Contributing editor
- FMA
- The Fabricator
- FABTECH
- Canadian Metalworking
Categories
- Additive Manufacturing
- Aluminum Welding
- Arc Welding
- Assembly and Joining
- Automation and Robotics
- Bending and Forming
- Consumables
- Cutting and Weld Prep
- Electric Vehicles
- En Español
- Finishing
- Hydroforming
- Laser Cutting
- Laser Welding
- Machining
- Manufacturing Software
- Materials Handling
- Metals/Materials
- Oxyfuel Cutting
- Plasma Cutting
- Power Tools
- Punching and Other Holemaking
- Roll Forming
- Safety
- Sawing
- Shearing
- Shop Management
- Testing and Measuring
- Tube and Pipe Fabrication
- Tube and Pipe Production
- Waterjet Cutting
Industry Directory
Webcasts
Podcasts
FAB 40
Advertise
Subscribe
Account Login
Search
Workforce training and automation, recurrent interwoven themes at FABTECH 2022
The metal forming and fabricating show beckoned 30,000 stampers, metal manufacturers to Atlanta
- By Kate Bachman
- November 30, 2022
FABTECH 2022 in Atlanta summoned nearly 30,000 attendees, falling short by only a few hundred of the number who attended the previous Atlanta show in 2018. More than 1,100 exhibitors displayed and demonstrated their technologies in the halls that totaled more than 10 football fields in size.
Prevalent on the FABTECH 2022 show floor was a feeling of exuberance detectable in the tenor of conversation, the pace of gait, the shine in people’s eyes, in the air—at just getting back to business. Show-goers were talking, nodding, sharing, hearing, watching, engaging, and just experiencing being together in a state of normalcy.
The unseasonably warm weather in Atlanta in November helped facilitate an easygoing after-hours uptick in activity. Downtown Atlanta was downright happening. Many people were out, ambling in and out of restaurants and bars, smiling, and conversing.
It felt really good to be there.
NASCAR race car driver and team owner Brad Keselowski showed his bonafides as a manufacturer in his keynote presentation, “Winning the Manufacturing Race,” in which he shared his unique perspective on integrated manufacturing modeled after the pit row approach.
In the stamping and metal forming area, there was a noticeable recurrency of themes surrounding workforce training and automation. Several of the technological advancements exhibited there are intended to either support a human workforce or reduce the reliance on it.
New Technology
Beckwood Press Co. launched its patent-pending linear servo press (LSP). The new type of press combines the flexibility of a hydraulic press with the performance of a servo-mechanical press, using an all-electric actuation system, the company says. “This combines the best of both worlds: Full tonnage throughout the stroke, dwell at bottom dead center, and precision without hydraulics, crankshafts, or flywheels,” said Caleb Dixon, sales manager. Models range from 125 to 500 tons of force.
Nidec Press & Automation debuted its global production control simulator. It comprises a digital twin of a press, the feed, and the transfer so that a stamper can see its system in motion. The simulator can be used for two things: “One is for training new operators off-site. You don’t need to have the press in front of you. We can do it in a classroom or in our training center,” said David Diaz-Infante, servo press scientist. In addition, it can be used for offline optimization of the motion profiles, creating the recipes for the new jobs before they arrive, die protection, and emergency stops, he added.
Wintriss Controls developed new features in its SmartPAC 2 controller to improve productivity and to allow remote subject matter experts quick access to troubleshooting. The company also displayed features to help and support automation, adding monitoring features to more effectively monitor complex dies and configurable tooling. “We have the world’s most powerful programmable limit switch that, in many cases, replaces PLCs,” said Product Manager Jim Finnerty.
AIDA America showcased its newest press, an A-series gap-frame servo press. It features an Allen Bradley servo control and 5% to 10% higher speeds than its previous servo gap frame press. Attendees were able to view a “silent” blanking die demonstration and see different motion profiles intended to help stampers solve challenges they may face, according to AIDA America Marketing Manager Lisa Goddard.
Workforce Training
Formtek-Maine stepped up its coil processing automation to help with workforce training. “The reason is the inability for customers to either hire or retain employees, said Kevin Enos, vice president of sales, Midwest. Help comes via step-by-step walk-throughs that are included in the HMI and the addition of multiple in-process capabilities such as punching, notching, slitting, and shearing on a single coil line.
Komatsu America Industries may have showcased its E2W300 servo press, but the buzz was on workforce training. “A lot of people tell us that their major concern is training because there are a lot of new industry technologies coming out, a lot of automation, new materials, and there is a high turnover rate in the industry as well,” said Vice President Jim Landowski. “Our policy is to maintain our training and retraining, without charge, throughout the life of that product,” he added.
