Contributing editor
- FMA
- The Fabricator
- FABTECH
- Canadian Metalworking
Categories
- Additive Manufacturing
- Aluminum Welding
- Arc Welding
- Assembly and Joining
- Automation and Robotics
- Bending and Forming
- Consumables
- Cutting and Weld Prep
- Electric Vehicles
- En Español
- Finishing
- Hydroforming
- Laser Cutting
- Laser Welding
- Machining
- Manufacturing Software
- Materials Handling
- Metals/Materials
- Oxyfuel Cutting
- Plasma Cutting
- Power Tools
- Punching and Other Holemaking
- Roll Forming
- Safety
- Sawing
- Shearing
- Shop Management
- Testing and Measuring
- Tube and Pipe Fabrication
- Tube and Pipe Production
- Waterjet Cutting
Industry Directory
Webcasts
Podcasts
FAB 40
Advertise
Subscribe
Account Login
Search
Tracking the supply chain disruption and opportunities for reshoring
- By Kate Bachman
- February 13, 2022
If ever a reminder were needed that manufacturing exists in an interconnected, interdependent supply chain, the 2020 (and continuing) supply chain disruption initiated by the coronavirus is that reminder.
The pandemic exposed the country’s vulnerabilities in an overreliance on foreign suppliers for medical supplies, semiconductors, construction materials, and other goods.
While most supply chains have resumed, semiconductor supplies are still constrained. The effects on manufacturing, especially in automotive, are well-documented.
Restore, Reshore, Revive
The Jan. 5 New York Times article “Supply Chain Woes Prompt a New Push to Revive U.S. Factories” stated what everyone who lost manufacturing jobs and businesses to globalization have been saying for some time now. The U.S. is too reliant on other countries’ suppliers. An overemphasis on the bottom line—both by outsourcing OEMs and by bottom-dollar consumers—put the U.S.’s self-reliance on a bottom-rung trajectory.
“Bringing manufacturing back to the United States was a major theme of former President Donald J. Trump, who imposed tariffs on imports from allies and rivals, started a trade war with China, and blocked or reworked trade agreements. Still, there was little change in the balance of trade or the inclination of companies operating in China to redirect investment to the United States,” the article noted.
Supply Chain Task Force
President Biden, too, pushed U.S. manufacturing initiatives. He signed a Made in America order his first week in office, and in July he formed a task force to focus on the disruption in U.S. supply chains, based on results of the White House report “Building Resilient Supply Chains, Revitalizing American Manufacturing, and Fostering Broad-based Growth.” The task force’s stated goal is to increase domestic manufacturing, limit shortages of critical products, and reduce dependence on global competitors. Several federal departments are working on these.
The Interior Department is working to determine where critical minerals can be produced and processed in the U.S. The Labor Department has allocated $100 million in grants for state-led apprenticeship programs to develop semi-conductors. The Energy Department will release a blueprint for developing supplies for lithium batteries and will fund $17 billion in loans to develop advanced batteries.
All well and good, but the chip shortage is complicated.
Semiconductor Shortage
The challenge to reshoring semiconductors is monumental, according to MN Gordon on Economic Prism.com. “While COVID lockdowns may have initially triggered the shortage, several decades of shortsighted decisions and simmering geopolitical tensions make it much more than a matter of fixing a few broken links in the supply chain.” He cites the consolidation of semiconductor manufacturers from 30 in 2001 to three today—Taiwan’s TSMC, South Korea’s Samsung Electronics, and the U.S.’s Intel.
“These two Asian firms, combined, control more than 70 percent of the semiconductor manufacturing market,” Gordan claims. Intel manufactures its chips, but “most other U.S.-based semiconductor companies are considered fabless – they design chips but outsource the manufacturing … to TSMC in Taiwan and Samsung Electronics in South Korea,” the article states.
Gordan maintains that because wafer fabrication requires massive capital investment, TSMC and Samsung have excelled because of supportive government policies.
The jury is still out to what degree the U.S. federal government support will do to alleviate the chip shortage.
Batteries, Chip Production in U.S.?
This disruption may have been the wakeup call needed. GM, which had to idle plants on and off because of the chip shortage, forged an agreement with GE Renewable Energy to improve supplies of rare-earth minerals and electrical steel. It also has committed to three U.S. plants to build its Ultium batteries.
Toyota recently announced plans to build a battery plant in North Carolina. Micron Technology announced plans to invest more than $150 billion in memory chip manufacturing and R&D--with some of it to be spent in the U.S. Samsung plans to build a $17 billion semiconductor plant in Texas, the New York Times article stated.
Interception Opportunities
So what can U.S. stampers do about chip shortages? Not much. But you can take advantage of the wave of sentiment for reshoring.
Ultra Tool & Manufacturing did just that (Read “Progressive stamping dies with custom substations eliminate secondary machining on deep-drawn containers,“). The company approached an OEM that had grown frustrated with supply delays from its Chinese supplier and won over three product lines by proving that it could not only fill the supplies quicker, but also less expensively.
Got thoughts?... I'd love to hear from you.
subscribe now
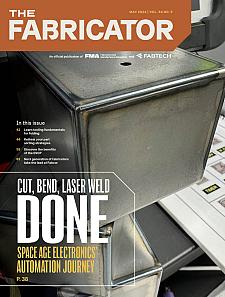
The Fabricator is North America's leading magazine for the metal forming and fabricating industry. The magazine delivers the news, technical articles, and case histories that enable fabricators to do their jobs more efficiently. The Fabricator has served the industry since 1970.
start your free subscriptionAbout the Author
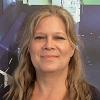
Kate Bachman
815-381-1302
Kate Bachman is a contributing editor for The FABRICATOR editor. Bachman has more than 20 years of experience as a writer and editor in the manufacturing and other industries.
- Stay connected from anywhere
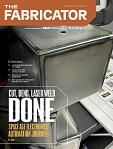
Easily access valuable industry resources now with full access to the digital edition of The Fabricator.
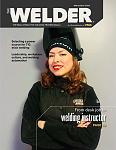
Easily access valuable industry resources now with full access to the digital edition of The Welder.
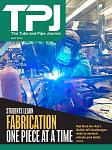
Easily access valuable industry resources now with full access to the digital edition of The Tube and Pipe Journal.
- Podcasting
- Podcast:
- The Fabricator Podcast
- Published:
- 04/16/2024
- Running Time:
- 63:29
In this episode of The Fabricator Podcast, Caleb Chamberlain, co-founder and CEO of OSH Cut, discusses his company’s...
- Trending Articles
Tips for creating sheet metal tubes with perforations
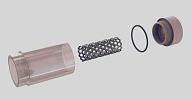
Are two heads better than one in fiber laser cutting?
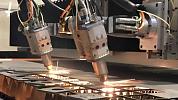
Supporting the metal fabricating industry through FMA
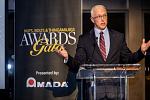
JM Steel triples capacity for solar energy projects at Pennsylvania facility
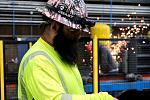
Omco Solar opens second Alabama manufacturing facility
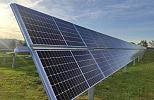
- Industry Events
16th Annual Safety Conference
- April 30 - May 1, 2024
- Elgin,
Pipe and Tube Conference
- May 21 - 22, 2024
- Omaha, NE
World-Class Roll Forming Workshop
- June 5 - 6, 2024
- Louisville, KY
Advanced Laser Application Workshop
- June 25 - 27, 2024
- Novi, MI