- FMA
- The Fabricator
- FABTECH
- Canadian Metalworking
Categories
- Additive Manufacturing
- Aluminum Welding
- Arc Welding
- Assembly and Joining
- Automation and Robotics
- Bending and Forming
- Consumables
- Cutting and Weld Prep
- Electric Vehicles
- En Español
- Finishing
- Hydroforming
- Laser Cutting
- Laser Welding
- Machining
- Manufacturing Software
- Materials Handling
- Metals/Materials
- Oxyfuel Cutting
- Plasma Cutting
- Power Tools
- Punching and Other Holemaking
- Roll Forming
- Safety
- Sawing
- Shearing
- Shop Management
- Testing and Measuring
- Tube and Pipe Fabrication
- Tube and Pipe Production
- Waterjet Cutting
Industry Directory
Webcasts
Podcasts
FAB 40
Advertise
Subscribe
Account Login
Search
Squeezing more uptime out of a tube or pipe mill
Using a cage forming system shortens changeover times
- By Eric Lundin
- August 30, 2017
- Article
- Shop Management
In every industry, the biggest enemy of continuous production is interruption. In tube or pipe production, interruptions for dimensional changes are necessary and planned, yet they are counterproductive. Every producer searches endlessly for ways to minimize interruptions and maximize uptime.
With a conventional mill, each product changeover usually requires changing every roll, which is a substantial undertaking. An alternative is cage forming, a process that uses universal roll sets in the forming section. Such rolls do not need to be removed and replaced when changing product sizes. In addition to reducing changeover time and lowering operating costs, the process reduces the investment in tooling rolls.
Cage Basics
Cage-forming pioneer SEUTHE developed CTA® (central tool adjustment) technology as an alternative to the conventional forming process in the 1990s.
“On a conventional mill making typical products, a changeover requires removing and replacing 24 roll tools,” said Jurgen Jost, president/CEO of ASMAG USA, a SEUTHE partner. “When using CTA, a typical changeover requires switching out eight roll tools” (see Figure 1).
In addition to adjusting the roll positions, the technology provides two other benefits.
“The CTA cage provides smooth transitions from one tool set to another,” said Jost. “In doing so, it produces a stress-relieved product. Also, it doesn’t mark the material.”
The process, which handles rounds, squares, and rectangles, is accompanied by a more recent technology, Flexible Cold Forming® (FCF), which forms squares and rectangles directly from the raw material.
“FCF uses one tool set for the entire mill,” Jost said, which makes product changeovers even faster. “No rolls need to be exchanged. You can produce all tube dimensions in the mill’s size range with a single tool set, which enables you to make small batches and frequent changeovers profitably.”
FCF’s ability to make stress-relieved product is due, in part, to the tooling arrangement. The tools are not opposite each other, but instead they alternate. As the strip moves through the cage, it is formed progressively from the right, then from the left, and so on.
“It’s a gentle way of forming,” Jost said.
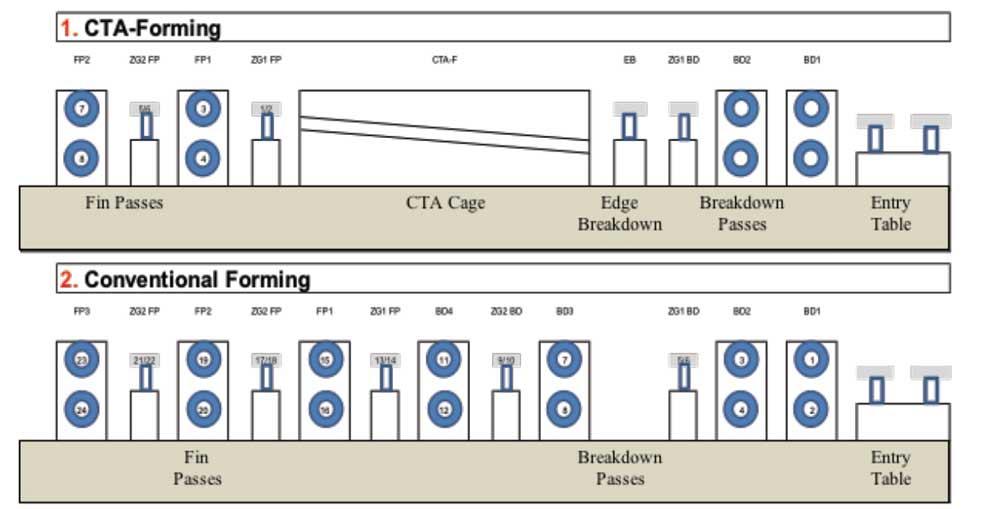
Figure 1
A cage-forming system, which can be retrofitted to an existing mill, can eliminate two-thirds of the tooling replacements associated with product changeovers.
