Contributing editor
- FMA
- The Fabricator
- FABTECH
- Canadian Metalworking
Categories
- Additive Manufacturing
- Aluminum Welding
- Arc Welding
- Assembly and Joining
- Automation and Robotics
- Bending and Forming
- Consumables
- Cutting and Weld Prep
- Electric Vehicles
- En Español
- Finishing
- Hydroforming
- Laser Cutting
- Laser Welding
- Machining
- Manufacturing Software
- Materials Handling
- Metals/Materials
- Oxyfuel Cutting
- Plasma Cutting
- Power Tools
- Punching and Other Holemaking
- Roll Forming
- Safety
- Sawing
- Shearing
- Shop Management
- Testing and Measuring
- Tube and Pipe Fabrication
- Tube and Pipe Production
- Waterjet Cutting
Industry Directory
Webcasts
Podcasts
FAB 40
Advertise
Subscribe
Account Login
Search
Notable quotes via CAR MBS 2022, Part II
EVs: New parts, new players
- By Kate Bachman
- November 16, 2022
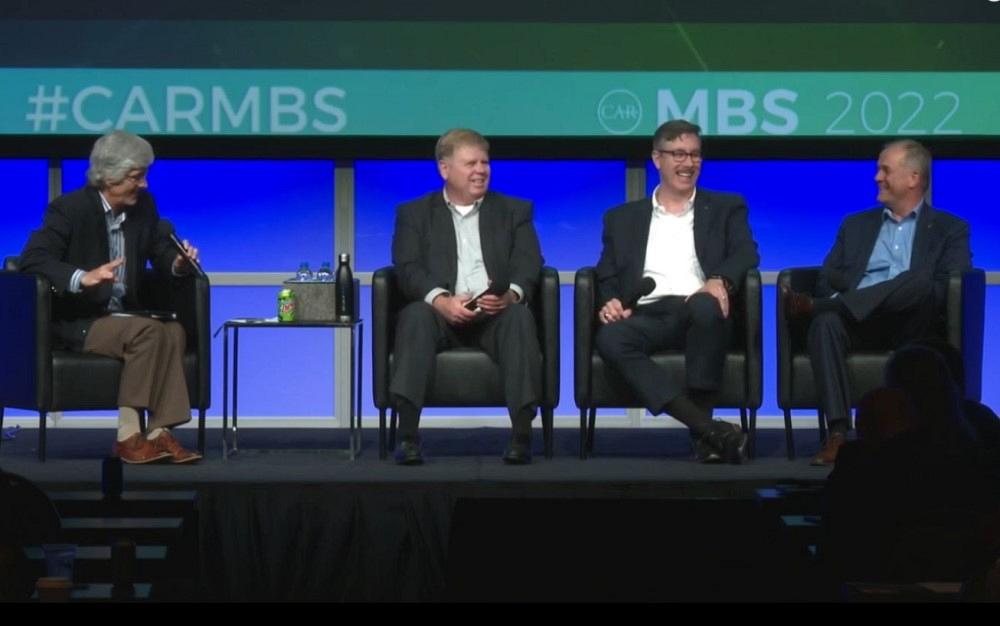
At the August Center for Automotive Research Management Briefing Seminar session, “Now That We Are All in on BEVs, Who Makes What?, Part II, weighed in how the evolution from ICE vehicles to EVs has shaken up the supply chain, considering that EVs require many different—and far fewer—components; on the importance of securing a reliable supply chain; material choices; and their own journeys to sustainability. Panelists were panelists Tim Grewe, director, electrification strategy for GM; John Warner, chief customer officer for American Battery Solutions; and Harry Husted, vice president and chief technology officer for BorgWarner.
At the Center for Automotive Research Management Briefing Seminar (CAR MBS), held in August in Traverse City, Mich., most sessions pivoted around, or intersected with, the automotive industry’s shift to vehicle electrification.
With automakers selling out their electric vehicles on reserve in a matter of hours, and the data showing battery-electric vehicles reaching 10% of the worldwide auto market in July, according to data compiled by CleanTechnica. Clearly, the auto industry is at the tipping point for the move to vehicle electrification.
“September is the first time that plug-in vehicle registrations will reach 1 million units. Worldwide, plug-in vehicle registrations jumped 61% year over year in July, totaling 778,000 units and representing the best first month of any quarter yet. Additionally, plug-ins made up 14% of the overall market share,” InsideEVs reported.
At the CAR MBS session, “Now That We Are All in on BEVs, Who Makes What?, Perspectives on Shifting Technologies, Roles, and Responsibilities – Part II, panelists weighed in how the evolution from ICE vehicles to EVs has shaken up the supply chain, considering that EVs require many different—and far fewer—components; on the importance of securing a reliable supply chain; material choices; and their own journeys to sustainability.
