- FMA
- The Fabricator
- FABTECH
- Canadian Metalworking
Categories
- Additive Manufacturing
- Aluminum Welding
- Arc Welding
- Assembly and Joining
- Automation and Robotics
- Bending and Forming
- Consumables
- Cutting and Weld Prep
- Electric Vehicles
- En Español
- Finishing
- Hydroforming
- Laser Cutting
- Laser Welding
- Machining
- Manufacturing Software
- Materials Handling
- Metals/Materials
- Oxyfuel Cutting
- Plasma Cutting
- Power Tools
- Punching and Other Holemaking
- Roll Forming
- Safety
- Sawing
- Shearing
- Shop Management
- Testing and Measuring
- Tube and Pipe Fabrication
- Tube and Pipe Production
- Waterjet Cutting
Industry Directory
Webcasts
Podcasts
FAB 40
Advertise
Subscribe
Account Login
Search
Laser machine helps tube fabricator perfect storage system, launch new company
Storage rack manufacturer relies on machine’s accuracy, repeatability for making precise tube weld joints
- By Eric Lundin
- November 10, 2018
- Article
- Cutting and Weld Prep
Like many fabricators, the staff at Technique Inc., Jackson, Mich., dealt with a persistent dilemma: continue using traditional storage racks or invest in an automated storage and retrieval system (ASRS). A specialist in rapid prototyping and low-volume production, the company has a metals inventory that is varied more than most: It keeps a stock of material in thicknesses from foil to ½ inch in dozens of ferrous and nonferrous alloys. Keeping the material organized and ready for quick retrieval is just as important to this fabricator as it is to any other, and perhaps more so.
A specialist in stamping, welding, and tube fabrication and a provider of emergency manufacturing for its clients, Technique never knows what it will deal with from one day to the next. Although its forte is its ability to develop prototyping tooling quickly and to turn around prototype parts in short order, keeping its inventory of sheet material organized is another critical element in the company’s success. The quicker the production personnel can get the material to the machine, the quicker they can make parts and get them out the door.
For storing large amounts of flat products—that is to say, sheet metal—few choices exist. In the view of Technique’s president, Ronnie Johncox, the market is dominated by just two types.
“The choices are cantilevered storage racks and automated tower systems,” he said. “Cantilevered storage racks are inexpensive but don’t have any features. Automated storage and retrieval systems are programmed, they come in many styles, most can be ordered with a large number of options, and they help keep track of inventory. However, for many small shops, the cost is difficult to justify.”
In short, the choices are simple or complex, and the price tags are proportional. Between these two extremes, Johncox found no products in the middle ground. What’s a fabricator to do? An entrepreneur at heart, Johncox developed his own system. It was such a success that he began building them for his customers, and eventually he spun off a new company, Big Steel Rack, to build and sell this new product.
Rack ‘em Up
Nobody wants to dedicate a lot of time to indirect labor; keeping inventory neat and organized is very indirect labor. Meanwhile, nobody wants to dedicate vast amounts of square footage to inventory; every additional square foot set aside for inventory is one less square foot dedicated to something that makes money—a machine. Put these two together, and chaos ensues.
“The big downside to a traditional shelving system is that disorganization creeps in,” said Big Steel Rack Vice President of North American Sales Paul Brockie.
Everyone starts out with good intentions, and for a while they keep every alloy and size separate. However, it’s hard to maintain such a system. Before long, a single shelf holds two or three thicknesses of sheet, or a few 4- by 8-foot sheets and several 5- by 10-ft. sheets, and perhaps some leftover material (drop sheets), and nobody takes the time to straighten this out.
On the other hand, ASRSs keep inventory organized, and they have another benefit in storage density: They hold a lot of inventory but use little floor space. Many refer to them as tower systems, a name that reflects this capability.
Johncox came up with a concept that captures the middle ground, providing a high-density system that makes organization a breeze. Like many innovations, the beauty of Big Steel Rack is its simplicity.
“This system has some of the features of automatic retrieval, but the price tag is closer to that of a series of cantilevered shelves,” Brockie said.
“The system has two components: racks and pallets,” he said. “The pallets have serial numbers, so keeping the inventory organized is a matter of creating a database that associates every serial number with the inventory stored on the corresponding pallet. When you use some material, you update the database. Maintaining the database means always knowing how much material you have on hand and always knowing where it is stored.”
“The database helps fabricators get around the downside that plagues traditional shelving systems,” he said. “It’s not uncommon to spend 10 or 15 minutes looking for material.” That’s another case of indirect labor chewing up profit.
