Principal
- FMA
- The Fabricator
- FABTECH
- Canadian Metalworking
Categories
- Additive Manufacturing
- Aluminum Welding
- Arc Welding
- Assembly and Joining
- Automation and Robotics
- Bending and Forming
- Consumables
- Cutting and Weld Prep
- Electric Vehicles
- En Español
- Finishing
- Hydroforming
- Laser Cutting
- Laser Welding
- Machining
- Manufacturing Software
- Materials Handling
- Metals/Materials
- Oxyfuel Cutting
- Plasma Cutting
- Power Tools
- Punching and Other Holemaking
- Roll Forming
- Safety
- Sawing
- Shearing
- Shop Management
- Testing and Measuring
- Tube and Pipe Fabrication
- Tube and Pipe Production
- Waterjet Cutting
Industry Directory
Webcasts
Podcasts
FAB 40
Advertise
Subscribe
Account Login
Search
Scratching the surface of total productive maintenance
How implementing TPM pays for itself many times over
- By Jeff Sipes
- February 6, 2018
- Article
- Shop Management
Sound familiar? What do we do to address the situation? Probably muscle our way through somehow and get the order out. We may get a certain amount of satisfaction by muscling the order out the door—maybe a few high-fives, doughnuts, or a special thank you to those who got it done.
But let’s take a step back and consider a more effective, longer-term approach: total productive maintenance (TPM). Why did the machine break down in the first place? Does the fault indication occur regularly? Did the machine operator know about this and just deal with it because he’s already told his boss about it many times and he’s tired of being ignored?
As lead times continue to shrink, equipment availability becomes increasingly vital. If your company is focused on breakdown maintenance, it may be time to consider TPM.
Defining TPM
TPM is a holistic approach to ensuring equipment is ready to run as it is designed to run whenever you need it to run. It has various components, including:
- Autonomous maintenance (AM), for which operators perform regular maintenance that is within their control and capability.
- A system that includes a schedule detailing tasks for daily, weekly, monthly, quarterly, semiannual, and annual preventive maintenance (PM).
- Measurement systems that indicate the state of TPM and equipment readiness; this can range from a simple measurement such as “operator PM compliance” to more sophisticated measurements such as “mean time between failure.”
- A process for analyzing pieces of equipment and how critical each is to the operation, then managing and investing in spare parts accordingly.
- Performing audits to ensure TPM occurs and that there is accountability for equipment readiness results.
Business Case for TPM
What happens when you do not know the state of your equipment? Chances are you make decisions based on feelings or anecdotes. That machine goes down about two hours a week. This robot welder seems to lose 45 minutes per shift. The chip conveyor seems to always be breaking down or getting clogged. All of these examples have costs associated with them. But without focus and measurement, it is all a guess.
When the spindle bearing has worn out and the machining center is down for 12 hours, you can assign a reasonably direct cost to that downtime. The new bearing had to be expedited from a supplier, the two maintenance technicians worked eight hours of overtime to make repairs, and the lost machine capacity resulted in a crew having to work on Saturday (unplanned overtime). Those are the tangible dollars.
But what about the less tangible forms of disruption … and, therefore, cost? When the machines and equipment are greasy, the floor around the machine is slippery, and the area is generally just one big mess. Who wants to jump in and get up close and personal with the machine? Probably not the operator and probably not the maintenance technician.
Identifying the problem and finding a solution in this situation will take longer than if you had a good handle on the equipment. Reactive maintenance time may not happen all at once. You’ll have 15 minutes here, 45 minutes there. A maintenance tech may just “make it work” to avoid a breakdown temporarily, at least until people on the next shift have no choice but to deal with the problem. These minor disruptions are much harder to quantify, but they can add up to major dollars and lost time.
Implementing TPM does have some incremental costs. These might include specific, targeted, and planned downtimes to perform PM. You probably will invest in specific spare parts. And you might decide to get serious and hire a TPM specialist, a person who “owns” the process of TPM. But you should expect these and other costs to be offset by the increased reliability and availability of your equipment.
Daily PMs Performed by Operators
Who knows more about the hour-by-hour performance of a piece of equipment than the operator? No one! Design a process for operators to follow so that they can handle the small things and keep an eye on the big things. This is the beginning of autonomous maintenance.
To implement this, identify what PM activities the operator should perform. They could include checking the oil level, clearing chips from a conveyor, checking that the air intake filter is clear, and confirming air pressure is within a target range.
Create a PM check list, a work order with PM activities, or something else that the operator can follow. Then have a maintenance technician and area supervisor train the operator at the machine on each shift. Then have the operator check off items on a check list or clock out on PM work orders each day.
Supervisors and/or the TPM manager (process owner) should audit these practices periodically to confirm that daily PM is really being done. Managers should measure for PM compliance and share results with stakeholders monthly.
The TPM process owner might be dedicated solely to TPM (more common in larger operations) or the same person as the maintenance supervisor or manager (as is typical in smaller operations). Either way, let’s carve out the TPM process owner’s roles and responsibilities to understand what this person should be doing and why this can be a high-impact job. We can divide the job into two focus areas: systems and information and process and execution.
