- FMA
- The Fabricator
- FABTECH
- Canadian Metalworking
Categories
- Additive Manufacturing
- Aluminum Welding
- Arc Welding
- Assembly and Joining
- Automation and Robotics
- Bending and Forming
- Consumables
- Cutting and Weld Prep
- Electric Vehicles
- En Español
- Finishing
- Hydroforming
- Laser Cutting
- Laser Welding
- Machining
- Manufacturing Software
- Materials Handling
- Metals/Materials
- Oxyfuel Cutting
- Plasma Cutting
- Power Tools
- Punching and Other Holemaking
- Roll Forming
- Safety
- Sawing
- Shearing
- Shop Management
- Testing and Measuring
- Tube and Pipe Fabrication
- Tube and Pipe Production
- Waterjet Cutting
Industry Directory
Webcasts
Podcasts
FAB 40
Advertise
Subscribe
Account Login
Search
Top 5 in 365—Articles about bending and press brakes
- By Vicki Bell
- April 5, 2018
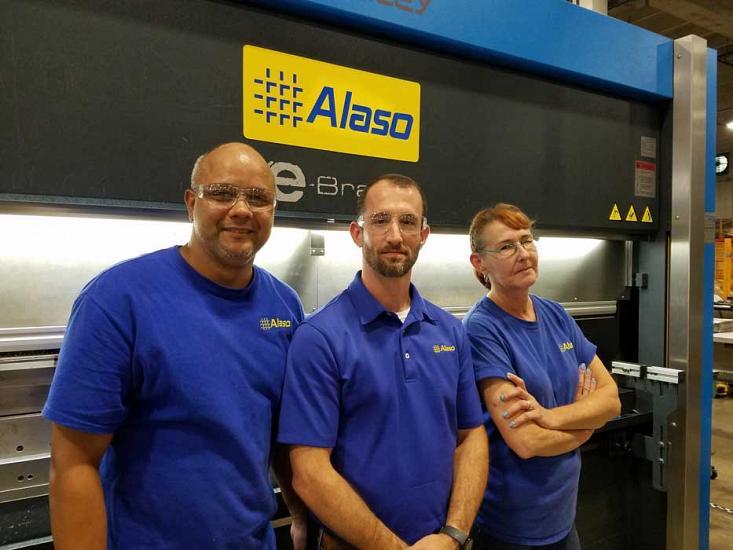
Toby Domingues, sheet metal department supervisor; Nick Millard, manufacturing manager; and Jill Mullis, press brake lead, pose in front of a 110-ton SafanDarley E-brake that has helped to boost bending productivity at Alaso, a Lakeland, Fla.-based manufacturer of commercial chicken housing systems.
Bending is among the most popular topics on thefabricator.com. In case you missed them, here are the top five most-read articles about this technology published on the site within the past year.
5. Press brake forming insights: The return flange goes deep
How to overcome the challenges of forming the deep return flange
The deep return flange: How do you define it, how is it used, and how do you form one? Part geometries like the deep return flange present forming challenges best overcome with close collaboration among the part designer, manufacturer, and press brake operator.
4. Time for new press brake tooling
How dies and punches affect the inside bend radius—Part I
The inside bend radius is at the very heart of precision metal fabrication. To achieve the radius you want, you need to understand how tooling interacts with the workpiece, but you also need to make sure your machine and tools are in good working order.
3. Press brake basics: Bending across the hem
How to apply the bend functions for a bent and hemmed part
How do you calculate the bend functions for parts that involve hems as well as bends across those hems? A hem has a specific elongation factor. Otherwise, you run the calculations and determine the bend lines as you would for any other part.
2. 5 steps to modernizing your old press brake
A right-fit retrofit may save big
A press brake is a press brake is a press brake, right? Nothing can be done to update it? Wrong! Many press brake owners find themselves in a predicament about what to do with their old press brakes. They’re caught between selling and moving the old machine and installing a new one. A cost-effective approach is to increase the productivity of an existing, properly functioning press brake by retrofitting it with features that can help reduce setup time, scrap, and operator fatigue.
1. The story behind the light curtain on the press brake
A new brake with a built-in light curtain keeps workers safe and boosts productivity at one of the world’s largest chicken housing manufacturers
Alaso, a Lakeland, Fla.-based manufacturer of commercial chicken housing systems, was looking for a way to boost bending productivity without putting press brake operators in harm's way. It found its answer with an electric press brake with a built-in light curtain. The bending technology, while off-putting at first, is now embraced by even the most veteran of brake operators.
Next up? Laser cutting.
subscribe now
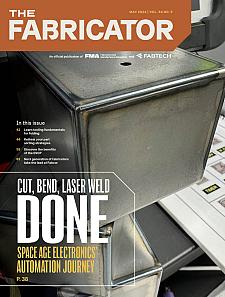
The Fabricator is North America's leading magazine for the metal forming and fabricating industry. The magazine delivers the news, technical articles, and case histories that enable fabricators to do their jobs more efficiently. The Fabricator has served the industry since 1970.
start your free subscriptionAbout the Author
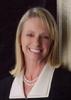
Vicki Bell
2135 Point Blvd
Elgin, IL 60123
815-227-8209
- Stay connected from anywhere
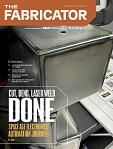
Easily access valuable industry resources now with full access to the digital edition of The Fabricator.
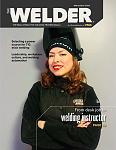
Easily access valuable industry resources now with full access to the digital edition of The Welder.
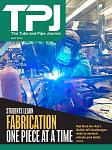
Easily access valuable industry resources now with full access to the digital edition of The Tube and Pipe Journal.
- Podcasting
- Podcast:
- The Fabricator Podcast
- Published:
- 04/16/2024
- Running Time:
- 63:29
In this episode of The Fabricator Podcast, Caleb Chamberlain, co-founder and CEO of OSH Cut, discusses his company’s...
- Trending Articles
Tips for creating sheet metal tubes with perforations
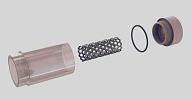
JM Steel triples capacity for solar energy projects at Pennsylvania facility
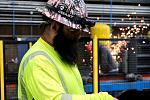
Are two heads better than one in fiber laser cutting?
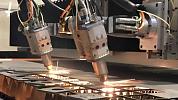
Supporting the metal fabricating industry through FMA
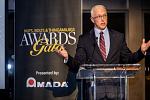
Omco Solar opens second Alabama manufacturing facility
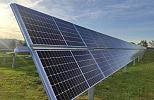
- Industry Events
16th Annual Safety Conference
- April 30 - May 1, 2024
- Elgin,
Pipe and Tube Conference
- May 21 - 22, 2024
- Omaha, NE
World-Class Roll Forming Workshop
- June 5 - 6, 2024
- Louisville, KY
Advanced Laser Application Workshop
- June 25 - 27, 2024
- Novi, MI