Independent welding consumables professional
- FMA
- The Fabricator
- FABTECH
- Canadian Metalworking
Categories
- Additive Manufacturing
- Aluminum Welding
- Arc Welding
- Assembly and Joining
- Automation and Robotics
- Bending and Forming
- Consumables
- Cutting and Weld Prep
- Electric Vehicles
- En Español
- Finishing
- Hydroforming
- Laser Cutting
- Laser Welding
- Machining
- Manufacturing Software
- Materials Handling
- Metals/Materials
- Oxyfuel Cutting
- Plasma Cutting
- Power Tools
- Punching and Other Holemaking
- Roll Forming
- Safety
- Sawing
- Shearing
- Shop Management
- Testing and Measuring
- Tube and Pipe Fabrication
- Tube and Pipe Production
- Waterjet Cutting
Industry Directory
Webcasts
Podcasts
FAB 40
Advertise
Subscribe
Account Login
Search
Consumables Corner: Heat input and its effects on material properties
- By Nino Mascalco, Rob Koltz, and Steve Sigler
- January 29, 2018
- Article
- Consumables
Q: How does heat input from welding affect the mechanical performance of welded joints? Do preheat and interpass temperature have any effect on them as well?
A: For many applications that involve thin plain carbon steel such as A36 or similar grades, these variables have minimal effect on the final welded joint. The variables become much more important when you are welding higher-strength or alloyed base materials, so we will focus on those applications.
To produce high-strength materials with good toughness properties, there are two types of material that have different mechanisms used in their manufacture: high-strength, low-alloy (HSLA) and thermo-mechanically controlled processed (TMCP) steel.
HSLA steel is produced by micro alloying, which is adding small amounts of alloy such as manganese, molybdenum, chromium, and nickel along with niobium, titanium, and vanadium.
TMCP is produced through carefully controlled temperatures and rolling pressures during steel production. In some cases, both methods are used to produce high-strength, quality steel with good toughness properties.
To answer your original question, welding heat input calculation is defined by voltage, amperage, and travel speed, and it is generally expressed as kilojoules per linear inch of weld (kJ/in.).
The general heat input range recommended for welding various types of carbon steel and specialty alloys is 30 to 70 kJ/in. However, not all materials are bound by that range.
Heat input from welding can have a serious effect on the mechanical toughness properties of the base material in the heat-affected zone (HAZ) and the weld metal itself. As a rule of thumb, the higher the strength and/or corrosion resistance of the base material, the higher level of precaution should be taken during welding.
In most cases, problems arise when the heat input is too low or too high. Heat input that is too high, either through excessive voltage, excessive amperage, or slow travel speed, can slow your cooling rate, resulting in excessive grain growth. This excessive grain growth shows up in changed mechanical properties, mainly a decrease in the material’s cold weather toughness.
Using incorrect welding parameters such as excessive voltage can cause small amounts of alloy to be lost in the arc, directly reducing the effective mechanical properties of the welded joint. This is also true with stainless steel, the result being degradation in corrosion resistance. For stainless steel, restricting heat input to 50 kJ/in. or less should prevent this from happening.
Slow travel speed usually occurs when you attempt to fill a large joint with only a few weld passes. This raises the heat input drastically. The solidification rate of the weld pool occurs at a slower rate, promoting grain growth in the weld metal and HAZ. Large grain size tends to produce a weaker microstructure but is largely dependent on filler metal and base metal chemistry, percentage of dilution, and peak temperatures.
Some HSLA steels have trace amounts of other elements added that act as grain refiners, such as boron or titanium, and can maintain good mechanical properties with acceptable weld heat input as high as 115 kJ/in.
For welding on TMCP or quench and tempered (Q&T) steels such as A514, limiting heat input and carefully controlling maximum interpass temperatures are critical to maintain the parent metal properties. Steel that gains better mechanical properties from the Q&T process are much more likely to lose these gains in strength and toughness if those values are excessive. Preheat and maximum interpass temperatures will be determined by material thickness, but the heat input should be limited to no more than 60 kJ/in.
