President
- FMA
- The Fabricator
- FABTECH
- Canadian Metalworking
Categories
- Additive Manufacturing
- Aluminum Welding
- Arc Welding
- Assembly and Joining
- Automation and Robotics
- Bending and Forming
- Consumables
- Cutting and Weld Prep
- Electric Vehicles
- En Español
- Finishing
- Hydroforming
- Laser Cutting
- Laser Welding
- Machining
- Manufacturing Software
- Materials Handling
- Metals/Materials
- Oxyfuel Cutting
- Plasma Cutting
- Power Tools
- Punching and Other Holemaking
- Roll Forming
- Safety
- Sawing
- Shearing
- Shop Management
- Testing and Measuring
- Tube and Pipe Fabrication
- Tube and Pipe Production
- Waterjet Cutting
Industry Directory
Webcasts
Podcasts
FAB 40
Advertise
Subscribe
Account Login
Search
Hammering parts with hydroforming
Pulsing pressure provides proficient pounding process
- By Teruaki Yogo
- October 11, 2010
- Article
- Hydroforming
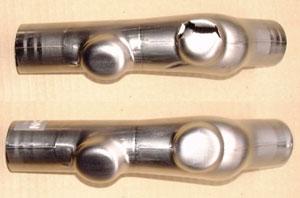
A component formed with a static pressure, top, ruptured before forming was complete. The hammering process formed the component to its final shape, bottom.
In recent years hydroforming has become a commonly used method of tube expansion for many applications, such as automotive chassis frames, exhaust manifold piping connectors, and air-conditioning system components. Because hydroforming uses water under high pressure to expand the tube or pipe from the inside, and water can take any shape, it’s a versatile process and is suitable for forming complex, single-piece components.
Pump up the Pressure (Then Reduce It)
One new development in this field is the hammering method, in which the pressure system uses a pulsing or vibrating action. This is in contrast to the conventional static pressure method, in which the water pressure increases gradually.
Hammering uses two alternating pressures. It reduces the drag force, which is the friction that develops between the workpiece and the die. As the internal pressure increases, the work expansion force increases the drag force, or friction, between the workpiece and the die. Also, the internal pressure becomes a force that pushes back against the hydraulic system. The combination of work expansion force and internal pressure is the reaction force.
As the reaction force increases, it becomes difficult to force the material to flow into all of the contours and recesses of the die.
The hammering method cycles between a high and low pressure (see Figure 1). The repeated pressure drops reduce the drag force, allowing the material to flow further in the die. It also prevents thinning at the expansion areas and improves the process capability.
The hammering process is driven by a pump that varies the pressure it develops, such as a direct drive volume (DDV) control pump, a high-pressure generator that uses a hydraulic servo pump. The DDV is a hybrid of an AC servomotor and reversible-piston pump. The pulsations are generated by controlling the forward and reverse rotation of the AC servomotor at high speed.
Hammering Terms and Parameters
Hammering data comprises a start-up pressure and a shutdown pressure; a start-up time and shutdown time; and, in some cases, a hold time. The difference between start-up pressure and a shutdown pressure is the amplitude. The time from start-up time to shutdown time (including hold time) is one cycle. The frequency is the number of cycles that elapse in one second and is measured in hertz (Hz).
Results from hydroforming trials have shown that the optimal hammering frequency range is between 1 and 3 Hz. Frequencies higher than 3 Hz make it physically impossible for the pressure to reach the intended high and low points. In other words, reversing the pressure more than 3 times per second doesn’t give the hydraulic system enough time to achieve the programmed pressures.
The optimal pressure range is between 725 and 4,350 pounds per square inch (PSI), or 5 to 30 MPa.
Programming. Compared to the traditional static method, hammering requires more parameters, so it can be difficult to optimize the process. Even a simple combination of frequency and amplitude has many possibilities. For example, the pressure may be raised while performing the hammering, or the expansion force may be synchronized to change with the hammering’s internal pressure. Furthermore, hammering may be used for part of the forming cycle and continuous pressure used for another part of the cycle (see Figure 2).
Note that the internal pressure, expansion force, and processing time can be affected by other factors, including the lubricant applied before processing.
