- FMA
- The Fabricator
- FABTECH
- Canadian Metalworking
Categories
- Additive Manufacturing
- Aluminum Welding
- Arc Welding
- Assembly and Joining
- Automation and Robotics
- Bending and Forming
- Consumables
- Cutting and Weld Prep
- Electric Vehicles
- En Español
- Finishing
- Hydroforming
- Laser Cutting
- Laser Welding
- Machining
- Manufacturing Software
- Materials Handling
- Metals/Materials
- Oxyfuel Cutting
- Plasma Cutting
- Power Tools
- Punching and Other Holemaking
- Roll Forming
- Safety
- Sawing
- Shearing
- Shop Management
- Testing and Measuring
- Tube and Pipe Fabrication
- Tube and Pipe Production
- Waterjet Cutting
Industry Directory
Webcasts
Podcasts
FAB 40
Advertise
Subscribe
Account Login
Search
Fabricator uses plasma technology to cut tube for ATV roll cages
Plasma power source with CNC provides clean, accurate cuts for Missouri shop
- By Eric Lundin
- May 2, 2022
- Article
- Cutting and Weld Prep
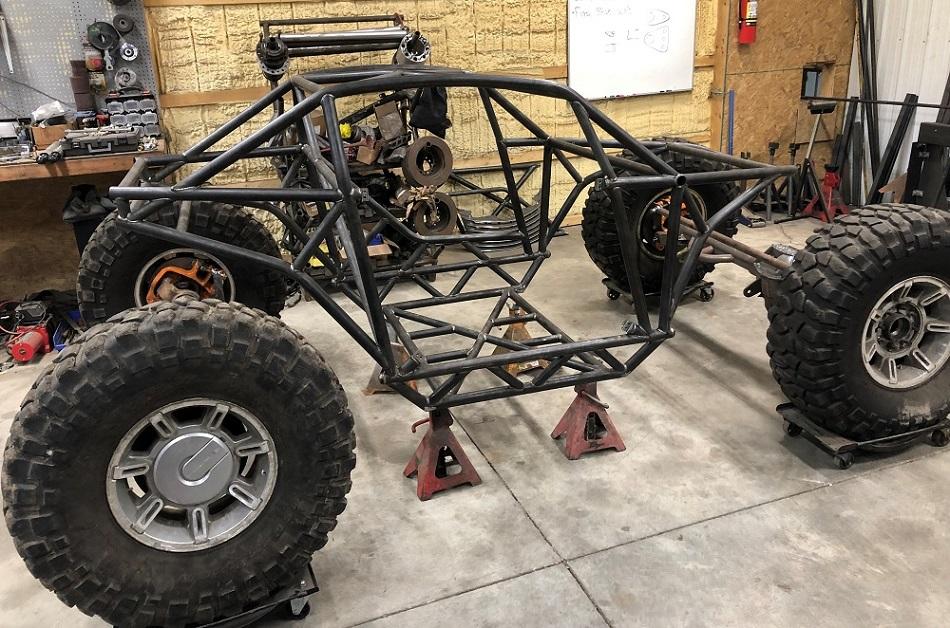
One of Travis Snider’s latest builds is a single-seater with the engine and transmission mounted next to the driver. When finished, it will have Ford super-duty axles, and the front and rear both will steer 50 degrees. The chassis took about a day for cutting, bending, and tack welding, Snider said.
In a manufacturing environment dominated by sheet and plate, tubular products pose more than a few fabricating challenges. Bending, cutting, welding—everything is more complicated when working around a circumference than when dealing with a flat surface and straight lines. Still, tubes are crucial. Although they aren’t used as extensively as sheet and plate, they’re nearly everywhere in manufacturing, useful for their strength-to-weight ratio and a variety of other reasons.
Long the mainstay for building vehicles of all sorts, including off-road vehicles, tube is an ideal material for frames, various structural and mechanical components, and safety cages. When used for building the structure of a top-fuel dragster, tube’s combination of strength and weight enable the racer to hit 330 MPH over a short distance, just 1,000 ft., without succumbing to the stresses of the race (usually). A heavier tube in a different configuration provides the frame and roll-over protection system (ROPS) for a bulldozer, even an enormous Caterpillar D11, which weighs 230,000 lbs.
Certainly, a more common off-road use for tubular products is the manufacture of an alphabet soup of vehicles used by consumers: sport utility vehicles, all-terrain vehicles, utility task vehicles, recreational utility vehicles, recreational off-highway vehicles, side-by-sides, and multipurpose off-highway utility vehicles (SUVs, ATVs, UTVs, RUVs, ROVs, SxSs, and MOHUVs). Designed for speeding over sand dunes, negotiating treacherous rock- and log-strewn courses, or competing in punishing hill-climbing races, most of these vehicles require a ROPS.