A Power Trio: Accuracy, Repeatability, and Processing Speed. Designing and building a storage system for one’s own use is one thing; producing them for sale is something else altogether. The former doesn’t have the time pressure, quality concerns, or the need for process consistency that the latter has. If you’re making a rack for your own use and it’s taking too long, it doesn’t matter as much as late deliveries matter to customers. If one of your own shelves isn’t straight and nobody notices right away, who cares? You’ll see it when it’s installed, and you can rework it then. It’s not like you’re delivering a misaligned product to a customer. Finally, if you notice that your shelf spacing varies a bit, that’s not really a problem, but your customers would notice and might interpret it as a sign of poor quality. Word-of-mouth advertising, the negative kind, can torpedo an otherwise good product.
Johncox knew that to achieve the accuracy, repeatability, and production volume he’d need for his product, he’d have to invest carefully. The accuracy and repeatability weren’t just helpful from a quality standpoint, but necessary from a process standpoint. Technique relies heavily on robotic welding, and robots need consistency. While a welder can look at a fit-up that varies from joint to joint and adjust the welding process to compensate, a robotic welding unit has no comparable decision-making capability. A robot makes the weld that it has been programmed to make and doesn’t do much beyond that.
In light of these concerns and constraints, the Technique staff quickly homed in on laser cutting to provide the end cuts for weld joints.
“When we started working on this project, we were already familiar with laser cutting,” Johncox said. “We had done laser cutting for our prototyping work, and we knew that the accuracy, fit, and repeatability of laser-cut components was far superior to the characteristics of saw-cut parts,” he said.
Although Technique already had a machine from BLM Group USA, one from the early 2000s, the company didn’t feel that it was tied to a particular brand. It was open to researching the machines from other vendors and put some time and effort into checking out the other machines on the market. Eventually, this process led Technique back to BLM. An early adopter of fiber technology, BLM brought the fiber concept to the tube laser cutting industry, and in Johncox’s view, the company continues to be an innovator.
“BLM machines were the first to have two loaders, one on each side of the machine,” he said.
“The main loader processes large bundles of tubing, allowing us to run the machine for several hours unattended,” Brockie said. “However, if we need to run just a few tubes, we can interrupt that job, make a few parts by loading them through the front of the machine, and then resume the large run, the one loaded from the back of the machine. This is a huge advantage in a prototyping shop.”
Without such a loader, the fabricator would have to either wait until the big production run was finished or unload the original raw material from the machine, load and run the few tubes for the low-volume run, then reload the material for the original run.
Taking all of this, and other features, into consideration, the company invested in an LT8.10, which uses a 3-kW fiber power source to cut mild steel (including galvanized), stainless steel, aluminum, copper, and brass tube in diameters up to 9.5 in. It accepts lengths up to 28 ft. Although other machines are available that have similar compelling features, Johncox is confident that this is the best machine for his application. “The software, the single-load capability, the dimensions it handles, and the weld seam detector collectively make it the best machine on the market for what we do.”
Storing Sheet and Plate or Tube, Pipe, and Bar. For a storage system that inventories items in many standard sizes, yet is customizable, the ability to cut long and large-diameter tubing is critical.
That is, the pallets are made to a few standard dimensions, corresponding to standard sheet sizes, but the racks vary in length and height. This means that the tubing used to build the structure varies in proportion with the projected loads. A bigger system needs more strength, so the company scales up the tube dimensions accordingly.
Understanding the loading is critical. “I heard of another fabricator who made his own racks,” Johncox said. “Apparently he didn’t calculate the stresses accurately. His inventory overloaded the system and it collapsed,” he said.
A second product line is similar to the first, but was developed for storing so-called long products, such as tube, pipe, and bar stock. Big Steel Rack used the same design concept, but it had to account for one critical difference. Tube, pipe, and bar are available in many more dimensions than sheet and plate. In commonly used small sizes, from 1⁄8 to 4 in., pipe is available in 13 diameters. Tubing further complicates matters because it isn’t restricted to common sizes; a shop equipped with a draw bench and die-making capability can make tube to any conceivable size it wants. Storing tube or pipe is anything but a one-size-fits-all proposition.
“The tube storage rack itself is made mainly from tube,” Brockie said. “To make each rack, we use the laser machine to make holes along the length of each tube, and then we insert a bushing into each hole.”
Again, simplicity. The user inserts pins into the bushings to create spaces for the tubes, placing the pins close together to make narrow spaces or far apart to make wide spaces, depending in the diameter of the product to be stored on that rack.
“Each of these tubes has hundreds of pin locations,” Brockie said. “It would take far too long to drill or machine these holes, but it’s a fast process on a laser machine.”
DoD, NASA, and OSHA
Many manufacturers cringe at the thought of getting involved in government work. The alphabet soup of government jargon is bad enough, but that’s nothing compared to learning about military standards, complying with the paperwork requirements, and other government obligations. Big Steel Rack, however, embraces its role as a government supplier. It got its feet wet doing some prototyping work.
