Contributing editor
- FMA
- The Fabricator
- FABTECH
- Canadian Metalworking
Categories
- Additive Manufacturing
- Aluminum Welding
- Arc Welding
- Assembly and Joining
- Automation and Robotics
- Bending and Forming
- Consumables
- Cutting and Weld Prep
- Electric Vehicles
- En Español
- Finishing
- Hydroforming
- Laser Cutting
- Laser Welding
- Machining
- Manufacturing Software
- Materials Handling
- Metals/Materials
- Oxyfuel Cutting
- Plasma Cutting
- Power Tools
- Punching and Other Holemaking
- Roll Forming
- Safety
- Sawing
- Shearing
- Shop Management
- Testing and Measuring
- Tube and Pipe Fabrication
- Tube and Pipe Production
- Waterjet Cutting
Industry Directory
Webcasts
Podcasts
FAB 40
Advertise
Subscribe
Account Login
Search
3 angles on press brake training: Part I (video enhanced)
Expert-taught in classroom or in-plant, or vendor-taught in plant
- By Kate Bachman
- March 29, 2018
- Article
- Shop Management
Editor’s Note: This article is the first of three in a series about different approaches to press brake training. Part I highlights training in a classroom environment; Part II, to be published in the May issue, explores press brake tooling and training on-site; Part III, which will be published in the July issue, explores training by a machine OEM, as well as part design.
The skilled worker crisis has been looming for a long time. Despite manufacturing resource centers, community college technology programs such as Skills for America’s Future, and a slow and spotty resurgence of tech classes in high schools, the complaint persists that new skilled and trained fabricators are too few and too far between. That is no less true for press brake operators than for anyone else.
The situation is near-dire, as skilled press brake fabricators in the typical shop number in the single digits. Shop owners’ worries go something like this: “If my experienced press brake operator gets hit by a bus, I’m in trouble.”
Fortunately, fab shop managers can stop worrying about an oncoming bus and can obtain good training for their employees from at least three angles.They can get a solid introduction and overview in a two-day certificate course taught by Fabricators & Manufacturers Association Intl. (FMA) instructor and press brake guru Steve Benson in a classroom setting with attendees from other companies. Alternatively, they can receive a customized overview and certificate course in their own plants on their own equipment taught by FMA instructors, including Benson; or they can receive training on the specific brand of new press brake they purchase from an OEM.
In Class by a Guru
Steve Blanchard, foreman at Pioneer Truckweld Inc., Salem, Ore., sent two of his newer press brake operators to FMA’s press brake training certificate class in February at FMA’s headquarters in Elgin, Ill.
“Press brake forming is kind of a lost art, if you will,” he said. Having been self-taught, Blanchard really appreciates the value of a curriculum program. “I did a lot of reading—and a lot of trial and error.”
Blanchard said that although the company performs ongoing training in-house, he thinks it is beneficial for the trainees to be exposed to training from more than the one experienced press brake operator in his plant. “I feel like if they get the basic fundamentals of forming, they’re going to be better prepared and not coming into it blind.
“I want Alejandro and Ben to attend this class and come back knowing the fundamentals—what type of tooling we can and cannot use, bend sequence…being able to calculate blank sizes of any given part—the tonnage calculations and the do’s and don’ts that come with being a proficient press brake operator,” Blanchard continued.
Pioneer fabricates the boxes for dump trucks from 12-gauge steel all the way to 5/16-in. AR 450 hardened plate (see Figure 1). One of Pioneer’s machines is a small TRUMPF 10-foot, 120-ton press brake with European tooling and setup and the other is a Cincinnati 600-ton machine with American tooling that bends 20-ft.-long parts.
