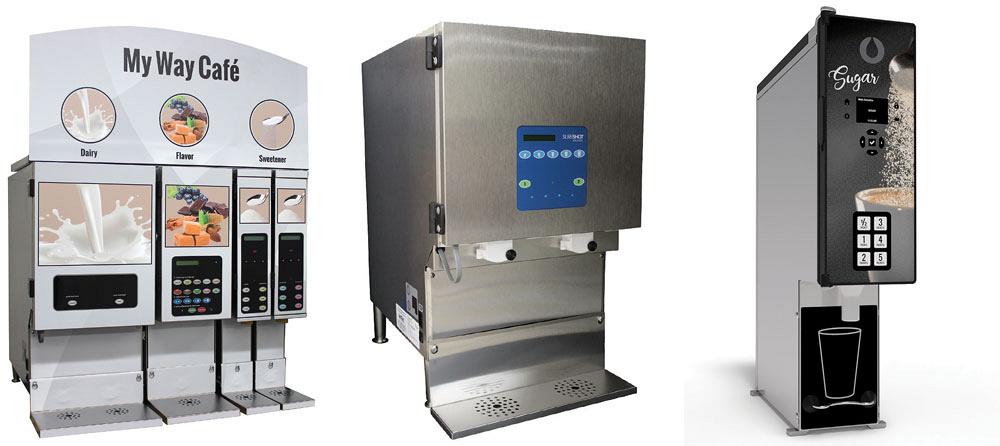
SureShot Solutions fabricates every component of its equipment, which is used in the beverage industry to dispense dairy, sweeteners, and flavors so that consumers can have their coffee or tea “their way.” Most of the 22- to 12-gauge stainless steel panels, doors, bodies, skins, backs, internal frames, and bases are bent on a press brake.
Editor’s Note: This article is the second of three in a series about different approaches to press brake training. Part I, which was published in the April issue, highlights training in a classroom environment; Part II explores training on-site; Part III, which will be published in the July issue, explores training by a machine OEM, as well as part design.
SureShot Solutions of Lower Sackville, N.S., Canada, manufactures portion-controlled dispensers for the beverage industry. Its dairy, sweetener, and flavor dispensers are staples in coffee bars and quick-serve restaurants (see lead image). Does starting your day depend on a double cappuccino with a hint of hazelnut? SureShot’s equipment just may be what apportions and dollops the defining flavor, mellowing dairy, and sweetener into your cuppa joe.
The company’s bend-over-backward approach to providing the precise blend a consumer craves extends to the way it manufactures equipment for its customers. In some cases, it customizes its dispensers, making them upon being ordered. A production run might be for 80 refrigerated dairy dispensers.
Most of the bending done in manufacturing its dispensers is performed on a press brake. The company’s business model results in a high-mix, low-volume lot size, which requires frequent changeovers and broad flexibility. Therefore, the operators performing the bending need a certain skill level.
Additional Education, Training Needed
The company underwent a transition a couple of years ago that resulted in a void of skilled press brake operators in the plant. Kelby Ernst, who came on as the new lead fabricator recently, perceived that the greenery of the staff needed education on press brake fundamentals.
“The shop was falling behind on orders,” Ernst said. SureShot manufactures as many as 15,000 parts per week. Many new employees had neither the knowledge nor the skill required to keep pace. Ernst reintroduced a formal training format, he said.
“Because not everybody comes in as a trained fabricator, we train everybody in-house. I saw that there was a lack of knowledge about why we choose certain tools, what bend allowances mean and how you calculate them—and why you calculate them that way,” Ernst said. “They would go through the motions and do their jobs adequately, but they didn’t really understand why they were doing what they were doing.”
Ernst said he believed that for them to progress so that they could take on new jobs proficiently, it was important for them to undergo more training outside of the company. “It makes for a better operator when he understands his job better—how to do it properly and why.”
Ernst had attended the Fabricators & Manufacturers Association’s (FMA’s) Precision Press Brake Certificate Course a few years ago and wanted to enroll his staff in it as well. “I saw the need for them to learn what I learned.” Rather than send eight operators from Nova Scotia to Elgin, Ill., he opted to have the full training course come to them—right at the plant.Guru in Your Shop
Having FMA’s press brake guru and course instructor Steve Benson go to the SureShot plant in Nova Scotia was a good fit for the company for several reasons.
