Contributing editor
- FMA
- The Fabricator
- FABTECH
- Canadian Metalworking
Categories
- Additive Manufacturing
- Aluminum Welding
- Arc Welding
- Assembly and Joining
- Automation and Robotics
- Bending and Forming
- Consumables
- Cutting and Weld Prep
- Electric Vehicles
- En Español
- Finishing
- Hydroforming
- Laser Cutting
- Laser Welding
- Machining
- Manufacturing Software
- Materials Handling
- Metals/Materials
- Oxyfuel Cutting
- Plasma Cutting
- Power Tools
- Punching and Other Holemaking
- Roll Forming
- Safety
- Sawing
- Shearing
- Shop Management
- Testing and Measuring
- Tube and Pipe Fabrication
- Tube and Pipe Production
- Waterjet Cutting
Industry Directory
Webcasts
Podcasts
FAB 40
Advertise
Subscribe
Account Login
Search
Engineering and fabricating a one-of-a-kind bridge to span the Mississippi River
An uncommon, converging twin true-arch bridge creates fabrication complexities
- By Kate Bachman
- August 10, 2023
- Article
- Plasma Cutting
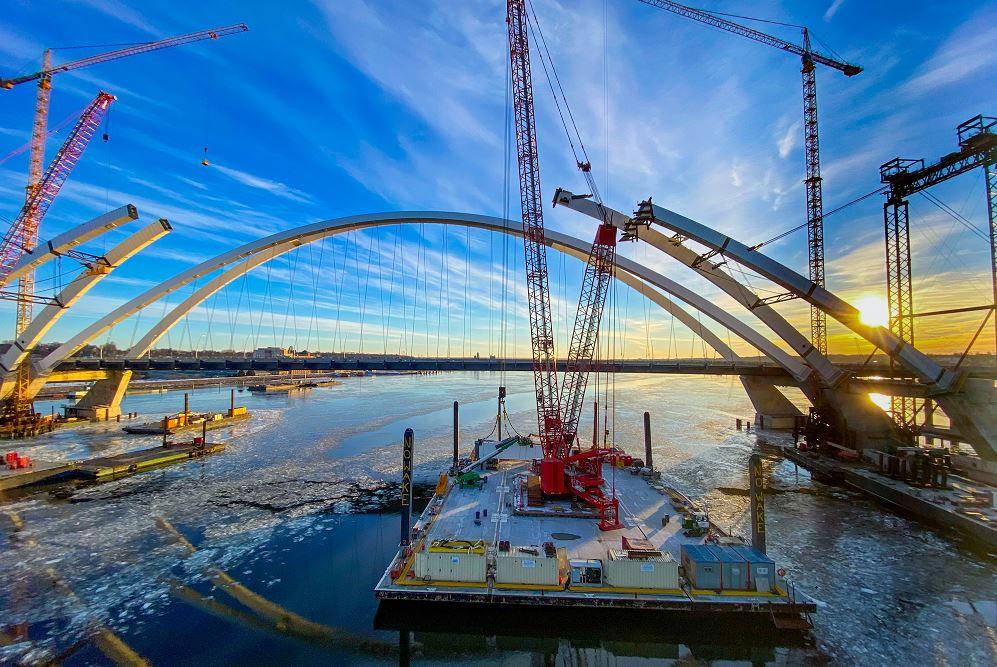
Industrial Steel Construction, Gary, Ind., fabricated the components and assemblies for a new arched bridge spanning the Mississippi River between Iowa and Illinois. It is a twin converging, true-arch, basket-handle bridge that is 98 ft. wide, 3,405 ft. long, and includes an 800-ft. arch span. Iowa DOT
The I-74 Iowa-Illinois Memorial Bridge that spanned the Mississippi River connecting Illinois and Iowa was functionally obsolete and over capacity, causing snarled traffic and a frequent need for repairs. A new bridge was badly needed.
But the replacement was not to be a duplicate, nor an ordinary bridge. Not only was the new bridge engineered to carry an increased load, be more than twice as wide as the existing bridge, and accommodate pedestrian walkways, it was designed to be a unique landmark bridge and spectacularly beautiful.