Whether the original, factory-installed ROPS in such a vehicle is sturdy enough is a matter of debate, one taken up by off-road enthusiast Travis Snider. The owner and founder of WelderD, a supplier of aftermarket roll cages, he’s able to weigh in on the matter. A professional engineer who spent 17 years at The Boeing Co., he’s familiar with materials, their strengths, and structural design. His doubts about factory-original ROPS stem from the material and the assembly method; in many cases, the tube wall is too light and the cages are held together by mechanical fasteners.
“Most side-by-side cages are bolted together in pieces to make assembly as easy as possible,” he said. “Aftermarket cages are as continuous as can be. Another factor is joint location. On many factory cages, the joints are convenient for manufacturing and assembly but disregard structural load paths.” As far as he’s concerned, the minimum ROPS certification they have to pass isn’t adequate for the intended use of these machines.
He knows a thing or two about stresses and load paths. Snider’s knowledge of materials and structures is such that he once had a gig teaching aircraft engineers the ins and outs of airframe repairs on the F15 Eagle, McDonnell Douglas’ venerable air superiority fighter. It’s much larger than some fighters, and it packs a punch. The dual Pratt & Whitney F100 engines develop 14,590 pound-feet of thrust, and the aircraft can withstand stresses that exceed 9g. Airframe repairs are necessary from time to time.
This is the caliber of expertise that consumers get when they purchase a roll cage from WelderD, which specializes in cages assembled and installed by do-it-yourselfers. The company cuts and bends the tubes, does some tack welding, and packages the subassemblies in kits for shipping.
“Most off-road enthusiasts know how to weld, so we ship kits unassembled to keep the shipping costs down,” Snider said. Anyone who has ever shipped any amount of tubing knows that shipping tubing means shipping air, and this isn’t cost-effective. Shipping an assembly made of tubing is much worse, so Snider ships kits that can be packed somewhat flat.
The Right Combination of Technologies for a Challenging Application
Bending sheet or plate means dealing with one inside surface, one outside surface, and a neutral axis; bending a tube means bending around the entire circumference—an inside and outside surface at the inside of the bend (the intrados), an inside and outside surface at the outside of the bend (the extrados), and much more compressing and stretching than takes place when bending a flat product. A bad combination of tube characteristics and bend radius can lead to wrinkles on the intrados and excessive stretching and weakening or failure on the extrados.
For bending, Snider relies on a Mittler Brothers bender, model MD-2500.
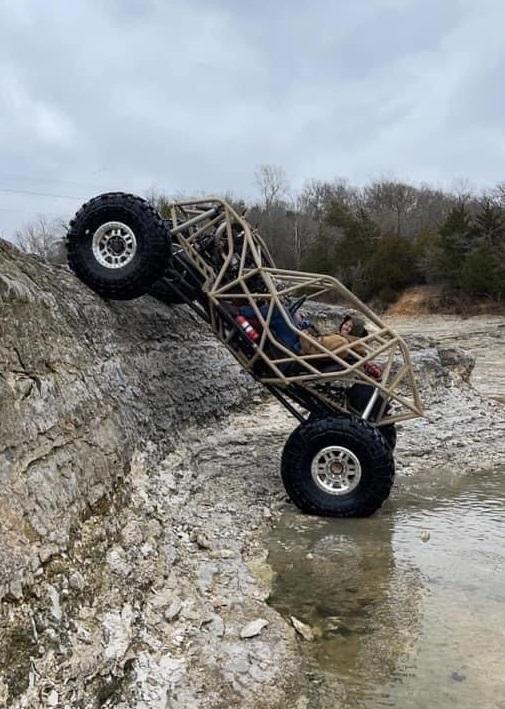
It’s built for neither comfort nor speed. Geared low and built with high ground clearance, this vehicle is built for crawling over nearly anything in its path, which it does well.
“The company is local, only 25 miles away, so it’s easy to get new dies,” he said. For the most part, Snider relies on off-the-shelf sizes, but the company provides custom dies on request. This helps in Snider’s other line of work, contract manufacturing.
Cutting tube for intersections likewise can be challenging, depending on the tools that are available. To make a saddle cut on a tube end by hand often means using homemade templates and common shop tools to make a contour at the end of one tube that matches the mating tube’s surface precisely. For a 90-degree intersection, this is difficult; for an intersection of any other angle, this is perhaps the most time-consuming and inconsistent process in all of metal fabrication. Fixturing and machining the tube is a possibility, but thermal processes tend to be much faster.