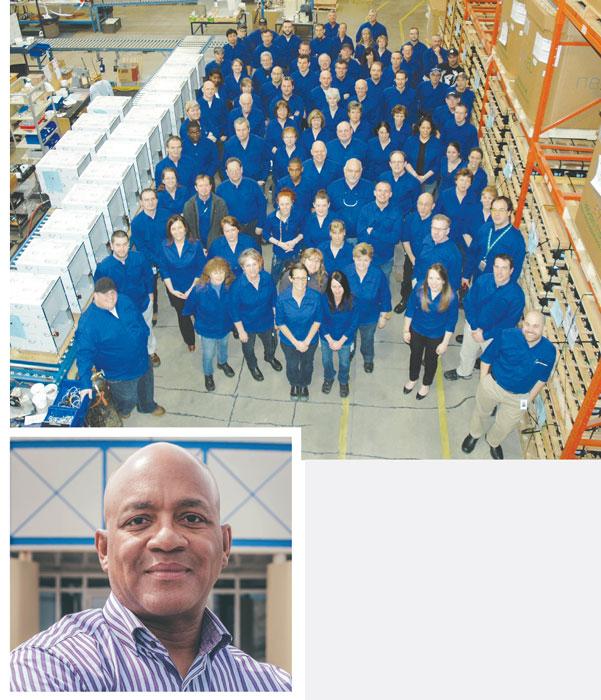
SureShot Solutions CEO and company founder Michael R. Duck developed the first portion-control dispenser in 1985 and has grown the company, in part, by offering highly customized equipment. That translates to high-mix, low-volume production, and that translates to the need for well-trained press brake operators with a broad skill set who can perform quick changeovers and adapt to making many product variations
First, the arrangement worked well logistically. It was less expensive to hold the training there than to fly and lodge eight people for the two-day course. Crossing national borders was an issue too. “Not everyone has a passport, so it was much easier to do it this way,” Ernst said.
Second, his staff could learn and test directly on their own tooling and machines.
Third, Benson was able to customize the course to SureShot’s requirements, based on what Ernst assessed his trainees needed to learn, and to extend the course to a full week (see Figure 1).
Having his fabricators attain a mastery of bend allowances was at the top of Ernst’s list. “Our parts have tight tolerances. It’s very important that they be able to bend and fabricate the parts to the drawing and get them to the engineers’ specifications,” Ernst said. “If they understand how to get there with the right tooling, can measure those parts, and understand how to make the proper adjustments, they’ll be able to make changes without assistance.”
Having them know how to choose the right tooling was next in importance. “It’s pretty critical for us, because when our engineers design parts, they base it off of the tooling we have,” Ernst said. “The fabricators have to understand that the air bending tool is not going to work the same as the bottom bending tool or they’re not going to get the proper bend. By knowing the tooling, they can choose the correct tool for bottom bending or coining or air bending they need for the job.”
Ernst said that the education needed to be even broader. “They needed to understand how and why things happen with metal. Really, anything else they could take from the training would be very, very helpful. As I said, they are not experienced fabricators, so we needed for them to get to that next level to be closer to what a trained fabricator can do.”
Learnings
The weeklong class began with metallurgy. “It started right from the ground up with a discussion of materials and what tensile strength is,” Ernst said.
The course covered terminology, springback and springback compensation, and bend angles. It included interactive instruction. Benson distributed samples and had the class work through example work problems.
Benson was able to adapt the curriculum as he got to know the students and assessed their knowledge base.
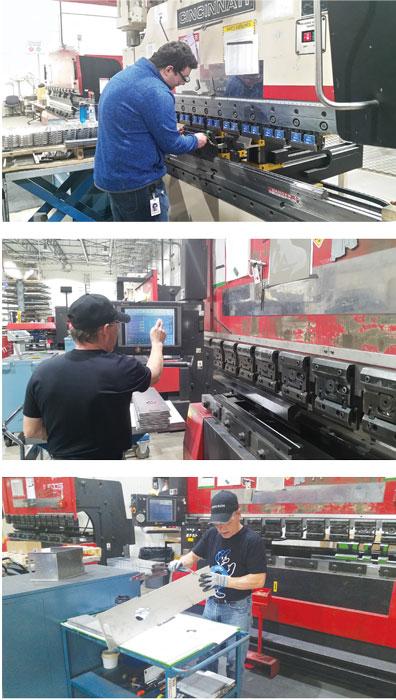
Figure 1
SureShot Solutions’ press brake operators must be well-trained to make the necessary adjustments and take the measurements needed to create parts that meet the manufacturer’s tolerance standards. On-site training administered by FMA’s press brake instructor and guru Steve Benson helped eight fabricators understand the hows and whys of press brake bending.
