Independent welding consumables professional
- FMA
- The Fabricator
- FABTECH
- Canadian Metalworking
Categories
- Additive Manufacturing
- Aluminum Welding
- Arc Welding
- Assembly and Joining
- Automation and Robotics
- Bending and Forming
- Consumables
- Cutting and Weld Prep
- Electric Vehicles
- En Español
- Finishing
- Hydroforming
- Laser Cutting
- Laser Welding
- Machining
- Manufacturing Software
- Materials Handling
- Metals/Materials
- Oxyfuel Cutting
- Plasma Cutting
- Power Tools
- Punching and Other Holemaking
- Roll Forming
- Safety
- Sawing
- Shearing
- Shop Management
- Testing and Measuring
- Tube and Pipe Fabrication
- Tube and Pipe Production
- Waterjet Cutting
Industry Directory
Webcasts
Podcasts
FAB 40
Advertise
Subscribe
Account Login
Search
Consumables Corner: Discovering the cause of lack of fusion in PJP joints
- By Nino Mascalco, Rob Koltz, and Steve Sigler
- November 16, 2015
- Article
- Consumables
Q: We manufacture various products for the agriculture and transportation industries. A majority of our products are made from 6061 and 5652 aluminum and are joined with gas metal arc welding (GMAW-S) using a 5356 filler metal and 100 percent argon shielding gas. Most of the joints are partial joint penetration (PJP) corner, lap, or T-joints, and we've always had problems with welds breaking on some of the tee-joints. When we inspect the failures, the problems seem to be caused by lack of fusion (LOF) at the root of the weld. How can we correct this?
A: You can take a few basic steps that might resolve this problem, but based on the information you provided, we need to make some assumptions.
Aluminum welding is a rather detailed process initially. Choice of base materials and weld filler metals for in-service conditions, such as overall strength and ductility, elevated or cryogenic temperatures, color matching, postweld heat-treatment, and manufacturability, plays a significant role. We'll assume you closely considered all of these variables when you selected the base material and filler metals. In other words, we're assuming nothing is going on from a chemical or metallurgical standpoint and that you are certain the failure is from LOF at the root of the weld.
Two variables might be contributing to the LOF. The 5356 filler metal is a high-strength wire that provides good feedability during welding and yields a strong weld joint. However, the negative effect is the weld puddle doesn't flow or wet out as well. You may be able to substitute a 4043 filler metal for the 5356 with your engineering department’s approval. Keep in mind, it is a softer wire so you may run into some feeding issues.
The other variable is the 100 percent argon shielding gas. Overall, argon provides the most robust welding conditions and desired postweld results. You can add 50 to 80 percent helium in some applications to balance the argon. This change usually increases welding speed, which may justify the initial cost of the helium. The other potential side benefit from helium is that it might increase the puddle fluidity, which may allow the weld puddle to flow better at the root of the weld joint and improve penetration. It's possible that a combination of the 4043 filler metal along with an addition of helium may alleviate your LOF issues.
For welding process considerations, here are some things to verify. Make sure the welding equipment is calibrated at least annually; inspect all cables/leads and hoses; and check the welding gun condition and shielding gas flow rates at the nozzle. Be sure to practice good technique such as a proper work and lead angles and keep the welding arc on the leading edge of the weld puddle. During welding itself, make sure the work lead is securely fastened to the workpiece. In many cases, a work lead in poor condition or with a poor connection to the workpiece causes an erratic arc that may prevent proper welding arc focus at the joint.
Last, be sure the base material is clean and free of contaminants before tack welding them together. This is commonly overlooked and can lead to problems.
Aluminum has good corrosion resistance because of the oxide layer it forms instantly when exposed to the atmosphere. This oxide layer also adds to the difficulty of welding, and the longer the base material is sitting around, the thicker that layer becomes. You can remove or reduce the thickness of the oxide layer before you weld using a file, wire brush, or grinding tool, which will also improve weld joint penetration and fusion at the root.
A simple and inexpensive way to test any of these options is to perform a standard T-joint break test.
About the Authors
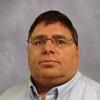
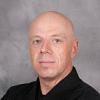
Rob Koltz
Application Engineer
411 S. Ebenezer Rd.
Florence, 29501
636-485-2253
Steve Sigler
Application Engineer
411 S. Ebenezer Rd.
Florence, South Carolina 29501
636-485-2253
About the Publication
Related Companies
subscribe now
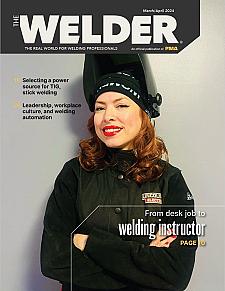
The Welder, formerly known as Practical Welding Today, is a showcase of the real people who make the products we use and work with every day. This magazine has served the welding community in North America well for more than 20 years.
start your free subscription- Stay connected from anywhere
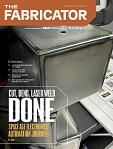
Easily access valuable industry resources now with full access to the digital edition of The Fabricator.
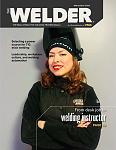
Easily access valuable industry resources now with full access to the digital edition of The Welder.
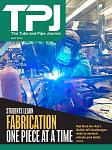
Easily access valuable industry resources now with full access to the digital edition of The Tube and Pipe Journal.
- Podcasting
- Podcast:
- The Fabricator Podcast
- Published:
- 04/16/2024
- Running Time:
- 63:29
In this episode of The Fabricator Podcast, Caleb Chamberlain, co-founder and CEO of OSH Cut, discusses his company’s...
- Trending Articles
Sheffield Forgemasters makes global leap in welding technology
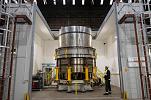
ESAB unveils Texas facility renovation
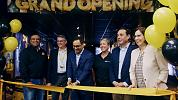
Engine-driven welding machines include integrated air compressors
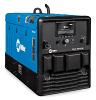
How welders can stay safe during grinding
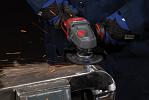
The impact of sine and square waves in aluminum AC welding, Part I
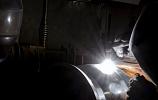
- Industry Events
16th Annual Safety Conference
- April 30 - May 1, 2024
- Elgin,
Pipe and Tube Conference
- May 21 - 22, 2024
- Omaha, NE
World-Class Roll Forming Workshop
- June 5 - 6, 2024
- Louisville, KY
Advanced Laser Application Workshop
- June 25 - 27, 2024
- Novi, MI