“Once you understand the military codes and standards, it gets easier,” Brockie said. “After you win a bid, you’re more likely to win other bids. We couple that with other strategies, like attending military-oriented trade shows.”
These strategies worked.
“We have sold storage rack systems to every branch of the military, including a system installed at the base at Pearl Harbor,” Brockie said.
The company used that knowledge to build a bridge to the National Aeronautics and Space Administration (NASA). NASA isn’t the military, but because it’s a government agency and Big Steel Rack is a Department of Defense (DoD) supplier, the company’s reputation helped open the door to NASA.
The Big Steel Rack executive team is confident that, like the Pentagon and NASA, the Occupational Safety and Health Administration (OSHA) would look upon this storage system with favor. It was designed with safety in mind.
“When you lift a single sheet on a forklift, it bends,” Brockie said. Driving a fork truck through a fabrication shop, carrying a sheet of steel with exposed, sharp edges that wave back and forth a bit as the fork truck moves along is a minor safety nightmare. The company’s pallets support the load, keeping sheets flat.
Second, a load of sheet steel can shift on the forks while the fork truck is in motion. Nobody wants to see what happens when a load of several hundred pounds on an extended fork shifts suddenly. A best-case scenario involves bent sheets or damaged edges.
“Our pallets encapsulate the forks,” Brockie said. “Even if the load shifts, it can’t flip the pallet off the forks.”
Finally, the pallets are longer and wider than the standard sheet dimensions, providing a buffer.
“Our pallet for 5- by 10-ft. sheets actually measures 66 by 126 in., providing an extra 6 in. in both dimensions,” Brockie said. Setting the stack of sheet in the center provides a 3-in. buffer all the way around, greatly reducing the laceration hazard at the edges and corners. Personnel walking through the shop might contact a pallet, but the sheet metal’s edges are inset from the pallet’s edges, making contact with the sharp edges unlikely.
Big Steel Rack, http://bigsteelrack.com
BLM Group USA, www.blmgroup.com
About the Author
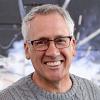
Eric Lundin
2135 Point Blvd
Elgin, IL 60123
815-227-8262
Eric Lundin worked on The Tube & Pipe Journal from 2000 to 2022.
About the Publication
Related Companies
subscribe now
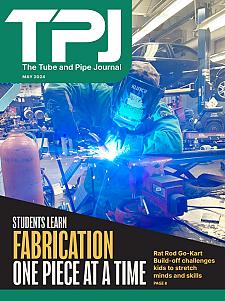
The Tube and Pipe Journal became the first magazine dedicated to serving the metal tube and pipe industry in 1990. Today, it remains the only North American publication devoted to this industry, and it has become the most trusted source of information for tube and pipe professionals.
start your free subscription- Stay connected from anywhere
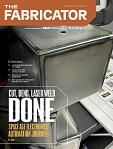
Easily access valuable industry resources now with full access to the digital edition of The Fabricator.
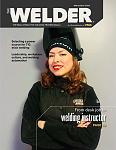
Easily access valuable industry resources now with full access to the digital edition of The Welder.
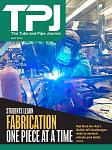
Easily access valuable industry resources now with full access to the digital edition of The Tube and Pipe Journal.
- Podcasting
- Podcast:
- The Fabricator Podcast
- Published:
- 04/16/2024
- Running Time:
- 63:29
In this episode of The Fabricator Podcast, Caleb Chamberlain, co-founder and CEO of OSH Cut, discusses his company’s...
- Trending Articles
Zekelman Industries to invest $120 million in Arkansas expansion
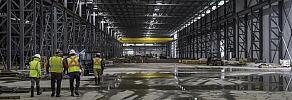
3D laser tube cutting system available in 3, 4, or 5 kW
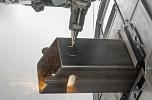
Corrosion-inhibiting coating can be peeled off after use
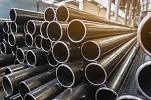
Brushless copper tubing cutter adjusts to ODs up to 2-1/8 in.
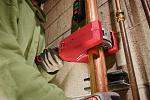
HGG Profiling Equipment names area sales manager
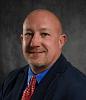
- Industry Events
16th Annual Safety Conference
- April 30 - May 1, 2024
- Elgin,
Pipe and Tube Conference
- May 21 - 22, 2024
- Omaha, NE
World-Class Roll Forming Workshop
- June 5 - 6, 2024
- Louisville, KY
Advanced Laser Application Workshop
- June 25 - 27, 2024
- Novi, MI