The systems and information focus entails defining TPM and asset management performance metrics and working with plant managers to develop and implement them. The TPM process owner also reports maintenance and asset performance metrics to senior management and provides general oversight to information system integrity and usage as it relates to TPM, AM, and asset control.
To carry out the process and execution focus, the process owner participates as a member of the leadership team. He sets TPM strategy, serves as the primary lead for maintenance budgets (the secondary lead is the plant manager), and builds the skill of the maintenance staff. The process owner also develops a spare parts strategy and leads the maintenance organization in the execution of this strategy. He provides leadership for AM training and development, and he works with plant managers to develop and execute an AM plan.
He leverages TPM best practices across the company and serves as the primary lead for maintenance staff performance evaluations. And he works closely with company leadership, ultimately ensuring that the right piece of equipment is available in the right place at the right time.
TPM Blitz
The TPM blitz is modeled after the kaizen event approach to improvement, except the focus is on the machine. A cross-functional team (maintenance technicians, operators, engineers, and managers, for example) meet for a set period of time (three-day blitzes are very effective). Maintenance technicians conduct a “pre-blitz” to assess what specific work needs to be done and what parts and supplies need to be ordered so that they’re on hand when the blitz starts.
The TPM blitz uses many of the same methods used in a kaizen event. It has many elements of 5S, visual controls, and root cause analysis. Deep cleaning (guards and way covers removed, cleaned, and painted) will take place, leaks will be found and fixed, and brakes/brushes/controls will be brought up to like-new condition.
The blitz gives maintenance technicians time to work on issues they routinely cannot get to, either because of the machine work load or because they need more time outside production to access a particular part of the machine. The TPM blitz can be a great way to perform semiannual or annual preventive maintenance.
Ready to Run
If the machine is not ready to run when you need it to run, bad things happen. These bad things can have tangible costs (overtime to make up for the unplanned downtime) and intangible costs and disruptions (the maintenance technician and the operator fuss with each other for 30 minutes trying to get the other to clean around the machine before breakdown maintenance can even begin).
Bad things also can include a customer who’s dissatisfied because you didn’t ship by the promised date. Unreliable, unpredictable, and underperforming equipment leads to stress among all the relevant parties.
TPM is a proven approach to bring your equipment up to a targeted condition—and we’ve only scratched the surface. The upside can be amazing. The cost and disruption of not pursuing TPM can be debilitating.
Jeff Sipes is principal of Back2Basics LLC, 317-439-7960, www.back2basics-lean.com. If you have improvement ideas you’d like to read about, contact him at jwsipes@back2basics-lean.com or Senior Editor Tim Heston at timh@thefabricator.com.
About the Author
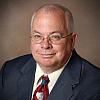
Jeff Sipes
9250 Eagle Meadow Dr.
Indianapolis, IN 46234
(317) 439-7960
subscribe now
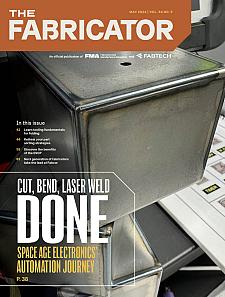
The Fabricator is North America's leading magazine for the metal forming and fabricating industry. The magazine delivers the news, technical articles, and case histories that enable fabricators to do their jobs more efficiently. The Fabricator has served the industry since 1970.
start your free subscription- Stay connected from anywhere
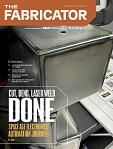
Easily access valuable industry resources now with full access to the digital edition of The Fabricator.
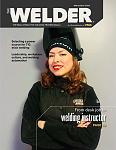
Easily access valuable industry resources now with full access to the digital edition of The Welder.
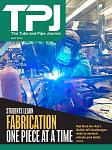
Easily access valuable industry resources now with full access to the digital edition of The Tube and Pipe Journal.
- Podcasting
- Podcast:
- The Fabricator Podcast
- Published:
- 04/16/2024
- Running Time:
- 63:29
In this episode of The Fabricator Podcast, Caleb Chamberlain, co-founder and CEO of OSH Cut, discusses his company’s...
- Trending Articles
Tips for creating sheet metal tubes with perforations
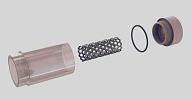
JM Steel triples capacity for solar energy projects at Pennsylvania facility
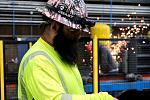
Are two heads better than one in fiber laser cutting?
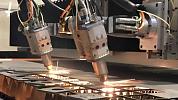
Supporting the metal fabricating industry through FMA
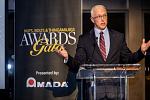
Omco Solar opens second Alabama manufacturing facility
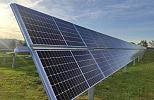
- Industry Events
16th Annual Safety Conference
- April 30 - May 1, 2024
- Elgin,
Pipe and Tube Conference
- May 21 - 22, 2024
- Omaha, NE
World-Class Roll Forming Workshop
- June 5 - 6, 2024
- Louisville, KY
Advanced Laser Application Workshop
- June 25 - 27, 2024
- Novi, MI