- FMA
- The Fabricator
- FABTECH
- Canadian Metalworking
Categories
- Additive Manufacturing
- Aluminum Welding
- Arc Welding
- Assembly and Joining
- Automation and Robotics
- Bending and Forming
- Consumables
- Cutting and Weld Prep
- Electric Vehicles
- En Español
- Finishing
- Hydroforming
- Laser Cutting
- Laser Welding
- Machining
- Manufacturing Software
- Materials Handling
- Metals/Materials
- Oxyfuel Cutting
- Plasma Cutting
- Power Tools
- Punching and Other Holemaking
- Roll Forming
- Safety
- Sawing
- Shearing
- Shop Management
- Testing and Measuring
- Tube and Pipe Fabrication
- Tube and Pipe Production
- Waterjet Cutting
Industry Directory
Webcasts
Podcasts
FAB 40
Advertise
Subscribe
Account Login
Search
Custom-made bundle unloader handles extremely cambered tubes
Belt-oriented system untangles, separates tubes from bundles
- November 28, 2018
- Article
- Materials Handling
Situation
Every automated process requires consistent parts to run efficiently and continuously. Out-of-print parts at the input end of a process generally lead to defective parts at the output end, and in extreme cases, they bring the process to a halt. In tube fabrication—especially of long, thin tubes, such as those used for automotive brake lines or fuel lines—noncompliance with straightness specifications is a common issue. Using a bundle unloader for such tubes is difficult, and in some cases impossible, because of the challenges in untangling a single tube. Singulating one tube and removing it from the bundle introduces unpredictable movements in the bundle that invariably tangle other tubes. The dynamic and unpredictable characteristics of this process makes it difficult to automate.
For low-volume applications of this sort, most fabricators rely on manual unloading. However, when an automotive parts supplier encountered this situation, it needed an automated process to keep up with the contracted part volume.
The parts came from a draw bench and were loaded into a hopper and sent to a straightener. Some camber was expected, but some of the tubes had up to 7 inches of camber from end to end.
Resolution
Engineers at Haven Mfg. found a way to use the tube shape as an advantage. They developed a system that uses several belts in parallel as a flexible trough. After a dozen or so tubes are deposited into this trough, the belts are drawn up slowly, making the trough wider and shallower, which causes the tubes to begin to untangle and settle into a single layer, unbundling themselves. A conveyor system moves the tubes through the machine as detectors monitor the contents of the conveyor. When the system detects more than one layer of tube—a tangle—the conveyor reverses direction, dumping the tubes back onto the belts, which have been relaxed to create the former trough. The cycle then starts over.
The tubes leave the sorting section in a consistent orientation, regardless of the camber’s severity, and the machine deposits them onto an inclined outfeed tray that acts as a buffer. A lifter then removes them, one tube at a time, and sends each one to the straightener.
Although the machine’s input section is not a fast-paced operation and includes frequent reversals, the buffer facilitates a continuous output that keeps pace with the straightener, which has a 7-second cycle time.
A video of the machine in action is available at http://havencut.com/custom-bundle-loader-severely-bent-tubes-video.
Haven Manufacturing Corp., http://havencut.com
About the Publication
Related Companies
subscribe now
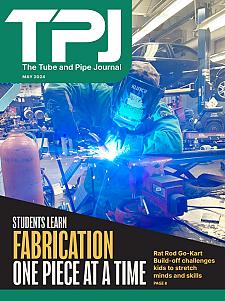
The Tube and Pipe Journal became the first magazine dedicated to serving the metal tube and pipe industry in 1990. Today, it remains the only North American publication devoted to this industry, and it has become the most trusted source of information for tube and pipe professionals.
start your free subscription- Stay connected from anywhere
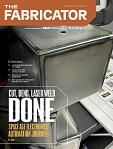
Easily access valuable industry resources now with full access to the digital edition of The Fabricator.
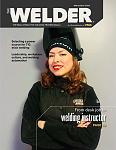
Easily access valuable industry resources now with full access to the digital edition of The Welder.
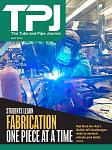
Easily access valuable industry resources now with full access to the digital edition of The Tube and Pipe Journal.
- Podcasting
- Podcast:
- The Fabricator Podcast
- Published:
- 04/16/2024
- Running Time:
- 63:29
In this episode of The Fabricator Podcast, Caleb Chamberlain, co-founder and CEO of OSH Cut, discusses his company’s...
- Trending Articles
Zekelman Industries to invest $120 million in Arkansas expansion
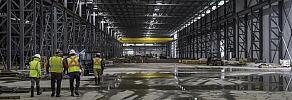
3D laser tube cutting system available in 3, 4, or 5 kW
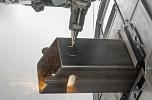
Corrosion-inhibiting coating can be peeled off after use
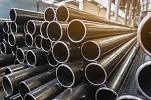
Brushless copper tubing cutter adjusts to ODs up to 2-1/8 in.
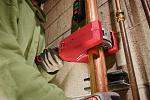
HGG Profiling Equipment names area sales manager
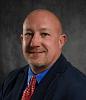
- Industry Events
16th Annual Safety Conference
- April 30 - May 1, 2024
- Elgin,
Pipe and Tube Conference
- May 21 - 22, 2024
- Omaha, NE
World-Class Roll Forming Workshop
- June 5 - 6, 2024
- Louisville, KY
Advanced Laser Application Workshop
- June 25 - 27, 2024
- Novi, MI