Panelists were Tim Grewe, director, electrification strategy, GM; Harry Husted, vice president and chief technology officer, BorgWarner; and Dr. John Warner, chief customer officer, American Battery Solutions.
STAMPING Journal brings you their words, verbatim.
Making the Transition
Tim Grewe: Awhile ago, we talked about a single EV-dedicated platform, Ultium; on how to streamline our factories; how to streamline our development, and how to pioneer innovation. Now we’re getting into the reality of transitioning the industry and the value chain … securing the supplies, scaling it, and sustaining it for the long run.
Harry Husted: BorgWarner has long been in the propulsion business, moving the vehicle, making it go down the road. We had been an engine-based, transmission-based propulsion system manufacturer. We announced an initiative about a year ago called “Charging Forward.” We declared that we’re all in on EVs from a propulsion standpoint. We’re going to shift the company revenue in a major way to be 25% EV by 2025, and 45% EV by 2030.
Our growing product portfolio covers virtually all electric propulsion areas including electric motors, battery packs, and power electronics like inverters and onboard chargers. We’re now making an electric drive module, which is the combination of a motor, an inverter, a gearset, and the surrounding auxiliaries.
"Affordability is still a problem in transforming the industry to these new vehicles. At GM, we’ve made big jump-downs in the costs, from the Bolt EV to the Hummer; a 40% reduction in the cost of the Ultium batteries … a good step. But we truly don’t know the bottom of the cost yet." --Tim Grewe, director, electrification strategy for GM
We’re making battery systems for commercial vehicles. With the acquisition of Rhombus Energy Solutions, we’re now making electric vehicle DC fast chargers in the state of Michigan, in Dearborn.
We make controllers for a variety of purposes, including battery electric vehicles, and thermal management products for electric vehicles.
So that’s the road that we’ve been on, transforming as a Tier 1.
In the Value Chain
John Warner: There are three types of battery pack manufacturers: On one end, there are the cell makers that have designed battery packs, both custom and standardized, to help get their cells into products. At the other end of the spectrum are OEMs that are trying to vertically integrate to help manage their costs. And then there are companies like us, American Battery Solutions, that are independent battery manufacturers, fitting everything else in the marketplace.
Husted: Back in 2015, we added electric motors to our portfolio. Then, with the Delphi acquisition, we added a very strong inverter portfolio. Combined with what we’ve done on gears, we’ve positioned ourselves to be able to do electric drive units. So, the thinking has been to look at sustainable mobility and getting sustainable energy all the way through to the wheels.
Where we sit today, we’ve got the electric system components and we have the intermediate piece, which is the DC fast charger that gets the energy from the grid to the vehicle.
Sourcing Decisions
Warner: We’ve got to build the supply chain. We’ve seen the legislation come through here recently that is trying to help us do that, but we’re still sitting in a position where 80% of all the lithium-ion battery materials in the world are processed in China, and 60% of them are mined there.
If we want to have energy independence, we’ve got to find a way to have more manufacturing here—and not just raw materials—the rest of the supply chain, too. If you talk to any battery company now, you’re going to be talking about lead times. We’re all looking at our supply chains and trying to get parts quicker, but some suppliers are giving me 60-week lead times right now.
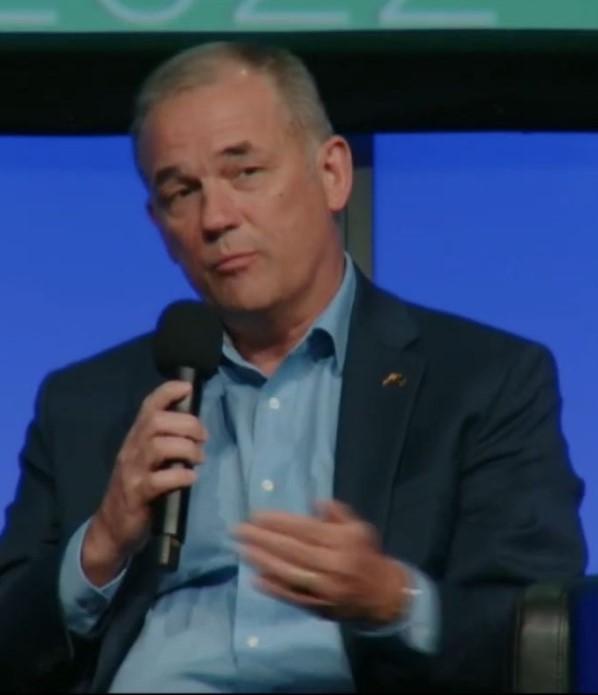
"We had been solely an engine-based, transmission-based propulsion system manufacturer. A year ago we declared that we’re all in on EVs from a propulsion standpoint. We’re going to shift the company revenue to be 25% EV by 2025, and 45% EV by 2030." --Harry Husted, vice president and chief technology officer for BorgWarner.
