Independent welding consumables professional
- FMA
- The Fabricator
- FABTECH
- Canadian Metalworking
Categories
- Additive Manufacturing
- Aluminum Welding
- Arc Welding
- Assembly and Joining
- Automation and Robotics
- Bending and Forming
- Consumables
- Cutting and Weld Prep
- Electric Vehicles
- En Español
- Finishing
- Hydroforming
- Laser Cutting
- Laser Welding
- Machining
- Manufacturing Software
- Materials Handling
- Metals/Materials
- Oxyfuel Cutting
- Plasma Cutting
- Power Tools
- Punching and Other Holemaking
- Roll Forming
- Safety
- Sawing
- Shearing
- Shop Management
- Testing and Measuring
- Tube and Pipe Fabrication
- Tube and Pipe Production
- Waterjet Cutting
Industry Directory
Webcasts
Podcasts
FAB 40
Advertise
Subscribe
Account Login
Search
Consumables Corner: Tips for welding thin materials
- By Nino Mascalco, Rob Koltz, and Steve Sigler
- March 15, 2018
- Article
- Consumables
Q: We're an independent welding supply and distributor company. We frequently field an array of questions from our broad customer base. While we have straightforward answers for most questions, we seem to have difficulty finding common ground on the topic of welding thin materials. What are some best practices for welding thin materials that we can share with our customers?
A: Thin material manufacturing is a large part of industry in the U.S. This includes various shapes of tubing, angles, and flat sheets, typically 24 gauge up to about 3/16-inch thick and usually manufactured from stainless steel, carbon steel, galvanized, or aluminum.To determine the best welding process, shielding gas, and electrode to use, start by reviewing the application. What is the base material type, thickness, condition or cleanliness, welding position, available welding equipment, and welder skill? Keep in mind the need for proper personal protective equipment, which is very important when welding stainless or galvanized steels.
When welding thin material, the goal is to minimize distortion and spatter, prevent burnthrough, and produce a sound weld with adequate fusion.
For plain carbon steel applications, you have many options. For the thinnest material up to about 14 ga., try using the gas metal arc welding (GMAW) process in short-circuiting transfer (SCT) mode with a 0.023-in.-diameter E70-S2, S3, or S6 classification filler metal and 75 percent argon/25 percent CO2 shielding gas. On 14-ga. through 3/16-in. material, consider using a 0.030-in.-dia. filler metal.
Another potential option is to use pulsed GMAW with a high argon-content shielding gas, such as 95 percent argon/5 percent CO2 or argon/oxygen. Equipment capable of performing pulsed GMAW is generally more expensive but provides highly appealing benefits. Pulsed welding allows for increased control over the welding arc, offers a wide range of operating parameters, and generates low spatter.
When welding in SCT mode, you should use either a slight drag or a neutral gun angle relative to the direction of travel, which should produce a low amount of spatter. For pulsed welding, push or drag the weld puddle to determine which produces the best bead appearance. Please note that you shouldn’t back-step into the puddle, as this negates the pulse feature.
Flux-cored arc welding (FCAW) is another option, although it is not ideal because it produces a protective slag layer that needs to be removed after welding. It has lower deposition efficiency rates compared to GMAW and produces greater levels of smoke and weld spatter. Again, using a small-diameter electrode will help keep the heat input down. This process is most beneficial for job-site welding, where you can use a self-shielded, flux-cored wire. No external shielding gas is required, and a majority the wires run in direct-current electrode negative, meaning most of the heat is generated in the filler metal wire and not the base material. GMAW, on the other hand, is direct-current electrode positive, which generates most of the heat in the base material.
The gas tungsten arc welding (GTAW) process works great for low-volume or high-quality welding applications. The benefits of this process include high-quality welds, no spatter, and the best fusion possible. In some cases a filler metal isn’t necessary; the joint fit-up will determine this. Keep in mind, this process does require a greater degree of operator skill. To help minimize distortion, use a small tungsten electrode, such as 3/32 in. dia., and grind it to a fine point in the direction parallel to the length of the tungsten. It is best to use 100 percent argon for a shielding gas.
For some applications, you may need to use shielded metal arc welding on the joints. Be sure to choose a small-diameter electrode, use low amperage, and maintain a fast travel speed to produce an all-around good weld in the flat and horizontal positions. If you can weld only in the vertical position, increase your welding amperage by approximately 25 percent and weld in the vertical-down progression. This requires some practice, but it can produce a reasonably sound weld. The more commonly used method is to weld in the vertical-up position, but this isn't ideal for thin materials.
Stainless steel will use similar welding techniques and strategies as carbon steel. The preferred method is pulsed GMAW, but if SCT is the only available option, increase the inductance of the power source (if possible) to increase weld puddle control.
