Editor
- FMA
- The Fabricator
- FABTECH
- Canadian Metalworking
Categories
- Additive Manufacturing
- Aluminum Welding
- Arc Welding
- Assembly and Joining
- Automation and Robotics
- Bending and Forming
- Consumables
- Cutting and Weld Prep
- Electric Vehicles
- En Español
- Finishing
- Hydroforming
- Laser Cutting
- Laser Welding
- Machining
- Manufacturing Software
- Materials Handling
- Metals/Materials
- Oxyfuel Cutting
- Plasma Cutting
- Power Tools
- Punching and Other Holemaking
- Roll Forming
- Safety
- Sawing
- Shearing
- Shop Management
- Testing and Measuring
- Tube and Pipe Fabrication
- Tube and Pipe Production
- Waterjet Cutting
Industry Directory
Webcasts
Podcasts
FAB 40
Advertise
Subscribe
Account Login
Search
Moving millions of feet of tube and pipe safely in the mill
Side-loading forklifts make handling long loads less dangerous at Ohio tube maker
- By Lincoln Brunner
- October 25, 2023
- Article
- Materials Handling
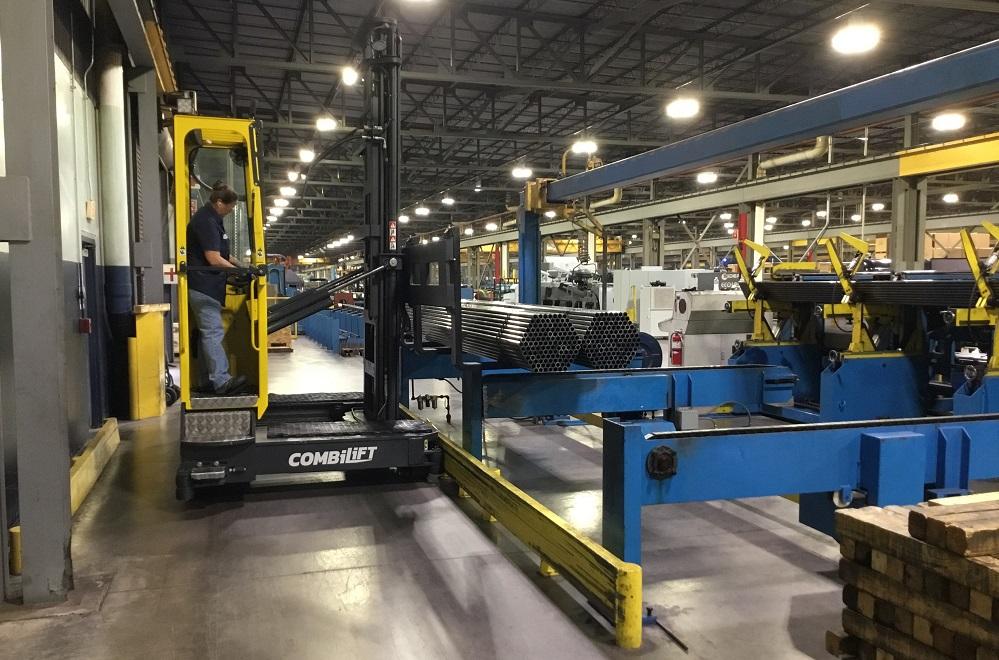
An operator at Jackson Tube Service moves tube bundles at the company’s plant in Piqua, Ohio. Jackson Tube Service
Moving tubes and pipes off the end of the mill is no small task, especially when the finished goods are up to 35.5 ft. long and possibly hundreds of pounds apiece.
For Jackson Tube Service Inc., Piqua, Ohio, that scenario plays out dozens or hundreds of times every workday as the company manufactures tubular goods for the automotive (as a Tier 2 supplier), power sports, motorcycle, and bicycle markets, among many others.
The company, founded in 1972, produces tube ranging in OD from 3/8 in. to 3 in. In all, Jackson manufactures about 100 million ft. of ERW tubing per year across nine tube mills, all of which need finished material moved out to the warehouse or to the next production process regularly and—most important—safely.
Filling a Role, Safely
All five of Jackson’s Combilift GT machines are stand-on units, powered by LPG and designed to move loads in tight spaces. With about 400,000 sq. ft. of space in its plant, tight spaces don’t normally concern Jackson as much as moving loads safely. In that regard, the company finds the GT’s 16-in.-high platforms a particularly helpful feature.
“Our number-one concern, why we really got into the side loaders, is safety,” Jackson Tube Service President/CEO Bob Jackson said. “We don’t want to have the material any higher off the floor than we have to. It comes off the tube mill, and it’s got oil on it, and you’re moving it around. If something would happen, it can slide off a fork, and we certainly don’t want anybody to get hurt.”
To facilitate fast, easy, and safe movement of long bundles of tubing, Jackson Tube began using Combilift side-loading forklifts more than 15 years ago. Jackson said the plant regularly uses three different types of units to move tubing: overhead cranes, traditional forklifts, and the five GT units. The latter do what the overhead cranes and traditional lifts cannot easily do.
“These tube mills are in six different bays,” Jackson said. “And we have a lot of overhead cranes, and they work well, but you can’t move material from bay to bay using the overhead cranes. So, that’s where these Combilifts work really well for us.
