Contributing editor
- FMA
- The Fabricator
- FABTECH
- Canadian Metalworking
Categories
- Additive Manufacturing
- Aluminum Welding
- Arc Welding
- Assembly and Joining
- Automation and Robotics
- Bending and Forming
- Consumables
- Cutting and Weld Prep
- Electric Vehicles
- En Español
- Finishing
- Hydroforming
- Laser Cutting
- Laser Welding
- Machining
- Manufacturing Software
- Materials Handling
- Metals/Materials
- Oxyfuel Cutting
- Plasma Cutting
- Power Tools
- Punching and Other Holemaking
- Roll Forming
- Safety
- Sawing
- Shearing
- Shop Management
- Testing and Measuring
- Tube and Pipe Fabrication
- Tube and Pipe Production
- Waterjet Cutting
Industry Directory
Webcasts
Podcasts
FAB 40
Advertise
Subscribe
Account Login
Search
4 strategies from stampers on how to build a capable, dedicated, and modern workforce
Resolving the skilled tool- and diemaker shortage problem may require more than perks and apps
- By Kate Bachman
- May 29, 2019
With the U.S. unemployment rate hovering around 3.6 percent and the skilled worker shortage taking effect in plants around the country, stamping manufacturing managers are grappling with how to operate a fully functioning plant with a diminishing skilled labor force.
“A million jobs are unfulfilled,” said financial analyst Gene Marks at FMA’s Annual Meeting in March.
“Where we are going in this industry and how we are going to get there is a question we are all talking about--often with no sure answers,” a manufacturer relayed recently.
Marks offered advice on how to attract and retain millennials, including offering mobile app Hello Wallet, working-from-home options, and financial help with student debt. “This [millennial] generation wants mobility and independence and flexibility,” he said.
With traditional tool-and diemaking apprenticeship programs out of reach in many locations, some stampers have resorted to setting up in-house training programs, tasking their experienced workers with teaching their apprentices.
Several readers responded to the sincere and revealing letter from tool- and diemaker apprentice Kenny Crist published in the March/April issue, in which he relayed his experiences with that approach. They suggest that resolving the skilled worker shortage problem may require more than perks and apps.
Don’t train, teach instead
One letter writer offered two suggestions: One, appeal to the experienced personnel who are passing on their trade to remember their own early experiences and opt for being respected for their knowledge rather than resented for being difficult and grouchy.
“Second, strike the word ‘training’ from your vocabulary and replace it with ‘teaching.’ It changes the perspective,” he said. I recall a reader writing in to say, “You train animals. You teach humans.”
Respect, connect, and tolerate
A director at a midsized manufacturer wrote in to say, “[Kenny Crist] expressed some views I found to be remarkable, and I believe that many in the industry need to pay close attention.”
He said that, as a young apprentice, he made a point of connecting with the older generation and found it to be rewarding and exciting in many ways. “The ability to connect with my elders in a positive way has not always been easy, but it has enabled me to advance my career and learn and grow in this business. This is not the case for many in my age group and younger.”
He regards much of the strife as a generational disconnect, both in terms of the younger generation being thin-skinned and the older generation being intolerant: “[Younger employees] seem to be easily broken down when berated for making mistakes and unwilling to deal with the stresses of manufacturing.”
He continued, “On the other hand, seasoned tool- and diemakers expect new employees to develop skills quickly. They are impatient about teaching them something more than once.
“The divide between the older generation and the new is wide and seemingly growing wider by the year. We need to find ways to bridge this gap and create an environment that works for the younger generation.”
Stop overworking your employees
Regarding creating that environment, I have some suggestions of my own. This might sting a little.
After the economy began recovering from the Great Recession, I remember that many shops were reluctant to hire additional employees for fear that they might have to lay them off. So they began having their current staff work longer hours, then more shifts. Owners grew accustomed to being able to get more labor-hours without having to pay more health insurance and other benefits.
That line of thinking may have been understandable in 2009, but it is no longer acceptable today, in light of eight years and seven months of a growing GDP, more than 100 consecutive months of job growth, and year-over-year generous profits.
It’s time to stop overworking your employees and let them have a life. Six- and seven-day workweeks, 10- to 12-hour shifts might be OK temporarily, but not long term. Those kinds of working conditions will not coax young people to become your new, dedicated workforce.
Pay the teachers
Finally, regarding the “grouch factor,” are you requiring your experienced tool- and diemakers and other skilled workers to pass on their hard-earned tribal knowledge without proper compensation? Are they expected to teach their successors while also having to perform their daily tasks?
If so, you’d do well to follow the lead of successful stamper Weiss-Aug, which elevated venerable journeyman Paul Rettberg to teacher status. Rettberg oversees several tool- and diemaker apprentices and runs a four-year course. (Read “Have a tool- and diemaker shortage?”
Got thoughts? I'd love to hear from you. kateb@thefabricator.com
subscribe now
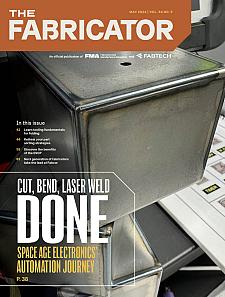
The Fabricator is North America's leading magazine for the metal forming and fabricating industry. The magazine delivers the news, technical articles, and case histories that enable fabricators to do their jobs more efficiently. The Fabricator has served the industry since 1970.
start your free subscriptionAbout the Author
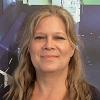
Kate Bachman
815-381-1302
Kate Bachman is a contributing editor for The FABRICATOR editor. Bachman has more than 20 years of experience as a writer and editor in the manufacturing and other industries.
- Stay connected from anywhere
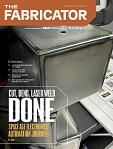
Easily access valuable industry resources now with full access to the digital edition of The Fabricator.
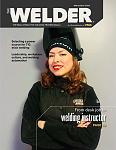
Easily access valuable industry resources now with full access to the digital edition of The Welder.
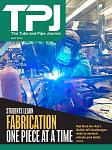
Easily access valuable industry resources now with full access to the digital edition of The Tube and Pipe Journal.
- Podcasting
- Podcast:
- The Fabricator Podcast
- Published:
- 04/16/2024
- Running Time:
- 63:29
In this episode of The Fabricator Podcast, Caleb Chamberlain, co-founder and CEO of OSH Cut, discusses his company’s...
- Trending Articles
Tips for creating sheet metal tubes with perforations
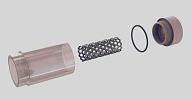
JM Steel triples capacity for solar energy projects at Pennsylvania facility
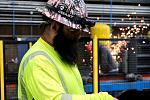
Are two heads better than one in fiber laser cutting?
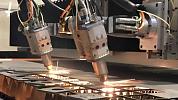
Supporting the metal fabricating industry through FMA
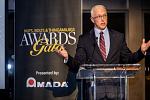
Omco Solar opens second Alabama manufacturing facility
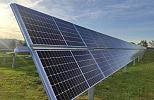
- Industry Events
16th Annual Safety Conference
- April 30 - May 1, 2024
- Elgin,
Pipe and Tube Conference
- May 21 - 22, 2024
- Omaha, NE
World-Class Roll Forming Workshop
- June 5 - 6, 2024
- Louisville, KY
Advanced Laser Application Workshop
- June 25 - 27, 2024
- Novi, MI