The main difference is matching the proper filler metal to the base material. When welding 304 stainless steel, use a 308 filler metal; for 316 stainless, use a 316 filler metal; and for welding stainless steel to carbon steel, use a 309 filler metal. The appropriate shielding gas mixtures for stainless steel GMAW are high in argon content, such as 98 percent argon/2 percent oxygen or CO2. Tri-mixes and even quad-mixes that use other gases like nitrogen or helium are available, but they aren’t cheap. Make sure you review your application and determine what is necessary. FCAW on stainless and carbon steel requires either 100 percent CO2 or a 75 percent argon/25 percent CO2 blend.
When welding aluminum, preweld joint preparation is very important. All welding processes benefit from a clean weld joint, but aluminum is unique in that it has a heavy oxide layer that has a higher melting point than the base material. Preparing the joint by wire brushing or grinding off the oxide layer and using a solvent to clean it will make the welding easier and produce a cleaner weld.
The commonly used aluminum grades typically require either an ER4043/ER4047 or ER5356 filler metal. Make sure you match your filler metal to the base material. For GMAW, shielding gas blends with at least 50 percent helium and an argon balance work very well but are also very expensive. If that is a concern, you can use 100 percent argon. For GTAW, use 100 percent argon and a small-diameter, 2 percent cerium tungsten electrode.
Galvanized welding will follow some of the same guidelines as welding carbon steel, except when dealing with the zinc layer on the surface, which is not conducive to the welding process and typically produces welds with porosity and poor bead appearance. If you are using GMAW, choose a shielding gas with a high CO2 content, such as the 75 percent argon/25 percent CO2 blend. Carbon dioxide is an active gas, meaning it assists in the cleaning action of the weld puddle and can help prevent porosity. Additionally, using slightly higher voltage and slower travel speeds can give adequate time for the welding puddle to de-gas and for the weld toes to tie in more smoothly.
Another option is to use a smaller-diameter flux-cored wire such as a dual-shield type. This wire uses an inner flux to produce a protective slag layer, and a shielding gas to clean and protect the solidifying weld puddle. Since this process has two methods of cleaning, it may produce the best bead appearance and weld quality even though it has lower deposition efficiencies.
While we didn’t cover every application, scenario, or base material, this information should give you a good starting point.
About the Authors
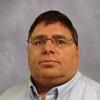
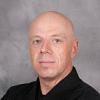
Rob Koltz
Application Engineer
411 S. Ebenezer Rd.
Florence, 29501
636-485-2253
Steve Sigler
Application Engineer
411 S. Ebenezer Rd.
Florence, South Carolina 29501
636-485-2253
About the Publication
Related Companies
subscribe now
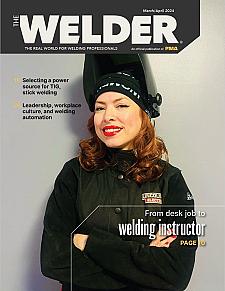
The Welder, formerly known as Practical Welding Today, is a showcase of the real people who make the products we use and work with every day. This magazine has served the welding community in North America well for more than 20 years.
start your free subscription- Stay connected from anywhere
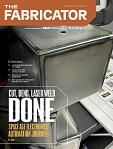
Easily access valuable industry resources now with full access to the digital edition of The Fabricator.
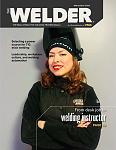
Easily access valuable industry resources now with full access to the digital edition of The Welder.
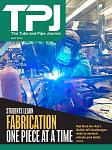
Easily access valuable industry resources now with full access to the digital edition of The Tube and Pipe Journal.
- Podcasting
- Podcast:
- The Fabricator Podcast
- Published:
- 04/16/2024
- Running Time:
- 63:29
In this episode of The Fabricator Podcast, Caleb Chamberlain, co-founder and CEO of OSH Cut, discusses his company’s...
- Trending Articles
Sheffield Forgemasters makes global leap in welding technology
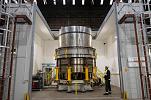
ESAB unveils Texas facility renovation
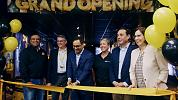
Engine-driven welding machines include integrated air compressors
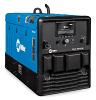
How welders can stay safe during grinding
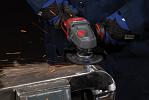
The impact of sine and square waves in aluminum AC welding, Part I
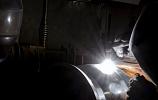
- Industry Events
16th Annual Safety Conference
- April 30 - May 1, 2024
- Elgin,
Pipe and Tube Conference
- May 21 - 22, 2024
- Omaha, NE
World-Class Roll Forming Workshop
- June 5 - 6, 2024
- Louisville, KY
Advanced Laser Application Workshop
- June 25 - 27, 2024
- Novi, MI