Once in a while, Snider farms out a job for laser cutting, but for the most part, he cuts tube in-house using a Hypertherm model, the Powermax45 XP air plasma cutter. Available in a 240-V, single-phase model, or a 480-V three-phase model, it produces up to 45 amps and has a recommended handheld cutting capacity up to 0.625 in. thick. It cuts quickly too. When cutting gauge material on an X-Y CNC table, it cuts around 180 in./min.
In Snider’s view, you get what you pay for, and in some cases, you get far more. While his equipment hasn’t needed much attention, it has needed a little, and he has been more than pleased by Hypertherm’s responses to his inquiries.
“Hypertherm has been flawless and even helped diagnose machine control problems in the beginning that were not their responsibility,” he said. He also has found that the company’s consumables are worth the money. Hypertherm is careful in its selection of supply chain partners, which ensures a supply of consistent, high-quality raw materials for its consumables, and uses statistical process control software to optimize the consumable inspection process.
“Hypertherm’s consumables are the only way to go, and a great difference can be seen in both quality of cuts and life of the consumables over cheap knockoffs,” he said.
The Right Background, The Right Time
“I’ve been into off-roading for a long time,” Snider said. After his years at Boeing and several other similar jobs, he finally decided to turn his hobby into a new phase of his career, launching WelderD in 2019.
Getting a business started shortly before a global pandemic struck sounds like it was bad luck, but it wasn’t. In an article summarizing recent sales of off-road vehicles, MotorcylesData.com states that sales of some categories already were robust, having doubled from 2012 to 2020, and that long-term trend was nudged along by a big jump in sales that occurred after the pandemic set in. Of course, businesses of all sorts had several very bad months in 2020, but the outcome was more money in the pockets of many consumers.
Temporary closures of many businesses—restaurants, movie theaters, and all others deemed nonessential—meant that many consumers had a little extra money to spend elsewhere. Many people gravitated toward outdoor activities, and various sorts of off-road vehicles sold briskly. And although Snider hasn’t been in business long, he’s off to a great start. His sales doubled in 2020 and doubled again in 2021.
Building a Junior Rock Crawler
While Travis Snider’s main line of work involves roll cages for specific makes and models, he gets involved in other projects as well. One custom project involved cutting the tube for an entire rock crawler. Another off-road enthusiast, Jason Hoffman, came up with his own design for a junior-size rock crawler for his daughter.
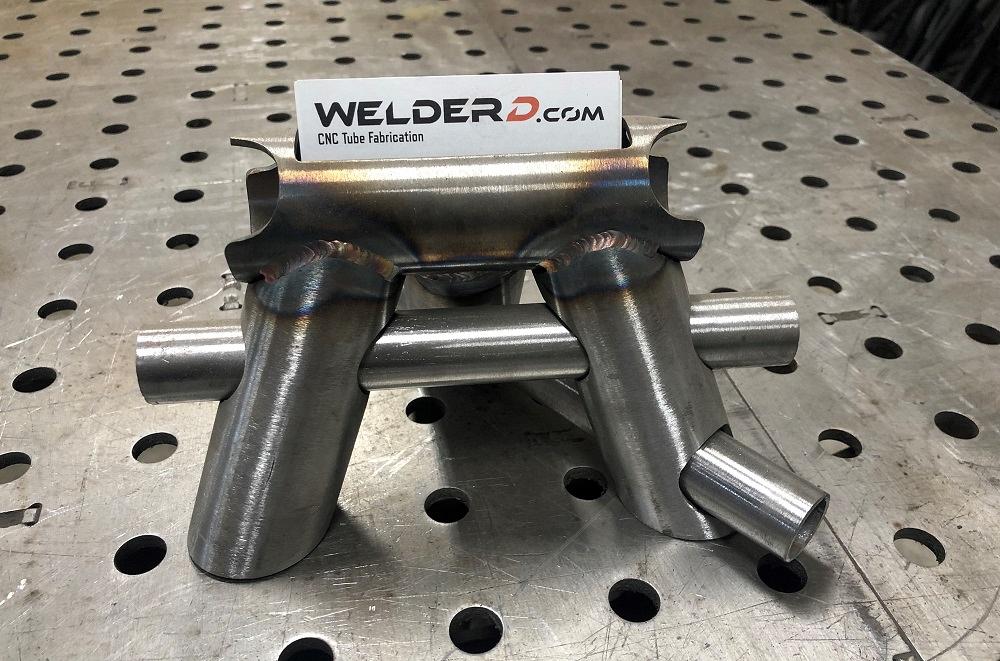
CNC plasma cutting makes quick work of cutting precise saddles and through-holes for tube intersections.