“The most productive way to operate a tube mill is to run longer lengths,” he added. “So, you’ve got these long sticks. We accumulate them into bundles, and then we’ve got to transport them. Either they’re finished and they go to the warehouse area, or we stage them for the next operation. The safest way to move them down a narrow aisle is long-ways, not sideways. So, the Combilifts work very well for that. And we can also go from bay to bay. They’re always out here moving a lot of material.”
The physical shape of Jackson’s product relative to storage space and the physical limitations of the factory floor is a huge issue. That’s where visibility plays a key role, according to Combilift’s President-North America Paul Short.
“When you’re traveling with the load left or right in the side-loader position, the product is in your field of vision,” Short noted. “You see the loads as you’re traveling forward or backwards, and you’re looking in that direction. Whereas if you’re using a regular lift, you would have to look up at each side of the load and make sure you’re clearing other objects or crane hooks or whatever else may be in the vicinity of the unit.”
Cooking With Gas
Jackson Tube Service runs two shifts daily, making the GTs much-used machinery. To keep the lifts as available and economical as possible, Jackson opted for LPG (propane)-powered units as opposed to the available diesel or lead acid battery-driven models. Having used side-loaders in the past from other companies, he liked the design, and having them propane-driven was a bonus.
Short said that having LPG tanks offers a degree of availability that doesn’t always come with other options.
“The reason a lot of customers like the LPG is, they can run 24 hours a day with minimal downtime,” Short said. “So, they don’t have to wait to charge, they don’t have to wait for batteries to cool down. They can just put in another LPG tank and run again for 24 hours. For some customers, that’s critical.”
Jackson also noted that while learning to drive the GTs takes some time, for the dozen or so people in his company that typically drivie the units, operating them has been easy. And while the Combilift units can’t do everything for a company that makes products 3 in. to more than 30 ft. long, they do fill a “huge gap” in the company’s material handling needs.
But at the end of the day, moving all of those products safely remains the main reason why the company continues to rely on the units so much.
“It’s hard to have one piece of material handling equipment do everything,” Jackson said. “We start with coiled steel and we ship finished tube. The key thing here is safety. If you’re trying to move long material and you’re taking it over people’s heads, it’s much more dangerous than keeping it down low and doing it longitudinally down an aisle.
“We have fork trucks, we have overhead cranes, but these side-loaders really fit well in between the two.”
About the Author
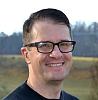
Lincoln Brunner
2135 Point Blvd.
Elgin, IL 60123
(815)-227-8243
Lincoln Brunner is editor of The Tube & Pipe Journal. This is his second stint at TPJ, where he served as an editor for two years before helping launch thefabricator.com as FMA's first web content manager. After that very rewarding experience, he worked for 17 years as an international journalist and communications director in the nonprofit sector. He is a published author and has written extensively about all facets of the metal fabrication industry.
About the Publication
Related Companies
subscribe now
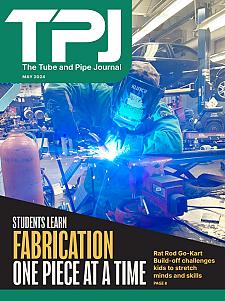
The Tube and Pipe Journal became the first magazine dedicated to serving the metal tube and pipe industry in 1990. Today, it remains the only North American publication devoted to this industry, and it has become the most trusted source of information for tube and pipe professionals.
start your free subscription- Stay connected from anywhere
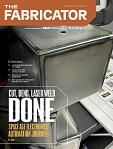
Easily access valuable industry resources now with full access to the digital edition of The Fabricator.
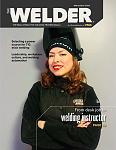
Easily access valuable industry resources now with full access to the digital edition of The Welder.
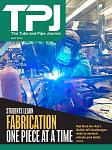
Easily access valuable industry resources now with full access to the digital edition of The Tube and Pipe Journal.
- Podcasting
- Podcast:
- The Fabricator Podcast
- Published:
- 04/16/2024
- Running Time:
- 63:29
In this episode of The Fabricator Podcast, Caleb Chamberlain, co-founder and CEO of OSH Cut, discusses his company’s...
- Trending Articles
Zekelman Industries to invest $120 million in Arkansas expansion
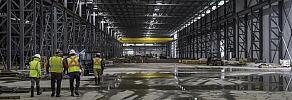
3D laser tube cutting system available in 3, 4, or 5 kW
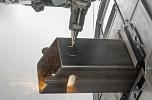
Corrosion-inhibiting coating can be peeled off after use
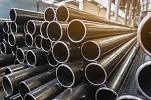
Brushless copper tubing cutter adjusts to ODs up to 2-1/8 in.
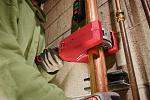
HGG Profiling Equipment names area sales manager
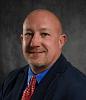
- Industry Events
16th Annual Safety Conference
- April 30 - May 1, 2024
- Elgin,
Pipe and Tube Conference
- May 21 - 22, 2024
- Omaha, NE
World-Class Roll Forming Workshop
- June 5 - 6, 2024
- Louisville, KY
Advanced Laser Application Workshop
- June 25 - 27, 2024
- Novi, MI