Editor
- FMA
- The Fabricator
- FABTECH
- Canadian Metalworking
Categories
- Additive Manufacturing
- Aluminum Welding
- Arc Welding
- Assembly and Joining
- Automation and Robotics
- Bending and Forming
- Consumables
- Cutting and Weld Prep
- Electric Vehicles
- En Español
- Finishing
- Hydroforming
- Laser Cutting
- Laser Welding
- Machining
- Manufacturing Software
- Materials Handling
- Metals/Materials
- Oxyfuel Cutting
- Plasma Cutting
- Power Tools
- Punching and Other Holemaking
- Roll Forming
- Safety
- Sawing
- Shearing
- Shop Management
- Testing and Measuring
- Tube and Pipe Fabrication
- Tube and Pipe Production
- Waterjet Cutting
Industry Directory
Webcasts
Podcasts
FAB 40
Advertise
Subscribe
Account Login
Search
Simplified automated consumables management and manual welds
Tech developer addresses tip change delays and weld gun ergonomics issues with product releases
- By Robert Colman
- November 11, 2023
- Article
- Arc Welding
The REVOLVER infinite-rotation semiautomatic MIG welding gun has a handle-to-cable interface that gives the operator freedom to weld at any position without cable resistance. Images: Nasarc
The welding equipment market is crowded with many big-name suppliers. For a smaller firm, it’s important to concentrate on producing specialty items that can stand out and make an impact on a company’s shop floor. Waterloo, Ont.-based Nasarc Technologies has found just such a route to success. Founded in 2001, Nasarc designs and produces advanced arc welding automation systems for automotive parts manufacturing, construction machinery, and a host of other parts production applications.
The company has made a name for itself with its flagship INTELLIREAM robotic torch maintenance centers and is now expanding its impact with the development of the Tip Exchange System (TES) and its new REVOLVER hand-held semiautomatic weld gun—the company’s first foray into manual technology.
Tip Change Automation
“Tip changes are something that frustrate everyone,” said Naseem Kteily, president and CEO of Nasarc. “They can take up to five minutes for an operator, which is a substantial amount of downtime for a welding robot. In a production line, if one robot needs a tip change, everything else grinds to a halt as well. An automated process like TES knocks that time down to about 30 seconds.”
The contact tip change system includes three components: the company’s REVOLUTION360 infinite rotation robotic MIG torch, the AUTOTIP automatic tip changer, and the AUTOCLEAN robotic torch maintenance center.
The robotic MIG torch is designed so that as it twists to reach welds, it does not, at the same time, twist the cable behind it. This means that less stress is placed on the cable, which should lead to a longer operating life cycle for that cable.
The robotic torch maintenance center includes automated nozzle reamer, automated nozzle removal and replacement, automated tip and diffuser cleaning, and automated wire cutter and antispatter sprayer. A nozzle gas flow sensor that detects gas flow at the point of use also is included.
The automatic tip changer includes automated tip removal and disposal and automated contact tip replacement. It’s equipped with a cartridge that holds 175 tips.
Of course, not all tip changes are simple.
“If burnback occurs, the robot controller will typically recognize that fact and will go through a different program to replace the tip,” said Kteily. “Normally, the system would cut the wire before removing the nozzle. But because the tip is fused, the system removes the nozzle first. The tip is cleaned so it can be clamped correctly, then it is drawn out and cut. The key is that the system adapts to issues like this automatically using the sensors it is equipped with.”
All of the Nasarc automated systems are Industry 4.0 compliant, which means it’s possible to monitor the machines’ cycle times, total ream cycles, spray cycles, and troubleshooting codes. The robotic MIG torch can monitor details like the resistance of the weld cable connected to it, the temperature at the power pin, and torch’s arc hours.