It is a true-arch, basket-handle bridge—one of the most complex bridge projects in the country. It is 98 ft. wide and 3,405 ft. long, including an 800-ft. arch span. The project required multiple steel girders and new approaches, and it had to be built on a new horizontal alignment.
The complex design proved to be complicated to fabricate. Every piece of the arch had unique dimensions.
Industrial Steel Construction’s Facility Factors In
Industrial Steel Construction (ISC), Gary, Ind., was awarded the steel fabrication of the components and assemblies for the new bridge, including the approaches. The facility is centrally located in the Great Lakes region, with direct access to intermodal transportation, rail, and Lake Michigan and the Illinois River system.
ISC’s facility is 1.6 million sq. ft. on 160 acres. Originally, the building was one of eight plants of American Bridge Fabricators, a division of U.S. Steel, founded in 1909 by J.P. Morgan and Elbert Gary.
ISC’s expansive building was advantageous because the company could fabricate and assemble the bridge under roof. The company has done assemblies as long as 950 ft. and has fabricated and assembled entire bridges under roof.
Precision With Under-Roof Control
ISC’s Executive Director Ankit Shah and Project Manager David Johnson explained why the under-roof fabrication was an advantage for this project.
The bridge’s design required a high degree of precision that is unusual for a project of its scale. “Whenever you want precision, you want the environment to be very controlled,” Shah said.
“We were able to assemble the floor system inside our 1.6 million-sq.-ft. shop from end to end, one half at a time,” Johnson said. Shop assembly that can be accomplished indoors is an advantage because overhead cranes can be used and thermal expansion and contraction that occurs when the steel members are exposed to sun, heat, rain, and snow are controlled.
ISC’s facility is 1.6 million sq. ft. on 160 acres, allowing for the entire bridge to be fabricated and assembled under roof. Industrial Steel Construction Inc.
The large indoor fabrication facility offered several benefits to the employees as well, because it protected them from the environment. The fabricator could use its more than 100 overhead cranes, with a 125-ton capacity, to move the massive, heavy arch members around. “Handling steel members of that size and weight would've been very difficult outdoors without those overhead cranes,” Shah said.
“Usually, plate girders are roughly 30,000 to 40,000 lbs. each. But when you talk about moving a 100-ton section through the fabrication process, only a few bridge fabricators nationally can manage that,” he added.
“We fabricated the structural steel for the whole bridge here, in Gary, which includes the approaches [plate girders] as well as the main span [true-arch, basket-handle bridge]. We were better able to meet the specification tolerances in the controlled fabrication environment of the plant under roof than we could have done outdoors,” Shah said.
A Tricky Bridge
Shah and Johnson described how the bridge’s unique design complicated fabrication.
“The approaches were plate girders that involved typical girder fabrication procedures,” Johnson said. “But the arch is a complex signature structure. It was uniquely designed; developing fabrication procedures involved a lot of planning.”
Not only is the bridge a true arch, it is a basket-handle type of arch—one of only two in the country, according to Shah. “The basket-handle true arch makes it more unique because you have complex geometry and more stringent tolerances in the fabrication process.”
The complexity stems from the fact that the two arches begin apart at the base and then converge at the keystone. Usually, arch bridges are aligned straight, with the keystone positioned in the center, so the geometry is not as complex as the I-74 bridge, Shah said. In addition, the arches taper—they are wider at the base and narrower at the top.
Each arch was constructed with 30 arched rib boxes. There were four typically shaped pieces at each level of the arches, each working its way up to the middle. However, each of them was unique in terms of length, size, and weight, Johnson said.
Fabrication Challenges
While many of the fabrication challenges were related to the complexity and size of the arch members, others were related to schedules and the need for high throughput. Each approach is constructed with more than 200 plate girders.
The company used Total Station surveyor equipment in the shop to make sure that all the geometry was aligned and matched the shop drawings and project specifications.
