Product Specialist, Saw Division
- FMA
- The Fabricator
- FABTECH
- Canadian Metalworking
Categories
- Additive Manufacturing
- Aluminum Welding
- Arc Welding
- Assembly and Joining
- Automation and Robotics
- Bending and Forming
- Consumables
- Cutting and Weld Prep
- Electric Vehicles
- En Español
- Finishing
- Hydroforming
- Laser Cutting
- Laser Welding
- Machining
- Manufacturing Software
- Materials Handling
- Metals/Materials
- Oxyfuel Cutting
- Plasma Cutting
- Power Tools
- Punching and Other Holemaking
- Roll Forming
- Safety
- Sawing
- Shearing
- Shop Management
- Testing and Measuring
- Tube and Pipe Fabrication
- Tube and Pipe Production
- Waterjet Cutting
Industry Directory
Webcasts
Podcasts
FAB 40
Advertise
Subscribe
Account Login
Search
Separating sawing operations from snags, setbacks, stumbling blocks
Troubleshooting sawing problems can improve throughput, increase blade life, optimize cut quality
- By Kent Moreau
- March 8, 2018
- Article
- Sawing
Tube and pipe present several sawing challenges, many of which can be resolved with a thorough understanding of sawing mechanics and the specific issues that arise when sawing tubular workpieces. Eliminating sawing problems helps in three areas: improving cut rates, increasing saw blade life, and optimizing cut quality.
When cutting a hollow workpiece, the blade performs an interrupted cut. It enters and exits one wall of the material, then enters and exits the other wall. Compared to cutting a solid workpiece, this puts additional force and stress on each tooth; when one tooth leaves contact with the cut and the next tooth enters the cut, the force is so great that it can actually break a tooth. After the stress causes a tooth to chip, or rips the tooth out altogether, the forces are even greater on the remaining teeth. Premature blade failure is a likely result.
Round workpieces present challenges in coolant distribution. The workpiece’s shape can divert coolant from the cut, leading to inaccurate cutting and increasing heat buildup. Both of these problems will prematurely destroy the tooth edge.
Many conventional bi-metal blades also produce a heat-affected zone (HAZ), an area in which the heat increases so much that it changes the characteristics of the steel. Cutting through the HAZ can cause the teeth to tear away from the blade. Likewise, if the blade speed is too low for the material, the process doesn’t provide enough penetration per tooth, causing more rubbing than cutting. This also can overheat the material.
Another challenge involves improper blade pitch, which is the number of teeth per inch. The number of teeth that contact the workpiece can affect both blade performance and durability. Too few teeth in contact with the work can lead to early tooth strippage; too many teeth can reduce the blade speed and ultimately make the material impossible to cut.
A constant-pitch blade can increase harmonic vibrations, leading to excessive noise, undesirable saw or saw blade vibrations, and in severe cases, bad cuts. Fabricators can get around this problem by selecting variable-pitch blades, which can greatly reduce harmonic vibrations. The varied tooth spacing interrupts the rhythms that lead to harmonics and improves chip evacuation.
Although every band saw blade looks somewhat alike, they vary substantially. Blade manufacturers develop new concepts in how they are constructed and incorporate new features as time goes on, making blades cut faster and last longer.
In decades past, a band saw blade might well have been a single strip of sheet steel with teeth that were cut into it, whereas an advanced blade these days is more likely made from several components. One example is a blade made from a patented process in which two strips of high-speed steel wire are joined to a backing steel. The joining process, solid-state diffusion bonding, uses about 20 percent of the heat used in a conventional welding process and generates 170 percent more weld contact area than conventional processes. The result is a significantly reduced likelihood of fracture and breakage at the interface of the two materials.
Shortly after initial use, blades made by this process develop a U-shaped groove, 0.001 to 0.002 inch deep, between the two high-speed steel edges. The cutting action of the grooved-tooth geometry produces two chips that are easier to remove and therefore less likely to weld to the saw teeth than conventional chips. The groove also permits increased coolant flow to the cutting surface. Proper coolant flow cools and lubricates the blade and flushes out chips.
Troubleshooting Guide
Blade Breakage
- Wrong blade selected - Choose a blade with appropriate tooth pitch for the application.
- Blade tension set improperly - Adjust blade tension per the saw manufacturer’s instructions.
- Feed pressure set too high - Reduce pressure accordingly.
- Inadequate lubrication - Verify that the lubricant matches the application and is mixed to the proper ratio. If necessary, adjust lubricant nozzles to improve lubricant flow.
- Pressure blocks set too tight - Adjust guides.
- Blade rubs on wheel flange - Adjust wheel alignment.
- Inadequate blade support - Tighten, align, adjust, or replace guides.
- Side guides set too tight - Adjust side guides.
Premature Tooth Wear
- Blade installed backward - Install blade in correct orientation.
- Improper blade break-in procedure - Use the blade manufacturer’s recommended break-in procedure.
- Excessively hard material or heavy surface scale - Choose a blade that is appropriate for the material.
- Excessively hard material - Increase feed pressure.
- Inadequate lubrication - Verify that the lubricant matches the application and is mixed to the proper ratio. If necessary, adjust lubricant nozzles to improve lubricant flow.
- Blade speed or feed pressure set too high - Adjust the settings in accordance with the manufacturer’s recommendations.
Jagged Cut
- Inadequate blade support - Tighten, align, adjust, or replace guides.
- Blade worn out - Replace blade.
- Feed pressure set improperly - Adjust in accordance with the manufacturer’s recommendations.
