Independent welding consumables professional
- FMA
- The Fabricator
- FABTECH
- Canadian Metalworking
Categories
- Additive Manufacturing
- Aluminum Welding
- Arc Welding
- Assembly and Joining
- Automation and Robotics
- Bending and Forming
- Consumables
- Cutting and Weld Prep
- Electric Vehicles
- En Español
- Finishing
- Hydroforming
- Laser Cutting
- Laser Welding
- Machining
- Manufacturing Software
- Materials Handling
- Metals/Materials
- Oxyfuel Cutting
- Plasma Cutting
- Power Tools
- Punching and Other Holemaking
- Roll Forming
- Safety
- Sawing
- Shearing
- Shop Management
- Testing and Measuring
- Tube and Pipe Fabrication
- Tube and Pipe Production
- Waterjet Cutting
Industry Directory
Webcasts
Podcasts
FAB 40
Advertise
Subscribe
Account Login
Search
Consumables Corner: Comparing filler metals for manual and robotic welding applications
- By Nino Mascalco, Rob Koltz, and Steve Sigler
- November 24, 2017
- Article
- Consumables
Q: Our job shop manufactures various products; some parts we weld manually or robotically on a jig, others we custom-build and weld manually. We currently use gas metal arc welding (GMAW) to assemble all of our parts. Which is the best welding process or wire type for all variations of welding we do? How much of an effect does the wire or process have on overall speed and efficiency?
A: With several options to choose from, what you will find is that you might require more than one process for the variety of work you are performing.
Depending on the condition of the steel and manufacturing tolerances that you must maintain, specialty processes such as laser hybrid welding might work for the robotic applications, but it will depend on the GMAW process. Additionally, you might want to consider submerged arc welding (SAW) for certain automated applications or for the custom-build work you do, but we’d need more information about specific products and weld joints to know for sure if that is a viable option.
In most cases it will come down to one of three wire types—solid, metal-core, and flux-core. All three wires can work with a range of shielding gases depending on the application and desired performance.
Argon and carbon dioxide blends are the most common. The more argon in the blend, the more expensive it is. But on the plus side, a high-argon blend achieves better mechanical performance, generates less fumes, and typically appeals more to operators. Carbon dioxide, a less expensive gas, will provide the broadest penetration profile, provide the best cleaning action but slightly lower mechanical test results, and generate more welding fume.
For a solid-wire or GMAW process, the classification and shielding gas will have the most significant impact on performance. In most applications, base materials have a light layer of mill scale, light rust, or pickling oil which, if not removed before welding, can affect welding performance. In this case, it is ideal to use an ER70S-6 wire with a 90 percent argon/10 percent carbon dioxide blend shielding gas. The electrode’s deoxidizers combined with the 10 percent carbon dioxide should provide adequate cleaning action and produce a weld with a good appearance, penetration, and smooth toe transitions. If you are welding on higher-strength steels, be sure you match the appropriate filler metal to the lowest-strength base material for that specific application.
Metal-cored wires are another option for flat or horizontal weld applications. These wires run very similar to solid wires except they do not run in the short-circuiting mode and cannot be welded vertical-up or overhead unless you have a machine capable of pulsed welding. Also, because of the higher current density of the wire, the melt-off rate is greater and results in poor performance in vertical-down welding positions. You would likely need to have another process for those applications.
Flux-cored wires can provide a one-wire solution but may not be the most economical for your situation. These wires can be used in most applications, but they produce lower deposition efficiencies and generate more fumes, which may not be desirable based on your shop's ventilation system.
Now let's compare speed and efficiency. Choosing a solid wire versus a metal-cored wire versus a flux-cored wire can have a significant impact on speed and efficiency. Metal-cored and flux-cored wires have a higher current density compared to solid wire of the same diameter. This means you can increase the wire feed speed (WFS) for the metal-cored or flux-cored wire while maintaining the same heat input as the solid wire.
Compared to solid wire, metal-cored wires allow for faster travel speeds and deposition rates at similar voltage and amperage since they both have efficiencies in the 92 to 99 percent range. However, cored wires have more manufacturing steps involved to produce them, which adds to the cost so the pay back may not be there depending upon your situation.
Flux-cored wires typically have an efficiency of around 86 percent because of the nonweld metal slag that has to be removed after each weld pass. The deposition rate will be lower based on its efficiency and the time it takes for the operator to remove slag. For this reason, flux-core wires are not typically used in robotic applications.
To answer your original question, there may not be one wire or process solution for your shop. If a majority of the steel is relatively clean, then staying with your current GMAW process is probably your best bet. If you are not already doing so, using two wire diameters may provide you the best optimization of applications.
About the Authors
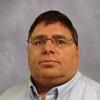
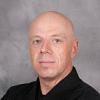
Rob Koltz
Application Engineer
411 S. Ebenezer Rd.
Florence, 29501
636-485-2253
Steve Sigler
Application Engineer
411 S. Ebenezer Rd.
Florence, South Carolina 29501
636-485-2253
About the Publication
Related Companies
subscribe now
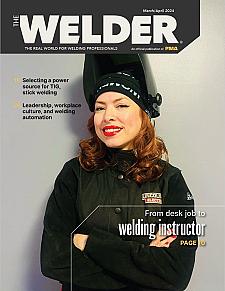
The Welder, formerly known as Practical Welding Today, is a showcase of the real people who make the products we use and work with every day. This magazine has served the welding community in North America well for more than 20 years.
start your free subscription- Stay connected from anywhere
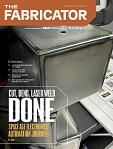
Easily access valuable industry resources now with full access to the digital edition of The Fabricator.
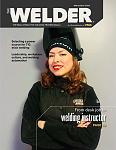
Easily access valuable industry resources now with full access to the digital edition of The Welder.
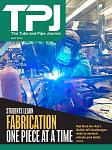
Easily access valuable industry resources now with full access to the digital edition of The Tube and Pipe Journal.
- Podcasting
- Podcast:
- The Fabricator Podcast
- Published:
- 04/16/2024
- Running Time:
- 63:29
In this episode of The Fabricator Podcast, Caleb Chamberlain, co-founder and CEO of OSH Cut, discusses his company’s...
- Trending Articles
Sheffield Forgemasters makes global leap in welding technology
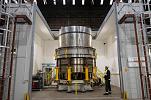
ESAB unveils Texas facility renovation
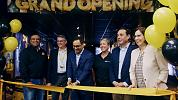
Engine-driven welding machines include integrated air compressors
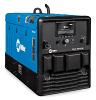
How welders can stay safe during grinding
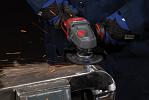
The impact of sine and square waves in aluminum AC welding, Part I
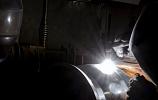
- Industry Events
16th Annual Safety Conference
- April 30 - May 1, 2024
- Elgin,
Pipe and Tube Conference
- May 21 - 22, 2024
- Omaha, NE
World-Class Roll Forming Workshop
- June 5 - 6, 2024
- Louisville, KY
Advanced Laser Application Workshop
- June 25 - 27, 2024
- Novi, MI