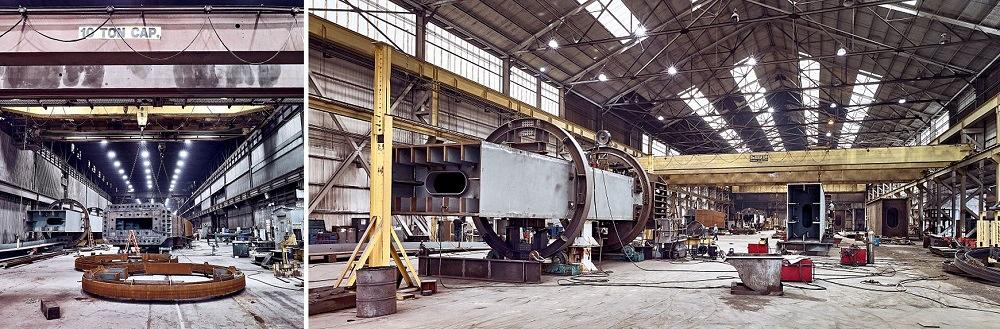
The fabricator devised a rolling ring concept to rotate the boxes to access all sides for welding. Industrial Steel Construction Inc.
Planning meetings were a weekly, sometimes daily event. “Each one of the arch members was handled like its own job,” Johnson said. “We had to fabricate them in sequence so that they were fabricated, assembled, and shipped when they were needed.”
“Dave played a very critical role in making sure that everyone was communicated with. We had thousands of meetings,” Shah said.
“We had to meet often because of the complexity; communication to the shop employees was important. It was imperative to make everybody aware of the contract requirements, including the project specifications,” Johnson said.
Plate Cutting, Drilling. The fabricators cut plate on Farley CNC oxyfuel and plasma cutting machines. Most drilling was executed on Farley CNC drilling machines.
To assemble the odd and varying shapes of the arch members, many splice plates were used as templates. The pieces were spliced together with several big splice plates, and those splice plates were cut and drilled to size. When the piece was assembled and put in the precise position, those plates were attached and then used as a template to drill through blank members manually to ensure a perfect match.
Rotating for Welding. It’s one thing to rotate a part that is light in weight, but it’s quite another to rotate a 240,000-lb. structural member. “After you weld it from one side, you have to rotate it to weld it on the next side. So we had to come up with some unique engineering designs to handle and move the pieces,” Johnson said.
The company devised a handling ring concept to rotate the boxes to access all the sides for welding. The rolling ring was not part of the bridge; it was just a positioner of sorts. “That was a big breakthrough in the project. We didn't have to keep on lifting and handling these large and heavy pieces, then putting them on their sides, handling them, and moving them again,” Shah said.
“Joe Hish, the owner of the company, came up with that idea. We could basically move the 125-ton pieces when we needed to safely,” Shah added.
Most of the submerged arc welding for the fillet and butt joints was performed with semiautomatic submerged arc equipment.
The heaviest boxes at the bases were 70-grade steel; others were 50-grade. A few of the sections were fabricated with fracture-critical material. “So, there was a mixture of material,” Shah said.
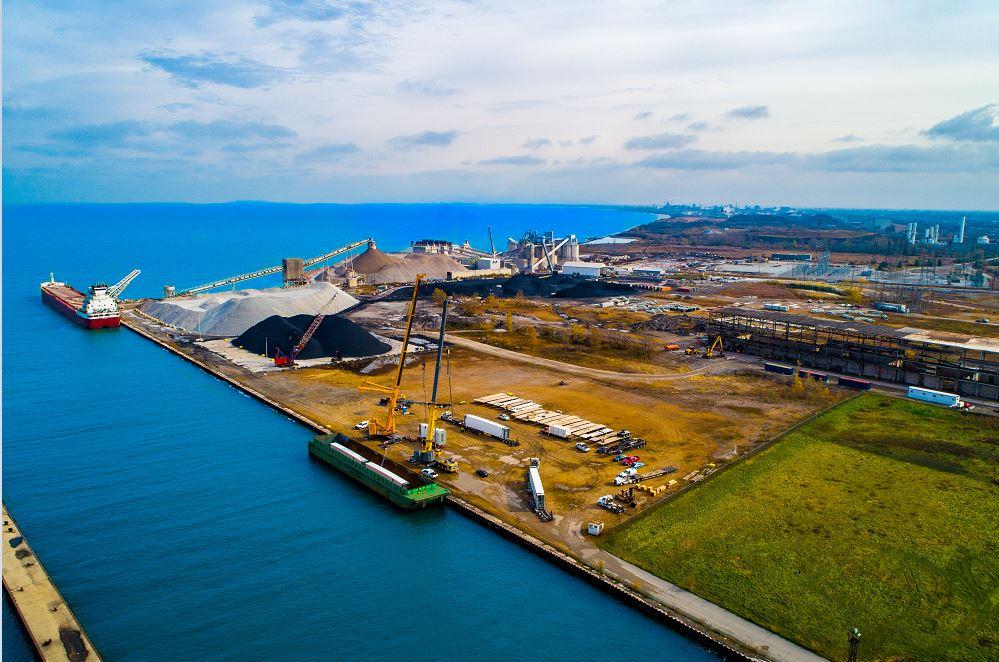
The arch component pieces and the fully assembled boxes were so large, they were shipped via barge from Gary down the Illinois River, then up the Mississippi River to Davenport, Iowa. The advantage of shipping by barge was that it was so large that they could load six sections at once. The disadvantage to the barge transport was that it required expedited production to meet river closing schedules and took months to complete. Industrial Steel Construction Inc.
Managing Distortion. The project called for extensive welding. A lot of longitudinal stiffeners that were attached on one side of the boxes’ flanges and webs caused distortion because of their heat input. “We learned from that and got better at controlling the distortion as we got further along. And we used heat straightening when needed,” Johnson said.