Excessive travel speed with low welding parameters can produce heat input values that are too low. Issues arise if this happens because of rapid solidification of the weld bead. The resulting weld can have a very unrefined grain structure and produce a weld deposit with excessive yield and tensile strength values that overmatch the base material. To prevent this from happening, maintain a heat input value greater than 20 kJ/in.
Preheating is done for two primary reasons. First is the desire to slow the cooling rate of the weld metal and HAZ to prevent undesirable microstructures from forming, such as martensite. Second is to drive off condensate, which is found on the material’s surface, from ending up in the weld joint and causing porosity or increasing the potential for hydrogen cracking. Preheating can also assist in reducing the amount of residual stresses in the weld metal and weld joint. In some applications this can eliminate the need for postweld heat treat (PWHT).
Controlling interpass temperature is important because it ensures that the weld’s cooling rate will be fast enough to deliver the required mechanical properties. For example, A514 interpass temperature should be kept under 400 degrees F, while NiCrMo steel such as 4340 can be as high as 650 degrees F. Keeping in mind these values are thickness-dependent.
To gain a better understanding of the metallurgy that determines the various possible outcomes, getting familiar with time-temperature-transformation diagrams or continuous-cooling-transformation diagrams will provide a good visual for the phase changes occurring in the weld metal and HAZ.
About the Authors
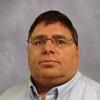
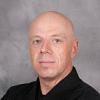
Rob Koltz
Application Engineer
411 S. Ebenezer Rd.
Florence, 29501
636-485-2253
Steve Sigler
Application Engineer
411 S. Ebenezer Rd.
Florence, South Carolina 29501
636-485-2253
About the Publication
Related Companies
subscribe now
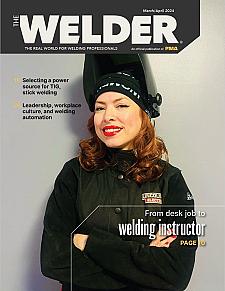
The Welder, formerly known as Practical Welding Today, is a showcase of the real people who make the products we use and work with every day. This magazine has served the welding community in North America well for more than 20 years.
start your free subscription- Stay connected from anywhere
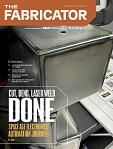
Easily access valuable industry resources now with full access to the digital edition of The Fabricator.
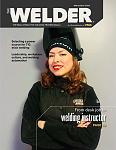
Easily access valuable industry resources now with full access to the digital edition of The Welder.
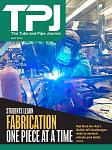
Easily access valuable industry resources now with full access to the digital edition of The Tube and Pipe Journal.
- Podcasting
- Podcast:
- The Fabricator Podcast
- Published:
- 04/16/2024
- Running Time:
- 63:29
In this episode of The Fabricator Podcast, Caleb Chamberlain, co-founder and CEO of OSH Cut, discusses his company’s...
- Trending Articles
Sheffield Forgemasters makes global leap in welding technology
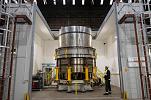
ESAB unveils Texas facility renovation
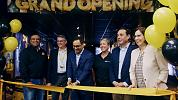
Engine-driven welding machines include integrated air compressors
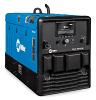
How welders can stay safe during grinding
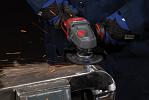
The impact of sine and square waves in aluminum AC welding, Part I
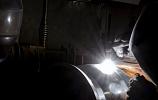
- Industry Events
16th Annual Safety Conference
- April 30 - May 1, 2024
- Elgin,
Pipe and Tube Conference
- May 21 - 22, 2024
- Omaha, NE
World-Class Roll Forming Workshop
- June 5 - 6, 2024
- Louisville, KY
Advanced Laser Application Workshop
- June 25 - 27, 2024
- Novi, MI