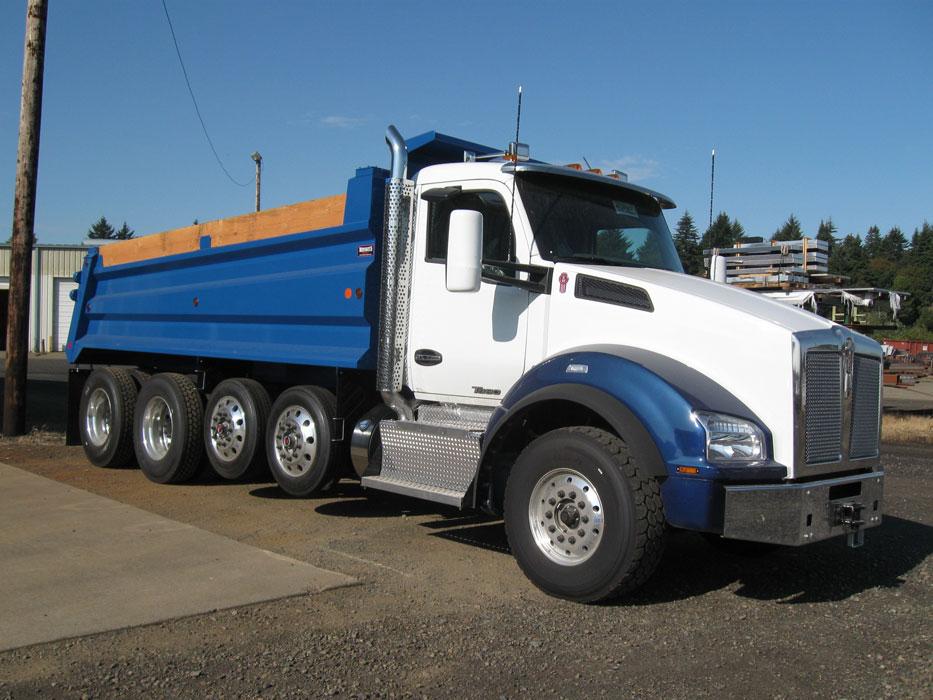
Figure 1
Pioneer Truckweld bends its dump bodies from 12-gauge steel to 5/16-in.-inch-thick AR 450 hardened plate on a Cincinnati 600-ton press brake that bends 20-ft.-long parts.
Learning the math is important in terms of saving material and material costs, he said. The fabrication of dump truck sides requires performing a lot of multiple bends. Many of the angles have tight tolerances. “We have prints to work off of, but sometimes we get the one-off custom stuff, where you have to sit down and do the math and figure out your blank for yourself. So I want them to do able to do that.”
Knowing the calculations will save money and time, making the operators more proficient, he added. “If they have to put 10 hits in a 10-gauge blank, I want them to know how much that sheet is going to grow as they’re making the bends all the way down it. That way they know what their material usage is, and they’re not burning up a piece of 60-by-120 10-ga. that ends up being wrong in the end.”
Training is necessary not only so that the operators are more productive, but also to prevent damage to the tooling and machine, Blanchard said. “The tonnage on some of that stuff is 33 tons a foot,” he said.
“I don’t want those guys to think they can bend anything in any machine. I want them to be able to calculate and realize, ‘I can’t use that tooling because I’ll end up breaking it.’ The machine might do it, but the tooling won’t hold up.
“It’s important when they’re grabbing material that they know which bottom they’re shoving it into,” Blanchard continued. “They need to know the bend tolerances, what it’s going to snap at, and if the machine is actually capable of bending it beforehand. From a production standpoint, if they grab a piece of ¼-in. AR450 plate and want to shove it into a 2-in. bottom, it’s not going to happen. They need to know that type of stuff before they load their tooling into the press brake.”
Press Brake Class Delivers
Fortunately the class does cover all of the above topics and many more.
It begins with bend functions, including the mathematics behind bend radii. Next, attendees learn to interpret flat patterns and blueprints for layout and forming. Benson gives an overview of the types of machine and forming methods.
The class delves into proper tool selection, tonnages, and load limits. Then the attendees are introduced to die selection and the die’s effect on radii. They learn about specialized tooling, including urethane, offset, and bump radius. Benson throws in some tips of the trade: “Better to shim up from the bottom than down”; “Dwelling at bottom helps set the material to counter springback”; and “Bend across the grain, not with the grain, to avoid cracking the material.”
The class goes over bottom bending and air bending—the advantages and limitations of each. The last and most enduring topic covered is safety. “Never put your hand between the punch and the die,” Benson emphasized.
Most of the course occurs in the classroom, although the group does have a chance to tour a nearby facility, where they can see press brakes bending in action. The second day wraps up with a test, which an attendee must pass to earn the certificate.
