Marketing Specialist
- FMA
- The Fabricator
- FABTECH
- Canadian Metalworking
Categories
- Additive Manufacturing
- Aluminum Welding
- Arc Welding
- Assembly and Joining
- Automation and Robotics
- Bending and Forming
- Consumables
- Cutting and Weld Prep
- Electric Vehicles
- En Español
- Finishing
- Hydroforming
- Laser Cutting
- Laser Welding
- Machining
- Manufacturing Software
- Materials Handling
- Metals/Materials
- Oxyfuel Cutting
- Plasma Cutting
- Power Tools
- Punching and Other Holemaking
- Roll Forming
- Safety
- Sawing
- Shearing
- Shop Management
- Testing and Measuring
- Tube and Pipe Fabrication
- Tube and Pipe Production
- Waterjet Cutting
Industry Directory
Webcasts
Podcasts
FAB 40
Advertise
Subscribe
Account Login
Search
Renowned auto parts manufacturer races ahead with plasma cutting system
Aftermarket exhaust systems were never manufactured so quickly and never sounded so good
- By Ann Thompson
- January 14, 2021
- Article
- Plasma Cutting
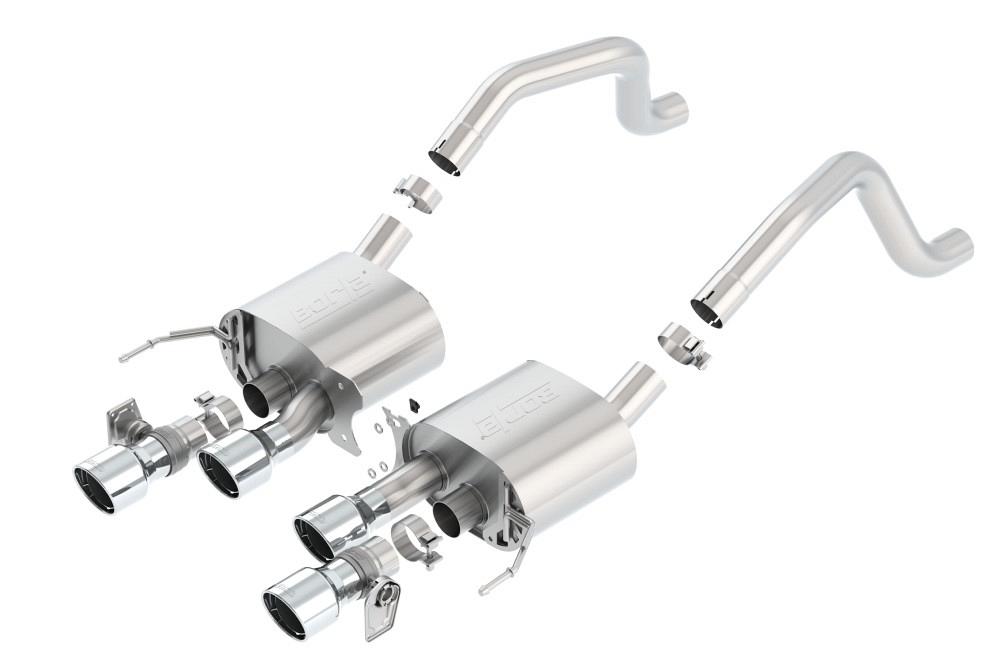
When aftermarket automotive parts manufacturer Borla Performance Industries switched from machining to plasma cutting, the company’s productivity improved in several ways—programming, cutting, and downstream operations. Borla Performance Industries
Alex Borla didn’t set out to be an inventor. Like many small business owners, he was just trying to keep his customers happy when he encountered a pretty big problem. One of his suppliers could no longer deliver parts.
The year was 1978 and Borla, in the business of selling and installing exhaust systems and other undercarriage components for Rolls-Royces, lost his supply of exhaust components. He knew tracking down another source would take time. That left Borla with two choices: lose sales or make his own parts. He decided to make the parts.
Using his own modest equipment, the 30-something immigrant developed more than a dozen exhaust system designs. His creations were good—better, in fact, than the parts he had been buying. Borla Performance Industries was born, with Borla making the systems and his wife managing the marketing and financial side of the business.
More than 40 years later, Borla is somewhat of an industry legend. To say the company’s exhaust systems are renowned among major automotive manufacturers and aftermarket distributors is an understatement. The racing world’s top competitors rely on Borla products for maximum performance, as do many consumers who aren’t involved in racing.
Getting the Most Out of an Exhaust System
At its most basic, an automobile’s exhaust system transfers exhaust gases from the engine to the sides or rear of the vehicle, where they disperse. Mufflers attenuate noise, catalytic converters reduce pollution, and that’s about it. Standard exhaust systems create back pressure, impeding the flow and stealing horsepower.However, some exhaust systems are far from basic. An exhaust system designed for a specific automobile, coupled with valve timing that opens the intake port before the exhaust port closes, can provide a flow so smooth that it creates a bit of a vacuum, helping to empty the cylinder of exhaust gasses and pull in more fuel at the input side. This process, called scavenging, is a goal of Borla systems—patented systems designed for racing and street use. Borla estimates that its technology can increase a street car’s horsepower and torque an average of 8.5%.