- Improper tooth pitch for the application - Choose a blade that complies with the blade manufacturer’s recommendations.
- Inadequate lubrication - Verify that the lubricant matches the application and is mixed to the proper ratio. If necessary, adjust lubricant nozzles to improve lubricant flow.
- Inadequate blade support - Tighten, align, adjust, or replace guides.
Wandering Cut
- Feed pressure set too high - Adjust in accordance with the manufacturer’s recommendations.
- Too little blade tension - Increase tension in accordance with the manufacturer’s recommendations.
- Saw teeth damaged - Replace the blade and verify that it matches the material hardness.
- Inadequate blade support - Tighten, align, adjust, or replace guides.
Chip Debris Accumulates in Blade Teeth
- Worn or missing chip brush - Adjust or replace.
- Inadequate lubrication - Verify that the lubricant matches the application and is mixed to the proper ratio. If necessary, adjust lubricant nozzles to improve lubricant flow.
- Blade speed or feed pressure set too high - Adjust the settings in accordance with the blade manufacturer’s recommendations.
- Wrong blade selected - Choose a blade with appropriate tooth pitch for the application.
- Blade Worn on One Side Only
- Worn wheel flange - Adjust or replace wheel.
- Blade guide worn or misaligned - Adjust or replace.
- Teeth chipping, embedding in workpiece - Replace blade and use the blade manufacturer’s recommended break-in procedure.
Broken Teeth
- Improper blade break-in procedure - Use the blade manufacturer’s recommended break-in procedure.
- Blade speed set too low - Adjust the speed in accordance with the manufacturer’s recommendations.
- Feed pressure set too high - Adjust the setting in accordance with the manufacturer’s recommendations.
- Teeth jam in cut - Increase blade speed and reduce feed pressure.
- Inadequate lubrication - Verify that the lubricant matches the application and is mixed to the proper ratio. If necessary, adjust lubricant nozzles to improve lubricant flow.
- Excessively hard material or heavy surface scale - Choose a blade that is appropriate for the material.
- Wrong blade selected - Choose a blade with appropriate tooth pitch for the application.
- Workpieces spin - Tighten vise or, if cutting bundles, use bundle clamps.
Wear or Damage on Blade Backing
- Excessive back-up guide preload - Adjust pressure block in accordance with the manufacturer’s recommendations.
- Blade tension set improperly - Adjust blade tension per the saw manufacturer’s instructions.
- Blade worn out - Replace blade.
- Blade speed or feed pressure set too high - Adjust the settings in accordance with the blade manufacturer’s recommendations.
Blade Twisted in Cut
- Feed pressure set too high, causing blade to bind - Adjust pressure per the saw manufacturer’s instructions.
- Inadequate blade support - Tighten, align, adjust, or replace guides.
- Workpiece misaligned - Tighten vise.
Finally, saw operators should rely on their own cutting experience to prevent small sawing problems from turning into big ones. In addition to looking for clues, listening for clues can be a big help. If a cut doesn’t sound right, it’s a sign that something is amiss, and the troubleshooting should start sooner rather than later.
Kent Moreau is a product specialist, saw division, for L. S. Starrett Co., 121 Crescent St., Athol, MA 01331, 978-249-3551, www.starrett.com.
About the Author
About the Publication
Related Companies
subscribe now
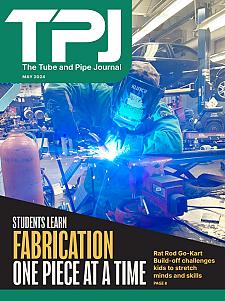
The Tube and Pipe Journal became the first magazine dedicated to serving the metal tube and pipe industry in 1990. Today, it remains the only North American publication devoted to this industry, and it has become the most trusted source of information for tube and pipe professionals.
start your free subscription- Stay connected from anywhere
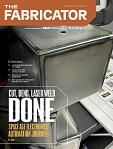
Easily access valuable industry resources now with full access to the digital edition of The Fabricator.
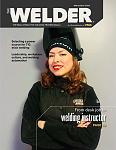
Easily access valuable industry resources now with full access to the digital edition of The Welder.
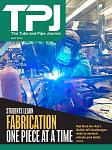
Easily access valuable industry resources now with full access to the digital edition of The Tube and Pipe Journal.
- Podcasting
- Podcast:
- The Fabricator Podcast
- Published:
- 04/16/2024
- Running Time:
- 63:29
In this episode of The Fabricator Podcast, Caleb Chamberlain, co-founder and CEO of OSH Cut, discusses his company’s...
- Trending Articles
Zekelman Industries to invest $120 million in Arkansas expansion
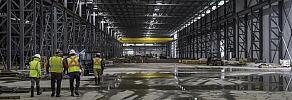
3D laser tube cutting system available in 3, 4, or 5 kW
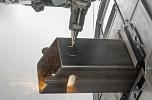
Corrosion-inhibiting coating can be peeled off after use
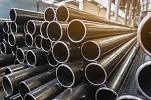
Brushless copper tubing cutter adjusts to ODs up to 2-1/8 in.
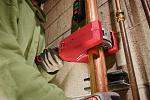
HGG Profiling Equipment names area sales manager
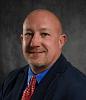
- Industry Events
16th Annual Safety Conference
- April 30 - May 1, 2024
- Elgin,
Pipe and Tube Conference
- May 21 - 22, 2024
- Omaha, NE
World-Class Roll Forming Workshop
- June 5 - 6, 2024
- Louisville, KY
Advanced Laser Application Workshop
- June 25 - 27, 2024
- Novi, MI