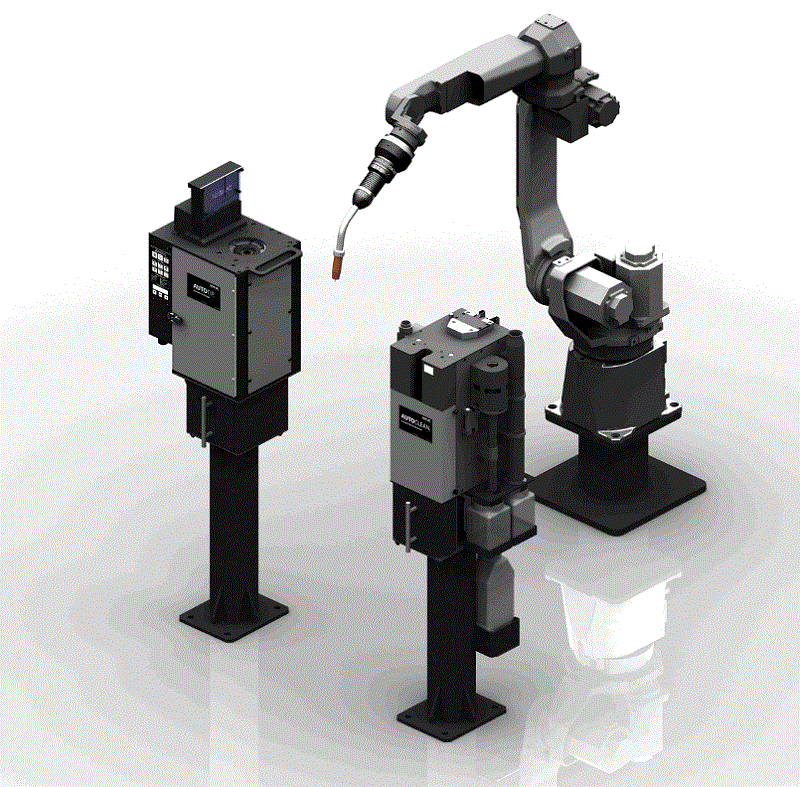
The contact tip change system includes three components: the REVOLUTION360 infinite rotation robotic MIG torch, the AUTOTIP automatic tip changer, and the AUTOCLEAN robotic torch maintenance center.
“All of this information is key for predictive maintenance,” said Kteily. “The resistance in a torch cable increases as it degrades. When that resistance hits a certain level, the system sends a signal recommending that the cable should be changed, avoiding any downtime or weld defects due to cable fatigue.”
The design of the system is modular, meaning everything is easy to access and maintain if a replacement part is ever needed.
Weld Gun Ease of Use
The technology that improves the movement and efficiency in the robotic MIG gun seemed ideal for a hand-held welding gun; it just took a little longer to move through product development.
The concept has come to fruition with the development of the REVOLVER infinite-rotation semiautomatic MIG welding gun.
The handle-to-cable interface gives the operator freedom to weld at any position without cable resistance. The handle is designed as a single body, aimed at making its serviceability simple.
Kteily sees benefits both for equipment longevity and user comfort.
By avoiding twisting the cable when moving the gun around, the cables maintain a certain resistance level for longer, without concern about fraying copper in the line.
But in terms of drawing interest in the market, ergonomics might be an even bigger attraction. The lack of strain from a twisting cable should lessen flexion and rotation on the wrist and stress on the elbow and shoulder. It also should significantly improve out-of-position welding capabilities.
“The difference in how easy it is on the wrist is noticeable. When you start moving around, it's just easier to move around. The cable's not getting all twisted up,” said Kteily. “We have a customer that trialed the gun for months. And one employee who had been welding for years had a bad shoulder, to the point where he was going to have to have surgery on it. We gave him the first generation of the REVOLVER to work with, which was bigger than the model we are going to market with. He was welding with it for two weeks, and he wasn't feeling any more pain. His shoulder was feeling good. The health and safety team at the company really took notice of that. They could see the savings that could come from not having to worry about repetitive strain injuries caused by twisting cables on a weld gun. In any business, you have to identify who your customer is. Sometimes it's the welder, sometimes it's the process engineer, sometimes it's health and safety, and sometimes it’s all of them.”
It may seem odd for a company that develops automation technology to be offering a semiautomatic welding gun, but as Kteily noted, even the most sophisticated adopters of welding automation still have jobs that require manual welding.