As a pack manufacturer, having strategic relationships with partners is really key. It’s critical to get access to those cells and for me to get product to my customers. And it’s not just cells, it’s the aluminums, it’s the contactors, it’s the BMS partners, so creating long-term strategic supply agreements with all of those is really important. Spot buys just doesn’t work in this environment anymore.
Grewe: The supplier selection is not a blind bid situation anymore, where the lowest price wins. It’s “Where is the value add?” “Do they provide an advantage all the way through?”
Scale for Cost Efficiencies
Grewe: We want to have the ability to secure and scale the battery, the raw materials, and processes to reduce cost. But we also want to allow for innovation; to fundamentally change the amount of energy it takes to process material. We’ve demonstrated a 95% material recovery from recycling. So how do you take all that investment you have when you scale, and then instead of the source being purely from the mine, being from the previous cars? You want to be ready for the next innovation without having to retool that cell factory.
Materials Selection
Grewe: A lot of material choices for the battery tray and the chassis—steel, aluminum, composites—come down to what are you are a master in. GM has incredible steel technology, incredible welding, and incredible mixed material technology. The Bolt EV has eight different kinds of steel in the battery tray. A lot of stamped structural parts are made of high-strength steel.
The Ultium is a unified body structure with pack structure combination where we can put the right material in the right place between the body and the actual pack. And so, with all that experience, and all that capability, our efficient manufacturing module lent itself to make that happen. Other OEMs don’t have that mastery–they have mastery in other areas—and choose alternative material solutions. I think we’ll stay with steel for a long, long time.
Warner: We tend to use either stamped or extruded aluminum for what we do. It really goes to setting the requirements for the application, and then backing into the material selection for their properties.
Most of the applications our batteries are going into are commercial fleet industrial applications that need robust materials. We’re adding a little more meat than what a cell-to-chassis or cell-to-packs system needs.
Husted: We use a mixture of aluminum and steel. Materials continue to be an area where we can innovate. One of our 100-kwh battery packs is over 800 lbs., so it needs a serious structural aspect to it. Structural support has to be engineered in.
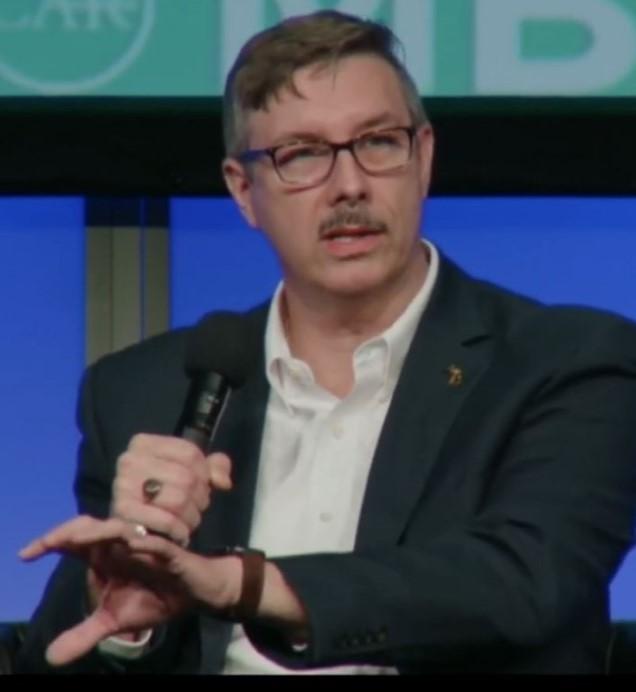
"If we want to have energy independence, we’ve got to find a way to have more manufacturing here—and not just raw materials—the rest of the supply chain, too." --John Warner, chief customer officer for American Battery Solutions
The Battery
Warner: The battery pack process … essentially, we’re buying cells, working with the cell makers, and we design and integrate those cells into scalable, modular solutions. A lot of the OEMs are moving to cell-to-pack designs … still trying to integrate those more
So, taking those cells, we do what we call modular assembly. Your design goes onto a thermal plate, making the initial electrical connections, whether welding or wire bonding the connections to the cells; you attach your BMS submodule to the cell voltage temperature mode; and then subassemble those modules into an enclosure with the thermal systems, your contacts, your BMS, and all of the things that make it run. So that’s the short process. And throughout, we do quality checks.
Grewe: You want the cell factories to run continuous operations, like newspaper presses, 24/7. The foils come in as the raw paper, the electrodes get coated onto them, and then you turn it into a cell. Part of having continuous operations is a secure and scalable supply. An interruption is very expensive. So securing that supply as demand grows means you need multiple avenues.
Husted: Battery systems for commercial vehicles, fast chargers … we’re in that business today.