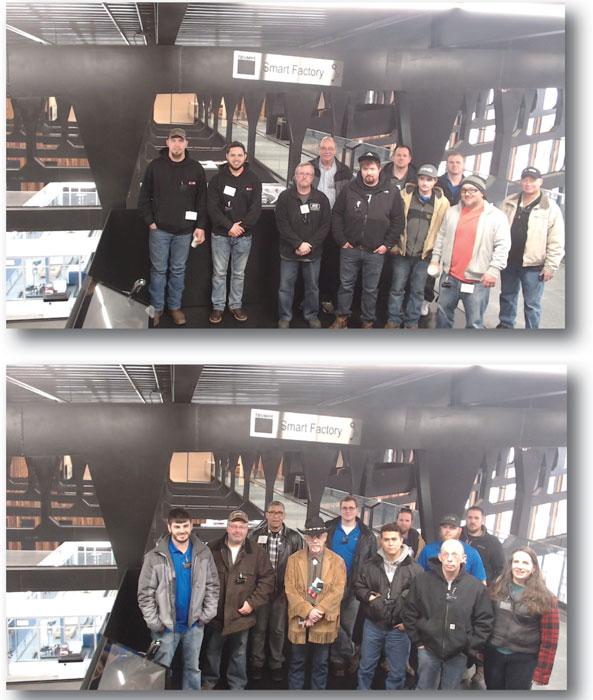
The FMA press brake certificate class in February toured TRUMPF’s Smart Factory to see press brake bending in action.
Attendees Rock the Course
Attendees at the class included experienced press brakes operators and those new to the trade, as well as engineers, designers, and instructors.
One of the two press brakes operators from Pioneer Truckweld who attended the course was Alejandro Mejia Leon. “Probably one of things that I was most surprised to learn is how deep into quality control you can go in bending or forming something … how much you can actually do with press brakes.”
Dennis Bouton has been a press brake operator at Rockford Toolcraft for seven years. He participated in the class to round out his knowledge, with an emphasis on the math and calculations. He said the class helped him gain a better understanding of why he was doing what he was doing. Much of what he learned previously was by trial and error, he said. It enriched his understanding of the bend line radius, calculations, air bending and bottom bending, and the terminology.
Jason Schultz is a designer for HCC Inc. His primary reason for attending the class was to gain a better understanding of what the operators can do with the tooling so he can design for manufacturability. “I’m trying to learn what the shop floor is dealing with in regards to what I’m designing,” he said. He was surprised to learn of some of the unique bend profiles that can be done and said that what he learned in the class will expand the types of parts that he designs. “The biggest thing that came from this is understanding the bottom dies and how they affect what the operator is trying to do. Understanding better what’s available to us on the shop floor helps me design better, makes it easier on the operators, and makes us more efficient,” Schultz explained.
Jonathon Cramer is a manufacturing engineer for Modine Mfg. He said he came from a roll forming and tube and pipe discipline and wanted to learn about press brake tooling and mathematics. “What I found most surprising is the versatility of press brake tooling. Where I come from, you have one set of tooling for one part. Here you can form a multitude of parts.”
Richard Davis attended both in the capacity of an instructor for Central Piedmont Community College and as CNC engineer for fabricator Jerico Performance Products in North Carolina, which supplies parts for racing companies. He has experience with press brakes from a CNC aspect and is researching press brakes to spec for a purchase for the college.
Steve Benson’s Top Takeaways
So what does the course instructor consider as the most important takeaways?
“The first most important takeaway is the inside radius—where it comes from and how important it is to everything sheet metal,” Benson said. “It’s the heart of sheet metal bending. If they don’t get the radius right, they won’t get anything else right.”
The second takeaway? “Tonnages; learning what the limits are and making sure they’re not going to overload the tooling so they don’t damage the press brakes.”
Third? “Learning about sharp bends. If they’re air forming, they can’t actually achieve that. The tool has to be sharper than the radius that’s going to be involved in the part. So they have to take that out of their calculations when they’re bending parts. Again, that gets back to the radius.
