Contributing editor
- FMA
- The Fabricator
- FABTECH
- Canadian Metalworking
Categories
- Additive Manufacturing
- Aluminum Welding
- Arc Welding
- Assembly and Joining
- Automation and Robotics
- Bending and Forming
- Consumables
- Cutting and Weld Prep
- Electric Vehicles
- En Español
- Finishing
- Hydroforming
- Laser Cutting
- Laser Welding
- Machining
- Manufacturing Software
- Materials Handling
- Metals/Materials
- Oxyfuel Cutting
- Plasma Cutting
- Power Tools
- Punching and Other Holemaking
- Roll Forming
- Safety
- Sawing
- Shearing
- Shop Management
- Testing and Measuring
- Tube and Pipe Fabrication
- Tube and Pipe Production
- Waterjet Cutting
Industry Directory
Webcasts
Podcasts
FAB 40
Advertise
Subscribe
Account Login
Search
Heading into a blistering storm that wasn’t
- By Kate Bachman
- April 24, 2018
On Wednesday of last week, I braced to face the second wave of a snowstorm that hit the upper Midwest the weekend prior to traveling to Paynesville, Minn., to interview metal fabricator Louis Industries. The region, northwest of Minneapolis, had been hit with a foot and a half of snow on Saturday and another half-foot was predicted.
I donned a pair of winter boots and my wooliest Nordic sweater, packed a winter storm kit—shovel, blanket, bag of sand, battery cables, and, that iconic but rarely used necessity, a candle in a can—and upgraded my rental vehicle to a two-story, four-wheel-drive SUV to brave what I thought would be a blizzardy, sleeting, wheel-gripping, all-day drive to Minnesota.
And then the storm bypassed me, somehow. I did not encounter a single snowflake.
It’s a little unusual for me to be overprepared. It’s more common for me to encounter something I’m not prepared for.
Turning Plowshares Into Metal Fabrications
Leo Louis, one of two brothers in the second generation of the family-owned company and current CEO told me that historically they have always tried to anticipate where the market is going so that they can stay in front of it—to be prepared for the storms, so to speak.
“Everything evolves and keeps changing, and you have to change with it,” Leo told me during the on-site interview. He has seen his family business evolve over three generations from its origins as a blacksmith shop. He has witnessed the demise of the plowshares that the company had manufactured for the surrounding agricultural industry in its early years and the manufacturer's evolution into a steel processor and job shop fabricating components for a broad range of industries.
Leo has seen the prominence of lasers in metal fabrication and the demise of drill presses. “Industry is calling for a different way of making things,” he said. “Lasers changed the way you look at doing things, so we just changed along with that. We had to stay ahead of the moves.”
New Business Model
Leo’s son, Lance Louis, who is the COO, said he has witnessed his share of changes as well.
Lance has shepherded the integration of software, engineering, design, and automation in metal fabrication. Dan Andersen, who heads up the design, engineering, and inspection there, explained it this way:
“What manufacturing is coming down to is the model. We're taking this SOLIDWORKS® model and creating a press brake program and the flat pattern for the laser for the punch. Oh, by the way, we're also taking the 3-D model and doing inspections. Now we can create a print and a weld fixture. It's become the pivotal important item. Once you get the model right, you can use the other software to create press brake programs, laser programs, inspection programs, 3-D robotic welding programs, 3-D printing, and fixtures for go/no-go gauges.”
Lance maintains that modeling software has altered the way the company approaches troubleshooting as well.
“It used to be, when a part was wrong, we'd argue over whose fault it was. What's nice about the software models is that now we can recreate how we made it so we can isolate the error. The conversation changes from ‘It's your fault, no, it's your fault’ to ‘Let's look at the model … how do we fix this?’”
Lance has also witnessed a waning population in his area that has directly affected his ability to grow his workforce along with the company.
“We used to have eight restaurants in town. Now we have two. We're losing people,” he commented.
“We're not getting kids from farms who have skills. Now we hire people without experience or skills and have to make it work,” Lance said. For that reason, he feels compelled to both have good training programs to educate employees to operate the equipment well, and to invest in intuitive software that shortens the time needed to train them. It’s all about being prepared for whatever the storm blows in.
When you are prepared, things go better than expected, don’t they?
Read more about Louis Industries in the June issue ofThe FABRICATOR®.
subscribe now
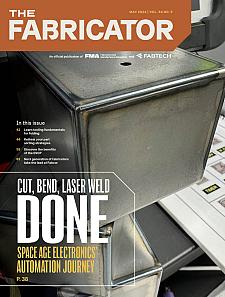
The Fabricator is North America's leading magazine for the metal forming and fabricating industry. The magazine delivers the news, technical articles, and case histories that enable fabricators to do their jobs more efficiently. The Fabricator has served the industry since 1970.
start your free subscriptionAbout the Author
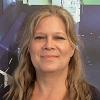
Kate Bachman
815-381-1302
Kate Bachman is a contributing editor for The FABRICATOR editor. Bachman has more than 20 years of experience as a writer and editor in the manufacturing and other industries.
- Stay connected from anywhere
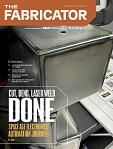
Easily access valuable industry resources now with full access to the digital edition of The Fabricator.
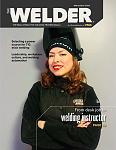
Easily access valuable industry resources now with full access to the digital edition of The Welder.
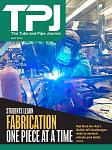
Easily access valuable industry resources now with full access to the digital edition of The Tube and Pipe Journal.
- Podcasting
- Podcast:
- The Fabricator Podcast
- Published:
- 04/16/2024
- Running Time:
- 63:29
In this episode of The Fabricator Podcast, Caleb Chamberlain, co-founder and CEO of OSH Cut, discusses his company’s...
- Trending Articles
Tips for creating sheet metal tubes with perforations
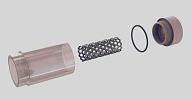
JM Steel triples capacity for solar energy projects at Pennsylvania facility
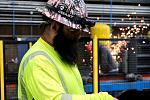
Are two heads better than one in fiber laser cutting?
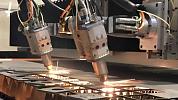
Supporting the metal fabricating industry through FMA
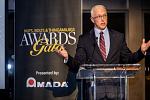
Omco Solar opens second Alabama manufacturing facility
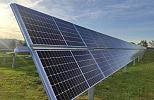
- Industry Events
16th Annual Safety Conference
- April 30 - May 1, 2024
- Elgin,
Pipe and Tube Conference
- May 21 - 22, 2024
- Omaha, NE
World-Class Roll Forming Workshop
- June 5 - 6, 2024
- Louisville, KY
Advanced Laser Application Workshop
- June 25 - 27, 2024
- Novi, MI