Today’s Processes for Today’s Challenges
Depending on the material, properly forming the flat strip into a round tube can be a substantial challenge. Developing the bend sequence—the necessary amount of bend in the proper location across the strip width in the optimal progression—takes a quite a bit of engineering knowledge and roll forming experience. Through the years, SEUTHE engineers have learned that proper strip guiding and strip edge bending are even more important in cage forming than in conventional forming. The company developed a supplemental technology to bend the strip edges so the shape is formed properly. This technology deals with difficult-to-form materials, such as alloys with a high deformation ratios or high yield strengths, or heavy-wall materials. It has been used successfully for making API X70, a material with minimum yield strength of 70,000 pounds per square inch.
CTA can be retrofitted to an existing system, regardless of manufacturer. SEUTHE can provide a separate control system for the cage, or it can provide a new control system that integrates the existing mill controls and the retrofitted cage system controls into a single unit.
SEUTHE GmbH, Deilinghofer Strasse 11, 58675 Hemer, Germany, 49-2372-5060, www.seuthe.com, or in the U.S. contact Jurgen Jost at 847-558-4423 or info@asmagusa.com.
About the Author
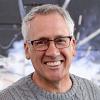
Eric Lundin
2135 Point Blvd
Elgin, IL 60123
815-227-8262
Eric Lundin worked on The Tube & Pipe Journal from 2000 to 2022.
About the Publication
subscribe now
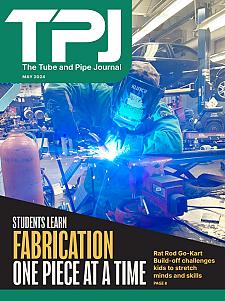
The Tube and Pipe Journal became the first magazine dedicated to serving the metal tube and pipe industry in 1990. Today, it remains the only North American publication devoted to this industry, and it has become the most trusted source of information for tube and pipe professionals.
start your free subscription- Stay connected from anywhere
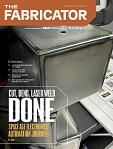
Easily access valuable industry resources now with full access to the digital edition of The Fabricator.
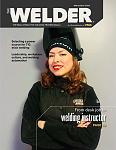
Easily access valuable industry resources now with full access to the digital edition of The Welder.
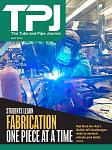
Easily access valuable industry resources now with full access to the digital edition of The Tube and Pipe Journal.
- Podcasting
- Podcast:
- The Fabricator Podcast
- Published:
- 04/16/2024
- Running Time:
- 63:29
In this episode of The Fabricator Podcast, Caleb Chamberlain, co-founder and CEO of OSH Cut, discusses his company’s...
- Trending Articles
Zekelman Industries to invest $120 million in Arkansas expansion
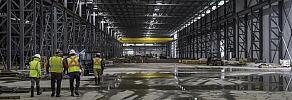
3D laser tube cutting system available in 3, 4, or 5 kW
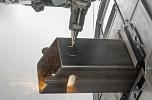
Corrosion-inhibiting coating can be peeled off after use
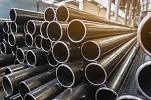
Brushless copper tubing cutter adjusts to ODs up to 2-1/8 in.
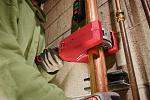
HGG Profiling Equipment names area sales manager
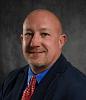
- Industry Events
16th Annual Safety Conference
- April 30 - May 1, 2024
- Elgin,
Pipe and Tube Conference
- May 21 - 22, 2024
- Omaha, NE
World-Class Roll Forming Workshop
- June 5 - 6, 2024
- Louisville, KY
Advanced Laser Application Workshop
- June 25 - 27, 2024
- Novi, MI