When using the hammering method, the achieved pressure isn’t always the same as the programmed pressure. This doesn’t indicate a problem or an abnormality; in some cases, the pressure doesn’t reach the target level because the expanding pipe relieves some of the pressure. This most often happens at the onset of expansion.
Troubleshooting. Two forming problems are rupturing and buckling.
Rupturing is usually the result of setting the internal pressure too high or the expansion force too low. This causes the material to stretch and become too thin in the expansion area, ultimately causing a rupture. This is why it is critical to balance the internal pressure and initial expansion force. To resolve the situation, adjust one of these pressures; it also may help to speed up the processing time.
Using an initial pressure that is too high also can cause the pipe to expand too quickly, causing the material at the axis sealing area to pull away. This, in turn, causes the fluid to leak, so the pressure does not rise to the set value and the processing can’t start.
On the other hand, buckling usually is caused by setting the internal pressure too low or the expansion force too high. Using a processing time that is too fast also may contribute to buckling.
Hammering Hydroformer System Diagram
A complete system uses three DDV pumps (see Figure 3). One generates the pulsating pressure that forms the tube; the others are multipurpose pumps used to raise and lower the press’s upper die at high speed. When the upper die is completely closed, the DDV seals and presses in both ends of the tube workpiece.
The DDV’s AC servomotor is regulated by a CNC. This controls the hammering frequency and pressure increase rate.
The pulse frequency and pressure on the secondary side is controlled by the reversible AC servomotor of the DDV pump and pulsing the primary side of the oil and water boosting cylinder at a ratio of 1-to-10. The shape that can be formed in one cycle of tube expansion is determined by the maximum water capacity in the high-pressure cylinder.
Compared to a conventional machine, a DDV hydraulic system uses less than one-third of the electricity (see Figure 4a) and oil; runs 10 decibels quieter (see Figure 4b); generates less than half of the heat; has a pressure loss that is less than half; requires less space; and does not require a large-capacity oil tank.
About the Author
Teruaki Yogo
41208 Capital Drive
Canton, MI 48187
734-453-2188
About the Publication
subscribe now
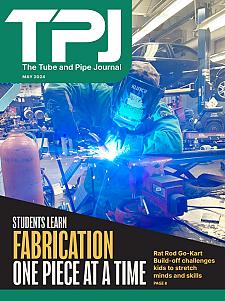
The Tube and Pipe Journal became the first magazine dedicated to serving the metal tube and pipe industry in 1990. Today, it remains the only North American publication devoted to this industry, and it has become the most trusted source of information for tube and pipe professionals.
start your free subscription- Stay connected from anywhere
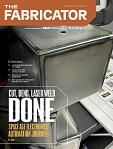
Easily access valuable industry resources now with full access to the digital edition of The Fabricator.
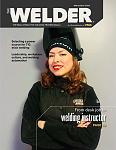
Easily access valuable industry resources now with full access to the digital edition of The Welder.
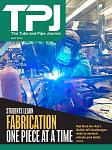
Easily access valuable industry resources now with full access to the digital edition of The Tube and Pipe Journal.
- Podcasting
- Podcast:
- The Fabricator Podcast
- Published:
- 04/16/2024
- Running Time:
- 63:29
In this episode of The Fabricator Podcast, Caleb Chamberlain, co-founder and CEO of OSH Cut, discusses his company’s...
- Trending Articles
Zekelman Industries to invest $120 million in Arkansas expansion
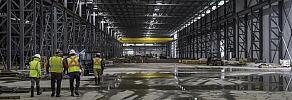
3D laser tube cutting system available in 3, 4, or 5 kW
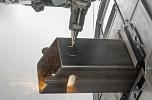
Corrosion-inhibiting coating can be peeled off after use
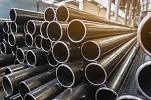
Brushless copper tubing cutter adjusts to ODs up to 2-1/8 in.
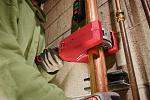
HGG Profiling Equipment names area sales manager
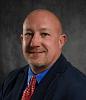
- Industry Events
16th Annual Safety Conference
- April 30 - May 1, 2024
- Elgin,
Pipe and Tube Conference
- May 21 - 22, 2024
- Omaha, NE
World-Class Roll Forming Workshop
- June 5 - 6, 2024
- Louisville, KY
Advanced Laser Application Workshop
- June 25 - 27, 2024
- Novi, MI