President
- FMA
- The Fabricator
- FABTECH
- Canadian Metalworking
Categories
- Additive Manufacturing
- Aluminum Welding
- Arc Welding
- Assembly and Joining
- Automation and Robotics
- Bending and Forming
- Consumables
- Cutting and Weld Prep
- Electric Vehicles
- En Español
- Finishing
- Hydroforming
- Laser Cutting
- Laser Welding
- Machining
- Manufacturing Software
- Materials Handling
- Metals/Materials
- Oxyfuel Cutting
- Plasma Cutting
- Power Tools
- Punching and Other Holemaking
- Roll Forming
- Safety
- Sawing
- Shearing
- Shop Management
- Testing and Measuring
- Tube and Pipe Fabrication
- Tube and Pipe Production
- Waterjet Cutting
Industry Directory
Webcasts
Podcasts
FAB 40
Advertise
Subscribe
Account Login
Search
Aluminum Workshop: Choosing aluminum alloys for welded fabrications
- By Frank Armao
- September 26, 2019
- Article
- Aluminum Welding
This Workshop isn’t the result of a specific user question. Instead, it is the result of a realization that many fabricators use 6061-T6 whenever they have a job that requires fabricating aluminum. Frankly, this is not the best solution in many cases.
We all know that 6061-T6 is readily available in most product forms and that it is fairly easy to weld once you know how. Does this mean that it is the best alloy for all applications? Not necessarily. Let’s look at what alloys are best for which applications, at least in a general sense.
First of all, it is important to remember that 6061 and all similar 6XXX alloys such as 6003, 6005, and 6082 are primarily extrusion alloys. That is because they are easy and relatively cheap to extrude. By the way, the AlZn alloy 7005 falls into this same category. They are all heat-treatable and weldable. However, they are all crack-sensitive too. This is addressed by using appropriate filler metal additions (4043 or 5356 for the 6XXX alloys, 5356 for 7005). However, all of these T6 alloys lose approximately 35 percent of the T6 properties when you weld them. Most people just accept this fact, but a few try to recover the T6 properties by postweld heat treatment.
The end result is that if the weldment you are fabricating consists of extrusions, one of the 6XXX (or 7005) alloys should be the alloy you choose. Does that make any of them the universal best choice? No.
Let’s consider a weldment that is made primarily from sheet or plate components. Is 6061-T6 the best choice for the base material? Probably not. In this case, one of the 5XXX alloys is probably better. While 6061-T6 is available as sheet or plate, a number of 5XXX alloys available in sheet and plate, such as 5052, 5154, 5454, 5086, and 5083, are better suited. They are much more ductile than the 6XXX alloys, so they will form easier.
From the weldability standpoint, 5XXX alloys are much less crack-sensitive and easier to weld than the 6XXX alloys. Also, from the standpoint of welded joint strength, they are significantly stronger. For instance, 6061-T6’s tensile strength is 40 KSI before welding, but only 24 KSI after welding. In comparison, the strength of 5083-O is 40 KSI before welding, and it is still 40 KSI after welding.
Which 5XXX alloy should you choose? That’s a subject for another Workshop. For now, it’s sufficient to say that the higher the Mg content of a 5XXX alloy, the stronger it is. With 5 percent Mg content, 5083 is one of the strongest and most readily available alloys.
What’s the end result? Use the best product form for the application. For weldments consisting primarily of extrusions, use one of the 6XXX alloys. For weldments consisting primarily of sheet or plate components, use a 5XXX alloy. For weldments consisting of a mixture of extrusions and sheet/plate, use a combination of the two.
About the Author
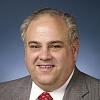
Frank Armao
Aluminum Consulting Inc.
440-479-0239
About the Publication
subscribe now
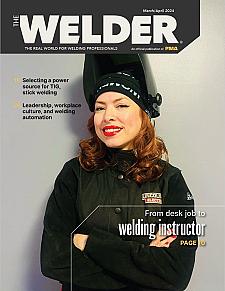
The Welder, formerly known as Practical Welding Today, is a showcase of the real people who make the products we use and work with every day. This magazine has served the welding community in North America well for more than 20 years.
start your free subscription- Stay connected from anywhere
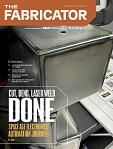
Easily access valuable industry resources now with full access to the digital edition of The Fabricator.
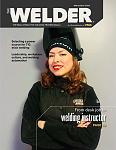
Easily access valuable industry resources now with full access to the digital edition of The Welder.
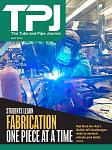
Easily access valuable industry resources now with full access to the digital edition of The Tube and Pipe Journal.
- Podcasting
- Podcast:
- The Fabricator Podcast
- Published:
- 04/16/2024
- Running Time:
- 63:29
In this episode of The Fabricator Podcast, Caleb Chamberlain, co-founder and CEO of OSH Cut, discusses his company’s...
- Trending Articles
Sheffield Forgemasters makes global leap in welding technology
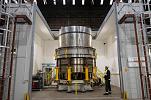
ESAB unveils Texas facility renovation
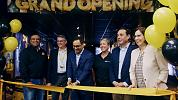
Engine-driven welding machines include integrated air compressors
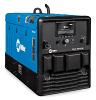
How welders can stay safe during grinding
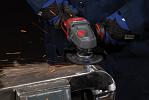
The impact of sine and square waves in aluminum AC welding, Part I
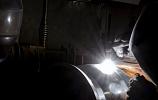
- Industry Events
16th Annual Safety Conference
- April 30 - May 1, 2024
- Elgin,
Pipe and Tube Conference
- May 21 - 22, 2024
- Omaha, NE
World-Class Roll Forming Workshop
- June 5 - 6, 2024
- Louisville, KY
Advanced Laser Application Workshop
- June 25 - 27, 2024
- Novi, MI