President
- FMA
- The Fabricator
- FABTECH
- Canadian Metalworking
Categories
- Additive Manufacturing
- Aluminum Welding
- Arc Welding
- Assembly and Joining
- Automation and Robotics
- Bending and Forming
- Consumables
- Cutting and Weld Prep
- Electric Vehicles
- En Español
- Finishing
- Hydroforming
- Laser Cutting
- Laser Welding
- Machining
- Manufacturing Software
- Materials Handling
- Metals/Materials
- Oxyfuel Cutting
- Plasma Cutting
- Power Tools
- Punching and Other Holemaking
- Roll Forming
- Safety
- Sawing
- Shearing
- Shop Management
- Testing and Measuring
- Tube and Pipe Fabrication
- Tube and Pipe Production
- Waterjet Cutting
Industry Directory
Webcasts
Podcasts
FAB 40
Advertise
Subscribe
Account Login
Search
Aluminum Workshop: Stress corrosion cracking in aluminum
3 tips to avoid using unsuitable filler metal, base material, and environmental conditions
- By Frank Armao
- Updated August 7, 2023
- July 1, 2020
- Article
- Aluminum Welding
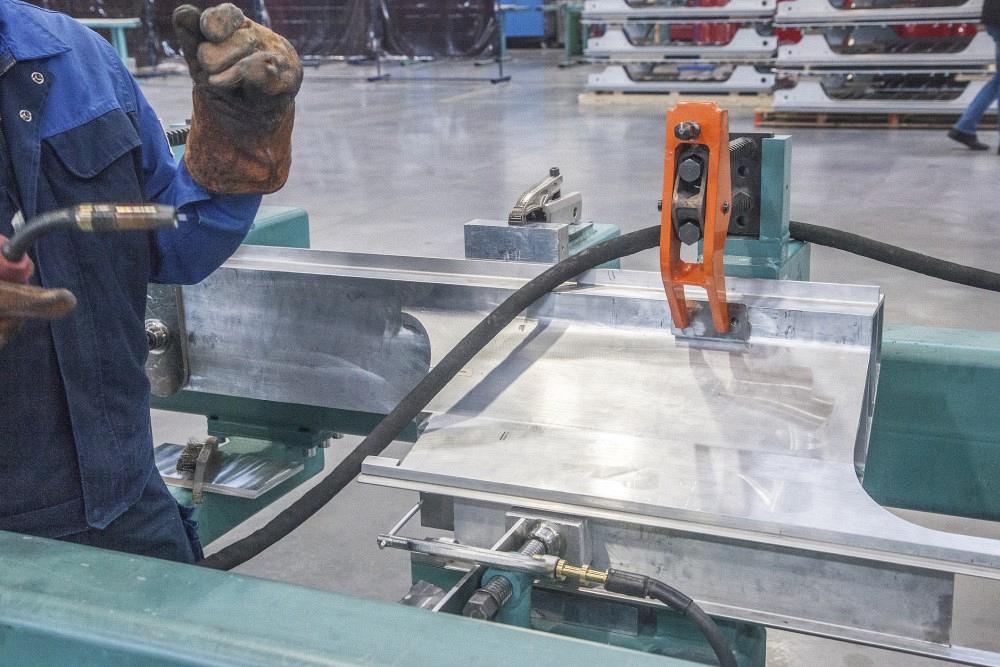
Most welders are familiar with the phenomenon called stress corrosion cracking (SCC). It occurs when the wrong filler metal or base material is combined with unsuitable environmental conditions. Getty Images
In this installment we will take a break from welding processes for fabricating aluminum and instead focus on how the filler metal and base metal are affected by welding and how cracking problems can sometimes occur.
Most people are familiar with the phenomenon called stress corrosion cracking (SCC). It occurs when the wrong filler metal or base material is combined with unsuitable environmental conditions.