Meeting Throughput Demands. Throughput was critical, Johnson stated. “Moving pieces from one step to the other—that was a key challenge because it's such a large project. We fabricated 4,300 tons of steel for each of the main span arch bridge, plus the 8,000-ton approaches.”
Shah added, “Manufacturing, processes, in general, have to be streamlined. Here, they are project specific. At the end of the day, we're not building the same car repeatedly. Each project is different, so it has to be customized. The planning of the steps and sequence to build each of those—whether it's the butt splicing, the cutting of the plates, drilling of the pieces, welding of them together, and then moving them all the way through blast and paint—has to be optimized to make sure that we meet the project schedule. So, streamlining those processes was very critical for us.”
Making Space. Even in a 1.6 million-sq.-ft. plant, space can be constricted. Another challenge of the project was that because the pieces were large, heavy, and bulky, the facility was tied up for a couple of years. “You cannot move multiple projects into the plant at the same time. You have to clear the space out, or at least move the pieces forward before you can bring in the next project,” Johnson said.
“Ironically, we did have another project at the same time—the Wellsburg arch bridge, a tied-arch type bridge located in Brilliant, Ohio. The biggest challenge was we had the I-74 being fabricated on one side and the Wellsburg arch going on at the other side. We had a balancing act in terms of which one moved next,” Shah said.
“Dave and I were going back and forth, trying to move the projects. The work at the I-74 Mississippi bridge was a much more complex project than the Wellsburg, but we were both struggling to find shop space at that time.”
There was one advantage to having two arched bridges within the I-74 bridge project, Shah explained. “We had a lot of learning experiences on the westbound bridge that we were able to apply to the eastbound bridge. The Mississippi bridge project ran smoother in terms of planning our sequence on the eastbound arch.”
Skilled Labor, Ingenuity Bridge Productivity Gap
Shah credits the skilled workers on staff for their ingenuity in meeting schedules and managing difficult fabrication tasks. “We are a strong team of 250 fabricating professionals here, and our workforce is just phenomenal. They have out-of-the-box thinking; they're creative and come up with solutions for complex projects. Design is one thing; fabrication is a completely different animal,” Shah said.
“Each piece varied in weight and geometry. The heaviest section was close to 120 tons. There were several things that ISC fabricating professionals did just to make sure that we could fabricate this complex bridge with safety first in mind.”
Extensive Shipping, Logistics Planning
Because the new steel arch bridge is located at a main navigational channel and the fabrications were shipped by barge, it was critical to have extensive coordination, planning, and high throughput to meet schedules.