“Then on the final day, we came down to the shop to measure bends on our own machines. They saw how if you change one setting, that will affect something else,” Ernst said.
Ready to Form
Ernst said that the program was a success. “I’ve seen a difference in the confidence in the newer guys, and the older guys said, ‘Oh, now I understand.’”
The group, as a whole, even some junior trainees, had a good success rate passing the exam.
The session took a deep curve into theory and math fundamentals and principles of quality sheet metal bending that some newer trainees did not fully absorb the first go-around. “So maybe we need to revisit that later. They remarked that it was tough and a bit long, but at the end of the day they understood better what their job was and what they needed to do. They all thought that it was definitely beneficial.”
Ernst said that the certificate aspect provides peace of mind in that he could be assured that they grasped a certain knowledge set. “When I go down to the shop floor and talk to the operators, we’re talking the same lingo. When I talk about bend allowances or air bending versus bottom bending, they understand what I’m talking about. If they’re having issues, I’m able to help.”
He said that most of the group is proficient enough to work fairly independently. “We get a lot of prototyping work in the shop. Our engineers will bring down a prototype part and ask, ‘You can make that part for me, can’t you?’ And they can take that part and build it without too many problems.”
The final proof was in the latte. SureShot’s good part rate increased from 90 percent to 97 percent in the 10-week period following the class.
SureShot Solutions, www.sureshotsolutions.com
About the Authors
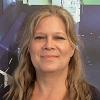
Kate Bachman
815-381-1302
Kate Bachman is a contributing editor for The FABRICATOR editor. Bachman has more than 20 years of experience as a writer and editor in the manufacturing and other industries.
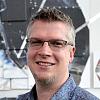
Rob Colman
Contributing Writer
subscribe now
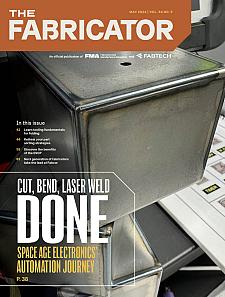
The Fabricator is North America's leading magazine for the metal forming and fabricating industry. The magazine delivers the news, technical articles, and case histories that enable fabricators to do their jobs more efficiently. The Fabricator has served the industry since 1970.
start your free subscription- Stay connected from anywhere
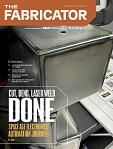
Easily access valuable industry resources now with full access to the digital edition of The Fabricator.
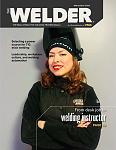
Easily access valuable industry resources now with full access to the digital edition of The Welder.
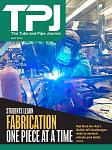
Easily access valuable industry resources now with full access to the digital edition of The Tube and Pipe Journal.
- Podcasting
- Podcast:
- The Fabricator Podcast
- Published:
- 04/16/2024
- Running Time:
- 63:29
In this episode of The Fabricator Podcast, Caleb Chamberlain, co-founder and CEO of OSH Cut, discusses his company’s...
- Trending Articles
Tips for creating sheet metal tubes with perforations
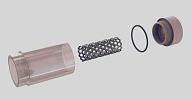
Are two heads better than one in fiber laser cutting?
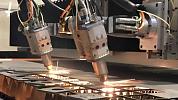
Supporting the metal fabricating industry through FMA
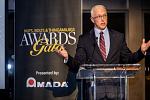
JM Steel triples capacity for solar energy projects at Pennsylvania facility
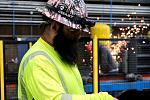
Omco Solar opens second Alabama manufacturing facility
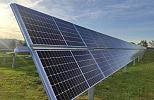
- Industry Events
16th Annual Safety Conference
- April 30 - May 1, 2024
- Elgin,
Pipe and Tube Conference
- May 21 - 22, 2024
- Omaha, NE
World-Class Roll Forming Workshop
- June 5 - 6, 2024
- Louisville, KY
Advanced Laser Application Workshop
- June 25 - 27, 2024
- Novi, MI