It is well-known that any Al alloy containing more than 3% Mg is subject to SCC. This includes most of the 5XXX alloys, such as 5083 and 5086, which are sheet and plate alloys. However, you must remember that almost all of the common Al 5XXX filler alloys, such as 5356, 5183, and 5556, also contain more than 3% Mg. Any of them can be susceptible to SCC under certain conditions, regardless of which Al alloy is used to weld.
However, the sensitivity to SCC depends largely on four factors:
- The alloy must contain at least 3% Mg.
- A stress must be present (the residual stresses around welds are almost always high enough to satisfy this requirement).
- An electrolyte, such as salt water, must be present.
- At some point the weld must have been exposed to service temperatures above 150 degrees F for a significant amount of time (hundreds of hours).
Keep in mind that all four of these conditions do not need to happen simultaneously. Once a weld is exposed to high service temperatures, a sensitive microstructure will have formed. Even if the service temperature is lowered, the presence of factors 2 and 3 will be enough to cause SCC.
What does an SCC look like? It is usually a jagged crack down the center of the weld, and it can be short or long depending on the stress level. In fact, I have seen SCCs that were 24 in. long.
Tips for Stress Corrosion Cracking
Here are three tips to avoid an SCC:
- Do not use the filler metals with higher Mg content referenced earlier if the service temperature is above 150 degrees F. This is true even if you are using a base metal which is not subject to SCC, such as the 6XXX alloys like 6061. The weld could still crack.
- If you must use a 5XXX filler at higher service temperature, use specialty filler metals such as 5554 that contain less than 3% Mg and are not subject to SCC. However, they are not as strong as the higher-Mg fillers like 5356.
- In general, if you are welding 6XXX alloys like 6061 for higher-temperature service, 4043 is usually the best choice.
As a closing thought, never use high-Mg base materials such as 5083 at service temperatures above 150 degrees F regardless of whether or not they are welded.
About the Author
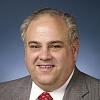
Frank Armao
Aluminum Consulting Inc.
440-479-0239
About the Publication
subscribe now
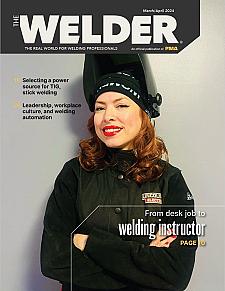
The Welder, formerly known as Practical Welding Today, is a showcase of the real people who make the products we use and work with every day. This magazine has served the welding community in North America well for more than 20 years.
start your free subscription- Stay connected from anywhere
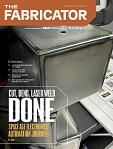
Easily access valuable industry resources now with full access to the digital edition of The Fabricator.
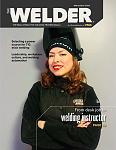
Easily access valuable industry resources now with full access to the digital edition of The Welder.
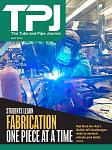
Easily access valuable industry resources now with full access to the digital edition of The Tube and Pipe Journal.
- Podcasting
- Podcast:
- The Fabricator Podcast
- Published:
- 04/16/2024
- Running Time:
- 63:29
In this episode of The Fabricator Podcast, Caleb Chamberlain, co-founder and CEO of OSH Cut, discusses his company’s...
- Trending Articles
Sheffield Forgemasters makes global leap in welding technology
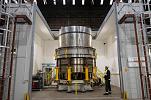
ESAB unveils Texas facility renovation
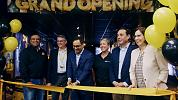
Engine-driven welding machines include integrated air compressors
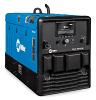
How welders can stay safe during grinding
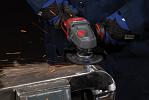
The impact of sine and square waves in aluminum AC welding, Part I
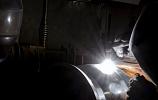
- Industry Events
16th Annual Safety Conference
- April 30 - May 1, 2024
- Elgin,
Pipe and Tube Conference
- May 21 - 22, 2024
- Omaha, NE
World-Class Roll Forming Workshop
- June 5 - 6, 2024
- Louisville, KY
Advanced Laser Application Workshop
- June 25 - 27, 2024
- Novi, MI