“I built my first Jeep when I was in high school,” Hoffman said. “It was probably in 2004 or 2005.” The off-road market was still somewhat a niche market for do-it-yourselfers, Hoffman recalled. Early work-oriented utility vehicles had been around for a while at this point, but the designs weren’t flashy. Most looked no more sporty than a golf cart. The target market comprised ranchers, groundskeepers, and any other outdoor workers who had to cover a lot of ground with a few tools or supplies. John Deere’s AMT (all-materials transporter) was introduced in 1987, Kawasaki introduced its Mule in 1988, and the Honda Pilot came out in 1989.
Recreational models with a sporty look were right around the corner. Yamaha introduced the Rhino to the market in 2004 and Polaris launched the Ranger RZR in 2007, and it wasn’t long before the recreational market took off.
Fast-forward to 2019 or so, and Hoffman was interested in building another vehicle. This one would be a rock crawler for his daughter. He put a lot of thought into it and developed a custom design.
A sheet metal worker and welder by trade, and the owner of a small fab shop himself, Hoffman knew what he had to do to build a rock crawler, but he didn’t have a machine that could cope with that amount of tube in a timely manner. He was already knowledgeable about plasma cutting, using a CNC Hypertherm Powermax85 for sheet work in his own shop, so when he found WelderD, he was on familiar ground.
The design had to be one-of-a-kind for two reasons. First, it had to be scaled properly to fit a child, his five-year-old daughter. Second, it had to accommodate the drivetrain and steering system, which are unique, to say the least.
“The engine and transmission are from a 2005 Arctic Cat. I coupled the transmission to a transfer case and axles that I salvaged from an old Suzuki Samurai,” he said. He put together a steering system using components from junked passenger cars.
“On a buggy, the steering unit usually is mounted in front of the axle ,” he said. “On most cars, the steering unit is behind it.” He needed a rack and pinion unit set up the right way and found that the Chrysler 300 had one like that. He mated it to the electronic power steering unit from a Saturn Vue.
He contacted Snider and sent over the drawing, which was nearly finished. He and Snider exchanged a few emails and Snider suggested some changes, part of the value engineering that Snider provides to any customer who asks. Before long, they had a finalized design—and Hoffman had a very happy daughter.
About the Author
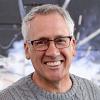
Eric Lundin
2135 Point Blvd
Elgin, IL 60123
815-227-8262
Eric Lundin worked on The Tube & Pipe Journal from 2000 to 2022.
About the Publication
Related Companies
subscribe now
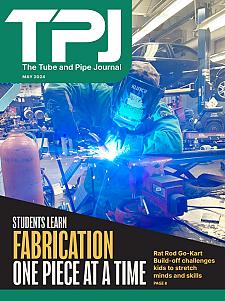
The Tube and Pipe Journal became the first magazine dedicated to serving the metal tube and pipe industry in 1990. Today, it remains the only North American publication devoted to this industry, and it has become the most trusted source of information for tube and pipe professionals.
start your free subscription- Stay connected from anywhere
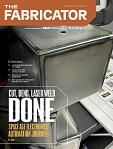
Easily access valuable industry resources now with full access to the digital edition of The Fabricator.
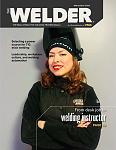
Easily access valuable industry resources now with full access to the digital edition of The Welder.
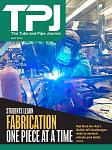
Easily access valuable industry resources now with full access to the digital edition of The Tube and Pipe Journal.
- Podcasting
- Podcast:
- The Fabricator Podcast
- Published:
- 04/16/2024
- Running Time:
- 63:29
In this episode of The Fabricator Podcast, Caleb Chamberlain, co-founder and CEO of OSH Cut, discusses his company’s...
- Trending Articles
Zekelman Industries to invest $120 million in Arkansas expansion
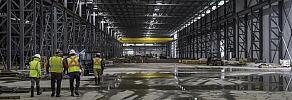
3D laser tube cutting system available in 3, 4, or 5 kW
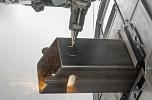
Corrosion-inhibiting coating can be peeled off after use
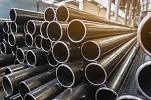
Brushless copper tubing cutter adjusts to ODs up to 2-1/8 in.
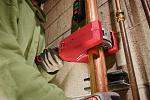
HGG Profiling Equipment names area sales manager
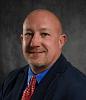
- Industry Events
16th Annual Safety Conference
- April 30 - May 1, 2024
- Elgin,
Pipe and Tube Conference
- May 21 - 22, 2024
- Omaha, NE
World-Class Roll Forming Workshop
- June 5 - 6, 2024
- Louisville, KY
Advanced Laser Application Workshop
- June 25 - 27, 2024
- Novi, MI