Commitment to EVs, Zero Emissions
Husted: We’re all in on EVs. We’re really making a big shift in our portfolio. For years, our vision has been a clean, energy-efficient world. Our mission is to deliver innovative and sustainable mobility solutions for the vehicle market. The journey we’re taking as an automotive Tier 1 is to shift ourselves toward a sustainable mobility future with electric propulsion
Grewe: GM has been very public about its commitment to an all-electric future in pursuit of zero emissions, zero crashes, and zero congestion.
Obstacles to Adoption
Grewe: Affordability is still a problem in transforming the industry to these new vehicles. At GM, we’ve made big jump-downs in the costs, from the Bolt EV to the Hummer; a 40% reduction in the cost of the Ultium batteries … a good step; and we’re forecasting another 20%. But we truly don’t know the bottom of the cost yet.
We need to get the charging aspect figured out. We don't want customers to have to be electricians and contractors with slide rulers to charge their vehicles. On a conventional ICE vehicle trip, the average is 400 miles and two stops for 20 minutes. You want to meet them [customers] there. Make it convenient to charge. Make sure they know where a plug is open.
Warner: Skilled labor. The demand for battery engineers is really high right now. We’re having to pay higher rates. But it’s more than just that. You've got to have that purpose. A lot of people coming into the industry want to come into a company where there’s a purpose, there’s a reason for being there. It’s not just the younger generation. We all want a reason and purpose for what we do.
Husted: What we see in the workforce is that most people are eager to work in these new spaces. They want to work on the latest technology, the latest vehicles. So, they’re ready to go, but what they need is help to turn that corner into the electric propulsion space. They’re great engineers. They just don’t have the product familiarity. That’s part of the training we give them. And then, they’re pretty good at taking it from there.
That passion, that sense of purpose, it’s important. People get it, that they can impact the world around us as we move to sustainability. They can change how clean the environment’s going to be.
The Future of EVs
Grewe: In the future, the most innovative and the most affordable are going to be the winners. EVs are definitely going to have smaller batteries. We’ll take mass out of the crash zone to reduce mass; incorporate power electronics right into the passenger compartment / battery area; and get the cost down via integration with the fundamental battery technology.
Warner: Everything in the battery pack is designed to protect the battery. As these new battery chemistries develop, you'll see an evolution in battery pack design.
subscribe now
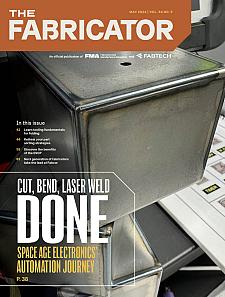
The Fabricator is North America's leading magazine for the metal forming and fabricating industry. The magazine delivers the news, technical articles, and case histories that enable fabricators to do their jobs more efficiently. The Fabricator has served the industry since 1970.
start your free subscriptionAbout the Author
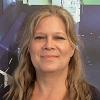
Kate Bachman
815-381-1302
Kate Bachman is a contributing editor for The FABRICATOR editor. Bachman has more than 20 years of experience as a writer and editor in the manufacturing and other industries.
- Stay connected from anywhere
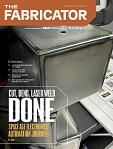
Easily access valuable industry resources now with full access to the digital edition of The Fabricator.
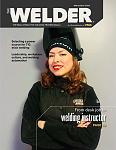
Easily access valuable industry resources now with full access to the digital edition of The Welder.
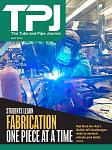
Easily access valuable industry resources now with full access to the digital edition of The Tube and Pipe Journal.
- Podcasting
- Podcast:
- The Fabricator Podcast
- Published:
- 04/16/2024
- Running Time:
- 63:29
In this episode of The Fabricator Podcast, Caleb Chamberlain, co-founder and CEO of OSH Cut, discusses his company’s...
- Trending Articles
Tips for creating sheet metal tubes with perforations
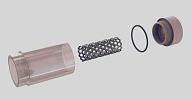
Are two heads better than one in fiber laser cutting?
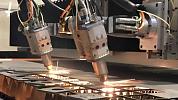
Supporting the metal fabricating industry through FMA
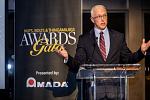
JM Steel triples capacity for solar energy projects at Pennsylvania facility
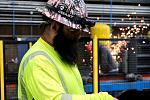
Omco Solar opens second Alabama manufacturing facility
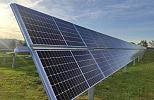
- Industry Events
16th Annual Safety Conference
- April 30 - May 1, 2024
- Elgin,
Pipe and Tube Conference
- May 21 - 22, 2024
- Omaha, NE
World-Class Roll Forming Workshop
- June 5 - 6, 2024
- Louisville, KY
Advanced Laser Application Workshop
- June 25 - 27, 2024
- Novi, MI