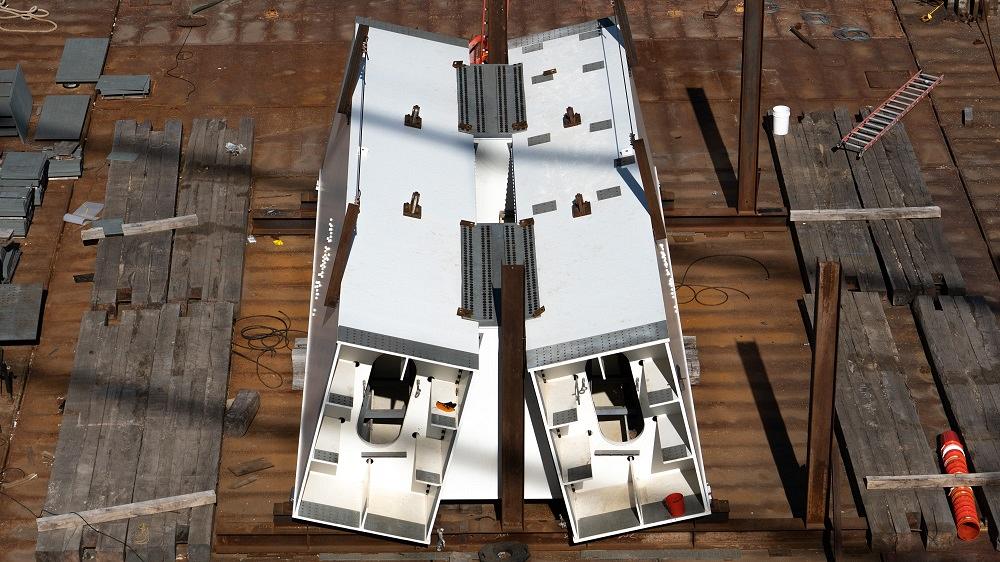
The basket-handle arch bridge makes it more complex to fabricate. The two arches begin apart at the base and then converge at the keystone. Shown is the keystone member. Iowa DOT
“It's the scale, it's the complexity, and even the distance to the site to a certain extent. If they were going to downtown Chicago, it would be a different story. Moving the members all the way to the Iowa side of the bridge created transportation challenges,” Shah said.
“We had to look at the project piece by piece to come up with a procedure on how we were going to assemble it. Of course, the erectors wanted all four corners first to build up around the horn,” Johnson added. Electrical installations and inspections had to be done before the members were loaded on the barge.
The arch component pieces and the fully assembled boxes were so large, they were shipped via barge from Gary down the Illinois River, then up the Mississippi River to Davenport, Iowa.
The advantage of shipping by barge was that it was so large that they could load six sections at once; only one member could be transported by truck.
The disadvantage to barge transportation was that it took a couple months to move pieces, but it was only three hours away by truck. Plus, the season for barging was limited. The upper Mississippi River is closed in early December because of ice formation.
“We had to meet a deadline of getting the pieces to the barge before wintertime,” Johnson said. “That created a time crunch to get these pieces completed, put them on a barge, and then shipped. That required some hustling on our end to make that happen.”
That “hustling” meant that the team worked around the clock and on weekends. “It was a lot of strain on our workforce to work them seven days a week for many weeks,” Johnson said.
Shipping some of the arch sections for the eastbound bridge by truck was no walk in the park either. “When you're crossing multiple states with such large pieces … that was a challenge for sure. For superloads over 200,000 lbs. gross weight, you need shipping permits from every state the load travels through, need regular escorts front and back of the load, and police escorts that change once you reach the state line,” Shah said. All these logistics required extensive planning and coordination.
“We are literally only seven miles to the Illinois border, but we needed Indiana police escorts from Gary to the Illinois state line. Then we had to have Illinois police escorts to take the load to the Iowa State line, and finally Iowa police escorts to take the load to the job site,” Shah said.
Coming Together On-Site
The bridge fabrication fit-up on-site went very well, Shah and Johnson explained.