It gets better. Many auto enthusiasts think “bigger is better,” but Borla’s many years of research has proven that this is false. Large-diameter systems impede flow and cool the exhaust, neither of which help performance. Larger-diameter pipes also amplify the lowest frequencies, which can be more of a bother than a benefit.
Borla has gone so far to create optimal exhaust sounds that the company developed the Borla Polyphonic Exhaust Harmonizer. Using straight-through pipes of varying diameters and lengths, this system combines the equivalents of tuned notes to create sounds that work together to make harmonious exhaust sounds. It’s the pinnacle of the company’s slogan: Sound like heaven, go like hell and available in three Borla series.
Although the harmonizer isn’t available as part of every Borla exhaust system, every Borla customer can count on the company’s million-mile warranty. The company’s use of austenitic stainless steel gives it the confidence to guarantee that its exhaust systems outlast the automobiles they’re fastened to.
Getting the Most Out of a Manufacturing Operation
It all comes together in Tennessee, where more than 200 employees work in a 330,000-sq.-ft. facility. While the company had perfected the design and build of its systems, it felt it could improve the overall efficiency of its manufacturing process, beginning with the programming of parts.“Our programming was more manual than we wanted,” veteran engineer Jim Smail explained. “First we’d design the parts in CAD software to include the required holes. Then the CAD operator would ask a specialist in the machine shop to convert the design into machine code. Only then could the operator cut the job.”
Smail estimates more than 150 parts were produced using this three-step programming process. It worked, but it took a lot of time.
“My background involves software, so this was a logical place for me to look for efficiency enhancements on the production floor,” Smail said. “The engineers I partner with wanted to automate the design-to-cut process as much as possible, as well as improve fit-up for welding and installation to the customer’s vehicle.”
In addition to examining the software it used, the Borla team also considered the machining process it was using. The traditional CNC machine the company used worked well but had a high operating cost because of short tool life and the need to remove swarf from inside the pipe.
Borla decided to replace its old CNC machine with a Hypertherm Powermax65 CNC plasma cutting machine equipped with Rotary Tube Pro software specifically designed for tube and pipe cutting. Using the software, the Borla team was able to import 3D CAD files or create new ones easily. The team also liked the ability to access side-wall cutouts quickly from a list of predefined shapes.
Smail found the new setup to be extremely intuitive and said that he was able to train an employee unfamiliar with programming to cut in a very short period of time.
“It’s hard to believe, but it’s the truth,” Smail said. “We transferred an employee from the manufacturing floor to the design lab, and now that person is programming complex jobs in addition to operating the machine.”
The Borla team also was impressed by the productivity increases. For one high-volume muffler component, the new process saves 10 minutes per pipe. Including time saved on secondary deburring and cleanup, cycle time fell from 600 seconds to 7 seconds – a decrease of almost 99%.
About the Author
About the Publication
subscribe now
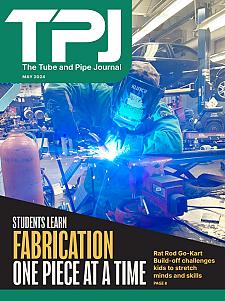
The Tube and Pipe Journal became the first magazine dedicated to serving the metal tube and pipe industry in 1990. Today, it remains the only North American publication devoted to this industry, and it has become the most trusted source of information for tube and pipe professionals.
start your free subscription- Stay connected from anywhere
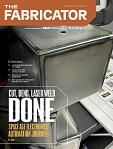
Easily access valuable industry resources now with full access to the digital edition of The Fabricator.
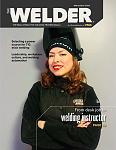
Easily access valuable industry resources now with full access to the digital edition of The Welder.
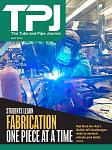
Easily access valuable industry resources now with full access to the digital edition of The Tube and Pipe Journal.
- Podcasting
- Podcast:
- The Fabricator Podcast
- Published:
- 04/16/2024
- Running Time:
- 63:29
In this episode of The Fabricator Podcast, Caleb Chamberlain, co-founder and CEO of OSH Cut, discusses his company’s...
- Trending Articles
Zekelman Industries to invest $120 million in Arkansas expansion
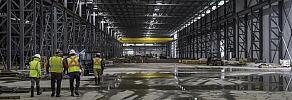
3D laser tube cutting system available in 3, 4, or 5 kW
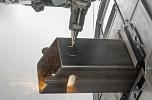
Corrosion-inhibiting coating can be peeled off after use
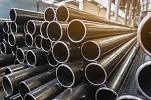
Brushless copper tubing cutter adjusts to ODs up to 2-1/8 in.
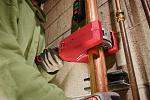
HGG Profiling Equipment names area sales manager
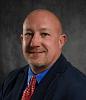
- Industry Events
16th Annual Safety Conference
- April 30 - May 1, 2024
- Elgin,
Pipe and Tube Conference
- May 21 - 22, 2024
- Omaha, NE
World-Class Roll Forming Workshop
- June 5 - 6, 2024
- Louisville, KY
Advanced Laser Application Workshop
- June 25 - 27, 2024
- Novi, MI