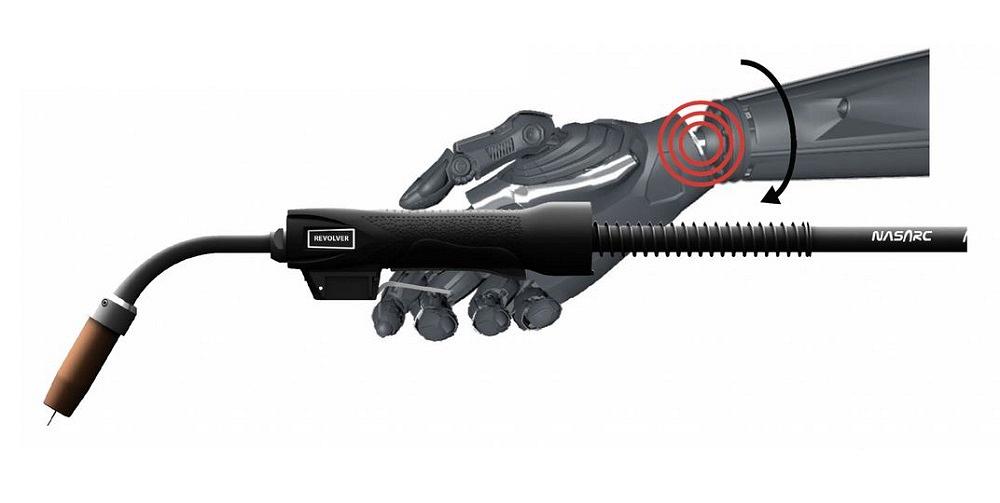
Nasarc’s REVOLVER decreases operator strain from a twisting cable by reducing flexion and rotation on the wrist and stress on the elbow and shoulder.
“If we can improve the efficiency and comfort of that operation, it adds value to our customer,” he said.
Editor’s Note: This article originally appeared in the September 2023 issue of Canadian Fabricating & Welding.
About the Author
Robert Colman
FMA Communications Canada Inc. 1154 Warden Avenue Suite #416
Toronto, ON M1R 0A1 Canada
(815) 399-8700
About the Publication
subscribe now
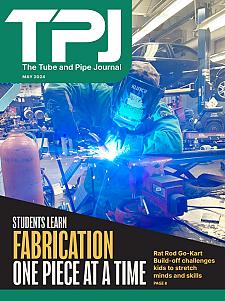
The Tube and Pipe Journal became the first magazine dedicated to serving the metal tube and pipe industry in 1990. Today, it remains the only North American publication devoted to this industry, and it has become the most trusted source of information for tube and pipe professionals.
start your free subscription- Stay connected from anywhere
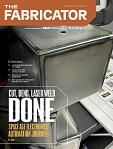
Easily access valuable industry resources now with full access to the digital edition of The Fabricator.
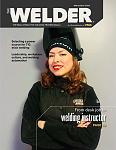
Easily access valuable industry resources now with full access to the digital edition of The Welder.
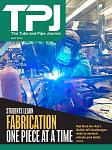
Easily access valuable industry resources now with full access to the digital edition of The Tube and Pipe Journal.
- Podcasting
- Podcast:
- The Fabricator Podcast
- Published:
- 04/16/2024
- Running Time:
- 63:29
In this episode of The Fabricator Podcast, Caleb Chamberlain, co-founder and CEO of OSH Cut, discusses his company’s...
- Trending Articles
Zekelman Industries to invest $120 million in Arkansas expansion
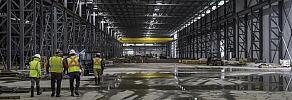
3D laser tube cutting system available in 3, 4, or 5 kW
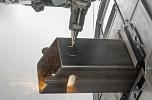
Corrosion-inhibiting coating can be peeled off after use
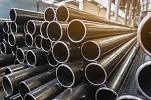
Brushless copper tubing cutter adjusts to ODs up to 2-1/8 in.
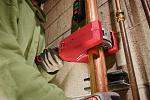
HGG Profiling Equipment names area sales manager
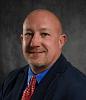
- Industry Events
16th Annual Safety Conference
- April 30 - May 1, 2024
- Elgin,
Pipe and Tube Conference
- May 21 - 22, 2024
- Omaha, NE
World-Class Roll Forming Workshop
- June 5 - 6, 2024
- Louisville, KY
Advanced Laser Application Workshop
- June 25 - 27, 2024
- Novi, MI