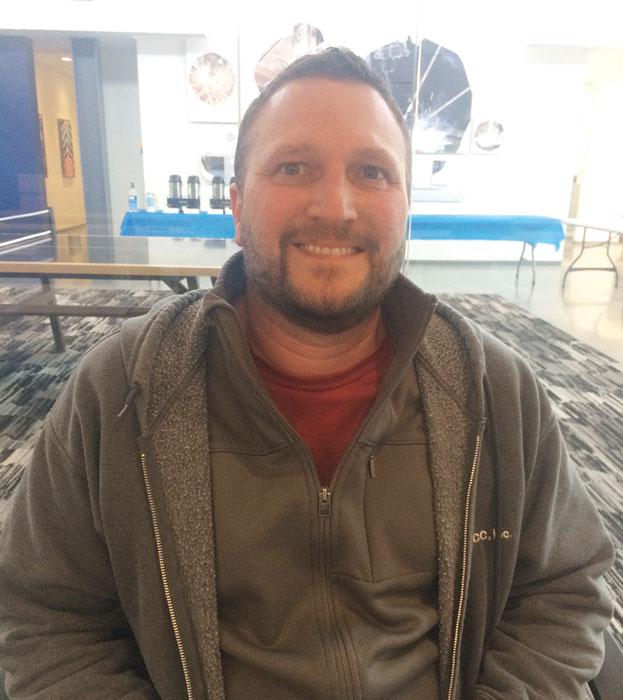
Jason Schultz, a designer for HCC, wanted a better understanding of the bending process and capabilities to improve his designs for manufacturability.
“The fourth most important takeaway would be safety—or maybe that’s the first,” Benson continued. “There are so many ways to get hurt. You can lose a finger if you’re not paying attention to the safety rules. You want to keep the body parts you started with.”
Cincinnati Incorporated, www.e-ci.com/press-brakes
Pioneer Truckweld, ptwtruckandpup.com
TRUMPF Inc., www.trumpf.com
About the Author
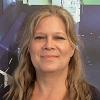
Kate Bachman
815-381-1302
Kate Bachman is a contributing editor for The FABRICATOR editor. Bachman has more than 20 years of experience as a writer and editor in the manufacturing and other industries.
subscribe now
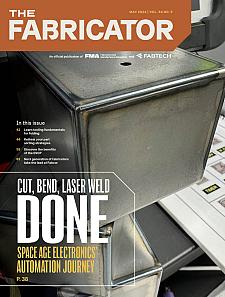
The Fabricator is North America's leading magazine for the metal forming and fabricating industry. The magazine delivers the news, technical articles, and case histories that enable fabricators to do their jobs more efficiently. The Fabricator has served the industry since 1970.
start your free subscription- Stay connected from anywhere
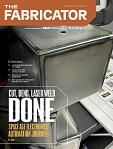
Easily access valuable industry resources now with full access to the digital edition of The Fabricator.
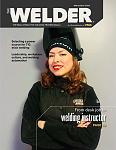
Easily access valuable industry resources now with full access to the digital edition of The Welder.
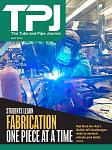
Easily access valuable industry resources now with full access to the digital edition of The Tube and Pipe Journal.
- Podcasting
- Podcast:
- The Fabricator Podcast
- Published:
- 04/16/2024
- Running Time:
- 63:29
In this episode of The Fabricator Podcast, Caleb Chamberlain, co-founder and CEO of OSH Cut, discusses his company’s...
- Trending Articles
Tips for creating sheet metal tubes with perforations
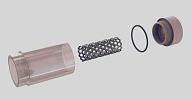
Supporting the metal fabricating industry through FMA
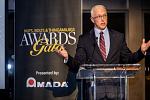
JM Steel triples capacity for solar energy projects at Pennsylvania facility
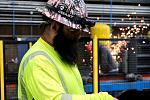
Are two heads better than one in fiber laser cutting?
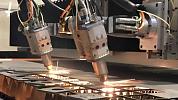
Fabricating favorite childhood memories
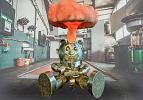
- Industry Events
16th Annual Safety Conference
- April 30 - May 1, 2024
- Elgin,
Pipe and Tube Conference
- May 21 - 22, 2024
- Omaha, NE
World-Class Roll Forming Workshop
- June 5 - 6, 2024
- Louisville, KY
Advanced Laser Application Workshop
- June 25 - 27, 2024
- Novi, MI