The arch bases at the bottom had to be very precisely machined for the fit-up at assembly and erection. It’s unusual for something as large as an 800-ft.-long bridge to need the precision of machining, but the members were all designed with tight tolerances. The arch bases had to be machined within 0.015 in.—which is extremely precise for a structural steel fabrication, according to Shah.
Every piece of the arch had unique dimensions. Everything had to be very precise to fit. The design company actually had a special provisions section for the project-specific tolerances.
Even with all of the careful planning and effort, with tight arches like these, some small adjustments had to be made. “The bridge was precisely fabricated, but field activities are outside of ISC’s control,” Johnson said, jokingly.
“The arch bases were 800 ft. apart,” Shah added. “It was like building a 1,000-ft.-long iPhone within tight fabricating tolerances.”
The only final adjustment needed was reducing the keystone member by less than a few inches to fit. “When they got to the keystone piece and they measured across, the dimension didn't come out exact. We had to do some trimming there,” Johnson said.
A Pinnacle Project
The I-74 Iowa-Illinois Memorial Bridge is one of the most complex the company has fabricated, Johnson and Shah agreed. Running plate girders and box sections is very different than fabricating a true-arch, basket-handle bridge, Shah said.
“Doing the eastbound and westbound of the I-74 arch bridges, back-to-back, definitely helped us understand the fabrication complexities required. The advantage of having fabricated the westbound arch sections first was that we used our learning curve on the eastbound,” Shah said.
“I think our workforce did a fantastic job. These kinds of signature projects are very unique, and being a part of this bridge brings us joy, a sense of accomplishment, and ‘can-do’ attitude for the entire ISC team,” he added.
Construction on the bridge project began in July 2017 and was completed by the end of 2021.
About the Author
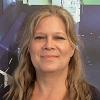
Kate Bachman
815-381-1302
Kate Bachman is a contributing editor for The FABRICATOR editor. Bachman has more than 20 years of experience as a writer and editor in the manufacturing and other industries.
Related Companies
subscribe now
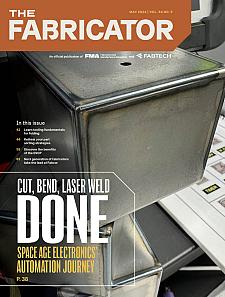
The Fabricator is North America's leading magazine for the metal forming and fabricating industry. The magazine delivers the news, technical articles, and case histories that enable fabricators to do their jobs more efficiently. The Fabricator has served the industry since 1970.
start your free subscription- Stay connected from anywhere
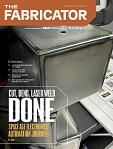
Easily access valuable industry resources now with full access to the digital edition of The Fabricator.
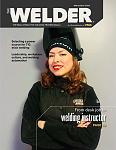
Easily access valuable industry resources now with full access to the digital edition of The Welder.
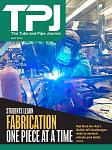
Easily access valuable industry resources now with full access to the digital edition of The Tube and Pipe Journal.
- Podcasting
- Podcast:
- The Fabricator Podcast
- Published:
- 04/16/2024
- Running Time:
- 63:29
In this episode of The Fabricator Podcast, Caleb Chamberlain, co-founder and CEO of OSH Cut, discusses his company’s...
- Trending Articles
Tips for creating sheet metal tubes with perforations
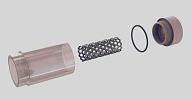
Are two heads better than one in fiber laser cutting?
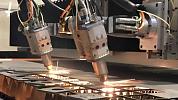
Supporting the metal fabricating industry through FMA
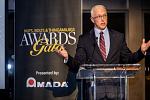
JM Steel triples capacity for solar energy projects at Pennsylvania facility
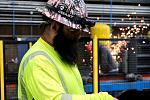
Omco Solar opens second Alabama manufacturing facility
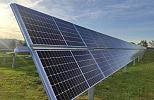
- Industry Events
16th Annual Safety Conference
- April 30 - May 1, 2024
- Elgin,
Pipe and Tube Conference
- May 21 - 22, 2024
- Omaha, NE
World-Class Roll Forming Workshop
- June 5 - 6, 2024
- Louisville, KY
Advanced Laser Application Workshop
- June 25 - 27, 2024
- Novi, MI