President
- FMA
- The Fabricator
- FABTECH
- Canadian Metalworking
Categories
- Additive Manufacturing
- Aluminum Welding
- Arc Welding
- Assembly and Joining
- Automation and Robotics
- Bending and Forming
- Consumables
- Cutting and Weld Prep
- Electric Vehicles
- En Español
- Finishing
- Hydroforming
- Laser Cutting
- Laser Welding
- Machining
- Manufacturing Software
- Materials Handling
- Metals/Materials
- Oxyfuel Cutting
- Plasma Cutting
- Power Tools
- Punching and Other Holemaking
- Roll Forming
- Safety
- Sawing
- Shearing
- Shop Management
- Testing and Measuring
- Tube and Pipe Fabrication
- Tube and Pipe Production
- Waterjet Cutting
Industry Directory
Webcasts
Podcasts
FAB 40
Advertise
Subscribe
Account Login
Search
Aluminum Workshop: Preweld cleaning - a friendly reminder
- By Frank Armao
- November 21, 2017
- Article
- Aluminum Welding
Instead of the standard question/answer format, this month I thought it might be time to review preweld cleaning, both why it’s important and which methods to employ. It is a topic that we must address periodically because it is so important in making acceptable weldments.
Adequate preweld cleaning is one of the most important actions you can take to ensure that the welds you make are of acceptable geometry and are defect-free. For instance, most people who have problems with porosity encounter it because they haven’t cleaned the weld area properly before they weld. Don’t automatically blame bad shielding gas or bad wire. While either can cause porosity, it is far more likely that the problem is lack of preweld cleaning.
Two separate aspects are key to cleaning aluminum before welding. The first is removing all oils, greases, lubricants, solvents, and other hydrocarbons from the base material in the weld area. These contaminants contain hydrogen. If they get into the welding arc, they are dissociated into hydrogen and other substances by the heat of the arc. This hydrogen causes weld porosity.
These contaminants can be removed from the weld area by one of two methods. The first, and most common, removal method is to saturate a clean, lint-free rag with a degreasing solvent and wipe down the area to be welded thoroughly. Good degreasing solvents include acetone, toluene, and MEK. If you don’t have access to these, carburetor cleaner or liquid-penetrant cleaner works well also. Do not use any sort of alcohol as a preweld cleaner as it simply spreads the contaminants around.
The second common degreasing method you can use is immersing or power washing the parts in a mild alkaline solution. This is a common practice in high-volume applications, such as automotive parts, but it is not commonly done in fabricating industries.
The second important step in preweld cleaning is to remove any oxides from the weldable surfaces. You can do this by hand using a clean stainless steel wire brush or by using a powered stainless steel brush. Be sure the brush is relatively soft (i.e., fine bristles) and use it with a light touch. Applying excessive pressure on the brush will actually burnish the oxide and drive it into the surface of the soft aluminum.
If you follow these simple practices, you should see an improvement in your weld quality.
About the Author
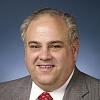
Frank Armao
Aluminum Consulting Inc.
440-479-0239
About the Publication
Related Companies
subscribe now
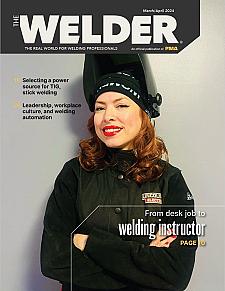
The Welder, formerly known as Practical Welding Today, is a showcase of the real people who make the products we use and work with every day. This magazine has served the welding community in North America well for more than 20 years.
start your free subscription- Stay connected from anywhere
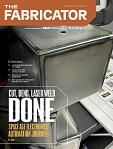
Easily access valuable industry resources now with full access to the digital edition of The Fabricator.
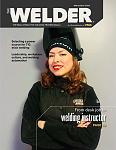
Easily access valuable industry resources now with full access to the digital edition of The Welder.
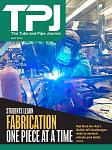
Easily access valuable industry resources now with full access to the digital edition of The Tube and Pipe Journal.
- Podcasting
- Podcast:
- The Fabricator Podcast
- Published:
- 04/16/2024
- Running Time:
- 63:29
In this episode of The Fabricator Podcast, Caleb Chamberlain, co-founder and CEO of OSH Cut, discusses his company’s...
- Trending Articles
Sheffield Forgemasters makes global leap in welding technology
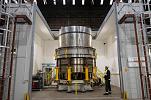
ESAB unveils Texas facility renovation
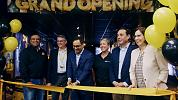
Engine-driven welding machines include integrated air compressors
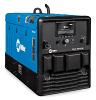
How welders can stay safe during grinding
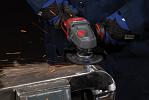
The impact of sine and square waves in aluminum AC welding, Part I
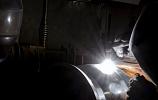
- Industry Events
16th Annual Safety Conference
- April 30 - May 1, 2024
- Elgin,
Pipe and Tube Conference
- May 21 - 22, 2024
- Omaha, NE
World-Class Roll Forming Workshop
- June 5 - 6, 2024
- Louisville, KY
Advanced Laser Application Workshop
- June 25 - 27, 2024
- Novi, MI