Coe Press Equipment has developed a number of approaches to workforce training. The first is virtual reality goggles that allow users to view what is on the shop floor and access the controls. Showgoers had a chance to try on the VR goggles to experience it. Second, the company developed a number of short videos on its website, designed to give stampers a primer in coil processing equipment. Third, Coe expanded its service staff significantly to offer hands-on training and assistance to support people in production.
“So this year we’ve hired over 14 people in service; we are opening three different service hubs; we have two service hubs opening in Mexico. We have a direct salesperson in Mexico. So, it’s about expanding our service footprint,” said President Reid Coe, adding, “It’s not just about shipping equipment.”
Sustainability EHS
Colt Automation showcased an uncoiler and feeder/straightener combination that has been developed specifically for work materials for electric vehicles. “We’ve really seen a surge of work in the electric vehicle segment of the market in the last year or so. This piece of equipment will be processing battery components for electric vehicles,” said Stuart Cordrey, vice president, sales. He said that the demand to process thin-gauge aluminum has increased. The feeder/straightener has been customized with an “alligator head” that allows operators to get inside and clean off the chaff so it doesn’t mark the aluminum, he said.
Tower Metalworking Fluids showcased its safety- and environmentally oriented Saf-T-Vanish metalworking fluids designed to protect more than the metal products. “Stampers have been talking about wanting to get more health and safety aware. They want to improve their processes and environment for their operators,” said Chris Fletcher, sales and marketing manager. The fluids are formulated with ingredients derived from nonhazardous materials. They contain no HAPs or VOCs and evaporate quickly without the use of harsh hydrocarbon-based solvents, eliminating the need for cleaning the parts before painting, plating, and final assembly.
CoilTech, a new exhibitor to FABTECH, showcased a new compact coil feeder requiring an average of 18 ft. of floor space. Its coil feeding lines, Series 1, Series 2, and HD Series 3, handle coil widths from 200 mm to 2,000 mm, and thicknesses from 0.4 mm to 10 mm. They are equipped with servo motorized coil side guides, a servo roll adjustment, a crocodile opening system, powered passline adjustment, and coil loading car.
subscribe now
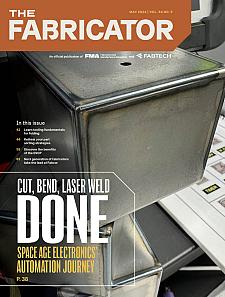
The Fabricator is North America's leading magazine for the metal forming and fabricating industry. The magazine delivers the news, technical articles, and case histories that enable fabricators to do their jobs more efficiently. The Fabricator has served the industry since 1970.
start your free subscriptionAbout the Author
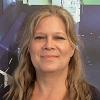
Kate Bachman
815-381-1302
Kate Bachman is a contributing editor for The FABRICATOR editor. Bachman has more than 20 years of experience as a writer and editor in the manufacturing and other industries.
- Stay connected from anywhere
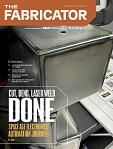
Easily access valuable industry resources now with full access to the digital edition of The Fabricator.
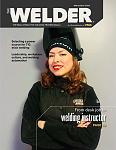
Easily access valuable industry resources now with full access to the digital edition of The Welder.
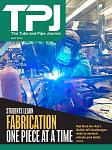
Easily access valuable industry resources now with full access to the digital edition of The Tube and Pipe Journal.
- Podcasting
- Podcast:
- The Fabricator Podcast
- Published:
- 04/16/2024
- Running Time:
- 63:29
In this episode of The Fabricator Podcast, Caleb Chamberlain, co-founder and CEO of OSH Cut, discusses his company’s...
- Trending Articles
Tips for creating sheet metal tubes with perforations
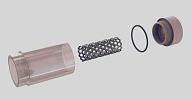
JM Steel triples capacity for solar energy projects at Pennsylvania facility
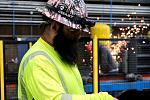
Are two heads better than one in fiber laser cutting?
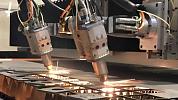
Supporting the metal fabricating industry through FMA
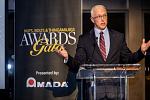
Omco Solar opens second Alabama manufacturing facility
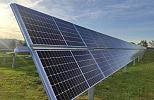
- Industry Events
16th Annual Safety Conference
- April 30 - May 1, 2024
- Elgin,
Pipe and Tube Conference
- May 21 - 22, 2024
- Omaha, NE
World-Class Roll Forming Workshop
- June 5 - 6, 2024
- Louisville, KY
Advanced Laser Application Workshop
- June 25 - 27, 2024
- Novi, MI